How Do I Straighten a Bent Drill Press Spindle: Tips and Tricks.
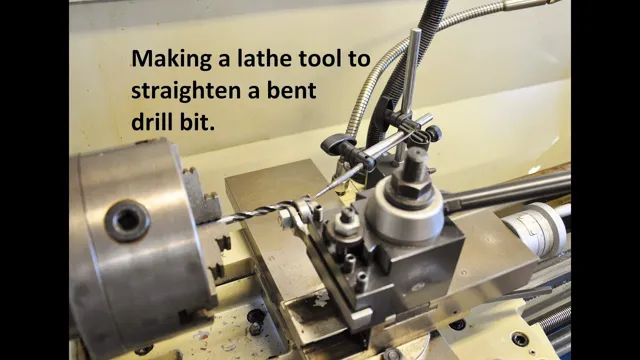
If you’re a DIY enthusiast or a professional woodworker, you know how important it is to keep your tools in good working condition. However, sometimes accidents happen, and your drill press spindle might get bent. A bent spindle not only makes your drill press unusable but can also lead to inaccurate drilling and damage to your workpiece.
Don’t throw away your drill press just yet because in this guide, we’ll show you how to straighten a bent drill press spindle. Whether you accidentally dropped your drill press or it got bent due to wear and tear, you can straighten it at home with simple tools and a little bit of patience. We’ll cover all the steps you need to take to straighten your drill press spindle and get it back to working condition.
So, grab your tools and let’s get started!
Overview
If you’ve encountered a bent drill press spindle, don’t fret, the fix is simpler than you might think. Here’s how you can straighten it. Firstly, remove the chuck and spindle from the press and clean them thoroughly.
Then, clamp the spindle in a vice, making sure to protect it with a cloth. Carefully use a mallet to tap the spindle in the opposite direction of the bend and test it frequently for straightness. Repeat the process until the spindle is straight, and remember to be gentle and patient to avoid causing any damage.
Lastly, reassemble the spindle and chuck back onto the press, and you’re good to go. With these simple steps, you’ll have a working drill press in no time. So, don’t worry if you find yourself with a bent spindle, fix it up with ease and get back to drilling in no time.
Explanation of Spindle Bend
Spindle bend is a complex topic that comes up frequently in the manufacturing industry. In simple terms, spindle bend refers to the deformation of a rotating spindle, which can lead to inaccurate machining and decreased product quality. This problem is commonly caused by uneven distribution of weight on the spindle or excessive cutting forces, which cause the spindle to flex and bend.
In severe cases, spindle bend can even cause damage to the spindle bearing or housing. To prevent spindle bend from occurring, manufacturers must carefully consider the weight and torque of their machining tools and make sure that they are appropriately balanced. Additionally, they must monitor cutting forces and speeds to ensure that they are well within the capabilities of the spindle.
By taking these precautions, manufacturers can avoid spindle bend and maintain high levels of product quality.

Why Straightening Is Important
Straightening hair can be beneficial for multiple reasons. Not only does it give a polished and put-together look, but it can also help improve the overall health of your hair. Straightening can help reduce frizz and makes it easier to manage.
By using heat styling tools, you can smooth out kinks and curls. Additionally, straightening can help prevent damage from tightly coiled hair by relaxing your strands. Straightening hair also allows it to reflect light more, which can make your hair look shinier and healthier.
It’s important to note that while straightening can be beneficial, it’s essential to use the proper products and tools to avoid damage or breakage. Overall, straightening can be a great way to achieve a desired look while also promoting optimal hair health.
Tools and Safety Measures
If you’ve noticed a bent drill press spindle, it’s important to address the issue promptly to ensure the safety of your workspace and prevent any further damage. A bent spindle can lead to inaccurate drilling or even breakage, posing a hazard to both the operator and the equipment. To straighten a bent drill press spindle, the first step is to remove it from the machine.
Then, using a hydraulic press or a sturdy vise, slowly and carefully exert pressure at the center of the bend until the spindle is straightened. It’s crucial to maintain heat control during this process, so as not to cause any thermal damage. Additionally, safety measures such as safety glasses and gloves should be worn at all times, and a second person should be present to assist with the process.
Once the spindle is straightened, it should be thoroughly inspected for any cracks or other damage before being reinstalled in the machine. By taking these measures, you can ensure the longevity and safety of your drill press equipment.
Materials and Equipment Needed
When it comes to woodworking, having the right tools and safety measures is essential for a successful and safe project. Some of the necessary tools for woodworking include a saw, hammer, drill, chisels, and clamps. Additionally, it’s important to have safety equipment such as safety glasses, earplugs, and gloves.
These will protect you from debris and loud noises that can cause harm to your eyes and ears. Additionally, gloves will give you a better grip on your tools, reducing the risk of injury from slipping. It’s also important to keep your workspace clean and organized to avoid tripping over tools and other materials.
Always read the instructions for your equipment and tools thoroughly to ensure proper usage and care. By taking these precautions, you can enjoy woodworking while staying safe and minimizing the risk of accidents or injuries.
Safety Precautions
When it comes to working with tools, safety should always be a top priority. Any time you’re using power tools, make sure you’re wearing the appropriate protective gear, such as safety glasses and ear protection. It’s also important to make sure the tool you’re using is functioning properly and has been inspected recently.
Never use a tool that is damaged or malfunctioning. Always follow the manufacturer’s instructions and warnings, and never remove safety features or guards. Additionally, it’s crucial to maintain a clean and organized work area to avoid tripping hazards and other accidents.
By taking these safety precautions and being mindful of your surroundings, you can ensure a safe and enjoyable experience while working with tools. Remember, as the saying goes, “an ounce of prevention is worth a pound of cure.”
Straightening Steps
If you’re wondering how to straighten a bent drill press spindle, the good news is that it’s usually possible to fix this issue with a little bit of work. However, it’s important to exercise caution when attempting this task, as any mistakes could lead to further damage or injury. To start off, you’ll need to remove the spindle from the drill press, and then clamp it securely in a vise.
Next, you can use a dial indicator to measure how much the spindle is bent, which will help you determine where you need to apply pressure to straighten it. Depending on the severity of the bend, you may need to use a hydraulic press or a specialized straightening tool to apply gentle pressure in the right spots until the spindle is perfectly straight once again. Be sure to check your measurements frequently throughout this process to avoid overcorrecting or causing additional damage.
With a little bit of patience and persistence, you’ll be able to restore your spindle to its former glory and get back to your drilling tasks with ease.
Disassembling the Drill Press
Disassembling a drill press can seem like a daunting task, but with the right steps, it can be broken down into manageable pieces. The first step is to gather all the necessary tools, including pliers, screwdrivers, and hammers. Once everything is in order, unplug the drill press and disassemble the chuck, removing any bits or pieces that may be lodged in its jaws.
Next, remove the motor housing by unscrewing the bolts and gently pulling it away from the body of the press. Take care not to damage any of the wiring or components as you do this. Finally, remove any additional parts such as the spindle, pulleys, and belts before cleaning each component separately to prepare it for reassembly.
With patience and care, disassembling a drill press can be a relatively simple task that helps keep your workshop in top working order.
Straightening the Spindle
If you notice that your spindle is no longer straight, don’t worry! Straightening out a spindle is not as difficult as you might think. The first step is to identify the problem areas and mark them. Then, use a straightening tool or a press to apply force to the marked spots until the spindle becomes straight.
It’s important to be patient and not apply too much force at once. You should gradually increase pressure until the spindle reaches the desired level of straightness. Once the process is complete, recheck the spindle to ensure that it’s fully straightened.
By following these simple steps, you can straighten your spindle and get back to work in no time!
Reassembling the Drill Press
When it comes to reassembling a drill press, there are several steps that need to be taken to ensure that everything is put back together correctly. One important step is straightening the pieces that may have become bent or misaligned during the disassembly process. This can be done by using a straightening tool to carefully manipulate the pieces back into their correct positions.
It’s important to take your time with this step to make sure that everything is lined up perfectly, as even the slightest misalignment can cause the drill press to not function properly. By taking the time to straighten the pieces carefully, you will ensure that your drill press is as good as new and ready for a variety of projects.
Conclusion
Straightening a bent drill press spindle can be a real headache, but fear not, with a little bit of ingenuity and some patience, you’ll have it fixed in no time. Remember, a straight spindle leads to straight holes, and straight holes lead to happy customers (or perfectionist hobbyists). So, go ahead, grab your toolbox, and straighten that spindle like a boss!”
FAQs
What could be the reason my drill press spindle gets bent?
A drill press spindle can get bent due to several reasons, such as applying too much pressure, incorrect use of the chuck key, or hitting the spindle with a hard object.
Can a bent drill press spindle be fixed?
Yes, a bent drill press spindle can be fixed, but it requires some technical knowledge and specialized tools. You can take the spindle to a professional repair shop or follow online tutorials to fix it yourself.
Is it safe to use a drill press with a bent spindle?
No, using a drill press with a bent spindle can be dangerous as it can cause the bit to wobble, resulting in an uneven hole or injury. It’s best to repair or replace the bent spindle before using the machine.
How often should I check my drill press spindle for bending?
It’s best to check your drill press spindle for bending periodically, at least once a month if you use the machine frequently. However, if you notice any unusual wobbling or shaking during operation, check the spindle immediately.
Can I prevent my drill press spindle from bending?
Yes, you can prevent your drill press spindle from bending by using the right drill bits, setting up the machine correctly, and avoiding excessive pressure. Additionally, always use the chuck key correctly, and keep the machine clean and lubricated to prevent damage.
What’s the cost of repairing a bent drill press spindle?
The cost of repairing a bent drill press spindle can vary depending on the severity of the damage and the repair shop’s rates. However, expect to pay at least a few hundred dollars for the repair.
Is it better to replace or repair a bent drill press spindle?
It’s better to repair a bent drill press spindle if the damage is not severe. However, if the spindle is heavily damaged, it’s more cost-effective to replace it with a new one rather than repairing it.