How to Make a Mill from a Drill Press: A Comprehensive Guide to DIY Milling in 2021
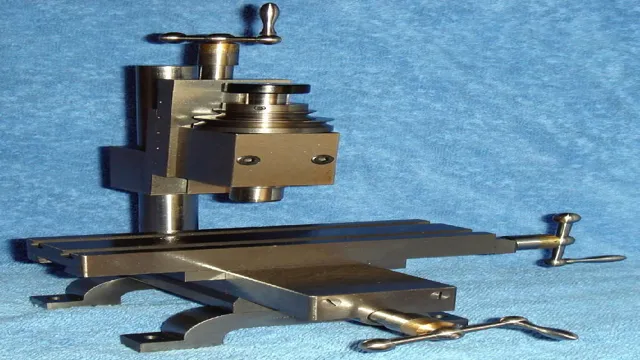
Have you ever wondered how to turn your standard drill press into a handy and efficient mill? Look no further! With a few simple modifications, you can easily transform your drill press into a milling machine that can handle a variety of tasks with ease. In this blog post, we will guide you through the step-by-step process of making a mill from a drill press, providing you with all the information you need to get started on your very own DIY milling project. So grab your toolkit and let’s get started!
Materials Needed
If you’re looking to turn your drill press into a mini mill, you’ll need a few essential materials to get started. First and foremost, you’ll need a set of milling jaws that can attach to your drill press. These jaws will hold your workpiece securely in place as you mill it down.
Additionally, you’ll need a milling vise that will clamp onto your drill press table, giving you even more control and precision. A set of end mills and drill bits will also be indispensable, as these tools will allow you to cut and shape your material to your desired specifications. Finally, you’ll need a digital readout (DRO) to make precise adjustments to your workpiece and ensure accuracy.
Armed with these materials, you’ll be well on your way to transforming your drill press into a reliable and versatile milling machine.
Drill Press
If you’re looking to buy a drill press, it’s important to know what materials you’ll need. First and foremost, the drill press itself is the most important tool you need. You can choose between benchtop or floor-standing models, depending on your needs.
Next, you’ll want to invest in a set of drill bits that are appropriate for the materials you’ll be working with. HSS (high-speed steel) bits are the most common and can drill through metal, wood, and plastic. If you plan on drilling through harder materials, like ceramics or glass, you may want to consider investing in diamond-tipped bits.
A clamp or vise is also useful to hold your workpiece securely in place while you drill. And lastly, safety gear is a must when working with power tools, so make sure you have safety glasses and hearing protection. With these materials, you’ll be all set to begin your drilling projects with your new drill press!

Angle Grinder
When it comes to using an angle grinder, there are a few materials that you should have on hand to ensure that you have a successful and safe experience. First and foremost, you will need the angle grinder itself, which comes in various sizes and power levels, depending on the job you need to do. You’ll also need a power source, a compatible extension cord (if necessary), and a suitable grinding wheel or blade for the task at hand.
It’s important to choose a wheel or blade that is designed for the type of material you’ll be cutting or grinding to minimize the risk of injury. Additionally, you may want to invest in personal protective equipment such as eye and ear protection, a dust mask, and sturdy work gloves to protect your hands from sparks and debris. By having these materials on hand and taking appropriate safety precautions, you can enjoy a successful and productive experience using an angle grinder.
Welding Machine
When it comes to welding machines, there are a few essential materials you’ll need to ensure a successful welding process. Firstly, the welding machine itself is crucial – make sure to choose one that fits your needs and budget. You’ll also need welding electrodes or filler material, depending on the type of welding you’ll be doing.
A welding helmet or mask is a must to protect your eyes and face from dangerous sparks and light. Gloves will protect your hands from heat and cuts, while a welding jacket or apron keeps your torso safe from sparks and burns. Don’t forget to have a fire extinguisher and first aid kit nearby just in case.
Lastly, having a sturdy workbench or stand to anchor your welding machine and materials will make the entire process much smoother and safer. Overall, these materials will help to ensure a successful and safe welding experience.
Steel Plate
When it comes to construction, steel plates are an essential component of many projects. They are incredibly durable and can withstand heavy loads and harsh weather conditions. To choose the right steel plate, several factors need to be considered, including the grade of the steel, size, shape, and thickness.
The grade of the steel plate determines its strength and durability, with higher grades costing more but providing increased safety. The size and shape of the steel plate should match the building’s design, with custom plates available to meet specific requirements. The plate’s thickness is also critical and should be determined based on the load-bearing requirements of the structure.
Therefore, when selecting steel plates, it is crucial to have a clear understanding of the requirements of the project to choose the right grade, size, shape, and thickness to ensure a safe, sturdy structure.
Steel Rods
Steel rods are a popular choice for construction projects due to their strength and durability. When it comes to making structures that can withstand the test of time, steel rods are a material that you simply can’t do without. In terms of materials needed, steel rods are relatively simple, as they are typically made from iron ore that has been heated and refined to create a strong and sturdy metal alloy.
However, there are a few other things that you’ll need if you plan to work with steel rods, such as protective gear like gloves and goggles, as well as the appropriate cutting and shaping tools. Steel rods can be cut and molded into a wide variety of shapes and sizes, making them a versatile choice for almost any construction project. Additionally, they’re inexpensive for their strength and the longevity they offer, making them an excellent option for anyone on a budget who doesn’t want to sacrifice quality or durability.
If you’re considering a construction project, steel rods are definitely a material to consider using.
Steps to Make a Mill from a Drill Press
If you are looking to create a milling machine but don’t want to buy a dedicated mill, you can repurpose a drill press to do the job. By following a few steps, you can create a functional mill that will provide a useful addition to your workshop. To start, you will need to secure a milling vise to your drill press table.
Next, you can create a spindle for the vise by attaching a chuck to a rod and mounting it in the drill press. Once you have the spindle in place, you can install a mill bit and begin milling. With a little practice and the right setup, you’ll be able to create precise cuts in metal, wood, and other materials.
Don’t forget to take safety precautions such as wearing eye protection and securing your workpiece. With these steps, you can easily make a mill from a drill press and take your DIY projects to the next level.
Step 1: Prepare the Base
If you’re looking to upgrade your drill press to a mill, there are certain steps that you’ll need to follow to ensure success. The first step is to prepare the base. This involves securing the drill press to a sturdy surface, such as a workbench or floor.
You can do this by either bolting it down or using clamps to hold it in place. Next, you’ll need to install a column adapter. This adapter is crucial as it allows you to attach the milling head to the drill press.
You’ll also need to remove the chuck from the drill press and replace it with the collet chuck. The collet chuck is the tool that holds the cutting tool in place and allows for precision when milling. It’s essential that you choose the right chuck size for the job at hand.
By following these steps, you’re well on your way to building a functional mill from your drill press. Just keep in mind that it’ll require patience and attention to detail to get it right.
Step 2: Create the Z-Axis
Now that we’ve created the X and Y axes for our drill press mill, it’s time to move onto the Z-axis. In order to do this, we’ll need to install a quill feed handle onto the drill press. This handle allows us to lower and raise the drill bit to make precise cuts.
Once the handle is installed, we’ll need to create a bracket to hold the motor in place. This bracket will need to be positioned in a way so as to allow the drill bit to be lowered and raised without interference. It’s important to ensure that the bracket is strong enough to support the weight of the motor and allow for smooth movement of the quill feed handle.
With the bracket in place, we can attach the motor to the bracket using bolts and then attach the motor to the drill press itself. Once everything is secured in place, we’re ready to move onto the next step in creating our very own drill press mill.
Step 3: Create the X-Axis
Before diving into creating the X-axis for your drill press mill, make sure you have all the necessary materials and tools. You will need a drill press, a drill bit, a vise, a ruler, a marker, and a piece of metal (preferably aluminum) that will serve as the X-axis. Once you have everything, begin by marking the center point of the metal piece, which will serve as the origin point for all measurements.
Then, using the ruler, mark the spots where you will drill holes for the bolts that will attach the x-axis to the drill press. Once you have all your holes marked, clamp the metal piece to the vise and begin drilling. Remember to take your time and double-check your measurements as you work.
Once all the holes are drilled, attach the X-axis to the drill press using the bolts and washers provided. With the X-axis securely in place, you’re ready to move on to the next step in creating your drill press mill.
Step 4: Create the Y-Axis
To continue making a mill from a drill press, the next step is to create the Y-axis. This is the axis that controls the left and right movements of the milling table. Start by getting a piece of steel plate and cut it into a rectangular shape.
Drill four holes in the corners of the steel plate, making sure they line up with the holes in the milling table. Next, bolt the steel plate to the milling table and attach a carriage bolt to the bottom of the plate. This bolt will serve as the pivot point for the Y-axis movement.
Attach a flat bar to the carriage bolt, making sure it is perpendicular to the steel plate. Finally, attach a lead screw to the flat bar and secure it in place. This lead screw will control the movement of the Y-axis.
It might seem complicated, but with accurate measurements and precise drilling, you can create a functioning Y-axis for your homemade mill.
Step 5: Install the Milling Head
Now, it’s time to install the milling head on your drill press to turn it into a mini mill. The milling head is a crucial part of the setup that allows you to make precise cuts and drill holes in materials. Start by removing the chuck from your drill press and attaching the milling head.
Follow the instructions provided by the manufacturer carefully to ensure that you do this step correctly. Once installed, you may need to make some adjustments to ensure that it’s level and centered. A milling vise is also necessary to hold your materials in place as you work.
It’s essential to make sure that everything is firmly secured in place to avoid any accidents. Taking the time to install the milling head properly will pay off when you start milling with your new setup. With everything in place, you’re almost ready to start milling.
Tips for Making a Mill from a Drill Press
Making a mill from a drill press is an excellent hack that can save you time and money. It’s a smart move for anyone who wants to do some DIY projects at home but doesn’t want to shell out cash for a milling machine. The first step is to remove the chuck from your drill press and replace it with a milling machine vise.
The vise will securely hold your workpiece in place while you mill it. Next, you’ll need to add a milling machine collet and cutting tools to your drill press. These accessories are crucial for milling and drilling operations.
Once you have all the necessary components, you can begin milling your workpiece. Start with a small cut to get the feel of the process and gradually increase the depth and width of each pass. With a bit of practice, you’ll be able to create precise cuts and achieve your desired results.
In short, with a few simple modifications, you can transform your drill press into a useful milling machine that can handle a variety of projects.
Tip 1: Use High-Quality Materials
If you’re attempting to make a mill from a drill press, one of the first tips to keep in mind is using high-quality materials. Investing in durable materials will help ensure that your mill lasts longer and operates more effectively. For instance, you may want to consider investing in high-speed steel drill bits or tungsten carbide inserts.
These materials are known for their superior strength and durability, making them perfect for handling the high demands of milling processes. By using quality materials from the start, you can avoid costly repairs or replacement down the line, while also producing high-quality milled products.
Tip 2: Take Safety Precautions
Making a mill from a drill press can be a lot of fun, but it can also be dangerous if safety precautions are not taken seriously. One important tip to remember is to always wear personal protective equipment such as safety glasses, gloves, and earplugs. The noise and debris from drilling can cause harm to your eyes, hands, and ears, and can even lead to serious injuries.
Another safety tip is to avoid wearing loose clothing or jewelry that could get caught in the drill press. Additionally, it’s important to keep the drill press clean and well-maintained to avoid any accidents or malfunctions. By following these safety precautions, you can enjoy the process of making a mill from a drill press without compromising your well-being.
So, don’t forget to prioritize safety when embarking on this exciting DIY project.
Tip 3: Take Your Time
When it comes to making a mill from a drill press, one of the most important tips to keep in mind is to take your time. Rushing through the process can lead to mistakes and potentially dangerous situations. Make sure to carefully plan out each step and double-check your measurements before making any cuts.
Additionally, take breaks when needed to avoid fatigue and maintain focus. Remember, creating a mill from a drill press requires precision and attention to detail, so don’t rush the process. By taking your time, you’ll be able to ensure a high-quality end product that will perform exactly as needed.
Tip 4: Test the Milling Machine before Use
When it comes to making a mill from a drill press, testing the milling machine before use is crucial. It may seem like an obvious step, but it’s easy to overlook and end up with disastrous consequences if not performed. Before you start milling, you need to make sure the machine is working correctly and efficiently.
Run some tests to check the milling machine’s speed and accuracy, and make sure the spindle runout is within the tolerable range. Familiarize yourself with the machine’s basic operations, and make sure to follow the safety guidelines and protocols appropriately. Taking these steps will go a long way in ensuring you have a pleasant and productive milling experience with your drill press.
Remember to take things one step at a time, and don’t hesitate to ask for help if you need it. With proper care and attention, you can turn your drill press into a robust milling machine that will provide you with endless possibilities.
Conclusion
Congratulations! You’ve just learned how to turn an ordinary drill press into a milling machine. With a little bit of creativity, resourcefulness, and some elbow grease, you can successfully build your own mini-mill. Just remember to always prioritize safety, precision, and stability when working with this tool.
Now, go forth and mill to your heart’s content! Who needs to buy a fancy milling machine when you can DIY your own right at home? Happy building!”
FAQs
What materials do I need to make a mill from a drill press?
To make a mill from a drill press, you will need a drill press, an XY vise, a milling bit, and a milling table.
Can I use any type of drill press to make a mill?
It is recommended to use a heavy-duty drill press with a strong motor and a quill that can be locked in place.
Do I need any previous experience with milling or machining to make a mill from a drill press?
It is helpful to have basic knowledge and experience in milling and machining, but there are many tutorials and guides available online for beginners.
How precise can I expect my mill to be when made from a drill press?
While a mill made from a drill press may not be as precise as a dedicated milling machine, you can still expect a fairly high level of precision with proper setup and calibration.
How do I properly align the XY vise on my drill press mill?
Align the XY vise by using a dial indicator to check for any misalignment, then adjusting the position of the vise until it is perfectly parallel with the milling table.
What types of projects can I complete with a mill made from a drill press?
With a drill press mill, you can complete a wide range of projects including machining parts, drilling holes, and shaping materials like wood or metal.
How do I maintain and care for my drill press mill?
Regularly clean and lubricate the mill to keep it functioning smoothly, and regularly check for any signs of wear or damage to prevent potential safety hazards.