How to Remove the Spindle from a JT33 Drill Press: Easy Tips and Tricks

Have you ever found yourself needing to remove the spindle from your JT33 drill press? Perhaps it’s become worn out or you need to replace it altogether. Whatever the reason, removing the spindle may seem like a daunting task if you’re not familiar with the process. But fear not, because in this blog post, we’ll guide you step-by-step through the process of removing a JT33 drill press spindle.
By the end, you’ll be equipped with the knowledge and confidence to tackle this task on your own. Think of it like a puzzle, with each step leading to the final solution. So let’s dive in and get started!
Introduction
If you’re looking to remove the spindle from a JT33 drill press, there are a few steps you’ll need to follow. First, make sure the drill press is unplugged and the chuck is removed from the spindle. Next, locate the spindle lock on the drill press and engage it to prevent the spindle from rotating.
Once locked, remove any screws or bolts that are holding the spindle in place. Depending on your specific model, there may be a keyway or taper fit that secures the spindle to the drill press. If this is the case, you will need a special tool to remove the spindle.
With the spindle removed, you can inspect it for any signs of wear or damage and replace it if necessary. By following these steps, you can easily remove the spindle from your JT33 drill press and keep it running smoothly for years to come.
Explanation of what a JT33 drill press is and why the spindle might need to be removed
If you’re a DIY enthusiast or a professional woodworker, then you might have heard of or even own a JT33 drill press. But for those who are new to this world, let me give you a brief introduction to what a JT33 drill press is and why the spindle might need to be removed. A JT33 drill press is a type of machine that is used for drilling holes into various materials such as wood, metal, and plastic.
The JT33 refers to the spindle taper that’s used in this type of drill press. A spindle is the part of a machine that rotates and holds the cutting tool, in this case, the drill bit. Over time, the spindle might become worn out or damaged, which could lead to reduced accuracy and performance.
In some cases, you might need to remove and replace the spindle to ensure that your drill press is working at its best.
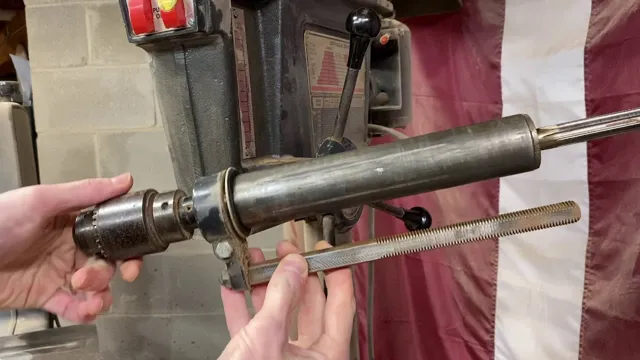
Step-by-Step Guide on Removing the Spindle
Removing the spindle from a JT33 drill press can be a daunting task, but with patience and attention to detail, it can be done with ease. Here is a step-by-step guide on how to remove the spindle from a JT33 drill press. Firstly, make sure that the drill press is switched off and unplugged before beginning any disassembly.
Then, remove the chuck by using a chuck key to loosen it. Next, loosen and remove the spindle nut using a wrench counterclockwise. Be sure to keep a firm grip on the spindle to prevent it from falling off.
Once the spindle nut is removed, push the spindle out of the quill using a drift or punch tool. Make sure to be careful not to damage the quill while pushing the spindle. Lastly, remove any debris or dust that may have accumulated in the quill before replacing the spindle.
And there you have it – a simple process for removing the spindle from a JT33 drill press.
Step 1: Turning off power and loosening the chuck
If you’re a DIY enthusiast or someone who occasionally fixes things around the house, learning how to remove the spindle from your power drill can be quite useful. Whether you need to replace a broken spindle or simply want to clean it, removing it is often the first step. The process may seem daunting, but it’s actually quite straightforward.
Step one is to turn off the power and loosen the chuck. This ensures that you’re not accidentally turning on the drill while you’re removing the spindle. To do this, unplug the drill or remove the battery, and then loosen the chuck by turning the key counterclockwise.
Make sure it’s loose enough to remove the bit or spindle, but not so loose that it falls out on its own. By following these simple steps, you’re well on your way to removing the spindle from your power drill.
Step 2: Removing the chuck and arbor
Removing the spindle of a lathe machine can seem like a daunting task, but it is not impossible. In this step-by-step guide, we will discuss how to remove the chuck and arbor from the spindle. Before proceeding with the removal of the spindle, it is essential to disconnect the lathe’s power source.
Once that is done, identify the spindle lock pin and disengage it. Locate the drawbar that secures the arbor to the spindle. Use a wrench to loosen the drawbar by turning it counterclockwise.
Once the drawbar is removed, the arbor can be freed from the spindle. The next step is to remove the chuck, which is attached to the arbor. Use a chuck wrench to loosen the set screws on the chuck.
Keep a firm hold of the chuck, and use a mallet to tap it free from the arbor. With careful maneuvering and steady pressure, the chuck can be completely removed from the arbor and the spindle. Following these steps is crucial to ensure successful removal of the spindle, arbor and chuck and optimal performance of your lathe machine.
Step 3: Removing the spindle collar
Removing the spindle collar can be tricky, but it’s a necessary step in the process to remove the spindle. The spindle collar is the piece that sits on the top of the spindle and holds it in place. To remove it, first, you need to make sure all power sources to the equipment are turned off and the spindle is not moving.
Next, you need to loosen the locking nut and slide it upwards on the spindle. Afterward, use a special tool called a spindle puller to apply force to the top of the spindle. This will loosen the spindle collar and allow you to remove it.
It’s important to note that the spindle puller needs to fit the spindle exactly, as using the wrong size can cause damage to the spindle. Once the collar is removed, the spindle should easily come out. Removing the spindle collar may seem like a daunting task, but it’s a necessary step in the process of repairing or replacing the spindle.
Step 4: Removing the spindle from the quill
If you’re looking to replace or repair the spindle in your milling machine, you’ll need to remove it from the quill. This process may seem daunting, but with the right steps, it can be a fairly simple task. The first step is to ensure that your machine is turned off and that the quill is fully retracted before you begin the removal process.
Next, you’ll need to locate the two set screws that hold the spindle in place. Using a wrench, you can loosen these screws and slide the spindle out of the quill. Be sure to handle the spindle with care, as it can be heavy and might require a second person to assist you.
With the spindle removed, you can then inspect it for any damage or wear and make necessary repairs or replacements. Overall, the process of removing the spindle is an essential step in maintaining the functionality of your milling machine.
Potential Problems and How to Fix Them
Removing the spindle from a JT33 drill press may seem like a daunting task, but with a little bit of guidance, it can be easily accomplished. The first thing to consider is whether the machine is unplugged and turned off before proceeding. Then, remove the chuck by loosening the screws and using a chuck key to unscrew it.
Once the chuck has been removed, locate the spindle lock and engage it so that it holds the spindle in place. Use an adjustable spanner to loosen the spindle nut, and carefully remove it by hand. If the spindle is still stuck, tapping it gently with a hammer should loosen it.
If all else fails, apply some penetrating oil to the spindle and let it sit for a few hours before attempting to remove it again. With patience and attention to detail, the spindle can be successfully removed, allowing for any necessary repairs or maintenance to be done.
Issue 1: Stuck Spindle
If you’re experienced enough to be using a lathe, then you’ll know that a stuck spindle can be a frustrating issue. However, before you start freaking out, there are a few things you can do to fix the problem. The first thing to check is whether the spindle is actually stuck, or if it’s just difficult to move.
It’s perfectly normal for there to be some resistance, especially if the lathe hasn’t been used in a while. However, if the spindle is genuinely stuck, then it could be due to a number of reasons. For example, the headstock bearings may have seized up, or there could be debris or rust inside the spindle bore.
To fix these issues, you’ll need to disassemble the headstock and clean everything thoroughly. Another potential cause of a stuck spindle is a broken or seized-up belt. In this case, you’ll need to replace the belt and check that the tension is correct.
By taking the time to diagnose the problem, you’ll be well on your way to fixing a stuck spindle and getting back to work.
Issue 2: Damaged Parts
If you’ve noticed that your electronic device is not functioning as it should be, it’s possible that some parts have been damaged. The first thing to do is to determine which parts specifically are not working or if there’s a problem with the overall device. A common issue could be with the battery which could be replaced.
Another issue could be a cracked screen, which would need to be repaired or replaced. Sometimes, damaged charging ports or headphone jacks can cause problems too. It’s important to address these issues promptly to prevent further damage or potential safety hazards.
Depending on the extent of the damage, it may be best to seek professional help or attempt to replace the damaged parts yourself. Ensure you are using genuine replacement parts, particularly for crucial components, to maintain the device’s reliability. Remember, always handle devices carefully to avoid any accidents or damage.
Conclusion
In conclusion, removing the spindle from a JT33 drill press is a task that requires patience, focus, and a good understanding of the machine. It’s important to remember that safety always comes first, so we recommend turning off the machine and unplugging it before getting started. Follow the steps carefully and don’t be afraid to ask for help if needed.
And remember, just like a good cup of coffee needs a perfect grind, a well-maintained drill press is essential for precision and accuracy. So, let’s get rid of that stubborn spindle and get back to drilling with ease and confidence!”
Summary of steps and reassurance that removing the spindle is a manageable task
If you’re planning on removing the spindle from your equipment, there are a few potential problems that you might encounter along the way. But don’t worry, with a bit of preparation and some know-how, these issues can be easily resolved. One common issue is rust or corrosion, which can make it difficult to unscrew nuts and bolts.
To combat this, you can use penetrating oil or a rust dissolver to loosen things up. Another issue is stripped screws, which can be caused by using the wrong tools or overtightening. To fix this, you can try using a screw extractor or a drill to remove the damaged screw.
If all else fails, you could also consider bringing in a professional mechanic to help with the task. Overall, while removing the spindle might sound daunting, with the right approach and a bit of patience, it’s a manageable task that can be accomplished with ease.
FAQs
What tools do I need to remove the spindle from a JT33 drill press?
You will need a spindle wrench, a drift punch, and a soft mallet.
How do I know if my drill press has a JT33 spindle?
Look for the letters “JT33” on the chuck or the spindle nose. Alternatively, you can measure the diameter of the spindle nose, which should be approximately 1.5 inches.
Can I remove the spindle without disassembling the entire drill press?
Yes, you can remove the spindle by following the manufacturer’s instructions and using the right tools. However, some models may require partial disassembly or removal of other components.
Is it safe to remove the spindle by myself?
As long as you follow the proper safety precautions and use the right tools, removing the spindle can be done safely. However, if you have never done this before or are unsure about any step, it is best to seek professional assistance.
How often do I need to remove and clean the spindle?
This depends on how frequently you use your drill press and the type of material you are drilling. As a general rule, it is good practice to clean and lubricate the spindle every six months to prevent rust and wear.
Can I replace the spindle if it is damaged or worn out?
Yes, most drill press spindles can be replaced if they are damaged or worn out. You will need to order a replacement spindle that matches the specifications of your drill press model.
What should I do if the spindle is stuck or difficult to remove?
First, make sure you are using the right tools and following the correct procedure. If the spindle still won’t budge, you may need to apply heat or penetrating oil to loosen the rust. In extreme cases, you may need to take the drill press to a repair shop for professional servicing.