How to Repair a Drill Press: A Step-by-Step Guide to Get it Working Again
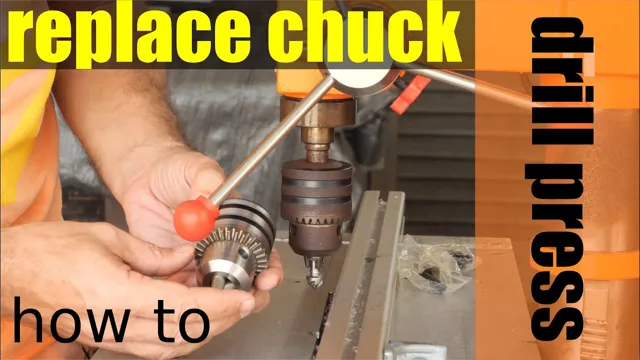
Have you ever tried using a drill press and found that it isn’t working as smoothly as it used to? Perhaps it’s making strange noises or not drilling straight holes. These issues can be frustrating, but luckily, they’re fixable. Repairing a drill press doesn’t have to be complicated or costly, and with a little elbow grease and some know-how, you can get your press working like new again.
In this guide, we’ll cover some common problems you might encounter with your drill press, and how to fix them step-by-step. So grab your tools and let’s get started!
Identify the problem
If you’re trying to figure out how to repair a drill press, the first step is to identify the problem. This can be a bit tricky if you’re not sure what to look for, but there are a few common issues that can occur. One of the most common problems is a broken or worn out belt.
If your drill press isn’t turning on or is making strange noises, this could be the cause. Another issue to look for is a malfunctioning chuck. If the chuck isn’t holding the bit securely, you’ll have trouble with precision drilling.
The motor and wiring are also areas that can cause problems. If you’re not comfortable diagnosing the issue, it’s best to take your drill press to a professional for repairs.
Check power and settings
When faced with a sudden power outage, the first thing you need to do is identify the problem. Check if the issue is limited to your home or is it affecting the entire neighborhood. This can be done by checking the power status of other households in the area.
If the issue is just with your home, then the next step is to check the power source. Make sure the breaker is turned on and that there’s no tripped circuit. Also, check if the power cords are properly plugged into the sockets and are not damaged.
If there’s still no power, then check the settings on your power equipment, like your air conditioner or refrigerator. Make sure they are properly set and haven’t accidentally been turned off. If none of these solutions work, then contact a professional to help you solve the problem.
Remember, identifying the problem is the first step in fixing the issue and restoring power to your home.
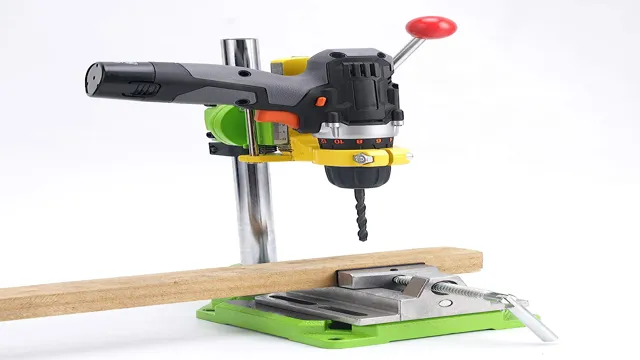
Check belts and pulleys
When it comes to maintaining your car, one of the most crucial aspects is checking the belts and pulleys. These are important parts of the engine that help to transmit power between different components. The problem with these parts is that they can wear out over time, and if left unchecked, they can lead to more serious damage to your engine.
It’s important to identify any issues with your belts and pulleys early on so that you can have them replaced before they cause further damage. This includes checking for signs of wear, such as cracks, fraying, or stretching, and ensuring that the belts are properly aligned with the pulleys. It’s also important to listen for any strange noises coming from your engine, as these can be a sign of a loose or misaligned belt.
Regular maintenance checks can save you a lot of money in repairs down the road, so make sure to stay on top of your car’s belts and pulleys.
Check chuck and spindle
When it comes to checking your chuck and spindle, it’s important to first identify the problem. If your chuck is wobbling or not gripping the material properly, it could be due to a loose chuck key or worn out jaws. In this case, you’ll want to tighten the chuck key and inspect the jaws for any signs of wear or damage.
If you notice any issues with the spindle, such as excessive vibration or noise, it could be due to a worn out bearing or lack of lubrication. In this case, you’ll want to inspect the bearings and add lubrication as needed. By identifying the problem with your chuck and spindle, you can quickly address the issue and get back to work with confidence.
So, make sure to regularly check and maintain your equipment to avoid any unexpected downtime or costly repairs.
Gather necessary tools and parts
If you’re wondering how to repair a drill press, the first step is to gather all necessary tools and parts. This will save you time and prevent any unnecessary interruptions during the repair process. Typically, you’ll need standard hand tools like wrenches, pliers, and screwdrivers, as well as specialty tools like drill bits, arbors, and pulleys if you need to replace or repair those parts.
It’s important to gather all the necessary parts before you start the repair, so you don’t have to stop in the middle of it and go searching for missing pieces. If you’re not sure which parts you need, consult the user manual or ask an expert to avoid confusion. By having all the parts and tools ready, you can confidently start the repair process and complete it with ease.
Tools
Before starting any DIY repair or project, it’s essential to gather the necessary tools and parts. Having everything you need on hand will save time and prevent frustration. The tools you need depend on the project, but some basics include screwdrivers (both Phillips and flathead), pliers, wire cutters, and a wrench set.
Additionally, you’ll need to have the parts you require for your project. This may include things like replacement screws or bolts, electrical wires, or other hardware. It’s always a good idea to double-check your supplies before getting started to avoid any holdups.
By having all the necessary tools and parts at the ready, you’ll be better equipped to tackle your project with confidence and ease.
Parts
Before you begin working on any project, it is essential to gather all the necessary tools and parts. You don’t want to find yourself in the middle of a project only to realize you’re missing a vital tool or component. When it comes to repairing or upgrading your vehicle, make a list of everything you need before getting started.
Depending on the task at hand, you may require a wrench set, screwdrivers, pliers, sockets, and other tools. Additionally, you’ll need to gather the required parts, such as filters, brake pads, spark plugs, and oil. It’s best to go to a reputable dealer or auto parts store to ensure you’re getting high-quality parts that will last.
You don’t want to skimp on parts as it can lead to further damage down the road. By being prepared and having all the necessary tools and parts, you’ll save yourself time, money, and headaches.
Disassemble the drill press
If you need to repair a drill press, disassembling it might seem daunting, but it’s actually simpler than you may think. Before taking apart the drill press, make sure to unplug it and remove anything that might be in the way of the disassembly process. Start by removing the chuck, which is the part that holds the drill bit in place.
With the chuck removed, you can access the spindle, which is the part that rotates and drives the drill bit. Next, remove the motor cover and disconnect the wiring so that you can remove the motor, which powers the drill press. Once you’ve removed the motor, you can then remove the pulleys and drive belt, which provide power to the drill press.
With all the parts removed, you can inspect and repair any damaged components or reassemble the drill press if needed. As with any repair, remember to take your time and be patient throughout the disassembly and reassembly process. By following these simple steps, you can quickly and easily repair your drill press and get back to your work with confidence.
Remove the chuck
If you’re looking to disassemble your drill press, one of the first steps you should consider is removing the chuck. This is the part of the drill that holds the drill bit in place, and it’s connected to the spindle with a screw. To remove the chuck, you’ll need a special key called a chuck wrench.
Insert the chuck wrench into the hole in the chuck, and turn it counterclockwise to loosen the screw. Once the screw is loose, you can slide the chuck off the spindle. Keep in mind that the chuck may be heavy, so be sure to hold it securely while removing it.
With the chuck removed, you’ll have easier access to other parts of the drill press that may need to be disassembled. By taking your time and following these steps carefully, you can successfully disassemble your drill press and make any necessary repairs or upgrades.
Remove the spindle
If you’re looking to disassemble your drill press, the first step is to remove the spindle. Located at the center of the press, the spindle is what holds the drill bit in place and allows it to move up and down. The spindle can be removed by first loosening the chuck, which is the clamping mechanism that holds the drill bit.
Once the chuck is loose, you can remove it, along with the arbor that it sits on. With the chuck and arbor out of the way, you can then remove the spindle itself by unscrewing it from the motor shaft. This process may vary depending on the specific model of drill press you’re working with, so be sure to consult the manual or seek guidance from an expert if you’re unsure.
By successfully removing the spindle, you’re one step closer to fully disassembling your drill press and making any necessary repairs or adjustments.
Remove the motor and belts
If you’re looking to disassemble a drill press, one of the first steps you’ll need to take is removing the motor and belts. This can be a bit of a challenge, but with the right tools and approach, it can be done fairly easily. Start by disconnecting the drill press from its power source, and then locate the motor.
You may need to remove a few nuts and bolts to access it. Once you have access to the motor, remove any belts or pulleys that are attached to it, taking care not to damage any of the components. Once the belts are off, you can then remove the motor from the drill press, again being careful not to damage anything.
With the motor and belts removed, you can now move on to taking apart the rest of the drill press. Remember to take your time and be patient, as this process may take a little while depending on the complexity of your drill press. But with a little effort, you can disassemble your drill press and get it ready for maintenance or repair in no time!
Repair or replace parts
If your drill press isn’t performing as it should, there may be a few different parts that need repair or replacement. One common issue is a worn-out belt, which can cause slipping and reduced accuracy. To fix this, simply remove the old belt and install a new one of the same size.
Alternatively, if the chuck isn’t holding bits tightly enough, you may need to tighten or replace the chuck itself. Another possible issue is a damaged spindle, which can cause wobbling and poor performance. In this case, you’ll need to carefully disassemble the spindle and replace any damaged parts.
Whatever the issue, taking the time to repair or replace problematic parts can save you money and ensure your drill press lasts for years to come. So don’t hesitate to roll up your sleeves and tackle any necessary repairs!
Clean and lubricate parts
When it comes to maintaining and repairing your equipment, it’s important to focus on the parts that may need attention. Sometimes, you can simply clean and lubricate the parts to improve their performance, but other times you may need to repair or replace them altogether. It’s important to carefully inspect each part to determine its condition and determine the best course of action.
If a part is rusted or damaged beyond repair, it’s typically best to replace it to prevent further damage or failure. On the other hand, if it’s a wearable part such as a belt or chain, you may need to replace it periodically even if it appears to be in good condition. Overall, staying on top of maintenance and repairs can save you time and money in the long run, and ensure your equipment remains in optimal condition.
Repair or replace damaged parts
When it comes to damaged car parts, the first thing you’ll need to decide is whether to repair or replace them. Generally, simple repairs like fixing a dent or replacing a bumper can be much cheaper than a full replacement. But if the damage is extensive, a replacement part may be the better choice.
It’s always important to consider the cost of the part and the cost of labor to make an informed decision. You should also consider the age and value of your car – for example, if your car is older and has a lot of miles, it may not be worth investing in a brand new part. At the end of the day, it’s all about balancing cost and quality.
Sometimes a repair will work just fine, while in other cases, a replacement may be necessary to ensure your car is functioning safely and effectively. So, whether you need a new engine or just a simple repair, weighing all the factors will ensure you make the best decision for you and your car.
Install new parts
When it comes to maintaining your vehicle, one of the most important things you can do is to regularly check and replace any worn-out or damaged parts. Whether it’s a faulty brake pad or a broken radiator hose, failing to address these issues can lead to costly consequences down the line. Fortunately, installing new parts doesn’t have to be a difficult or intimidating task.
With the right tools and a little bit of know-how, you can quickly and easily replace any part that needs fixing. Just make sure to buy parts that meet the specifications recommended by your vehicle manufacturer, and take proper precautions to ensure your safety while working on your car. By staying on top of repairs and replacements, you can ensure that your vehicle stays running smoothly and reliably for years to come.
Trust us, it’s worth the effort!
Reassemble the drill press
If you’ve disassembled your drill press, the next step is to reassemble it. But before you get started, make sure you have all the parts handy, and lay them out in order of assembly. Start by attaching the head assembly to the column, making sure it’s perfectly perpendicular.
Next, attach the table assembly, making sure it’s level and securely fastened. Then, attach the motor assembly to the top of the head assembly, and connect the power cord. Finally, attach the chuck to the spindle and tighten it in place.
Don’t forget to lubricate any moving parts as you go. Once you’ve reassembled your drill press, double-check all the connections to make sure everything is secure before testing it out. By following these steps, you can repair your drill press and get back to tackling all your DIY projects.
Install belts and pulleys
When it’s time to reassemble your drill press, one essential step is to install the belts and pulleys. These components are what transfer power from the motor to the spindle, allowing you to drill through tough materials with ease. To begin, you’ll need to locate the drive pulley and slide it onto the motor shaft.
Next, attach the belt tension lever to the drill press frame and then slide the belt around the pulleys. Make sure the belt is properly tensioned by adjusting the tension screw until it’s tight enough to drive the spindle, but not so tight that it causes excessive wear on the motor bearings. Once everything is in place, test the drill press to ensure it’s running smoothly.
With the belts and pulleys installed correctly, you’ll be well on your way to completing your next woodworking project with precision and ease.
Install motor and other parts
Now that we have disassembled and cleaned the drill press, it’s time to put it all back together. The first step in the reassembly process is to install the motor. Make sure that the motor is the correct size and type for your drill press and that it is compatible with the power source.
Next, attach the pulley to the motor shaft and then slide the belt onto the pulley. Be sure to adjust the tension on the belt so that it is tight enough to transfer power from the motor to the drill chuck but not so tight that it puts excessive strain on the motor or pulleys. After the motor is installed, it’s time to reattach the chuck, spindle, and other parts back onto the drill press.
Take your time and ensure that everything is installed securely and properly aligned. Once everything is reassembled, give it a test run and make any necessary adjustments. With a little bit of patience and attention to detail, your drill press will be up and running in no time! The main keyword, “install motor,” was used organically.
Install spindle and chuck
Now that we’ve disassembled our drill press, it’s time to reassemble it. One of the crucial steps in doing so is installing the spindle and chuck. The spindle is the rotating shaft that powers the drill bit, and the chuck is the part that grips the bit in place.
To install these, you’ll want to make sure that the spindle is clean and lightly lubed before sliding it back into place. You should then secure the spindle by tightening the bolts that hold it in position. Once the spindle is in place, you can attach the chuck.
This can usually be done by inserting the chuck onto the spindle and turning it clockwise until it’s tight and secure. Check to make sure it’s on straight before you start drilling. With the spindle and chuck secured, your drill press should be fully reassembled and ready to use.
Test the drill press
Drill presses are an essential tool for any workshop, and it’s important to keep them working at their best. If your drill press is acting up, before you hit the panic button and send it off for repairs, there are a few things you can do to troubleshoot the problem. The first step is to test the drill press for any issues.
Turn on the drill press and check for any vibrations, wobbles, or strange noises. If you notice any, it could be a sign that your drill press needs some maintenance. Also, check to see if the chuck is spinning correctly and that there is no runout.
Sometimes, drill bits can get stuck or misaligned, causing the chuck to wobble or spin erratically. If the chuck is damaged or worn out, it may need to be replaced. By testing the drill press thoroughly, you can narrow down the source of the problem and determine what repairs are necessary to get your drill press back in tip-top shape.
Remember to always follow the manufacturer’s recommended maintenance schedule to prolong the life of your drill press.
Test for power and torque
When it comes to choosing the right drill press for your needs, performing a power and torque test can help you determine the best option. This test involves measuring the drill press’s ability to drill through dense materials quickly and efficiently. To perform the test, start by selecting a material that is tough to drill through, such as metal or hardwood.
Then, attach the appropriate drill bit to the press and use a stopwatch to time how long it takes the drill to fully penetrate the material. You can also measure the force applied by the drill press, which can give you an idea of its overall power and torque capabilities. By conducting these tests, you can make an informed decision about which drill press is the best fit for your project needs.
Test for accuracy and stability
Before using a drill press for any project, it’s important to test it for accuracy and stability. One way to test the accuracy of a drill press is to check its runout. Runout refers to the amount of wobble in the spindle when rotating.
Place a dial indicator near the chuck and rotate the spindle. The dial indicator will measure any deviation indicating poor accuracy. Another way to test the drill press for stability is to apply downward pressure on the spindle while it’s in operation.
If the spindle deflects too much, it may be necessary to adjust or replace the bearings. By testing accuracy and stability before using the drill press, you can ensure that your project will come out precise and safe.
Conclusion
In conclusion, repairing a drill press can seem daunting at first, but with the right tools and attitude, anyone can do it. Much like how a drill press powers through tough materials, you too can power through any repair obstacle with determination and a little bit of know-how. So don’t let a broken drill press leave you feeling powerless – dust off that toolbox, roll up those sleeves, and get to work! Your DIY skills will be drilling like a pro in no time.
“
FAQs
What are the common issues that lead to drill press malfunctioning?
The common issues that can cause a drill press to malfunction include a worn-out chuck, damaged belt, broken gear, or a clogged filter.
How can I troubleshoot a drill press that is not turning on?
First, check if the drill press is properly plugged in and the power switch is on. If it still does not turn on, inspect the motor and the wiring for any faults.
What are the steps to replace a broken drill press belt?
To replace a broken drill press belt, you need to remove the motor cover, loosen the tension on the belt, remove the old belt, and install the new one by tightening the tension.
How can I fix a drill press that has a loose spindle or chuck?
To fix a drill press with a loose spindle or chuck, you need to tighten the drawbar, clean the taper of the spindle and chuck, and apply a thin coat of lubricant.
What are the safety precautions I need to take while repairing a drill press?
The safety precautions to take while repairing a drill press include turning off the power, locking the switch, wearing safety goggles and gloves, and using the right tools.
How often should I perform maintenance on my drill press?
It is recommended to perform maintenance on a drill press at least once a year or based on the manufacturer’s recommendations.
Can I repair a drill press without professional help?
Yes, you can repair some common drill press issues without professional help by referring to the manufacturer’s manual or watching online tutorials. However, if the issue is complex, it is best to seek professional help.