How to Use Electrofusion Welding Machine: A Step-by-Step Guide for Beginners
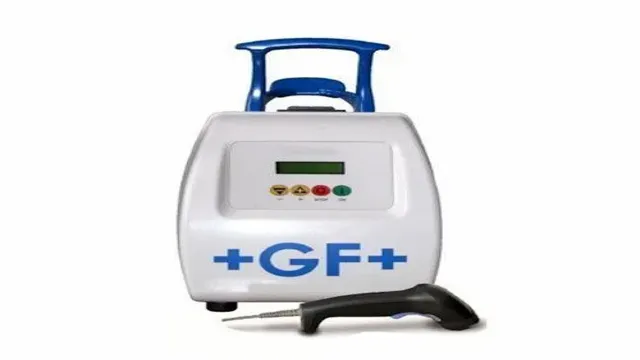
Have you ever needed to join two pieces of plastic together but weren’t sure how to do it effectively and securely? An electrofusion welding machine might just be the tool you need. This device allows for seamless welding of plastic pipes and fittings using an electrical current. It is an efficient and reliable method of joining plastic that is commonly used in the construction and plumbing industries.
In this blog, we will explore how to use an electrofusion welding machine, the benefits of using this method, and tips for achieving a successful weld. So, whether you’re a professional or a DIY enthusiast, read on to learn more about this innovative technique.
Safety Precautions
Electrofusion welding machines are commonly used in the construction and maintenance of pipelines. However, like any piece of equipment, it’s imperative to follow safety precautions when using them. When operating an electrofusion welding machine, it’s essential to wear appropriate protective clothing, including gloves, safety glasses, and a face shield, and ensure that the machine is installed and grounded correctly to avoid electrical shock.
Additionally, inspect the equipment before using it, and be sure to follow the manufacturer’s instructions regarding its operation. To prevent accidents, it’s advisable to keep the welding machine out of reach of children and untrained individuals who may accidentally touch it while it’s in operation. Furthermore, always use the machine in an adequately ventilated area to prevent inhaling harmful gases that may be produced during the welding process.
If you follow these precautions, you can safely use an electrofusion welding machine to complete your pipeline projects.
Proper attire
When it comes to safety precautions, one of the most important things you can do is dress appropriately for the task at hand. Whether you’re working in construction, operating heavy machinery, or engaging in any other activity where protective gear is necessary, proper attire can reduce the risk of injury and keep you safe on the job. The type of clothing you wear will depend on the specific hazards involved, but some key elements to consider include high-visibility colors, non-slip soles on shoes, and materials that can resist punctures, cuts, and other types of damage.
By wearing the right gear and taking other preventative measures, like following safety guidelines and undergoing proper training, you’ll be doing your part to keep yourself and those around you safe from harm.
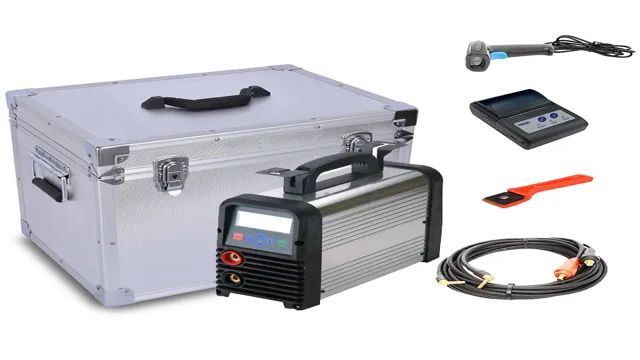
Proper ventilation
When setting up your workspace, make sure to prioritize proper ventilation to keep yourself and others safe. Good air flow is key for reducing the risk of inhaling harmful substances such as fumes and dust, and can help prevent the buildup of excess heat and moisture. Opening windows and doors, installing fans, and using air purifiers are all effective ways to improve air quality in your space.
When working with chemicals or other potentially hazardous materials, be sure to take extra precautions by using proper protective gear and checking in with any applicable safety guidelines. Remember, a well-ventilated workspace is not only a safer environment for you, but also supports overall well-being and productivity. So, keep the air flowing and breathe easy!
Disconnect power source
One of the most crucial safety precautions when working with electrical appliances or systems is to disconnect the power source. It might appear obvious, but it is essential to remember as it can save you from electrocution or other potential hazards. Before beginning any maintenance or repair work, always make sure to switch off the power at the main circuit breaker and inform others in the vicinity about your activity.
Even with the power off, it is advisable to use a voltage tester to ensure that there is no more electrical flow. Ignoring this safety precaution might lead to severe injury or damage to the equipment, so please make sure to implement it as a standard operating procedure. Stay cautious and aware of your surroundings when dealing with electrical systems to avoid unwanted and unfortunate incidents.
Keyword: safety precautions
Preparing the materials
If you’re wondering about how to use an electrofusion welding machine, it’s essential to start by preparing the materials. Electrofusion welding is a method of fusing pipes and fittings, which involves the use of electric current to melt and join the materials. First off, you need to inspect the pipeline’s physical condition to ensure that it’s clean, dry, and free from defects.
Next, use a specialized cleaning tool to scrape the surface of the materials to remove any dirt, moisture or contaminants that can affect the fusion process. After that, fit in the correct size and type of electrofusion fittings compatible with the pipeline’s material and diameter. Finally, connect the welding machine to the pipeline and conduct a dry run to ensure that everything lines up before starting the fusion process.
With the right tools and preparation, you can easily learn how to use an electrofusion welding machine to join pipes and fittings seamlessly.
Clean pipe ends
When it comes to preparing materials for a plumbing project, it’s important to start by making sure your pipe ends are clean and smooth. Any debris or rough edges can lead to leaks or a compromised connection. So, how do you clean your pipe ends? First, use a pipe cutter or saw to make a straight, even cut.
Then, use a deburring tool or sandpaper to remove any burrs or rough spots. Finally, wipe down the pipe with a clean cloth to remove any remaining debris or dust. Taking the time to properly prepare your materials can save you time and headaches in the long run.
So, give your pipes a little TLC before getting started on your next project.Keyword: pipe ends.
Confirm pipe and fitting compatibility
When working on a piping project, it’s crucial to ensure that the pipes and fittings are compatible with one another. This involves checking the materials used, the sizing, and the overall design of the pipes and fittings. One of the most important steps in preparing the materials is checking the compatibility of the pipe and fitting materials.
Different materials can have different expansion coefficients, meaning that they may react differently to changes in temperature or pressure. For example, PVC and metal pipes may have different expansion rates, which can make it difficult to connect them without causing leaks or other issues. By taking the time to confirm the compatibility of your pipes and fittings, you can help ensure that your project runs smoothly and that there are no unexpected problems.
This can save you time, money, and frustration in the long run.
Setting up the machine
If you’re looking to get started with electrofusion welding, the first step is obviously to set up the machine. While the specific steps may vary somewhat depending on the particular make and model of machine you’re using, there are a few basic principles that apply across the board. First, you’ll need to make sure that you have all the necessary components, including the welding machine itself, the control unit, and the fittings or pipes that you’ll be welding.
You’ll also need to ensure that the machine is properly grounded and that all connections and cables are securely fastened. Once you’ve done that, it’s simply a matter of following the instructions in the user manual and practicing until you feel comfortable with the process. Remember, electrofusion welding takes a bit of skill and technique, but with patience and practice, anyone can learn to use the machine effectively.
Install fusion machine and accessories
Installing a fusion machine for welding requires a few considerations to get it working in optimal condition. First, you need to select an appropriate location to set it up, considering its weight and the space it requires. Secondly, it would be best to pay attention to the temperature in the surrounding, ensuring that it remains optimal.
Next, you need to safely uncrate the components, before assembling the machine’s mainframe, and then fix the heaters and facer appropriately. Finally, you need to connect the necessary power source, add the hydraulic oil, and test the machine to ensure it runs correctly. It is essential to ensure all the accessories are assembled correctly, and safety precautions are adhered to when installing a fusion machine.
The accuracy of the machine’s alignment plays a critical role in its output and consequent results. Thus, it is paramount to check that the facer positions and carriage movement are calibrated before welding. Remember, a wrongly-assembled machine can result in defects and extra costs.
Installing the fusion machine and accessories requires careful consideration to ensure optimal output.
Set temperature and time
Setting up your coffee machine can be a daunting task, but once you know what to do, it’s a breeze. The first step is to set the temperature and time correctly. This varies depending on your machine, but most models will have instructions in the manual.
The temperature is important as it determines the strength of your coffee, so make sure to adjust it according to your preference. The time is also crucial as it ensures that your coffee brews at the right pace, not too fast or too slow. Once you’ve set both the temperature and time, you’re ready to start brewing! Remember that the process may take a few minutes, so be patient and let the machine do its work.
With the right temperature and time settings, you’ll be able to enjoy a delicious cup of coffee in no time.
Welding the Pipes
If you’re looking for a reliable and efficient way to join pipes, electrofusion welding might be the solution you need. This technique uses an electrofusion welding machine to weld two pipes together. First, you need to prepare the pipes by making sure they’re clean and dry.
Then, you need to attach the electrofusion fitting to one of the pipes. Next, you need to connect the welding machine to the fitting and align the pipes. Once everything is set up, you can start the welding process by following the manufacturer’s instructions.
In general, the machine will apply a voltage to the fitting, heating it and melting both pipes. When the welding is finished, you should let the pipes cool down before inspecting the joint. This process can be used for a wide range of pipe materials, including polyethylene, PVC, and more.
With the right equipment and technique, electrofusion welding can provide an incredibly strong and secure joint that can last for many years. So, if you need to weld some pipes, consider using an electrofusion welding machine.
Align the pipes and fittings
Welding the pipes is a crucial step when aligning the pipes and fittings for any pipeline project. It’s important to ensure that the pipes and fittings are well-aligned before welding them together to avoid welding mistakes and potential leaks. To align the pipes, you can use clamps or pins to hold them in place and ensure they’re level.
Once you’ve aligned the pipes and fittings, it’s time to weld them together. Welding involves heating the metal until it melts and fusing it together using a filler material. This process requires precision and skill to ensure that the weld is strong and leak-free.
In summary, aligning the pipes and fittings is the foundation for successful welding and creating a robust pipeline. The keyword here is welding, and it’s important to consider the alignment process before starting the welding process to prevent errors and leaks that can cause damage and delay.
Weld the pipes together
Welding pipes together is one of the most critical steps in piping installations. It involves joining two or more metal pipes using intense heat generated from an electric arc or gas flame. The process requires specialized expertise and precision to ensure the integrity and safety of the pipeline.
The first step in welding the pipes is to clean the surfaces of any rust, oil, or dirt using a wire brush or grinder. Then, the pipes are aligned, clamped, and tack welded to hold them together temporarily. The next step is to apply the main weld that fuses the pipes.
The welding technician uses a welding machine to deposit the filler metal on the joint, which melts and cools to create a solid bond. Welding creates high temperatures and toxic fumes that pose health and safety risks; hence proper ventilation and protective gear are mandatory. The welded joint should be inspected for any defects and tested for leaks before the pipeline can be put into operation.
Welding is a crucial skill in the piping industry, and it requires proper training, certification, and adherence to safety regulations to ensure reliable and safe installations.
Finishing the Job
If you’re planning on using an electrofusion welding machine, it’s important to know how to use it correctly to ensure a strong and secure weld. The first step is to properly prepare the pipe ends by cleaning and chamfering them to ensure a tight fit. Next, set the welding parameters on the machine according to the manufacturer’s instructions and clamp the pipe ends into the machine’s fitting sockets.
Once the machine has finished heating the fitting and the pipe, it will signal when it’s time to manually attach the two ends. Hold the pipe and fitting together until they’re fused, then let the joint cool according to the guidelines. Remember to always follow the manufacturer’s instructions and safety precautions to avoid injury or damage to the equipment.
With the right technique, an electrofusion welding machine can provide a strong and reliable joint for a variety of applications.
Cool the fusion area
Cooling the fusion area is a crucial step in finishing the job of nuclear fusion. The intense heat generated during a fusion reaction can cause serious damage to the reactor if it’s not dissipated quickly enough. This is why engineers and scientists use a variety of cooling techniques to lower the temperature of the fusion area without interrupting the reaction.
One popular method is to use liquid lithium, which can absorb the heat and carry it away from the plasma. Another technique involves using a flow of faster-moving gas in the spaces between the magnets that create the magnetic field that holds the plasma in place. Whatever technique is used, the goal is the same: to keep the temperature of the fusion area under control, allowing the reaction to continue while minimizing the risk of damage to the reactor.
Check for leaks
When it comes to finishing a job, it’s important to check for leaks to ensure that everything is in working order. Even the smallest of leaks can cause big problems down the line, so it’s best to be proactive and address any issues before they escalate. Start by checking all visible pipes and connections for signs of leakage, such as discoloration or moisture.
It’s also a good idea to check hidden areas, like under sinks or behind walls, for any signs of dampness or water damage. If you do find a leak, be sure to address it right away, whether that means tightening a connection or replacing a damaged pipe. By taking the time to check for leaks, you’ll be able to rest easy knowing that the job was completed properly and your home is protected from potential damage.
Remove any extra material
When it comes to finishing the job, removing any extra material is crucial. Whether you’re working on a DIY project or contracting a professional builder, ensuring that all excess materials are cleared away is an important final step. Not only will it leave your space looking clean and tidy, but it will also provide a safer environment.
This is especially important for construction sites where leftover materials can pose a tripping hazard and potentially cause injury. Additionally, it’s much easier to identify any potential issues or problems when there isn’t any clutter to get in the way. By adhering to this simple step, you’ll ensure that your project is completed to the highest standard and that you and your team can move on to the next project without obstruction.
So don’t forget to spend that extra bit of time removing any remaining materials, and you’ll be setting yourself up for success!
Conclusion
In conclusion, using an electrofusion welding machine is like playing a game of connect-the-dots, except the dots are pipes, and there’s no picture to show you how it’s supposed to look in the end. But fear not, with practice and a little bit of finesse, you’ll be able to fuse pipes together like a pro. Just remember to follow the manufacturer’s instructions, wear appropriate safety gear, and always double-check your connections.
With these tips in mind, you’ll be fusing pipes like a lightning bolt in no time!”
FAQs
What is Electrofusion Welding and How Does It Work?
Electrofusion welding is a method of joining two HDPE pipes using electricity and heat fusion. The process involves inserting a heating wire into the socket of the pipe fitting, and then fusing the pipe and fitting together by running an electrical current through the wire.
What Types of Electrofusion Welding Machines Are Available?
There are a variety of electrofusion welding machines available on the market, ranging in size, shape, and power. Some machines have a built-in barcode scanner for quick and easy fusion reports, while others have a more advanced control system for precise temperature and time control.
What Are the Advantages of Electrofusion Welding?
Electrofusion welding has several advantages over traditional welding methods. It is a fast, efficient, and cost-effective method of joining pipes, and it produces a strong, durable, and leak-proof joint. It is also environmentally friendly, as no chemicals or solvents are required.
How Do You Prepare Pipe Ends for Electrofusion Welding?
To prepare pipe ends for electrofusion welding, they must be cleaned and scraped to remove any dirt, debris, or oxidation. A chamfer tool is used to bevel the pipe ends, which helps to align the pipes and ensure a strong fusion joint.
What Safety Measures Should You Take When Using an Electrofusion Welding Machine?
When using an electrofusion welding machine, it is important to wear protective gloves, goggles, and clothing to prevent injury from heat or electrical shock. Always follow the manufacturer’s instructions carefully, and never touch the heating element or use the machine in wet conditions.
Can Electrofusion Welding Be Used on All Types of Pipes?
Electrofusion welding is typically used on HDPE (high-density polyethylene) pipes. It is not suitable for other types of pipes, such as PVC or metal pipes.
What Quality Control Measures Should You Use for Electrofusion Welding?
To ensure that electrofusion welding is performed correctly, it is important to conduct regular quality control checks. This includes checking the voltage, temperature, and fusion time during the welding process, as well as performing visual inspections of the joints after fusion.