What is Ultrasonic Welding Machine? An Insight into its Working and Applications
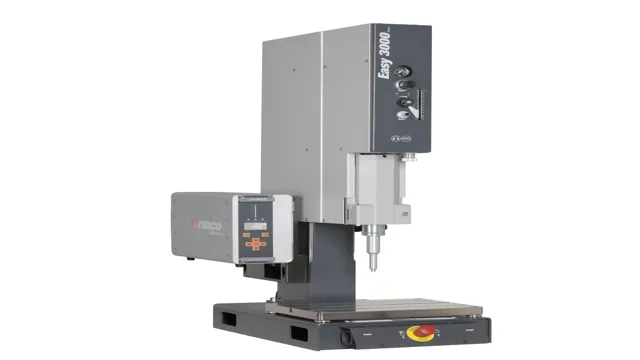
Ultrasonic welding machines may sound like the stuff of science fiction, but they’re actually quite commonly used in a range of industrial applications. But, what is an ultrasonic welding machine, exactly? Well, put simply, it’s a type of welding machine that uses ultrasonic waves to fuse together two materials. These machines are especially useful when it comes to working with plastics, as they can seamlessly bond two pieces of plastic together without the need for any additional adhesives or materials.
If you’ve ever wondered how plastic products are made, it’s likely that an ultrasonic welding machine played a big role in their production. In this blog, we’ll take a closer look at what ultrasonic welding machines are, how they work, and why they’re so useful in a range of different industries.
Definition
An ultrasonic welding machine is a type of welding equipment that uses high-frequency vibrations to join materials together without the need for any additional adhesive or fastening materials. It works by transmitting ultrasonic waves through the materials being joined, which causes them to vibrate and heat up. The heat and pressure caused by the vibration melts the materials at their joining surface, forming a strong, permanent bond.
Ultrasonic welding is commonly used in industries such as automotive, electronics, medical devices, and packaging. These machines are highly efficient and precise, allowing for fast and effective production processes. Additionally, they are environmentally friendly since they do not require any solvents or adhesives, and they produce no emissions or waste.
With the use of an ultrasonic welding machine, manufacturers can create high-quality, durable products that meet their exact specifications.
Explanation of Ultrasonic Welding and How it Works
Ultrasonic welding is a process of joining two plastic parts together using high-frequency ultrasonic vibrations. This process works by applying pressure to the parts that need to be welded and then introducing high-frequency acoustic vibrations. This action produces friction between the two surfaces, causing them to heat and melt.
As the melting occurs, the pressure held by the ultrasonic welding tool maintains contact between the two parts until they have cooled down and solidified. The result is a strong, seamless bond created without the need for any adhesives or additional materials. Ultrasonic welding is a reliable and efficient method commonly used in various industries, including automotive, aerospace, medical, and packaging.
With its ability to join plastics quickly, precisely, and without damaging the components or the surrounding environment, ultrasonic welding has become an essential technique in modern manufacturing.
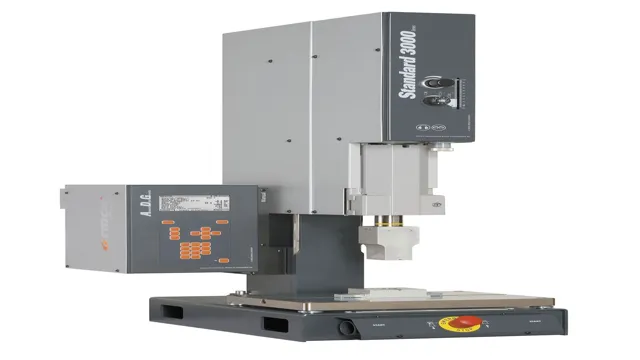
Applications
Ultrasonic welding machine is a type of equipment that uses high frequency mechanical vibrations to join two or more pieces of materials together. This process is commonly used in automotive, medical, and electronics industries to create strong, durable and precise bonds between materials that would otherwise require other types of welding or adhesive methods to join them. The ultrasonic welding machine uses an ultrasonic transducer to convert electrical energy into mechanical vibrations, and then applies these vibrations to the materials being joined.
As a result, the materials are melted and fused together, forming a permanent bond that is resistant to cracking, breaking, or tearing. Ultrasonic welding machines are also highly efficient, easy to operate, and suitable for a wide range of materials including plastics, textiles, and metals. Overall, ultrasonic welding machines are a versatile, reliable and cost-effective solution for many industrial manufacturing applications.
Materials Used for Ultrasonic Welding
Ultrasonic welding is a popular bonding technique that has gained wide acceptance in various industries today. This method utilizes high-frequency mechanical vibrations to melt and fuse materials together. Some of the most common materials used for ultrasonic welding include thermoplastics, aluminum, ceramics, and nonferrous metals.
When it comes to the applications of this technology, thermoplastics are the materials that are most commonly used in ultrasonic welding. This is because of their unique properties which make them ideal for this type of bonding. For instance, thermoplastics are highly flexible, which allows them to absorb the energy generated by ultrasound without breaking.
Additionally, these materials have low melting points, which makes them easier to bond together using ultrasonic energy. Overall, ultrasonic welding is a highly effective and versatile process that has a wide range of applications in various industries, thanks to the use of materials such as thermoplastics, aluminum, ceramics, and nonferrous metals.
Industries That Use Ultrasonic Welding
Ultrasonic welding is a popular technique used by various industries due to its fast and precise results. One of the primary applications of ultrasonic welding is in the manufacturing of medical devices. These devices are often made of plastic or thermoplastic materials, which can be challenging to weld using traditional methods.
Ultrasonic welding creates a strong and airtight bond that is essential in sensitive medical equipment. The automotive and aerospace industries also utilize ultrasonic welding to manufacture parts such as fuel tanks, sensors, and interior components. Ultrasonic welding is also used in the production of consumer electronics, including laptops and smartphones.
The technique is beneficial in creating small and complex parts with intricate designs. Additionally, the food and packaging industry use ultrasonic welding in sealing and cutting packaging materials. These materials need to be sealed accurately to avoid contamination and ensure that the contents are well preserved.
The versatility and effectiveness of ultrasonic welding make it an essential tool for numerous industries.
Advantages
Ultrasonic welding machines are unique pieces of equipment that can fuse two materials together through ultrasonic vibrations. This process has several advantages over traditional welding methods, making it an excellent choice for many manufacturers. Firstly, ultrasonic welding machines do not require any additional materials such as adhesives or fasteners, which can save time and money.
Secondly, the welding process is incredibly precise, producing consistent welds every time. Another advantage is that the process is quick, allowing for high-volume production runs. Lastly, ultrasonic welding machines can weld complex shapes and hard-to-reach areas, making them versatile tools for many industries.
Overall, the advantages of ultrasonic welding machines make them a popular choice for manufacturers looking for fast and cost-effective welding solutions.
Speed and Efficiency
When it comes to business, speed and efficiency are crucial. The faster you can complete a task, the more work you can get done in a day. And the more efficient you are, the less time and resources you waste on unnecessary activities.
This is why businesses strive to streamline their processes and boost their speed and efficiency. The advantages of this approach are many. For one, increased productivity means more revenue and higher profits.
It also means happier employees who are less stressed and more motivated to do their best. Speed and efficiency can also give a business a competitive edge, enabling it to respond to customer needs and market changes quickly. But achieving speed and efficiency isn’t always easy, especially in complex organizations or industries.
It requires careful planning, the right tools and technologies, and a culture of continuous improvement. Nevertheless, the benefits make the effort well worth it. So, if you want to succeed in today’s fast-paced, competitive business world, prioritize speed and efficiency in everything you do.
Clean and Reliable
Clean and Reliable- Advantages Choosing a clean and reliable product offers several advantages that make it a wise investment. First and foremost, a clean product ensures that it is free from harmful chemicals or contaminants that can cause health issues in the long run. Additionally, a reliable product guarantees that it will work as intended and will not break down or malfunction easily, reducing the need for repairs or replacements.
Using a clean and reliable product also contributes to a sustainable environment by reducing waste, energy consumption, and pollution. Moreover, it can enhance the user’s experience, making them feel satisfied and confident about their purchase, thereby increasing brand loyalty. In the long run, businesses that prioritize clean and reliable products can enjoy increased revenue and customer satisfaction, making it a win-win situation.
In conclusion, choosing clean and reliable products is advantageous for both the consumer and the environment, making it a compelling choice in today’s world.
Cost-effective
Cost-effective business strategies are always a welcome addition to any company’s structure. There are several advantages of implementing these strategies, including the ability to save resources, minimize expenses, and increase revenue. By cutting costs without sacrificing quality, companies can use the funds saved to increase their marketing or production budget.
Cost-effective strategies could also involve outsourcing work to countries with lower labor costs where the same job could be performed for less money. Besides, using the latest technological advancements, such as automation or AI, can also improve processes and reduce overall costs. At times, companies must acknowledge that cutting corners could lead to sub-par results; therefore, effective cost-cutting strategies should focus on efficiency instead of eroding customer experiences.
Overall, the advantages of cost-effective business strategies are many, and their implementation could lead to a successful business with higher profits.
Disadvantages
When it comes to using an ultrasonic welding machine, there are certainly advantages to consider. However, it’s important to also be aware of any potential disadvantages that may come along with this method of production. For example, while ultrasonic welding is quick and efficient, it can also sometimes be a bit costly to set up and maintain.
Additionally, this method is not always ideal for welding thicker materials, as it may not provide enough strength in the bond. Finally, it’s worth noting that ultrasonic welding may not be the most environmentally friendly option, as it often requires a significant amount of energy to run. Despite these drawbacks, ultrasonic welding can still be a highly effective choice for certain applications, and it remains a popular method for many manufacturers.
Limited Joint Strength
One of the biggest disadvantages of limited joint strength is the possibility of joint damage and injury. If a joint is unable to support a certain amount of weight or pressure, it becomes at risk of dislocation or fracture. This is particularly common in older individuals or those with pre-existing joint conditions, such as arthritis.
Additionally, limited joint strength can also impact overall mobility and range of motion. Individuals may find it difficult to perform certain activities or movements without experiencing discomfort, pain, or even injury. It’s important to address limited joint strength through proper exercise and rehabilitation techniques to avoid further damage and prolong joint health.
Limited Thickness
Limited thickness can be a major disadvantage when it comes to certain materials. For instance, in the world of construction, thin materials can be prone to warping or breaking under stress. This can lead to structural instability, which can be potentially dangerous.
Additionally, materials with limited thickness may not provide the same level of insulation as thicker materials. This can result in increased energy costs and a less comfortable living or working environment. It’s important to carefully consider the thickness of materials when planning any type of construction or renovation project, and to choose materials that are both structurally sound and energy-efficient.
By doing so, you can help ensure the safety and comfort of those who will be using the space in question.
Conclusion
In short, an ultrasonic welding machine is like the lovechild of a vibrating tuning fork and a powerful glue gun. It uses high-frequency vibrations to melt two pieces of material together, creating a strong and seamless bond without any unsightly marks or messy adhesives. So, whether you’re a manufacturer looking to streamline your assembly process or just a curious DIY enthusiast, an ultrasonic welding machine is a handy tool to have in your arsenal.
Just don’t let it go to your head – you may be a master of joining materials with sound waves, but you’re still not quite on par with a superhero.”
FAQs
What is an ultrasonic welding machine?
An ultrasonic welding machine is a type of welding equipment that uses high-frequency ultrasonic vibrations to join materials together.
What materials can be welded using an ultrasonic welding machine?
Ultrasonic welding machines can be used to weld a variety of materials such as thermoplastics, synthetic fabrics, and metal.
How does an ultrasonic welding machine work?
An ultrasonic welding machine works by converting electrical energy into high-frequency mechanical vibrations, which are used to create heat and pressure to join materials together.
What are the advantages of using an ultrasonic welding machine?
Advantages of using an ultrasonic welding machine include faster and more efficient joining of materials, no need for additional consumables such as glue or screws, and the ability to join materials with complex shapes or sizes.
What are the applications of ultrasonic welding machines?
Ultrasonic welding machines are used in a broad range of manufacturing industries, including automotive, electronics, medical, and packaging.
How does an ultrasonic welding machine compare to traditional welding techniques?
Ultrasonic welding machines offer several advantages over traditional welding techniques such as faster cycle times, reduced distortion, and no need for additional consumables.
What factors should be considered when selecting an ultrasonic welding machine?
Factors to consider when selecting an ultrasonic welding machine include the material to be welded, the required strength of the weld, and the production volume and cycle time requirements.