How to Rebuild an Air Compressor: A Step-by-Step Guide for DIYers
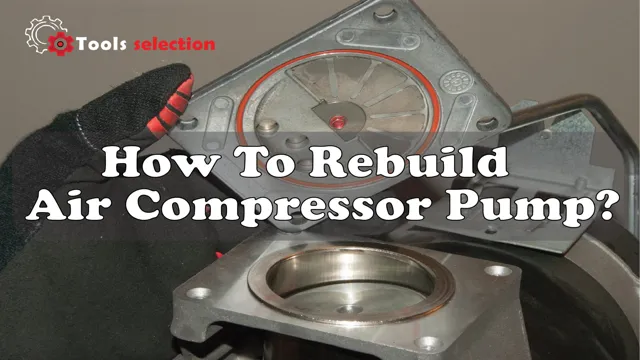
If you’re someone who relies on an air compressor for your daily tasks, you know how frustrating it can be when it suddenly stops working. Don’t worry, though. You don’t have to go out and buy a brand-new compressor just yet.
In fact, rebuilding your air compressor is a cost-effective and straightforward solution. Whether you’re an experienced DIYer or a beginner, in this blog post, we’ll show you step-by-step how to rebuild an air compressor. Think of it this way: just like a car needs regular maintenance to run smoothly, so does your air compressor.
Over time, the parts in your compressor wear out or become clogged with dirt and debris. This can lead to decreased performance or complete failure. But with a little bit of elbow grease and some basic tools, you can get your air compressor up and running like new again.
So, why pay for a costly repair job or a brand-new compressor when you can do it yourself? By following our simple guide, you’ll save money, gain valuable experience, and most importantly, breathe new life into your air compressor. It’s time to roll up your sleeves and get to work!
Step 1: Safety First
If you plan on rebuilding an air compressor, you must prioritize safety first. Before doing anything, make sure that the air compressor is turned off and unplugged. Also, wear protective gear, such as goggles and gloves, to avoid any potential injuries.
You might want to read through the manufacturer’s manual to learn about the potential hazards and precautions specific to your model. If you’re dealing with an older air compressor, be aware of any rusted and damaged parts that may need to be replaced. Remember that even small air compressors can generate a significant amount of pressure, so be mindful of the risk of explosion, and work in a well-ventilated area.
By taking these necessary precautions, you can ensure that you’ll be safe while working on your air compressor. In short, always remember that safety is a crucial aspect of rebuilding an air compressor and should never be compromised.
Wear protective gear, unplug the compressor, and release pressure
Safety is of the utmost importance when it comes to using a compressor. Before doing anything else, it is crucial to wear protective gear to avoid any accidents. This means wearing gloves, safety glasses, and appropriate clothing to cover your body.
Once you are suited up, it is important to unplug the compressor to ensure that it is powered off and cannot start unexpectedly. Then, you should release the pressure remaining in the compressor to avoid any potentially dangerous situations. By following these steps, you can minimize the risk of accidents and injuries, ensuring a safe and productive use of your compressor.
Always remember, safety should never be compromised for convenience or speed.
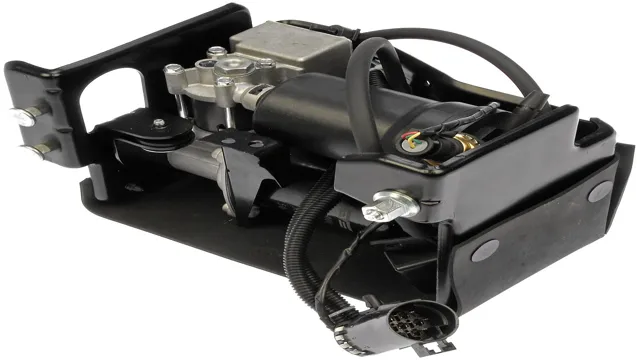
Step 2: Disassembly
Once you have gathered all the necessary tools and replacement parts, it’s time to disassemble your air compressor. Start by unplugging the unit and opening the drain valve to release any built-up pressure. Remove the pressure switch, the motor, and the compressor head.
Inspect all the components carefully, paying close attention to any signs of damage, corrosion, or wear. Use a wire brush or sandpaper to clean the parts thoroughly and apply lubricant to the moving components. Take note of any parts that need to be replaced and order them as soon as possible.
Don’t forget to label and organize all the parts that you remove to make reassembly much easier. With the compressor fully disassembled and all the parts cleaned and inspected, you’re now ready to move on to the next step in rebuilding your air compressor.
Remove the cover, motor, pump, and other components
In order to repair or maintain a water pump, you need to first disassemble it. The second step in this process is to remove the cover, motor, pump, and other components. This can be a bit tricky, so make sure to take your time and carefully follow the manufacturer’s instructions.
You’ll likely need a few tools to complete this step, such as a screwdriver, pliers, and wrenches. Once you’ve removed the necessary components, you can start to inspect and clean them. Be sure to check for any signs of wear and tear, damage, or corrosion.
If you notice any issues, you may need to replace certain parts. Remember, it’s important to take your time during the disassembly process to avoid causing damage or making mistakes. With patience and attention to detail, you can successfully take apart a water pump and keep it running smoothly for years to come.
Step 3: Inspection
Now that we’ve disassembled the air compressor and ordered the necessary replacement parts, it’s time to move onto the next step of the rebuilding process: inspection. This is a critical step in ensuring that your air compressor is safe to use and will perform optimally. Take a close look at each component, checking for any signs of wear and tear, cracks, or other damages.
Pay special attention to the piston rings, connecting rods, and bearings. Bearings, in particular, should be thoroughly inspected as they can wear down over time and cause significant damage to the compressor if not replaced. Any damaged or worn parts should be replaced with new ones to ensure the longevity and proper functioning of the unit.
Once the inspection is complete, we can proceed with the rebuilding process, confident in the knowledge that our air compressor will run smoothly and efficiently.
Check parts for wear, damage, and debris build-up
During the inspection process, it’s imperative to check every part of the machinery for wear, damage, and debris accumulation. This could include gears, belts, chains, and other moving parts. Don’t overlook any nooks or crannies as debris build-up can lead to serious issues down the road.
If you notice any signs of excessive wear, cracks, or breakage, it’s crucial to replace those parts immediately. Neglecting to replace worn or damaged parts can lead to system failure, which could be both costly and dangerous. Think of it as taking your car in for a check-up, you wouldn’t want to continue driving with a broken belt or worn tires.
The same principle applies to industrial machinery. By regularly inspecting and replacing damaged parts, you’ll extend the life of the machinery and ultimately save money in the long run.
Replace any damaged or worn parts, clean debris build-up
Once you’ve removed any visible debris from your equipment, it’s time to move on to the next step – inspection. Inspecting your equipment is crucial for ensuring it’s operating at its best, which means you need to be thorough. Look for any damage or wear on parts that may need to be replaced, such as belts, hoses, or filters.
Not addressing these issues could lead to more significant problems down the line, so it’s important to take the time to inspect all aspects of your equipment. Additionally, be sure to clean any debris build-up you come across during the inspection. This not only helps the machine run better, but it also makes it safer for operators to use.
By taking the time to inspect and clean your equipment, you’re prolonging its lifespan and saving yourself money in the long run. Remember, a little maintenance goes a long way!
Step 4: Reassembly
Now that you have thoroughly cleaned all the parts of your air compressor, it’s time to start the reassembly process. Start by putting the oil seal back into place, followed by the bull gear and the drive gear. Then, place the back cover onto the compressor and use a screwdriver to secure it tightly.
Next, put the cylinder back into place, making sure it’s flush with the housing. Slide the piston back into the cylinder and secure it tightly. Finally, put the head and the valve plate back into place, making sure all the bolts are tightened.
Make sure to double-check all of the parts before turning on the compressor to ensure that everything is functioning properly. Congratulations, you have successfully rebuilt your air compressor and saved money on a repair!
Put the parts back together in correct order
Reassembling the parts in their correct order is crucial in bringing your device back to life. Before proceeding, make sure to consult the manual or take note of the disassembly steps to ensure that you will not miss or mix any parts. Start by cleaning the parts if necessary to remove dirt, dust, or old adhesives that may affect the performance of the device.
Then, carefully fit in the parts one by one, making sure that they are in the correct position and alignment. Use the right tools and fasteners as indicated in the manual to secure the parts in place. Take your time and do not force the parts if there is resistance.
A misaligned or damaged part can cause malfunction, so double-checking is necessary. Reassembly requires careful attention to detail to bring your device back to its functioning state.
Reattach cover, motor, and pump
After successfully replacing the damaged parts, it’s time to reassemble your washing machine. The next step involves carefully placing the cover back on top of the machine. Make sure to align it properly with the body of the washer.
Before you proceed with attaching the motor, ensure that the motor’s rubber bushings are in the correct position. Once you have done this, position the motor back in place and connect the electrical connections. The last and final step involves fitting the pump back into its housing.
It’s crucial to ensure that the impeller aligns with the drive shaft before you fasten it. Once everything is in its place, fasten everything securely to make sure there’s no rattling when the machine is working. After reattaching all the components, connect the power and water supply, and turn on the washing machine.
Watch the machine closely to make sure everything is running smoothly, so you can complete your laundry without any issues. Overall, reassembling your washing machine after repairing a problem like a damaged pump or motor can seem challenging, but, with a little care and attention, it can be relatively straightforward. Taking it one step at a time and ensuring that everything is correctly aligned and in the right place is key.
So, roll up your sleeves and get ready for a rewarding DIY repair experience!
Step 5: Testing
After the rebuilding process is complete, it’s time to test your air compressor. Before turning it on, make sure everything is hooked up correctly and all fasteners are tightened. It’s essential to follow the manufacturer’s instructions when testing, as each compressor model can differ.
In general, you will want to turn on the power button and allow the compressor to run for at least fifteen minutes to allow the oil to circulate. During this time, be sure to listen for any unusual sounds, vibrations, or leaks. If you notice anything unusual, turn off the compressor immediately and address the issue before continuing.
Once you’ve completed the testing, you can use the air compressor for its intended purposes. Remember to always use personal protective equipment, including gloves, eye protection, and hearing protection, to stay safe while operating the compressor.
Plug the compressor, start and test to ensure it’s working correctly
Once you’ve connected your compressor to the power source and checked for any leaks, it’s time to test it out to ensure everything is working correctly. Start by plugging in your compressor and turning it on, being sure to follow any specific instructions from the manufacturer. Keep an eye on the pressure gauge and make sure it’s rising as expected.
If you notice any unusual noises or vibrations, immediately turn off your compressor and investigate the issue further. It’s always better to be safe than sorry when it comes to equipment that can be potentially dangerous. Once you’re happy with the initial test, it’s a good idea to put your compressor through its paces by using it for a variety of tasks.
Give it a good workout and make sure it’s up to the task before you start relying on it regularly. Congratulations, you’re now ready to let your compressor do the hard work for you!
Conclusion
In conclusion, rebuilding an air compressor is like giving new life to an old friend. It’s a fun and rewarding process that allows you to not only save money, but also gain a better understanding of how your compressor works. With a little elbow grease and some basic knowledge, you can breathe new life into your beloved air compressor and have it running like new in no time.
So don’t be afraid to get your hands dirty and start your rebuilding adventure today!”
By following these steps, you can easily rebuild your air compressor and extend its lifespan.
After rebuilding your air compressor, it’s essential to carry out some tests to ensure it’s functioning correctly. Firstly, you should visually inspect the air compressor for any leaks or loose connections. Then, power up the device and check the pressure gauge to verify the output pressure matches the predetermined setting.
If the pressure is too high or low, you’ll have to adjust the regulator to the correct level. To validate the air compressor’s performance, you can engage the motor and listen to the unit as it operates. An unsteady sound may indicate an issue with the bearings or a misaligned pulley.
Finally, switch off the machine, allow it to cool, and test for any residual pressure by using the drain valve. Performing these tests will ensure that your air compressor is running smoothly and efficiently, extending the lifespan of your rebuilt unit.
FAQs
What are the common signs that an air compressor needs to be rebuilt?
The common signs include oil leaks, reduced airflow, strange noises, and high oil consumption.
How often should an air compressor be rebuilt?
It depends on the usage and maintenance of the compressor, but on average, it should be rebuilt every 3-5 years.
Can I rebuild my air compressor myself?
It is possible to rebuild an air compressor yourself, but it requires knowledge of the compressor’s mechanisms and specialized tools.
How much does it cost to rebuild an air compressor?
The cost varies depending on the type of compressor and the extent of the damage, but it can range from $200 to $1000.
What should I do before rebuilding my air compressor?
Before rebuilding, make sure to gather all the necessary tools and replacement parts, perform a thorough inspection, and follow the manufacturer’s guidelines.
How long does it take to rebuild an air compressor?
It depends on the complexity of the compressor and the extent of the damage, but it can take anywhere from a few hours to several days.
Can I prevent the need to rebuild my air compressor?
Yes, regular maintenance and proper usage can prevent the need for a full rebuild and prolong the lifespan of the compressor.