How to Tell if Your Air Compressor is Bad: Signs and Symptoms

Is your air compressor acting up? If it feels like your tools are struggling, or you’re not seeing the usual performance you’re used to, there’s a strong chance that your air compressor could be the culprit. Air compressors are an essential part of any workshop or construction site, providing vital power to the tools we rely on. But when they start to break down, the consequences can be significant.
Not only can a faulty air compressor limit your capabilities, but it can also put your safety at risk. The good news is that spotting a bad air compressor is relatively straightforward. While there can be a few different symptoms, some of the most common include leaking oil or air, a sense of excessive vibration, or a noticeable drop in performance.
But what do these issues mean, and how can you tell if your air compressor is beyond repair? In this blog post, we’re going to explore everything you need to know about bad air compressors. From diagnosing common symptoms to exploring the best solutions, we’ll help you fix your compressor and get back to work in no time. Whether you’re a seasoned professional or a DIY enthusiast, it’s crucial to keep your air compressor in tip-top shape.
So, if you’re experiencing any issues, keep reading to find out more.
Symptoms of a Bad Air Compressor
Air compressors are an essential tool in many workshops, but they can develop problems over time. If you’re wondering how to tell if your air compressor is bad, there are several symptoms that you should look out for. The first sign of trouble is a decrease in the amount of air pressure that the compressor can provide.
This could be due to low oil levels or damage to the compressor’s internal components. Another common symptom is excessive noise, which could be caused by worn out parts or loose fittings. You may also notice leaks in the air lines or water in the tank, which could indicate a problem with the compressor’s cooling system.
If you experience any of these issues, it’s important to get your air compressor checked as soon as possible to avoid costly repairs down the line. So, keep an eye out for these symptoms to ensure that your air compressor is running smoothly and efficiently.
Decreased Performance
If you notice your air compressor not working the way it used to, it could be a sign of a bad compressor. One of the clear symptoms of a bad air compressor is decreased performance. Your compressor may take longer to build up air pressure, it may not hold air pressure as well, or it may produce less air pressure overall.
These performance issues can stem from a range of problems, including worn-out parts, leaks, or issues with the motor. The longer you ignore these issues, the more severe they can become and the higher the risk of damage to your compressor. If you catch the problem early, you may be able to fix it by replacing faulty parts or tightening connections.
However, if the problem has gone on for too long, you may need to replace your compressor altogether. Don’t let a bad air compressor compromise your work – stay vigilant for signs of decreased performance and take action as soon as possible to keep your air compressor in top shape.
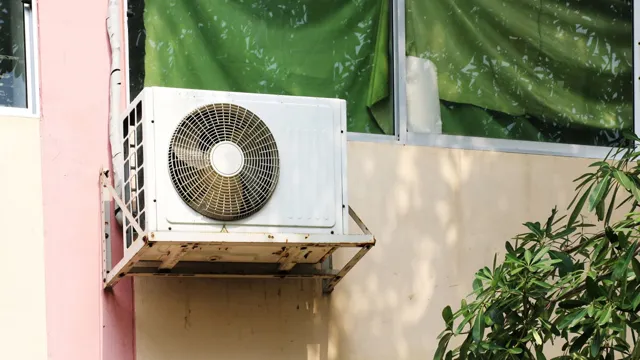
Loud or Unusual Noises
As an air compressor ages, it may start to exhibit some alarming symptoms that indicate it’s on its way out. One of the most common and noticeable symptoms is loud or unusual noises. If you hear your compressor making noises louder than its usual operating hum, it’s a sign that something is wrong.
The noise could be due to a damaged bearing, loose parts, worn-out motor components, or a leak in the air system. Ignoring these symptoms could lead to serious damage to your air compressor, and that’s why it’s crucial to act swiftly and rectify the problem. Don’t let a small noise turn into a big headache and take action immediately by hiring a professional repair service.
They can diagnose the problem quickly and fix it before it spirals out of control, saving you from potentially costly repairs and replacements. So, if you hear strange sounds coming from your air compressor, don’t wait; get it checked out right away to keep your equipment running smoothly.
Leaking Oil or Air
If you own an air compressor, it’s essential to keep an eye out for any signs that it might be failing. One of the most common symptoms of a bad air compressor is leaking oil or air. You’ll know something’s not right if you notice hissing or whistling sounds coming from the machine, or if there’s oil dripping from it.
These issues can be caused by a variety of problems, including worn-out seals, improperly tightened fittings, or damaged valves. Neglecting to address these issues can lead to decreased efficiency and increased energy costs. That’s why it’s crucial to address any signs of a bad air compressor as soon as they arise.
So, be sure to keep an eye out for any leaks or unusual sounds, and consult a professional if you’re unsure how to proceed. With a little bit of maintenance, your air compressor can keep working efficiently for years to come.
Testing Your Air Compressor
If you’re wondering how to tell if an air compressor is bad, there are a few signs to look out for. The first thing to check is the overall performance. If your compressor seems to be working harder than usual, or isn’t producing enough pressure, it could be a sign that something is wrong.
Another red flag is if your compressor is making unusual noises, like grinding or hissing sounds. This could indicate a problem with the motor or other internal components. Additionally, if you notice any leaks or damage to the compressor tank or hoses, it’s best to have it inspected by a professional.
In any case, it’s important to regularly perform routine maintenance on your air compressor to keep it running smoothly and catch potential issues before they become major problems.
Check the Pressure Switch
When it comes to testing your air compressor, one important aspect you need to check is the pressure switch. It plays a critical role in turning off the compressor when the pressure in the tank reaches the maximum limit. To test the pressure switch, you first need to disconnect the power supply and release the pressure from the tank.
Then, using a multimeter, check if the switch is functioning properly by connecting the probes to the terminals. If the reading is within the specified range, the pressure switch is working fine. However, if it’s not reading correctly, you may need to replace the switch.
Remember, a faulty pressure switch could lead to over-pressurization, damaging the compressor, or even cause an explosion. Therefore, it’s essential to test the switch regularly to ensure your safety and the longevity of the air compressor.
Inspect the Electrical Connections
When testing your air compressor, it’s important to inspect all electrical connections thoroughly. This involves examining the wiring and ensuring that all connections are securely in place. Loose or damaged connections can cause electrical shorts that may lead to serious damage or even injury.
It’s important to take safety precautions such as wearing protective gear and unplugging the compressor before inspecting the electrical components. If any issues are found, it’s best to have a professional electrician or technician take a look and make any necessary repairs. By regularly inspecting your electrical connections, you can help prevent potential hazards and keep your air compressor functioning properly.
Examine the Motor
When it comes to testing your air compressor, examining the motor is a critical step. The compressor motor is the heart of your air compressor, and it powers the entire machine. So, if the motor isn’t in good condition, your compressor won’t function properly.
To check the motor’s health, start by looking for any visible damage or loose parts. Make sure the motor is clean and free of debris that could cause damage. Next, test the motor’s performance by running the compressor.
Listen for any unusual noises or vibrations, which could indicate a problem. Additionally, check the motor’s amp draw to ensure it’s operating within the manufacturer’s recommended levels. With these steps, you can ensure your air compressor motor is in good working order and will provide reliable operation for your needs.
Fixing an Air Compressor
Air compressors are a vital tool in many workshops and garages, used to power air tools, inflate tires, and perform other functions. But how can you tell if your air compressor is bad and needs to be fixed or replaced? One of the most common signs of a bad air compressor is if it fails to start up, or if it cycles on and off too frequently. Other signs to watch out for include low air pressure, excessive noise or vibration, and leaking oil or air.
If you notice any of these symptoms, it’s essential to address the problem right away to ensure safe and reliable operation of your air compressor. With proper maintenance and care, you can keep your air compressor running smoothly and efficiently for years to come.
Replacing the Pressure Switch
Fixing an air compressor can be a daunting task, but sometimes it’s necessary to replace certain components such as the pressure switch. The pressure switch is responsible for turning the air compressor on and off, making it a critical component. One common issue with pressure switches is that they can get stuck in the “on” position, causing the compressor to continue running even when the desired pressure level is reached.
To replace the pressure switch, start by turning off the compressor and unplugging it from the power source. Locate the pressure switch and remove any wires connected to it. Then, remove the mounting bracket and old pressure switch, and install the new switch in its place.
Reattach all wires and mounting brackets, double-check everything is secure, and turn on the power. With a new pressure switch installed, your compressor should resume normal operation. Remember, safety should always be your top priority when working on any type of machinery, so take your time and make sure to follow all safety guidelines.
Repairing the Motor
If your air compressor’s motor has given up, you might want to try repairing it before investing in a new machine. To begin, disconnect the power and remove the motor’s housing. Check the wiring to see if any connections are loose or burnt out.
Make replacements as necessary and ensure all the wires are firmly connected. If the wiring looks good, then move on to the motor’s bearings. A motor with worn-out bearings will produce a grinding sound or not run at all.
Applying lubrication might solve the problem. However, if the bearings are damaged beyond repair, they need to be replaced. One other common issue is the start capacitor.
A bad capacitor prevents the motor from starting. Use a multimeter to check its functionality and replace it if it’s damaged. With these steps complete, you can put the motor back together and plug it back in to see how it performs.
Repairing a motor can save you a lot of money and add more life to your compressor.
Preventive Maintenance Tips
If you’re wondering how to tell if your air compressor is bad, there are a few signs you can look out for to ensure it’s in good working order. Firstly, check for any unusual noises or vibrations when the compressor is operating, as this could indicate a potential issue with the motor or belt. Additionally, keep an eye on the compressor’s pressure gauge to ensure it’s maintaining consistent pressure levels and isn’t experiencing any drops or fluctuations.
It’s also essential to perform routine maintenance on your air compressor, such as regularly changing the oil and filters, and ensuring adequate ventilation to prevent overheating. By taking preventative measures and addressing any potential issues early on, you can avoid costly repairs or replacement and keep your air compressor operating smoothly for years to come.
Regular Lubrication
Regular Lubrication is one of the most essential preventive maintenance tips that can help keep your machinery or equipment running at optimal performance levels. It involves the application of lubricants to the moving parts of your equipment to reduce friction and prevent wear and tear. Not only does regular lubrication minimize the risk of costly breakdowns, but it also helps extend the operational life of your equipment.
Lubrication is especially important for high-speed machinery and equipment that run at high temperatures, as this can cause the lubricant to break down faster. By ensuring that the right lubricants are being used and that they are applied regularly, you can help keep your equipment in top working order for longer. So, don’t overlook the importance of regular lubrication for your machinery and equipment.
It’s an easy and cost-effective way to maintain optimal performance and prevent premature failure.
Keeping the Air Filters Clean
Keeping the air filters clean is an essential part of maintaining indoor air quality. With regular use, the filters in your HVAC system can get clogged with dirt and debris, which can reduce their effectiveness and increase energy consumption. The best way to keep your air filters clean is to replace or clean them regularly, depending on the type of filter you have.
Disposable filters should be replaced every one to three months, while reusable filters should be cleaned every one to three months, depending on the manufacturer’s instructions. You can also consider upgrading to a high-efficiency filter that captures more dust and allergens. By keeping your air filters clean, you can improve the air quality in your home, reduce energy costs, and prolong the life of your HVAC system.
Draining the Tank Regularly
If you want your car to perform at its best, you need to include draining the tank in your regular preventive maintenance routine. Draining the tank is essential for removing any debris, moisture, and sediment that may have accumulated at the bottom of the tank. Neglecting this task can result in clogging of the fuel filter and damage to the fuel injectors, causing your car to run poorly, bogged down, or even stall out.
To prevent this, it is advisable to drain the tank every 15,000 miles or once a year, depending on your usage. Moreover, make sure that you use a high-quality fuel additive to prevent corrosion and improve the fuel’s performance. Draining the tank can be a DIY task or done by a professional mechanic.
Taking care of your fuel tank will ensure smooth driving and increase your car’s longevity, saving you money in the long run. So don’t neglect your fuel tank and make a habit of draining it regularly.
Conclusion
In summary, the best way to tell if your air compressor is bad is to pay attention to its behavior. Is it making strange noises, leaking oil, or failing to operate at the right pressure? These are all signs that something is wrong. So next time you’re feeling unsure about the health of your air compressor, take a closer look and use your senses to assess its condition.
And remember, if all else fails, just ask yourself: is your compressor feeling a little wheezy? If so, it might be time to trade up and invest in a newer, more reliable model. Happy compressing!”
FAQs
What are the symptoms of a bad air compressor?
The symptoms of a bad air compressor include low pressure or no air output, strange noises coming from the compressor, and air leaks.
How can I check if my air compressor is working properly?
You can use a pressure gauge to check the air pressure output of the compressor. Additionally, listen for any unusual noises or vibrations, and check for any air leaks.
What are the common causes of air compressor failure?
The most common causes of air compressor failure include overheating, wear and tear on internal components, and lack of proper maintenance.
Can a bad air compressor affect other tools in my workshop?
Yes, a bad air compressor can affect the performance of other tools that rely on compressed air. It may cause them to function improperly or not at all.
Should I repair or replace a bad air compressor?
It depends on the extent of the damage and the cost of repair. In some cases, it may be more cost-effective to replace the compressor rather than repair it.
How often should I perform maintenance on my air compressor?
It is recommended to perform maintenance on your air compressor at least once a year, or more frequently if it is used frequently or in a harsh environment.
Are there any safety precautions I should take when working with a potentially bad air compressor?
Yes, always wear appropriate safety gear such as goggles, gloves, and ear protection. Additionally, never attempt to repair or handle a malfunctioning air compressor without proper training and experience.