How to Plumb Air Compressor Lines for Optimal Performance and Efficiency
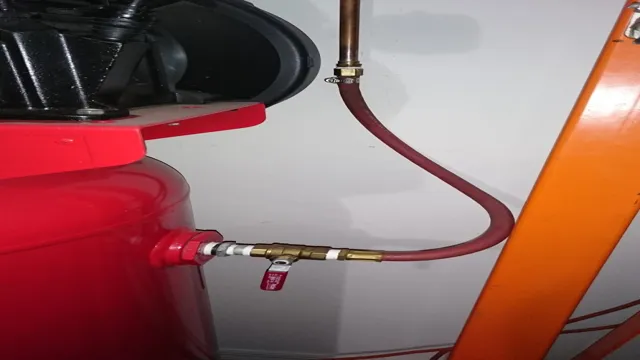
Do you own an air compressor? Are you looking for a reliable guide on how to plumb air compressor lines? Look no further because we’ve got you covered. Plumbing air compressor lines may seem daunting at first, but with the right knowledge and tools, it can be a straightforward task. Think of the air compressor lines as the veins of your compressor system.
They are responsible for transporting air from the compressor to the various pneumatic tools. Hence, a well-plumbed air line system will guarantee maximum efficiency of your tools and will ultimately save you time and money. In this blog, we’ll provide you with step-by-step instructions on how to plumb air compressor lines and the tools needed for the job.
We’ll also give you some tips on how to avoid common mistakes and ensure that your air compressor is functioning at its best. Whether you’re a seasoned DIYer or new to the world of air compressors, by the end of this blog, you’ll be able to plumb air compressor lines like a pro and enjoy uninterrupted use of your pneumatic tools. So, let’s dive in!
Assess Your Needs
If you’re setting up an air compressor system in your workshop or garage, it’s important to assess your needs before plumbing air compressor lines. Consider factors such as the size of your air compressor, the amount of air pressure you need to operate your tools, and the distance between the compressor and where the air will be used. You’ll also want to think about the type of piping you want to use, whether it’s PVC or copper.
Keep in mind that PVC is cheaper and easier to install, but copper is more durable and has a better flow capacity. It’s also important to install a regulator and filter to ensure the air is clean and at the correct pressure for your tools. By evaluating your needs and taking the necessary precautions, you can create a reliable and efficient air compressor system that will power all of your DIY projects.
Identify the Tools and Materials Required
Assess Your Needs Before embarking on any DIY project, it’s essential to assess your needs and determine the tools and materials you’ll require. The first step is to consider the task at hand and the end result you’re aiming to achieve. Next, take into account your skill level and whether you have any previous experience with similar projects.
Once you’ve evaluated your needs, you can begin gathering the necessary tools and materials. It’s important to select quality products that will help you achieve the desired outcome and stand the test of time. Whether you’re working on a small repair job or undertaking a major renovation, planning ahead and assessing your needs will save you time, money, and headaches in the long run.
So take the time to consider your requirements and be sure to invest in the right tools and materials for the job.
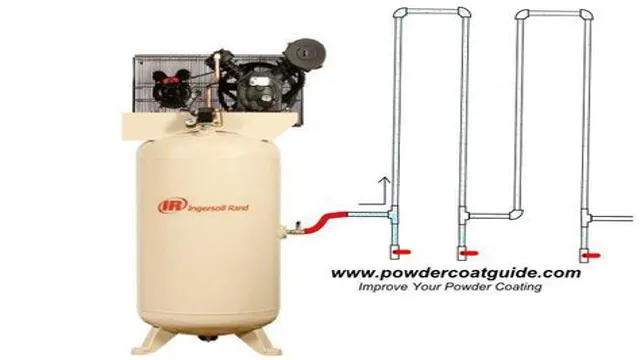
Determine the Layout Approach
When determining the layout approach for your website, it’s crucial to assess your needs. Consider your goals, target audience, and the type of content you’ll be sharing. Are you a business looking to sell products or a blogger sharing personal stories? Will you be using a lot of images or videos? Answering these questions will help you determine the best layout approach for your website.
You don’t want a layout that’s too busy or cluttered, as this can overwhelm your visitors and make it difficult for them to navigate. On the other hand, you don’t want a layout that’s too barebones, as this can come off as unprofessional. Finding the right balance is key.
Remember to keep your website user-friendly and visually appealing, with easy-to-find navigation and clear calls-to-action. This will help keep visitors engaged and increase the chances of them becoming returning customers or readers.
Calculate the Required Hose Length
When it comes to calculating the required hose length, it’s essential to assess your needs. Before you make any purchase, you must determine the job at hand and the distances that need to be covered. Measuring the length and width of your work area can help you determine the total distance that the hose will need to cover.
Additionally, you should take any obstacles, such as corners or objects, into account when selecting your hose’s length. This will help you avoid snagging or tangling your hose during use, ensuring that your work is as efficient as possible. For example, if you need to water plants around a corner or through a small space, you’ll need to purchase a hose that can easily maneuver around these obstacles.
By taking the time to assess your needs and the requirements of your job, you can find the perfect length hose for your task at hand.
Installation Process
If you are wondering how to plumb air compressor lines, the process is not as complicated as you may think. Firstly, you will need to decide on the type of piping system you want to use. PVC piping is an affordable option, but it must be rated for compressed air.
Copper and aluminum piping are both durable options, with aluminum being lightweight and easy to install. Once you have chosen your piping, you can begin to plan how you will run the lines throughout your workspace. It is important to include a shut-off valve near each outlet to regulate the air flow and prevent damage to your tools.
You should also add a moisture separator and an air filter to ensure clean and dry air is running through your system. By taking the time to correctly install your air compressor lines, you can avoid potential damage or malfunctioning in the future.
Install the Regulator and Filter
When installing a regulator and filter, it’s important to first shut off the flow of air to the system. Then, mount the regulator and filter to a secure surface using appropriate hardware. Attach the inlet and outlet ports on the regulator and filter to the corresponding pipes on the system, making sure to use Teflon tape or another sealing tape to prevent air leaks.
Once everything is connected, turn on the air flow and adjust the regulator to the desired pressure. It’s important to regularly check the filter element and replace it if it appears dirty or damaged. By installing a regulator and filter, you can ensure that your pneumatic system runs smoothly and efficiently, protecting your equipment and helping to prevent costly downtime.
Install the Aftercooler and Moisture Separator
If you’re looking to install an aftercooler and moisture separator, it’s important to understand the installation process. The first step is to choose a location where the unit can be securely mounted, taking care to ensure that the air flow won’t be obstructed. Once you’ve identified a suitable location, you’ll need to install the aftercooler and moisture separator by connecting the air inlet and outlet ports to the appropriate compressed air lines.
It’s important to double-check that all fittings and connections are tight, and that there are no leaks. Finally, before using the aftercooler and moisture separator, it’s recommended that you perform a thorough check to ensure that the unit is functioning correctly. This will help to ensure that your compressed air system operates efficiently and without any issues.
With careful installation and proper maintenance, your aftercooler and moisture separator will help to ensure that your compressed air system is free of moisture and contaminants, helping to extend the life of your equipment and reduce maintenance costs.
Install the Air Hose
Installing the air hose is a crucial process to ensure smooth and efficient operation of any air compressor system. It may seem like a simple task, but it requires careful attention to detail. First, locate the port on your air compressor where the hose will be attached.
Then, insert the threaded end of the hose into the port and tighten it using a wrench. Make sure the connection is secure, but avoid overtightening as it may cause damage to the threads. Once the hose is in place, you can connect it to the appropriate air tool using a quick-connect fitting.
Always check for any leaks or damage before using the system. By following these simple steps, you can easily install an air hose and ensure maximum performance from your air compressor.
Connect the Air Compressor
If you’re planning to install an air compressor, connecting it correctly is crucial. The first step is to determine the power source of your compressor. If it is electric, ensure that it’s compatible with your electrical system and is grounded correctly.
If it’s gas-powered, ensure that you have adequate ventilation in the installation area. Next, connect the air intake filter to the compressor unit and connect the pressure switch to the tank and pump. You should also install an air regulator, which is essential in controlling the pressure of the compressed air.
To ensure safety, install a check valve between the compressor and the tank to prevent backflow of air into the compressor. Finally, connect the air hose to the regulator and your desired tool, and your air compressor is ready to go. Following these steps will help you ensure that your air compressor is installed correctly and safely, and you can enjoy its benefits without worrying about any accidents or malfunctions.
Safety Considerations
When it comes to plumbing air compressor lines, safety is of utmost importance. Make sure to carefully read and follow all instructions provided with your air compressor, and wear appropriate safety gear while working. Always use quality, durable materials and fittings that are rated for the pressure and temperature of your system.
It’s also important to properly secure and support your lines to prevent them from sagging or becoming damaged over time. When installing your lines, make sure they are free from bends, twists, or kinks that could restrict airflow or cause them to burst. Regularly inspect your system for signs of wear or damage, such as cracks, leaks, or corrosion, and replace any faulty components immediately to prevent hazardous conditions from arising.
By taking a careful, deliberate approach to plumbing your air compressor lines, you can enjoy efficient, safe operation for years to come.
Wear Protective Gear
When it comes to any activity that may have risks, wearing protective gear is essential. Whether you’re riding a skateboard or working on a construction site, you’re putting yourself in harm’s way. Injuries can happen at any time, and it’s always better to be safe than sorry.
Protective gear can include things like helmets, knee pads, elbow pads, and gloves. By wearing these items, you’re reducing the likelihood of severe injuries should an accident occur. It’s important to make sure that any protective gear you’re wearing fits correctly and is appropriate for the activity you’re doing.
Don’t assume that just because you’re wearing gear that you’re invincible. It’s still crucial to be cautious and aware of your surroundings. Whether you’re an expert or a beginner, safety should always be your top priority.
So, before you head out to your next activity, make sure you have all the proper protective gear. Remember, it’s better to be safe than sorry.
Properly Ground Electrical Components
When it comes to electrical components, proper grounding is crucial to ensure safety. Grounding an electrical device means connecting it to the earth’s conductive surface, creating a path for electrical current to flow safely into the ground. Without proper grounding, an electrical component can become a potential electrocution hazard.
Grounding also protects against electrical shock, power surges, and equipment damage. So, always make sure to follow the manufacturer’s instructions carefully when installing any electrical device and consult with a licensed electrician if needed. Remember, safety is paramount, and a little extra effort in grounding electronic components can prevent serious accidents from happening.
Maintenance Tips
If you’re setting up an air compressor, it’s important to plumb the lines properly to ensure optimal performance. One of the first things to consider is the type of piping you’ll use – copper, PVC, or flexible hoses. Copper is a great option for durability and longevity, but it’s also more expensive.
PVC is a cheaper option but may not last as long. Flexible hoses are a good choice if you’re using your compressor in a mobile setup. Whatever piping you choose, make sure you have the right fittings and connectors to avoid leaks.
It’s also important to consider the size of the piping – larger diameters will allow for more airflow but can also lead to higher costs. Once your piping is set up, be sure to drain any condensation regularly to prevent damage to your compressor and tools. With proper setup and maintenance, your air compressor will operate efficiently and last for years to come.
Regularly Check for Leaks
Regularly checking for leaks is one of the most overlooked yet vital maintenance tips that often goes unnoticed. Leaks have the potential to cause significant damage to your home, possibly leading to costly repairs. It’s crucial to inspect your pipes, faucets, and toilets frequently to check for any visible leaks.
Signs of leaks include water stains, mold growth, and damp areas in your home. A small leak that goes unnoticed can escalate into a larger problem, so it’s essential to fix them as soon as they are detected. Make sure to inspect your plumbing system regularly to detect leaks before they cause long-term damage.
By doing this, you can save yourself a lot of stress, time, and money on costly repairs. Don’t ignore any signs of leakage; instead, contact a professional plumber right away to fix the problem before it gets out of hand. Regularly checking and maintaining your plumbing system is the key to maintaining a healthy and happy home for you and your family.
Keep the System Clean
Regular maintenance is crucial to keep your system running smoothly and efficiently. One important way to do this is by keeping the system clean. This means regularly cleaning all of the system’s components and ensuring that they are free of dust, dirt, and debris.
A clean system not only runs better, but it can also prolong the life of your equipment. One helpful maintenance tip is to schedule routine cleanings at least once a year. You can also make sure that air filters are changed regularly, which can help to improve the air quality in your home and prevent clogs.
Additionally, be sure to check your system’s ventilation and ductwork to ensure that they are clean and free of any blockages. By keeping your system clean, you can ensure that it operates properly and efficiently, while also promoting a healthier living environment.
Schedule Periodic Maintenance
Regular maintenance is essential for keeping your equipment and machinery in top condition. Neglecting routine maintenance can lead to costly repairs and breakdowns, resulting in unwanted downtime. To ensure that your machinery stays in tip-top shape, schedule regular maintenance checks and adhere to the manufacturer’s recommended service intervals.
Regular maintenance includes checking fluid levels, inspecting belts and filters, lubricating moving parts, and replacing worn parts. Failing to take care of these simple tasks could result in a major malfunction or even an accident. So, prioritize regular maintenance as it will save you from costly repairs and keep your machinery running effectively.
Remember, prevention is always better than the cure!
Store the Compressor Properly
When it comes to maintaining your compressor, how and where you store it matters. Proper storage can significantly extend the lifespan of your machine. Always store your compressor in a dry, temperature-controlled environment that is away from direct sunlight and moisture.
Make sure the space you store it in is well-ventilated. Before storing, clean the machine and ensure it is fully drained of any fluids. Cover it with a thick, breathable cloth to protect it from dust and other debris.
It’s also essential to store it in a place where it won’t be knocked over or subjected to vibrations and shock. Taking these steps ensures that your compressor is ready to be used when you need it and will operate efficiently. Remember, proper storage is a crucial part of maintenance, and it pays dividends in the long run.
So, take care of your compressor, and it will take care of you!
Conclusion
In conclusion, plumbing your air compressor lines may seem overwhelming at first, but with the right tools and techniques, it’s actually quite simple. Just remember to use high-quality pipes and fittings, properly secure all connections, and plan your layout strategically to minimize pressure drops and maximize efficiency. And if all else fails, just turn to the professionals – because sometimes, leaving it to the experts is the wittiest and cleverest decision you can make!”
FAQs
What size air compressor lines should I use for plumbing?
The size of the air compressor lines you should use for plumbing depends on the size of your air compressor and the tools you’ll be using. Generally, it’s recommended to use 3/8″ or 1/2″ lines for most applications.
How do I connect air compressor lines to the compressor?
To connect air compressor lines to the compressor, you’ll need to use appropriate fittings and connectors. Make sure to follow the manufacturer’s instructions and secure all connections properly.
Can I use PVC pipe for air compressor lines?
No, PVC pipe is not recommended for air compressor lines as it can’t withstand high pressure and can shatter or burst, causing serious injury or property damage. Use only approved materials such as copper, steel, or aluminum.
How do I install an air dryer in my air compressor line?
Installing an air dryer in your air compressor line involves connecting the dryer between the compressor and the air tool, and following the manufacturer’s instructions for proper installation, use, and maintenance.
How often should I clean my air compressor lines?
You should clean your air compressor lines regularly to prevent buildup of moisture, dirt, and debris that can clog the lines, reduce airflow, and damage the tools. The frequency of cleaning depends on your usage, air quality, and environment, but a general recommendation is every 3-6 months.
What type of oil should I use for my air compressor?
The type of oil you should use for your air compressor depends on the compressor model and manufacturer’s recommendations. Generally, you should use a high-quality compressor oil that meets the industry standards for viscosity, lubrication, and resistance to oxidation and corrosion.
How do I troubleshoot air compressor line problems?
If you experience problems with your air compressor lines, such as low pressure, leaks, or vibrations, you should troubleshoot the system by checking for common causes such as loose or damaged connections, clogged filters, worn-out parts, or improper installation. Some issues may require professional assistance.