How to Properly Set a Torque Wrench: Tips and Tricks for Accurate Tightening
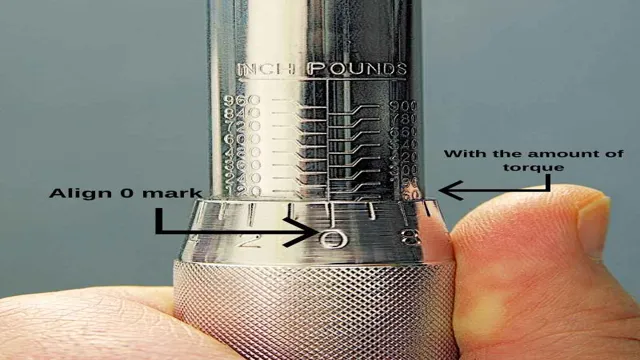
When it comes to automotive work or even simple DIY projects, a torque wrench is an essential tool to have in your arsenal. However, if you’re not properly setting a torque wrench, you could be risking safety hazards or compromising the integrity of your project. Imagine building a piece of furniture, only to have it fall apart because the joints weren’t tightened enough.
Or worse yet, a car part coming loose because it wasn’t tightened to the correct torque specifications. These scenarios are preventable if you know how to properly set your torque wrench. In this blog post, we’ll take a closer look at the importance of torque wrenches, how to properly calibrate them, and how to use them effectively.
Whether you’re a seasoned mechanic or a beginner DIY enthusiast, this information will come in handy for your next project. So, let’s dive in!
Understanding Torque Wrenches
If you’re planning to perform DIY maintenance on your car, a torque wrench is an essential tool to ensure that you’re tightening bolts and nuts to the manufacturer’s specified tightness. The process of setting a torque wrench may seem complicated, but it’s actually quite simple. Firstly, you need to determine the right torque value for the bolt or nut you’re working on.
You can find this information in your car’s owner’s manual or in a catalog of torque values. Once you’ve identified the correct value, adjust the torque wrench accordingly. Tighten the bolt or nut using short, rapid movements until you hear a clicking sound, indicating that you’ve reached the given torque value.
Be careful not to over-tighten the bolt or nut as this may cause it to strip or break. With proper use, a torque wrench can help prevent mechanical problems and keep your car running smoothly. Remember, it’s always better to be safe than sorry!
What is a Torque Wrench?
Torque Wrench Have you ever heard of a torque wrench? Do you know what it is and how it works? Well, a torque wrench is a tool used to tighten bolts or nuts to a specific torque measurement. This is important because over-tightening can cause damage to the bolt or the material being held together, while under-tightening can result in a loose connection that can be dangerous. A torque wrench is designed to ensure that the correct amount of force is applied to achieve the desired level of tightness.
There are different types of torque wrenches, including beam-type, click-type, and digital-type. Each one works in a slightly different way, but they all operate based on the same principle of applying a specific amount of torque. Beam-type torque wrenches use a pointer attached to a beam, while click-type torque wrenches provide an audible “click” sound to let you know when the preset torque has been reached.
Digital-type torque wrenches use electronic sensors and a display screen to read the torque measurement directly. In conclusion, a torque wrench is an essential tool for achieving precise tightening of bolts or nuts. It ensures that the correct amount of force is applied, preventing damage to the bolt or the material being held together, and ensuring a safe and secure connection.
So, if you are looking to tighten bolts or nuts accurately, consider using a torque wrench.
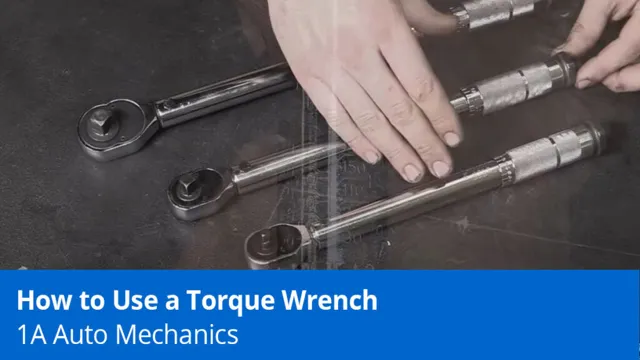
Why is it Important to Use a Torque Wrench?
Torque Wrenches When it comes to tightening bolts and nuts for different applications, not using the appropriate level of force can lead to potential hazards or even equipment failure. This is where torque wrenches come in. A torque wrench is an essential tool for mechanics or anyone who works on machinery and vehicles, as it accurately measures the amount of torque being applied.
Using a torque wrench ensures that the right amount of force is applied to fasteners, preventing any damages and increasing the safety and durability of the equipment being tightened. With different types of torque wrenches available in the market, it is important to choose the right one for your intended application. Depending on your needs, you may require a digital or a click-type torque wrench.
Using a torque wrench may take some time to get used to, but it’s crucial to follow the manufacturer’s instructions strictly to get the most accurate results. Overall, using a torque wrench is an important safety measure that will help prolong the life of your equipment. It’s a small investment with big returns.
Types of Torque Wrenches
If you are working with bolts or nuts, understanding torque wrenches is crucial. These wrenches are designed to tighten fasteners to a specific torque setting to ensure proper fastening without over-tightening, which could damage the hardware or underlying material. There are different types of torque wrenches available, depending on your specific needs.
Beam wrenches are the most common type and work by bending a beam to indicate the applied force. Click or ratchet wrenches are popular due to their ease of use, as they click or release once the torque setting is reached. Digital torque wrenches come with a digital readout, making them easier to read and are preferred for higher level accuracy and precision.
Hydraulic torque wrenches are designed for heavy-duty settings and have a hydraulic pump to precisely adjust torque. Understanding the different types of torque wrenches will allow you to choose the best one to complete your project safely and accurately.
How to Set a Torque Wrench
If you’re working with mechanical or automotive components, having the right amount of torque is crucial to prevent damage or malfunction. A torque wrench is a highly specialized tool that can ensure the precise torque required for each fastener, but setting it up correctly is essential. To properly set a torque wrench, make sure to select the correct torque value according to the manufacturer’s specifications.
Then, adjust the handle or digital display until it reaches that value, making sure to avoid over-tightening or under-tightening. It’s also important to use the right technique when applying torque to avoid turning the wrench in a way that could affect its accuracy. By taking these simple steps, you can accurately set your torque wrench and ensure optimal performance of your machinery or vehicles.
Step 1: Calibrating Your Wrench
Calibrating a torque wrench is the first and most crucial step to ensure a seamless torque tightening process. Over time and usage, torque wrenches can become inaccurate, which makes calibration essential. Firstly, identify the range of your torque wrench, which is displayed on the handle or packaging.
Secure your tool in a vise or against a solid surface. Attach the proper torque calibration equipment to the end of the wrench, and rotate the tool to zero. Next, apply load force onto the tool slowly and steadily, then return the wrench to zero once it clicks.
Repeat this process until achieving consistent readings and ensure everything meets the manufacturer’s guidelines. This is how to set a torque wrench precisely. Remember to calibrate your torque wrench every 3000 uses or annually to ensure accurate results.
An incorrectly calibrated wrench can lead to tightened screws that are too loose or too tight, leading to safety hazards, damages to the equipment, or both, putting the operator at considerable risk.
Step 2: Choose the Right Socket
When it comes to using a torque wrench, it’s not just about tightening bolts as much as possible. To ensure the correct tension is applied to your bolts, you need to select the right socket. The right socket size will fit snugly onto the bolt head, allowing you to achieve the correct torque without slipping or rounding off the head.
The first step in selecting the right socket is to check the bolt size. Check the size of the bolt head using a socket gauge or a set of calipers. Once you have determined the correct size, choose a socket with the appropriate drive size.
For example, a 3/8″ drive socket should be used with a 3/8″ torque wrench. Using the wrong drive size can cause the wrench to slip or even break. Finally, select the appropriate socket type.
A six-point socket should be used for hex bolts and an eight-point socket for square bolts. By following these simple steps, you can ensure that your torque wrench is properly calibrated to achieve the desired torque on your bolts.
Step 3: Set the Torque Value
When it comes to using a torque wrench, setting the right torque value is crucial. But how do you do it properly? First, you need to consult the manufacturer’s manual or look for the torque specifications of your specific vehicle or equipment. Once you know the target torque value, you can adjust the wrench accordingly.
Most torque wrenches have a scale that you can twist to set the desired torque value, while others have digital displays that allow you to input the exact value. Make sure to set the wrench to the foot-pound or newton-meter unit of measurement as required. Once you’ve set the value, test the wrench on a bolt or nut that doesn’t require specific torque and see if the wrench clicks or breaks as expected.
If it does, you’re all set to start using the torque wrench for its intended task. Just remember to recheck and reset the torque value after every use to ensure accurate and consistent results.
Step 4: Tighten the bolt
When it comes to tightening bolts, it’s crucial to ensure the right amount of torque is applied to prevent damage or accidents. This is where a torque wrench comes in handy. But how do you set it? First, you need to determine the appropriate torque value specified in the manufacturer’s manual.
Then, attach the socket to the torque wrench and align it with the bolt you need to tighten. Twist the handle to adjust the torque level to the desired value, and make sure no other factors affect the reading, such as applying pressure or using extensions, as they can skew the results. Once the desired value is set, place the wrench on the bolt and steadily apply the required force until you hear or feel a click.
This click signifies that the bolt has been adequately tightened to the specified torque value. By using a torque wrench, you can ensure that your bolts are securely fastened without the risk of overtightening or undertightening, leading to potential risks.
Step 5: Retighten the bolt
Setting a torque wrench can be perplexing, but the process can be broken down into steps. After selecting the right torque value based on your equipment’s specifications, line up the wrench with the bolt. Press down on the wrench until you hear a click, indicating that the torque value has been reached.
Make sure to hold the wrench steady until the click so the torque value is set correctly. After it clicks, double-check the torque value has been set to avoid overtightening or undertightening. Retighten the bolt by turning it clockwise using the wrench.
Repeat the process for each bolt. Remember, a torque wrench is essential for precision and preventing damage to your equipment, so it’s worth taking the time to ensure it is set correctly.
Tips for Using a Torque Wrench
If you’re working on your car or bike, you probably know how important it is to have the right torque on your nuts and bolts. Using a torque wrench can help ensure that everything is tight and secure. However, if you don’t set the torque wrench properly, you might not get the results you’re looking for.
Here are a few tips on how to properly set a torque wrench: First, make sure you know the proper torque specs for the bolts you’re working on. Then, set the torque wrench to the desired amount, usually by rotating the handle until you reach the correct setting on the scale. When tightening the bolt, make sure you go slow and steady, applying force in a smooth, controlled manner.
Finally, double-check the torque with a torque angle gauge if necessary. By following these steps, you can ensure that your wrench is set correctly and that you’re tightening your bolts to the proper torque specifications.
Warning Signs of Over-Tightening
Using a torque wrench can be a game-changer when it comes to ensuring your bolts and nuts are tightened to the right amount. However, over-tightening can lead to damaging threads, bolts, and even the parts being held together. Therefore, it is crucial to know the warning signs of over-tightening, such as stripped threads, bolt heads deforming, or cracking.
Maintaining knowledge of these signs can help prevent any unnecessary failures. When using a torque wrench, follow the manufacturer’s recommendations on the appropriate torque setting and ensure the tool meets the specification. Remember to always use an appropriate torque conversion chart when changing from one measure of torque to another, such as pounds to Newton-meters.
With these tips and knowledge, you can safely and effectively use a torque wrench for your needs.
Regular Maintenance
Regular maintenance of your torque wrench is essential to ensure accuracy and prolong its lifespan. Here are a few tips to make sure you are using your torque wrench correctly. Firstly, make sure it is calibrated before each use.
This will guarantee that the torque readings are accurate. Secondly, use the correct setting for the job at hand. Applying too much torque or too little can cause damage.
It’s better to err on the side of caution and go with the lower setting if you are unsure. Lastly, store your torque wrench in a safe place and keep it clean. Dust and debris can accumulate, which can affect the accuracy of your readings.
By following these simple tips, you can keep your torque wrench in tip-top condition and ensure your projects are completed precisely and safely.
Using an Extension
If you’re using a torque wrench, it’s critical to use the right extension to avoid damaging the tool or your workpiece. To begin with, make sure you select the appropriate extension for the task at hand, which is usually specified by the manufacturer. Additionally, if you’re tightening bolts or nuts in confined spaces, using an extension may seem like a good idea, but it can add to the amount of torque required, especially if the extension is lengthy.
Furthermore, you should stop using an extension when it exceeds the recommended torque rating, as it can raise the likelihood of over-tightening or breaking a component. Finally, it’s essential to double-check the connection between the wrench, extension, and socket to ensure that everything is tight and secure before using the torque wrench. By following these pointers, you can confidently use an extension and ensure that your torque wrench operates effectively and safely.
The key is to keep in mind that accurate torque readings are essential in any application, and using the right extension is critical for achieving that goal.
In Conclusion
In summary, setting a torque wrench is like finding the perfect balance between your ex-partner’s nagging and your current partner’s understanding. Both have their place and can be useful, but too much or too little can lead to disaster. So, always consult your manufacturer’s recommendations and use the proper technique to ensure your bolts are tightened just right.
Trust us, your future self and your project will thank you!”
FAQs
1. What is a torque wrench and how does it work? A: A torque wrench is a tool used for tightening bolts or nuts to a specific torque value. It works by applying a predetermined amount of force to the fastener being tightened. 2. What units of measurement are used for torque wrenches? A: Torque wrenches can be calibrated and used in different units of measurement, such as foot-pounds, Newton-meters, inch-pounds, or kilogram-meters. 3. Why is it important to use a torque wrench? A: Using a torque wrench ensures that bolts or nuts are tightened to the correct specifications, preventing under- or over-tightening that can lead to damage or failure of the fastener or the object being secured. 4. What are some common mistakes to avoid when using a torque wrench? A: Some common mistakes include using the wrong unit of measurement, not calibrating the wrench correctly, using the wrong socket size, or applying force to the handle instead of the square drive. 5. How do I properly calibrate a torque wrench? A: To calibrate a torque wrench, you should use a torque tester that is calibrated to a known standard. Apply the wrench to the tester and adjust it until it reaches the desired reading. 6. Can I use a torque wrench for loosening bolts or nuts? A: No, torque wrenches should not be used for loosening fasteners. Doing so can damage the wrench and affect its accuracy. 7. How often should I calibrate my torque wrench? A: It is recommended to calibrate your torque wrench at least once a year, or more frequently if it sees heavy use. Additionally, you should recalibrate the wrench if it is dropped or otherwise damaged.