How Air Compressors Are Classified: A Comprehensive Guide to Understanding the Different Types
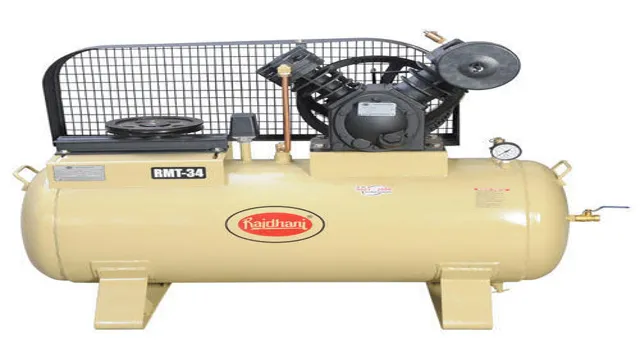
Have you ever wondered about the different types of air compressors available in the market? Air compressors vary in size, shape, and performance, making them suitable for a wide range of applications. Understanding the classification of air compressors can help you choose the right type for your specific needs. In this blog post, we will explore the various classifications of air compressors, providing you with the necessary information to make an informed purchase decision.
So, fasten your seatbelt and get ready to dive into the world of air compressors.
Introduction
Air compressors are classified based on different factors like size, power source, and application. The size of an air compressor is usually determined by the volume of air it can compress. Generally, compressors are classified into three categories: small, medium, and large.
A small air compressor is portable and ideal for DIY projects and small-scale applications. Medium compressors are suitable for small workshops, while large compressors are used in factories, workshops, and other industrial settings. Air compressors can also be classified based on their power source, with electric, gas-powered, and diesel-powered compressors being the most common types.
Another significant factor used in classifying air compressors is their application. For instance, medical grade air compressors are used in hospitals, while industrial compressors are used for powering pneumatic tools and machinery. Overall, understanding the different classifications of air compressors can help you choose the most suitable compressor for your specific needs.
What is an Air Compressor?
An air compressor is a machine that compresses air and then stores it in a tank to be used later. These machines are widely used in various industries, and they come in different shapes and sizes based on their intended uses. For instance, some air compressors are very small and portable, making them a handy tool for DIY enthusiasts.
Others are large and industrial-sized, providing the necessary power for heavy-duty applications. An air compressor typically consists of a motor, pump, and a tank. When the motor turns on, it pumps air into the tank and compresses it, creating potential energy that can be used later.
Once compressed, the air can be released from the tank through a hose and used for various tasks like powering tools. Overall, air compressors are essential devices that make work easier in many different industries.
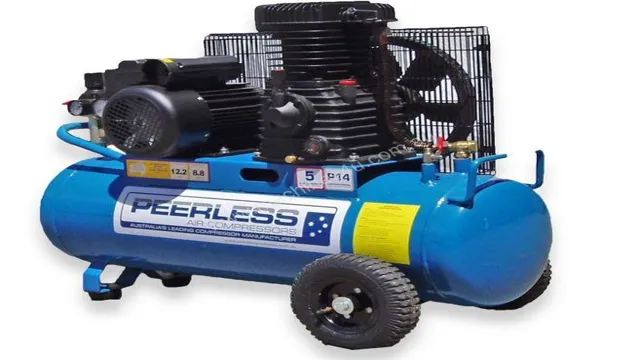
Why is Air Compressor Classification Important?
“air compressor classification” Introduction: Air compressors come in a variety of types and sizes, and selecting the right one for your needs is crucial. There are numerous factors to consider when selecting an air compressor, such as what it will be used for, how frequently it will be used, and even where it will be located. One of the most important factors to consider when selecting an air compressor is its classification.
By understanding the different classifications of air compressors, you can make a more informed decision about which one will work best for you. So why is air compressor classification so important? Let’s dive in and find out. Air compressor classification serves as a guide for selecting the right type of compressor based on its intended application.
The primary purpose of an air compressor is to increase the pressure of air by first reducing its volume. Depending on the application, air compressors may be classified by their design, operating principle, and performance characteristics. The classification of an air compressor has a significant impact on its ability to perform effectively and efficiently in its intended environment.
Understanding the classification of air compressors is particularly important when it comes to workplace safety. Different types of air compressors may require unique safety measures, and selecting the wrong type may result in equipment and product damage, injuries, and even fatalities.
Air Compressor Classification Systems
Air compressors are classified based on various criteria such as their design, operation, drive system, and the type of gas or air they compress. The most common classification is based on their design, which includes reciprocating, rotary screw, rotary vane, and centrifugal compressors. Reciprocating compressors use a piston or diaphragm that moves back and forth to compress the air into a cylinder.
They are best suited for low or medium airflows that require high pressures. Rotary screw compressors use two interlocking helical screws to compress the air. They are ideal for continuous operation at higher flow rates.
Rotary vane compressors use a rotor with vanes that slide in and out of a cylindrical chamber to create pressure. They are efficient for low or medium airflows at a moderate pressure. Centrifugal compressors operate at high speeds and use centrifugal force to compress the air.
They are best suited for large airflows at lower pressures. Understanding the classification systems can help you choose the right compressor for your specific needs.
Based on Operation Mechanism
Air compressors are classified according to their operation mechanism, and each type serves a different purpose. Firstly, there’s the reciprocating compressor, which compresses air by forcing it into a chamber with a piston. This type is excellent for high-pressure applications and intermittent use.
Secondly, there’s the rotary screw compressor, which compresses air using two meshing rotors that drive it down a chamber. This type is ideal for continuous use and low-pressure applications. Lastly, there’s the centrifugal compressor, which compresses air through centrifugal force.
This type is best suited for large-scale applications, such as power plants and industrial sites. Understanding the benefits and limitations of each type is crucial in selecting the right air compressor for your business or personal use. These classification systems help consumers make informed choices when purchasing air compressors, ensuring their needs are met effectively.
Based on Design
Air Compressor Classification Systems are based on design and manufacturers classify compressors according to their design. The most common classification system includes oil-lubricated and oil-free compressors. Oil-lubricated compressors are designed to handle high-pressure tasks and need oil lubrication to function smoothly.
Meanwhile, oil-free compressors are much easier to maintain, as they do not require oil lubrication, and offer a cleaner air supply for sensitive applications such as dental offices or laboratories. Another classification system is based on the number of compression stages within an air compressor system. A single-stage compressor compresses air in one stroke, while a two-stage compressor compresses air in two stages, offering a higher level of efficiency.
When choosing the right compressor system for your needs, it’s important to consider factors such as price, energy efficiency, maintenance requirements, and the specific tasks that the compressor will be used for.
Based on Power Source
Air compressor classification systems are determined by their power source. The three main classifications are electric-powered, gas-powered, and diesel-powered air compressors. Electric-powered air compressors are the most common and are suitable for indoor use.
They are quiet, adjustable, and require minimal maintenance as they have fewer moving parts than gas-powered compressors. Gas-powered air compressors are suitable for outdoor use and areas without electricity. They are often used in construction sites and can generate a higher PSI than electric-powered compressors.
Diesel-powered air compressors are the most heavy-duty and powerful. They are commonly used in industrial settings and construction sites where a large volume of compressed air is required. The power source of an air compressor is an important consideration when selecting the right tool for the job.
Examples of Air Compressor Classifications
Air compressors can be classified in different ways based on various factors. One of the most common ways air compressors are classified is based on their power source. Electric air compressors are powered by electricity and are generally used for small to medium-sized tasks.
Whereas, gasoline or diesel-powered air compressors are used for larger tasks, where electricity is not readily available. Another way air compressors are classified is by their design, which includes two major types: reciprocating air compressors and rotary screw air compressors. Reciprocating air compressors are the simpler and more traditional type, whereas rotary screw air compressors have more complex components.
Additionally, air compressors can be classified based on their performance ratings, such as pressure, flow rate, and horsepower, which determines their suitability for specific applications. Understanding how air compressors are classified can help you choose the right one for your needs.
Reciprocating Air Compressors
Reciprocating air compressors are just one of the many classifications of air compressors. These types of compressors operate by using a piston, which moves back and forth within a cylinder. This creates a vacuum that draws in air, which is then compressed and sent through the discharge valve.
Reciprocating air compressors can be used for a variety of applications, such as pneumatic tools, spray painting, and air conditioning, among others. They come in both single-stage and two-stage models, which differ in the number of times air is compressed before being sent through the discharge valve. Single-stage compressors are typically used for smaller tasks, while two-stage compressors are better suited for larger applications.
Rotary Screw Compressors
Rotary screw compressors are a common type of air compressor that is used in various industries. These compressors use a positive displacement method to compress air, where the two spinning rotors compress and then discharge air into a chamber. This process allows for continuous and smooth airflow, making them suitable for high-demand operations.
Rotary screw compressors are suitable for large-scale industrial operations that require high pressurized air, such as manufacturing, mining, and construction. They are known for their energy efficiency, reliability, and durability, making them a wise investment for businesses looking for long-term solutions. Overall, rotary screw compressors are an excellent example of how various types of air compressors can be classified based on their functionality, efficiency, and size.
So, if you’re looking for a reliable and efficient air compressor, rotary screw compressors could be just what you need.
Conclusion
In summary, air compressors can be classified based on their design, capacity, and power source. From reciprocating to centrifugal compressors, from portable to stationary models, and from electric to gasoline-powered units, the options are plenty. However, no matter the classification, all air compressors share a common goal: to turn energy into compressed air for a wide range of industrial, commercial, and personal applications.
So, whether you need to inflate tires, power pneumatic tools, or operate large-scale machinery, there’s an air compressor out there to suit your needs. And if you’re still not convinced, just remember this: air compressors are like a superhero’s cape – they can do wonders with just one swoosh.
FAQs
What is an air compressor?
An air compressor is a device that converts power into potential energy stored in pressurized air.
What are the different types of air compressors?
The main types of air compressors are reciprocating, rotary screw, and centrifugal.
How is a reciprocating air compressor classified?
A reciprocating air compressor is classified by the number of cylinders, the type of cooling system, and the drive system.
What are some common uses of a reciprocating air compressor?
Reciprocating air compressors are commonly used for small-to-medium sized applications, such as powering air tools or inflating tires.
What is a rotary screw air compressor?
A rotary screw air compressor uses two helical screws to compress air and does not require valves like a reciprocating compressor.
How is a rotary screw air compressor classified?
A rotary screw air compressor is classified by the type of oil system, cooling system, and whether it is oil-free or oil-injected.
What are some common uses of a rotary screw air compressor?
Rotary screw air compressors are commonly used for medium-to-large sized applications, such as powering manufacturing machinery or running HVAC systems.