How do I Connect Two Air Compressor Tanks to Increase Efficiency: A Complete Guide

If you own an air compressor and you’re in search of more compressed air storage, combining two air compressor tanks can be a viable solution. However, many people are unaware of how to connect two air compressor tanks correctly. In this article, we’ll guide you through a step-by-step process of connecting two air compressor tanks, so you can increase your air supply.
Whether you’re a DIY enthusiast or a professional mechanic, this post will provide you with all the knowledge you need to get the job done safely and efficiently. So, let’s dive in!
What You’ll Need
If you’re wondering how to connect two air compressor tanks, it’s not as complicated as it might seem. Here’s what you’ll need: two fittings, one for each tank, a compressor hose, and Teflon tape. The first step is to make sure both tanks are completely drained of air and disconnected from any power source.
Then, attach the fittings to the tanks using Teflon tape to ensure a tight seal. Next, connect the compressor hose to one of the fittings and attach the other end to the other tank. Make sure all connections are secure and turn on the power.
The air should flow between the tanks, allowing you to use both as a single, larger tank. This setup can be especially useful if you need more air pressure or a longer run time than a single tank can provide. With these simple steps, you can connect two air compressor tanks with ease.
Air compressor tanks
When it comes to using air compressors, having a tank is crucial for storing pressurized air. But what do you need to consider when choosing a tank? Firstly, think about the size of the tank that you require. This will depend on the amount of air you need to store and how frequently you use it.
You’ll also want to consider the material of the tank, with options ranging from steel to aluminum to composite materials. Additionally, don’t forget to vet the maximum pressure rating of the tank and ensure that it’s compatible with your compressor. Other features like the presence of drain valves and pressure gauges can also be beneficial.
Ultimately, finding a durable, well-made air compressor tank that meets your specific requirements will ensure that you’re able to get your work done efficiently and effectively.
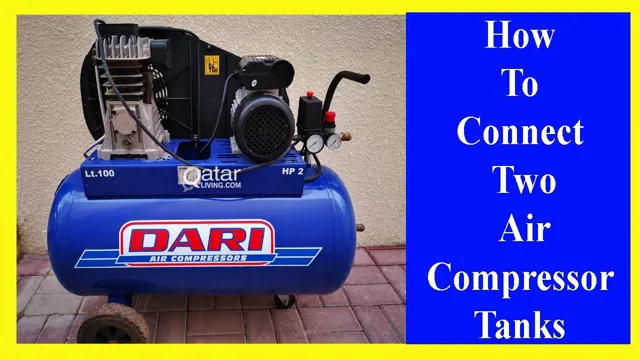
Compressor hose
If you’re planning to use a compressor for your DIY projects or small business, you’ll need a compressor hose to connect it to your tools. These hoses are made from different materials, depending on their intended use and the types of liquids or gases they’ll transport. The materials commonly used for compressor hoses are rubber, PVC (polyvinyl chloride), and polyurethane.
Rubber hoses are durable and can withstand high pressure, while PVC hoses are great for low-pressure applications and are easy to handle. Polyurethane hoses are lightweight and flexible, making them ideal for tasks that require maneuverability. When choosing a compressor hose, consider its length, diameter, and the fittings that will connect it to your compressor and tools.
Also, make sure to choose a hose that matches your compressor’s capacity and the pressure requirements of your tools. By selecting the right compressor hose, you can ensure that your tools will operate efficiently and safely. So, before you start your next project, invest in a quality compressor hose that will help you get the job done.
Pipe cutter
If you need to cut pipes, a pipe cutter is an essential tool to have. There are a few things you’ll need to consider before tackling the project. Firstly, ensure that the pipe cutter is the right tool for the job.
Pipe cutters are best suited for cutting copper, PVC, and other soft metal tubing. If you need to cut harder materials, such as steel or cast iron, a hacksaw or reciprocating saw would be a more appropriate option. Secondly, check the size and diameter of the pipe you need to cut.
Pipe cutters come in different sizes, and it’s important to select the right one for the job. Lastly, ensure that you have a steady hand and a clear workspace to avoid injuries. Overall, if you prepare the appropriate materials and are careful, using a pipe cutter can be an effective and efficient way of cutting pipes.
NPT fittings
If you’re working with piping systems that require high-pressure and high-temperature environments, NPT fittings are an excellent choice. NPT fittings are compatible with many types of tubes, and they can handle much higher pressure than other fitting options. So, what do you need to use NPT fittings in your piping system successfully? Firstly, you’ll need the correct measuring tools such as vernier calipers to determine the dimensions, diameter, and thread size of your piping components.
You’ll also need a torque wrench to tighten the fittings to the correct torque settings, ensuring a tight and leak-free seal. Additionally, you’ll need thread tape or pipe sealant to apply to the threads to prevent leaks and provide a secure seal. And don’t forget safety equipment like gloves, safety glasses, and ear protection to keep you safe while working with these fittings.
With the right tools and equipment, using NPT fittings can be a breeze.
Step 1: Drain and Disconnect
Connecting two air compressor tanks is not as difficult as it may seem. To start the process, you must first drain and disconnect both air compressor tanks. It is important to ensure that there is no pressure in either tank and that they are completely empty before attempting to connect them.
Begin by turning off the power supply and opening the drain valve on each tank to release any remaining air. Once both tanks are drained, disconnect the air hoses or piping from the tanks. This will allow you to inspect and prepare the tanks for connection.
Properly draining and disconnecting the tanks is crucial for safety reasons, so do not skip this step. By following these simple steps, you will be one step closer to connecting your air compressor tanks.
Drain tanks and disconnect from power source
If you’re looking to maintain or repair your tank, the first step is to drain and disconnect it from its power source. This is essential to ensure your safety while working on the tank. To drain the tank, you’ll need to turn off the power supply, open the valves, and let the water flow out.
You can do this by using a bucket to collect the water, or a hose to direct the water to a drain. Once the tank is empty, you can disconnect it from its power source by turning off the circuit breaker or unplugging it from the wall. It’s important to make sure the power is completely disconnected before proceeding with any repairs or maintenance to avoid any accidents.
Remember to always follow the manufacturer’s instructions for draining and disconnecting your tank, as the process may vary depending on the type and model of your tank. By following these steps, you can safely and effectively work on your tank without any disruptions.
Step 2: Cut and Install Pipe
Connecting two air compressor tanks requires patience and precision. Once you have planned your layout and gathered the necessary tools and materials, it’s time to start cutting and installing the pipe. Use a pipe cutter to accurately cut the pipe to the desired length and avoid any gaps in the joint.
Don’t forget to deburr the pipe to ensure a smooth connection. Next, install the pipe into the fitting using sealant or tape to prevent any air leaks. It’s important to ensure that the two tanks are level and secure before connecting the pipe.
Once everything is in place, test the connection by powering on the compressor and monitoring for any unusual sounds or air leaks. Connecting two air compressor tanks may sound intimidating, but with a little patience and attention to detail, anyone can do it.
Use pipe cutter to cut necessary length of pipe
When it comes to installing pipes, one of the essential steps is cutting the pipe to the necessary length. This is where a pipe cutter becomes your go-to tool. A pipe cutter is a handy device used to cut pipes cleanly and accurately.
It’s effortless to use. You simply place the pipe inside the cutter and tighten it until it’s snugly in place. Then, rotate the cutter around the pipe, tightening the cutter a little more after each rotation until you’ve cut through the pipe.
Once you’ve got the right length of pipe, it’s time to install it. Precisely where it goes depends on the specific plumbing project. But, make sure to use the proper fittings, joint compound, and Teflon tape for the best installation.
Overall, with the right tools, cutting and installing pipes is relatively easy to do, making it a DIY project that can save you some money.
Install NPT fittings on both ends of pipe
To continue the process of installing NPT fittings, the next step is to cut the pipe to the desired length and install the fittings on both ends. Firstly, the pipe needs to be measured and marked with a marker or pencil, indicating where it will be cut. A pipe cutter or saw can be used to cut the pipe, making sure to follow the markings precisely.
Once the pipe has been cut, it’s essential to smooth out any burrs or rough edges that may cause damage to the fittings. After that, NPT fittings can be installed on both ends of the pipe, making sure they are tightened securely. It is important to note that NPT fittings are tapered, so they need to be tightened until they snugly fit in the tapered opening of the pipe.
This process helps to ensure a tight seal and prevents any leaks. Checking for any leaks is crucial before using the pipe, so it’s best to run a pressure test to ensure that the fittings are not leaking. In summary, to install NPT fittings on a pipe, one needs to cut the pipe to the desired length, smooth out any rough edges, and install the fittings on both ends.
Step 3: Connect Tanks
Connecting two air compressor tanks is a relatively easy process that involves a few simple steps. To begin, ensure that both tanks are clean and free of debris. Next, locate the outlet valve on each tank and remove any protective caps.
Using a connector fitting, attach one end to the outlet valve on the first tank and the other end to the inlet valve on the second tank. Be sure to tighten the fittings to prevent air leaks. Finally, open the valves on both tanks and wait for them to pressurize.
Once they are fully pressurized, your two tanks are now connected and ready to use. It’s important to note that when connecting multiple tanks, it’s essential to evaluate the maximum pressure rating of each tank to ensure that they are compatible. With these simple steps, you can effectively connect two air compressor tanks and double your air supply capacity.
Attach compressor hose to one tank and NPT fitting on other
In this step, we’ll be connecting the two air tanks by attaching the compressor hose to one tank and the NPT fitting on the other. This is an essential step in setting up your air compressor system, as it allows the tanks to work together to produce the necessary amount of compressed air for your needs. To begin, ensure that both tanks are secured and level on their bases.
Then, take the compressor hose and attach it securely to the designated tank, making sure it is tightened and sealed properly. Once the hose is attached, take the other end and attach it to the NPT fitting on the other tank. A key point to remember here is the importance of using the right NPT fitting for your tanks.
Not all fittings are created equal, so it’s best to check the manufacturer’s recommendations to ensure you’re using the appropriate one for your system. Finally, once everything is securely attached and sealed, turn on your air compressor and allow the two tanks to fill up with compressed air. This process may take some time, so be patient and let the tanks fully charge before using them.
By connecting your tanks using the compressor hose and NPT fitting, you’ll be able to produce the necessary amount of compressed air to power your tools or equipment. With this step complete, you’re well on your way to setting up your air compressor system and getting to work on your projects.
Attach pipe to remaining NPT fittings on both tanks
Now that the tanks are prepared, it’s time to connect them! The third step in the process is to attach the pipe to the remaining NPT fittings on both tanks. This is a critical step to ensure a secure and safe connection between the tanks. It’s important to ensure that the pipe is the appropriate size for the fittings and that it’s tightened properly.
A loose fitting can result in leaks, which would be dangerous and costly. Once the pipe is attached, you can move on to the next step and finish the installation. Remember, taking the time to do this step correctly will save you headaches in the future and ensure that your tanks are functioning properly.
So, don’t rush this step and double-check everything to ensure a worry-free operation.
Step 4: Test Connection
So, you’ve managed to attach two air compressor tanks together and you’re now at the final step, testing the connection. This is an important step as you don’t want to have any leaks that could potentially be dangerous and cause harm. One way to test the connection is to use soapy water.
Apply a mixture of dish soap and water onto all the connections, valves, and accessories. Turn on the compressor and let it run for a few minutes. If you see any bubbles forming around the connections, it means there’s a leak.
Tighten any loose connections and retest. Once you’ve confirmed there are no leaks, you’re all set. You now have a larger compressed air storage system that can power larger tools or equipment.
Congratulations on expanding your compressor system!
Reconnect power and test air pressure in tanks
After making all the necessary connections of the air compressor, it’s time for step 4, where you need to reconnect the power and test the air pressure in the tanks. Reconnecting the power requires caution, and you should ensure your hands are dry before touching any electrical connection. Turn on the power and monitor the compressor for any unusual noises or vibrations that may indicate a problem.
Now, it’s time to test the air pressure in the tanks, which is an essential step before using the air compressor for any work. Attach a regulated air pressure gauge to the outlet valve and turn on the compressor. Wait until the compressor reaches its maximum operating pressure, then check the gauge reading to ensure it matches the recommended pressure outlined in the user manual.
It’s essential to get the pressure right before starting any job to prevent damage to tools and ensure safety. By following these steps, you’ll be ready to start using your air compressor to tackle a range of DIY projects around the house or in the garage.
Conclusion
In essence, connecting two air compressor tanks is a lot like building a bridge between two islands – it requires some precise planning, a bit of mechanical know-how, and a willingness to embark on a DIY adventure. But with the right tools and some determination, you can create a powerful and efficient system that will keep your tools running strong and your projects soaring to new heights. So, whether you’re a seasoned DIYer or just starting out, don’t be afraid to take the leap – with a little ingenuity, you’ll be connecting those tanks like a pro in no time!”
FAQs
What is the benefit of connecting two air compressor tanks together?
Connecting two air compressor tanks can increase the overall air storage capacity, allowing for longer periods of use without having to wait for the compressor to refill.
What materials do I need to connect two air compressor tanks?
You will need a compressor tee fitting, air hose, and appropriate connectors to attach the tanks to the fitting.
Can any air compressor tanks be connected together?
In general, air compressor tanks can be connected regardless of the brand or model. However, it is important to ensure that the tanks have the same maximum working pressure and are compatible with the compressor tee fitting.
How do I determine the proper size for my connected air compressor tanks?
To determine the appropriate size for your connected air compressor tanks, consider the maximum air pressure and flow rate required for your tools and applications. Consult the manufacturer’s specifications or consult with an expert for guidance.
Is it possible to connect more than two air compressor tanks?
Yes, it is possible to daisy chain multiple air compressor tanks together using additional compressor tee fittings and air hoses. However, it is important to ensure that the overall system is properly balanced and can handle the increased storage and output.
Can I connect air compressor tanks of different shapes and sizes?
It is recommended to use air compressor tanks that are of similar shape and size to ensure proper balance and pressure distribution. Connecting tanks that are vastly different in size or shape can cause issues with pressure and flow regulation.
How do I properly maintain my connected air compressor tanks?
Regular maintenance, including draining excess moisture and checking for leaks, is important for ensuring the longevity and efficiency of your connected air compressor tanks. It is also recommended to periodically check the overall system balance and pressure output.