How to Calculate Air Compressor Requirements for Industrial Applications

If you’re in need of an air compressor for your industrial or commercial operation, it’s important to determine the correct size and capacity required. Calculating air compressor requirements can be a daunting task, but it’s crucial to ensure your equipment operates efficiently and effectively. The size and type of compressor needed depends on several factors, including the use of air tools, the number of employees, and the size of the facility.
In this blog, we’ll break down the steps to help you determine the right air compressor for your needs, so you can make an informed decision. Whether you’re a seasoned professional or a novice, we’ve got you covered with this comprehensive guide to calculating air compressor requirements.
Understanding CFM and PSI
When it comes to using air compressors, understanding the terms CFM and PSI is critical. CFM stands for cubic feet per minute and refers to the amount of air flow the compressor can generate. Meanwhile, PSI refers to pounds per square inch and measures the air pressure.
These two measurements together are what determine the compressor requirements for a specific project. To calculate the requirements, consider the tools being used and their CFM and PSI needs. Then, add up the total requirements and select a compressor that meets or exceeds those needs.
It’s important to note that these requirements may vary depending on the nature and complexity of the project. Properly understanding CFM and PSI ensures that your air compressor is effective and meets the needs of your project. So, before you choose an air compressor, take the time to determine your requirements and find the right one for the job.
Explanation of CFM
CFM or Cubic Feet per Minute is a measure of airflow indicating how much air volume is moved through a specific pipe or system in a designated amount of time. PSI, on the other hand, stands for Pounds per Square Inch and measures the pressure of the air being moved. Both CFM and PSI are critical factors for selecting the right air compressor for specific applications.
CFM represents the air volume that flows through air tools while PSI tells you how powerfully that air will come out, making them equally important. Just like how drinking a single cup of coffee won’t have the same effect as an entire pot, airflow produced by an air compressor must match the requirements of your tools for optimal performance. So, it’s crucial to understand the CFM and PSI requirements for your equipment before purchasing an air compressor to ensure you’re getting the right one for the job.
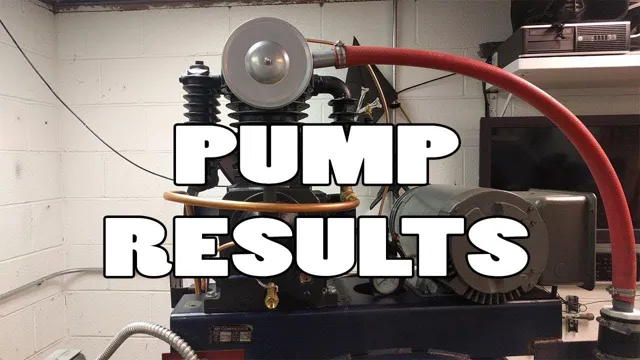
Explanation of PSI
When it comes to power tools, it’s essential to understand the difference between CFM and PSI. CFM stands for Cubic Feet per Minute and is a measurement of a tool’s airflow capacity. Meanwhile, PSI stands for Pounds per Square Inch and is a measure of the tool’s air pressure output.
The two are co-dependent in terms of the tool’s overall performance. CFM determines the volume of air a tool can supply, while PSI determines the force at which the air is delivered. In simpler terms, CFM is like the diameter of a garden hose, and PSI is like the pressure of the water running through the hose.
Just like you wouldn’t be able to fill a pool with a small diameter hose, a power tool with a low CFM rating won’t be able to handle larger projects. Similarly, just like a high pressure hose can deliver water with a lot of force, a power tool with a high PSI rating can deliver air with more force, allowing it to handle tougher tasks. So, it’s crucial to consider both CFM and PSI when selecting a power tool that can meet your specific needs.
Determining Your Air Tool Requirements
If you’re planning to use air tools, you’ll need to figure out how much air pressure and volume your tools require to run properly. To calculate your air compressor requirements, you’ll need to know the CFM (cubic feet per minute) and PSI (pounds per square inch) ratings for each of your air tools. The CFM rating refers to the amount of air that the tool requires to operate at maximum efficiency, while the PSI rating refers to the pressure level needed to operate the tool.
Most air tools require between 70 and 90 PSI, but there are exceptions, so be sure to check the specifications for each tool. Additionally, some tools require more CFM than others, so it’s essential to calculate the total CFM requirement for all of your tools to determine the minimum air compressor size you need. Once you have this information, you can select an air compressor that meets or exceeds your air tool requirements.
By doing so, you’ll ensure that your tools run smoothly and efficiently when you need them most.
Identifying Required CFM and PSI for Each Tool
When it comes to air tools, it’s important to choose the right compressor to power them. Each tool has its own unique air requirement in terms of both CFM (cubic feet per minute) and PSI (pounds per square inch). Without the proper CFM and PSI, your tools won’t function correctly, or may not even work at all.
It’s crucial to identify the requirements of each tool and ensure that your compressor can meet those needs. For example, a pneumatic nailer may only need 2 CFM at 90 PSI, while a sandblaster may require 10 CFM at 100 PSI. If you’re unsure of what your tool needs, consult the manufacturer’s instructions or a professional.
By determining the specific air tool requirements, you can ensure that your compressor can provide enough air power to get the job done effectively and efficiently.
Calculating Total CFM and PSI Requirements
Air tool requirements Before purchasing any air tool, it’s essential to determine the CFM and PSI requirements of your air tools. CFM, which stands for cubic feet per minute, refers to the amount of air that the air compressor can deliver. PSI, which stands for pounds per square inch, refers to the pressure at which air is delivered.
Determining your total CFM and PSI requirements is crucial as it helps to avoid purchasing an air compressor that’s not powerful enough for your tools. Different air tools have varying CFM and PSI requirements, and it’s essential to determine the highest demand among all of your tools. To calculate your total requirements, add the CFM and PSI requirements of each tool, and select an air compressor that meets or exceeds the total requirements.
By doing so, you’ll ensure that your air compressor can power all your tools effectively.
Sizing the Air Compressor
When it comes to calculating the requirements for an air compressor, there are a few important factors to consider. First and foremost, you’ll need to determine your air demands in terms of cubic feet per minute (CFM), which refers to the volume of air needed to power your tools or equipment. Once you have this figure, you’ll need to factor in variables such as altitude, temperature, and humidity, which can all affect the performance of your compressor.
Additionally, it’s important to consider the duty cycle, or how often and for how long the compressor will be running, as well as any potential future expansion plans. By taking all of these factors into account, you can accurately size your air compressor to ensure it meets your needs both now and in the future.
Matching the Compressor with Total CFM and PSI Requirements
When choosing an air compressor, it’s crucial to ensure that you’re getting one of the correct size. You’ll need to match the compressor’s output (measured in cubic feet per minute, or CFM) with the total CFM and PSI requirements of the tools and equipment you plan on using it with. If you have tools with high CFM requirements, you’ll need a larger compressor to keep up with the demand.
It’s also important to consider the pressure rating of the compressor, as not all tools require the same PSI to operate efficiently. You don’t want to end up with a compressor that’s too small or too weak for your needs, as it can lead to frequent breakdowns and costly replacements down the line. Be sure to do your research and consult with a professional before making a purchase to ensure you get the right compressor for your specific needs.
Importance of Compressor Duty Cycle
The importance of compressor duty cycle cannot be overstated when it comes to sizing the right air compressor for your applications. Duty cycle refers to the amount of time that an air compressor can operate at peak performance before it needs to rest. This is crucial because if the compressor is overworked, it can lead to overheating, premature wear and tear, and even complete breakdown.
To avoid this, it is essential that you size your air compressor according to the actual air demand of your applications. This means taking into account variables such as pressure, temperature, and volume requirements. By doing so, you can ensure that your compressor operates efficiently and reliably, without putting undue strain on its components.
So, whether you are a DIY enthusiast or a professional contractor, it is important to choose an air compressor with the right duty cycle to get the job done effectively and safely.
Additional Considerations
When calculating the air compressor requirements for your business or industrial application, there are several additional considerations to take into account. First and foremost, you will want to ensure that you choose a type of compressor that is appropriate for your specific needs, such as a rotary screw or reciprocating compressor. Additionally, you will want to consider the power source and fuel efficiency of the compressor, as well as the duty cycle and run time required for your application.
It is also important to factor in the ambient temperature and altitude of your location, as these can have an impact on the performance of your compressor. Finally, make sure to consider any future expansion plans or changes to your application that may impact your air compressor requirements. By taking into account all of these additional factors, you can ensure that you choose the right air compressor for your unique needs and that it will be able to operate efficiently and effectively for years to come.
Tank size and Portability
When it comes to propane tank size, the main consideration is assessing your fuel usage needs. The larger the propane tank size, the fewer times you’ll need to refill it. However, larger tanks are also less portable, and they may not fit in certain outdoor spaces.
If you’re planning to use propane for outdoor activities, camping trips, or tailgating, a smaller, more portable tank may be a better fit. Generally, portable propane tanks range from 1- to 20-pound capacity, while larger tanks can store up to 100 gallons or more. It’s also important to consider regulations in your area regarding propane tank sizes, placement, and storage.
Always follow guidelines to ensure safety and proper use. Ultimately, choosing the right propane tank size and portability will depend on your individual needs, usage, and preferences.
Oil-free vs. Oil-lubricated Compressors
When deciding between an oil-free or oil-lubricated compressor, there are a few additional considerations to take into account. One factor to consider is the cost of maintenance. Oil-lubricated compressors require regular oil changes and filter replacements, which can add up over time.
However, oil-free compressors may require more frequent maintenance on other components, such as valves and cylinders. Another consideration is the level of noise produced by the compressor. Oil-lubricated compressors tend to operate at a lower decibel level than their oil-free counterparts, which can be important in certain environments.
Additionally, it’s important to keep in mind the specific application of the compressor. Oil-free compressors are typically better suited for clean environments, such as medical facilities or food production plants, where the risk of contamination must be minimized. On the other hand, oil-lubricated compressors may be more appropriate for heavy-duty industrial applications due to their ability to handle high temperatures and pressures.
Ultimately, the choice between an oil-free or oil-lubricated compressor will depend on a variety of factors, and it’s important to carefully consider each one before making a decision.
Compressor Noise and Location
When it comes to compressor noise and location, there are a few additional considerations that may affect your decision-making process. One thing to keep in mind is the proximity of your compressor to any neighbors or shared walls. If you live in a community with noise restrictions, it’s important to choose a location that won’t violate any rules.
Additionally, if you plan on using your compressor in an indoor space, you should be aware of the potential for increased noise levels and take steps to soundproof the area. Another consideration is the type of compressor you choose – some models are designed to operate more quietly than others, so do your research and look for options with low decibel ratings. By taking these factors into account, you can minimize compressor noise and ensure a more pleasant experience for yourself and those around you.
Conclusion
In conclusion, calculating air compressor requirements may seem daunting at first, but with a little bit of math and some consideration of your specific needs, you can make the process a breeze. Don’t let the jargon or technical specifications intimidate you – just remember to factor in variables such as required volume, pressure, and duty cycle, and you’ll be well on your way to selecting the perfect compressor for your needs. And if all else fails, just remember: when it comes to air compressors, bigger isn’t always better – it’s all about finding the right fit for you!”
FAQs
What factors should be considered when calculating air compressor requirements?
When calculating air compressor requirements, factors such as required flow rate, pressure, duty cycle, and compressor type should be taken into consideration.
How do I determine the required flow rate for my air compressor?
The required flow rate for your air compressor can be determined by evaluating the air tools and equipment you will be using and their individual needs, as well as taking into account the total volume of your facility.
What is the duty cycle of an air compressor?
The duty cycle of an air compressor refers to the amount of time it can operate at full capacity without needing to be turned off or cooled down.
What compressor type is best suited for high-volume operations?
Screw compressors are typically the best choice for high-volume operations, as they can deliver continuous air flow and are highly efficient.
Can multiple air compressors be used together to meet high air demand?
Yes, multiple air compressors can be used in tandem to meet high air demand, but it is important to ensure that they are properly sized and coordinated to avoid potential damage.
What is the difference between a single-stage and two-stage compressor?
A single-stage compressor compresses air one time and delivers it to a storage tank, while a two-stage compressor compresses air twice before delivering it to the storage tank, resulting in higher pressure and greater overall efficiency.
What type of maintenance is required for air compressors?
Regular maintenance such as oil changes, filter replacements, and cleaning is necessary to ensure optimal performance and extend the lifespan of air compressors.