How to Connect Air Compressor Pressure Switch: A Step-by-Step Guide
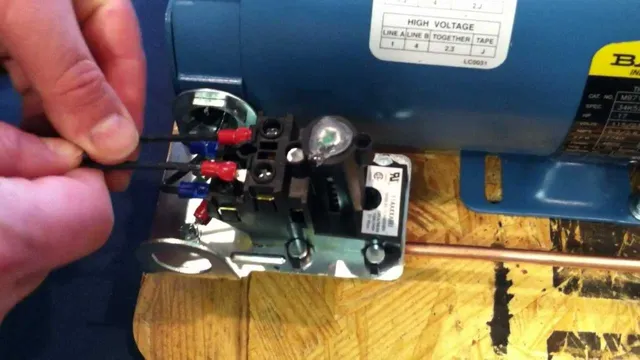
If you’re wondering how to connect an air compressor pressure switch, you’ve come to the right place! As the heart of your compressor, the pressure switch is vital in controlling the amount of air pressure that is built up inside the tank. Whether you’re a DIY enthusiast or a professional mechanic, connecting a pressure switch can be intimidating. But with the right tools and a bit of know-how, you can easily install your new pressure switch and get your compressor up and running in no time.
In this guide, we’ll walk you through the steps involved in connecting an air compressor pressure switch, so you can diagnose and fix any issues that arise on your own. So let’s get started!
What is an Air Compressor Pressure Switch?
If you’re wondering how to connect an air compressor pressure switch, you’re not alone. An air compressor pressure switch is an essential component that senses changes in air pressure and turns your compressor on and off accordingly. Without this switch, your compressor could run continuously, causing damage or even a fire hazard.
To connect the pressure switch, ensure that your compressor is unplugged and that the pressure switch is rated for the correct voltage and pressure range of your compressor. Then, connect the wires according to the manufacturer’s instructions, typically using terminals labeled for power source and motor connection. Once wired, adjust the pressure switch settings to your desired pressure levels and test the compressor to ensure proper function.
With a properly installed air compressor pressure switch, you can ensure safe and effective performance from your compressor for years to come.
Definition and function of air compressor pressure switch
An air compressor pressure switch is a crucial component of an air compressor system that helps control the pressure levels within the system. It is responsible for regulating the compressor’s motor and adjusting the pressure of the air that is being discharged from the compressor. Without an air compressor pressure switch, the compressor would continue operating and producing air until it overheats and eventually breaks down.
With its ability to control and monitor the pressure levels, the air compressor pressure switch ensures the durability and longevity of the compressor, providing reliable performance for years to come. Additionally, the pressure switch also plays a vital role in energy efficiency, as it can be set to turn off the compressor once it reaches a certain pressure level, helping to conserve energy and reduce costs. Ultimately, an air compressor pressure switch is a critical component of any air compressor system, ensuring the correct pressure levels and ultimately extending the life of the compressor.
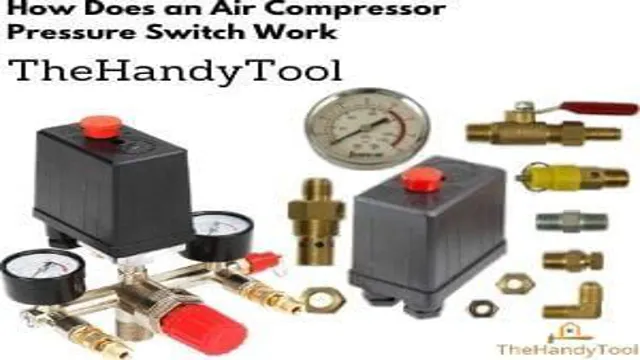
Tools and Materials Needed
If you’re looking to connect your air compressor pressure switch, you’ll need a few tools and materials to get started. The first thing you’ll need is a suitable pressure switch for your compressor. Depending on the type of compressor you have, you may need a different type of pressure switch, so make sure to do your research before purchasing one.
Once you have your pressure switch, you’ll need to gather a few tools, including a wrench, screwdriver, and pliers. You’ll also need some electrical tape and wire strippers if you’re connecting it yourself. It’s important to make sure you have the right gauge wiring and terminals for the switch before proceeding.
Before connecting the switch, ensure that the compressor is unplugged and that there’s no power running to it. It’s always good practice to double-check before making any electrical connections. With your tools and materials on hand, you should be able to connect your air compressor pressure switch with ease.
List of required tools and materials to connect the pressure switch
Connecting a pressure switch requires a few essential tools and materials to ensure a secure and reliable connection. Firstly, make sure you have the appropriate sized wrench to fit the pressure switch’s fittings, as well as a pipe cutter or PVC cutter to cut the pipe to the correct length. It’s also crucial to have Teflon tape to prevent any leaks from occurring.
Additionally, a pressure gauge can help in testing and adjusting the system’s pressure. Finally, a power drill or screwdriver is necessary for mounting the switch onto a surface. By having all these tools and materials at hand, you can ensure a smooth and successful installation of your pressure switch.
Step-by-Step Guide
If you’re looking for an easy way to get your air compressor up and running, one of the first things you’ll need to know is how to connect the pressure switch. This small but extremely important piece of equipment is responsible for regulating the amount of pressure inside your compressor, preventing it from overheating or causing other damage. The good news is that connecting the pressure switch isn’t all that difficult – in fact, it can be done in just a few simple steps.
First, you’ll need to carefully read the installation instructions that came with your pressure switch to make sure you understand all the necessary wiring connections. Then, you’ll need to find a suitable location for the switch, making sure it’s easily accessible and won’t get in the way of any other components. Finally, you’ll need to connect the wiring and test the compressor to make sure everything is working correctly.
With a little patience and attention to detail, you should be able to get your air compressor up and running in no time!
Step 1. Turn off the power supply
When it comes to working with electronics, it’s important to ensure your safety before doing anything. That’s why step 1 in any electronic repair or maintenance process is turning off the power supply. This may seem like common sense, but it’s a step that’s often overlooked.
By turning off your device’s power supply, you prevent any potential electrical shocks that could harm you or damage your device. It’s important to note that simply unplugging your device is not always enough, as some devices have capacitors that can hold an electrical charge even when unplugged. That’s why it’s essential to turn off the power supply at the source, such as flipping a switch or unplugging the power cord.
So before you start any electronic repair or maintenance work, always make sure to turn off the power supply first to stay safe and prevent any damage to your device.
Step 2. Locate the pressure switch
To successfully troubleshoot your furnace pressure switch, the second step is to locate it. The pressure switch is typically located near the furnace blower or burner assembly. It is a small device with wired connections and a hose that connects to the furnace’s combustion chamber.
It’s important to turn off the furnace before locating the pressure switch. Once you’ve found it, check if there are any loose wires or fittings, as they may be the cause of your furnace’s malfunction. Additionally, inspect the hose connected to the switch for any signs of wear or damage that may lead to leakage.
Remember that if you’re unsure about locating the pressure switch or making any repairs, it’s always best to contact a professional technician to ensure that everything is done safely and correctly.
Step 3. Disconnect wires from old switch
When it comes to replacing an old switch, the third step is to disconnect the wires from the old switch. This can seem daunting, but it’s actually a straightforward process if you follow a few simple steps. First, make sure to turn off power to the switch by either flipping the circuit breaker or removing the fuse that controls it.
Once the power is off, use a voltage tester to double-check that there’s no electricity running through the wires. After confirming that it’s safe to proceed, unscrew the faceplate and remove it to expose the wires. Take a picture of the wiring configuration or label each wire with tape to help you remember where each one goes.
Then, using a screwdriver, loosen and remove the screws holding the wires on the old switch. Gently pull the wires out of the switch and set it aside. Congratulations, you’ve successfully completed step 3! The next step is to connect the wires to the new switch.
Step 4. Install and connect new pressure switch
After removing the old pressure switch, it’s time to install and connect the new one. The first step is to check if the new switch is compatible with the current system. Then, read the manufacturer’s instructions carefully before proceeding.
Locate the terminals, which may be marked “T1” and “T2” or “L1” and “L2,” depending on the model. Connecting the wires is easy, first, loosen the screws on the terminals and attach the wires according to the manufacturer’s instructions or your previous observation. Ensure that the wires are connected to the correct terminals to avoid any electrical issues.
Once all wires are fastened, tighten the screws onto the terminals, ensuring that they are snug. Finally, attach the cover plate back on the new pressure switch and turn on the power. Check that the switch controls the system’s pressure correctly.
If done correctly, you’re done with pressure switch installation, congratulations!
Step 5. Adjust the pressure switch settings
Adjusting the pressure switch settings is an important step in ensuring that your air compressor works efficiently and effectively. The pressure switch is responsible for regulating the air compressor’s pressure by turning the compressor on and off as needed. To begin the adjustment process, you’ll first need to locate the pressure switch on your air compressor.
The pressure switch should have two adjustment screws, one for setting the cut-in pressure, which is the pressure at which the compressor turns on, and one for setting the cut-out pressure, which is the pressure at which the compressor shuts off. Using a wrench or screwdriver, you can adjust these settings by turning the screws clockwise or counterclockwise. Be sure to consult your air compressor’s manual to determine the appropriate settings for your specific model.
As you adjust the pressure switch settings, pay close attention to how the compressor responds. You’ll want to ensure that the compressor turns on and off at the appropriate pressures and that it doesn’t overwork itself or operate in an unsafe manner. With a little time and effort, you can adjust the pressure switch settings on your air compressor and enjoy reliable, efficient performance for years to come.
Testing and Troubleshooting
Connecting your air compressor pressure switch may seem like a daunting task, but with the right instructions, it can be a breeze. First, make sure you have all the necessary tools and equipment, including a wrench, pliers, and Teflon tape. Then, turn off the power to the compressor and disconnect any electrical connections.
Locate the old pressure switch and remove it by unscrewing the fittings with your wrench. Use the Teflon tape to seal the threads of the new pressure switch and install it using the same fittings. Before reconnecting the electrical connections, turn on the power and test the compressor to ensure proper functionality.
If there are any issues, check for leaks and double-check the wiring connections. In no time, you’ll have a fully functioning air compressor ready to tackle any task.
How to check if the switch is working properly
If you want to check whether the switch is working properly, there are a few simple steps you can follow. First, check the power source and make sure that it is properly connected. If there is no power, the switch won’t work.
Next, try toggling the switch on and off several times to see if it responds correctly. If the switch feels loose or doesn’t click into place, it may need to be tightened or replaced. Finally, check the wiring and connections to make sure that everything is secure and in the right place.
If you still can’t determine whether the switch is working or not, it may be time to call in a professional. A qualified electrician can use specialized tools to check the switch and troubleshoot any issues that might be causing problems. By following these simple steps, you can ensure that your switch is working properly and avoid any potential safety hazards.
Common problems and how to troubleshoot them
Testing and Troubleshooting are important aspects of any project, from simple websites to complex software applications. Common problems can arise at any stage of the process, including design, development, testing, and deployment. It is important to have a systematic approach to testing and troubleshooting, starting with identifying the problem and its root cause.
From there, one can develop a testing plan, with clear objectives, test cases, and expected outcomes. Common testing techniques include functional testing, usability testing, performance testing, and security testing. Tools such as debugging, logging, and monitoring can help identify and isolate problems.
Troubleshooting is an iterative process that requires patience, persistence, and good communication skills. It is important to document the steps taken, the results obtained, and any solutions found. By having a solid testing and troubleshooting process in place, one can ensure a high-quality product that meets the needs of the end-users.
Conclusion
Connecting an air compressor pressure switch may seem like a daunting task, but fear not, as it’s as easy as connecting the dots. With just a few simple steps, you’ll have your compressor up and running like a well-oiled machine. It’s like connecting with your inner handyman, and you don’t even need a toolbelt to do it.
So go ahead, take the plunge, and impress your friends with your newfound air compressor installation skills. Who knows, you might even become the next Bob Vila of the air compressor world.”
Summary of the steps to connect an air compressor pressure switch
If you are experiencing issues with your air compressor not properly regulating its pressure, it could be due to a faulty pressure switch. In order to connect a new pressure switch, you will need to first ensure that your compressor is turned off and unplugged for safety. You will then need to locate the old pressure switch and remove it, taking note of how it was connected.
Next, you can attach the wires to the corresponding terminals on the new pressure switch and attach the switch to the compressor. After turning the compressor back on, you should test the pressure to ensure that it is properly regulating. If there are still issues, you may need to troubleshoot, checking for loose wires or faulty parts.
By following these steps and troubleshooting as needed, you can ensure that your air compressor is working efficiently.
Final thoughts and tips for a successful installation
When it comes to installing any new system or piece of machinery, testing and troubleshooting are crucial steps to ensuring a successful installation. This involves thoroughly testing all aspects of the installation to ensure that everything is functioning as it should. One tip is to run several test scenarios that mimic real-world use cases to identify any potential issues before they become major problems.
Additionally, troubleshooting any issues that do arise during testing is key to ensuring that the installation is working optimally. This may involve reviewing installation manuals, contacting technical support for assistance, and utilizing available resources to identify and resolve any issues. By taking the time to thoroughly test and troubleshoot the installation, you can ensure that it is functioning properly, and avoid any issues down the line.
FAQs
What is an air compressor pressure switch?
An air compressor pressure switch is a device that monitors the pressure in your air compressor and turns it on or off depending on the value set on the switch.
How do I connect an air compressor pressure switch?
To connect an air compressor pressure switch, first, disconnect the power supply to the compressor. Then, remove the cover of the switch and connect the power wires to the terminals, ensuring the correct polarity. Finally, connect the air lines to the switch’s inlet and outlet ports.
How do I adjust the pressure switch on my air compressor?
To adjust the pressure switch on your air compressor, turn the adjustment screw on the switch clockwise to increase the pressure or counterclockwise to decrease it. Check the pressure with a gauge and make sure it matches the desired pressure, and then tighten the locking nut to secure the setting.
What is the correct pressure level for an air compressor?
The correct pressure level for an air compressor depends on the application and the tools being used. Typically, the pressure range is between 90 and 120 PSI, but some tools may require higher or lower pressures. Always check the tool’s manual for the correct pressure level.
What should I do if my air compressor pressure switch fails?
If your air compressor pressure switch fails, you should first disconnect the power supply to the compressor. Then, remove the cover of the switch and check for any damage or loose connections. If the switch is damaged, you will need to replace it with a new one.
Do I need a special type of pressure switch for my air compressor?
You do not need a special type of pressure switch for your air compressor. However, you should make sure that the switch is rated for the correct voltage and amperage of your compressor to prevent any damage or malfunction.
Can an air compressor pressure switch be repaired?
It is possible to repair an air compressor pressure switch, but it is often more cost-effective to replace it with a new one. If the switch is not working properly, check for loose connections or damage before considering repairing it.