How to Fill Air Compressor Tank: Step-by-Step Guide for Safe Inflation
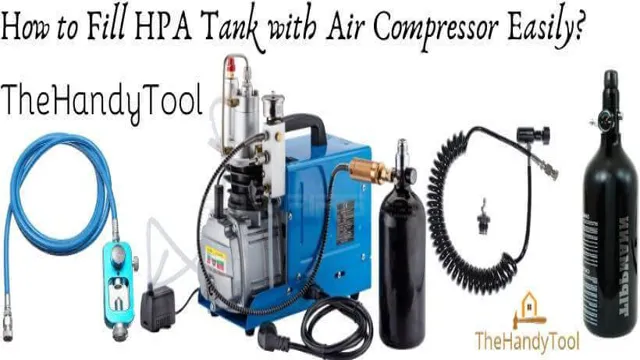
Air compressors are an essential tool for many DIYers or professionals to carry out a variety of tasks. Whether you are filling up car tires or powering a nail gun, an air compressor can be a real lifesaver. But, how do you fill the air compressor tank effectively? You want to make sure you do it safely and properly to ensure optimal results.
In this blog post, we’ll share with you the best way to fill an air compressor tank so you can get the most out of your device. We’ll also give you some tips and tricks to help make the process more accessible and efficient. So, buckle up and get ready to discover the secrets to effective air compressor tank filling!
What You Will Need
Hey there! So, you want to learn how to fill air compressor tanks? Well, the first thing you’re going to need is an air compressor, of course. You’ll also need an air hose to connect the compressor to the tank. Make sure the hose has the right fittings to connect to both the compressor and the tank.
You’ll also need safety equipment, such as eye protection and gloves to protect you from flying debris. It’s important to choose the correct air pressure gauge, as well, so you can monitor the amount of air that’s going into the tank. Finally, make sure you have an understanding of the tank’s maximum capacity and the recommended air pressure for the items you’ll be using it for.
By having these items on hand and following the right steps, you’ll be able to successfully and safely fill your air compressor tank.
Air compressor
Air compressor So, you’ve decided to get yourself an air compressor, but now you’re wondering what you’ll need to make it work properly. Well, first and foremost, you’ll need an air hose. This is the conduit that connects the compressor to your tools or equipment.
You’ll want to make sure you get a hose that is both strong and flexible, as it will need to withstand the pressure of the compressed air while remaining supple enough to maneuver. Additionally, you might consider investing in a regulator, which will allow you to adjust the pressure of the air coming out of the compressor to match the requirements of your specific tool or application. And finally, you’ll need to add some oil to your compressor, which will keep its components lubricated and running smoothly.
Make sure you follow the manufacturer’s recommendations for the type and amount of oil to use, and be sure to check the oil level regularly. With these basic components in place, you’ll be well on your way to using your air compressor to power your pneumatic tools or do any number of other tasks that require compressed air.
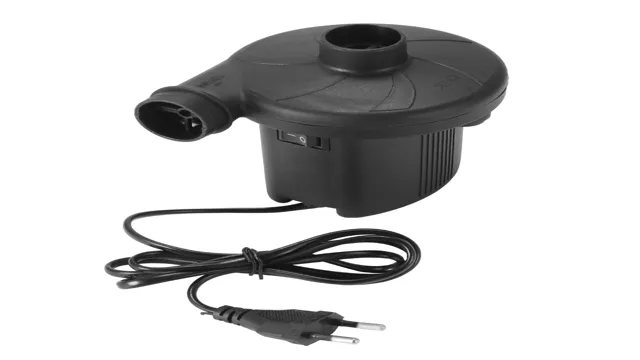
Air hose
When it comes to using an air hose, there are a few things you will need to ensure you can correctly and efficiently complete your task. Firstly, you will need an air compressor to provide the air pressure needed to operate the hose. A good quality air hose is also crucial, with the right length and diameter to suit your specific needs.
Depending on your task, you may require additional fittings and adapters to connect your hose to your compressed air source and the tool or application you are using. Safety should also be at the forefront of your mind, so make sure you have eye and ear protection, as well as a good understanding of how to operate your air hose safely. By having all of the necessary equipment, you can simplify your task, allowing you to complete it to the best of your ability.
Pressure gauge
If you want to measure the pressure of a gas or liquid, then you’ll need a pressure gauge. These devices are essential for ensuring that pipelines, tanks, and other systems are operating within safe pressure limits. To use a pressure gauge, you’ll first need to choose the right type for your application and ensure that it’s compatible with the pressure range you’ll be measuring.
Common options include Bourdon tube gauges, diaphragm gauges, and electronic pressure sensors. Additionally, you’ll need to have some basic accessories on hand, such as hoses, fittings, and adapters, to connect the gauge to the system you’re measuring. With the right equipment and a little know-how, you can easily take accurate pressure readings and keep your operations running smoothly.
So whether you’re working in a lab, workshop, or industrial plant, make sure to have a reliable pressure gauge on hand to help you get the job done safely and efficiently.
Air compressor oil
If you have an air compressor, it’s important to use the right type of oil to keep it running smoothly and avoid costly repairs. Here’s what you will need to ensure that your air compressor stays in top condition. First, you will need to select the right oil for your compressor.
Make sure to check your manual or the manufacturer’s website for recommendations on the type of oil that your compressor requires. Second, you will need to check the oil level regularly and add more oil as needed. It’s important to use the correct level of oil – too little can cause damage to your compressor, while too much can cause it to overheat.
Lastly, be sure to change the oil regularly to keep your compressor running efficiently. By following these simple steps, you can ensure that your air compressor will last for years to come.
Steps to Follow
Filling your air compressor tank can be a straightforward process as long as you follow the necessary steps. First, ensure that the compressor is turned off and unplugged, and relieve any pressure inside the tank. Then, locate the tank’s filling valve and attach the air hose.
Check the owner’s manual to find out the recommended maximum pressure for your tank, and set the pressure gauge accordingly. Begin filling the tank slowly, monitoring the pressure gauge and making adjustments as needed. Once the tank reaches the recommended pressure, turn off the compressor and disconnect the hose.
Don’t forget to take safety precautions, such as wearing eye protection and keeping the hose and nozzles free of debris. With these steps, you’ll be able to fill your air compressor tank with ease and ensure that it’s ready for whatever job you have in mind.
Step 1: Check oil level
If you want to keep your engine running smoothly and avoid costly repairs, it’s important to regularly check your oil level. This is a simple but crucial step that many car owners overlook. To get started, make sure your car is parked on a level surface and the engine is turned off.
Locate the dipstick, which is usually near the oil cap, and pull it out. Wipe it clean with a rag or paper towel, then reinsert it all the way back in. Pull it out again and take note of the oil level, which should be between the marked lines on the dipstick.
If it’s low, add more oil as needed. Remember to use the recommended type of oil for your vehicle, which can be found in your owner’s manual or online. By following this simple step, you’ll ensure your engine is properly lubricated and extend its lifespan.
Step 2: Check pressure level
When it comes to maintaining your vehicle, checking the tire pressure level is a crucial step. The pressure level is essential as it directly impacts the tire’s grip on the road, the fuel economy, and the general performance of the vehicle. You can check the pressure level yourself using a tire pressure gauge or go to a professional to have it done for you.
It is essential to check the tire pressure level when the tires are cold, meaning when the vehicle has not been driven for at least three hours or has not been driven for more than a mile. Generally, the recommended pressure level ranges between 30-35 psi, but it may vary according to the car’s model and the kind of tires being used. Maintaining the appropriate tire pressure level can prolong the tire’s life, reduce fuel consumption, and make the driving experience smooth and safe.
So, be sure to check your tire pressure level regularly to ensure your car’s proper maintenance.
Step 3: Connect air hose
When it comes to using pneumatic tools, connecting the air hose is a crucial step that you cannot afford to ignore. To successfully connect the air hose, the first thing you need to do is to inspect the hose. Look out for any cuts, cracks, or leaks that may compromise its functionality.
If you spot any damages, it is essential to replace the hose before proceeding. Once you have inspected the hose and confirmed that it is okay, attach one end to the tool’s air inlet and the other to the air compressor’s quick-connect coupler. Make sure that you tighten the connections to avoid any air leaks.
Note that proper air hose connection allows the tool to receive adequate air pressure for optimal performance. Always ensure that you disconnect the air hose whenever you are done using your tools. Remember, neglecting this step can lead to air leaks or even hose bursts, jeopardizing your safety and that of people around you.
Step 4: Open release valve
Now that you have successfully completed the distillation process, it’s time to release the pressure held in the still by opening the release valve. This final step is integral to ensuring the safe and proper operation of the still. The release valve allows any excess pressure to escape and prevents any damage to the still, making it last longer.
Failure to open the release valve can result in a dangerous build-up of pressure within the still, which can cause explosions and other hazardous accidents. So, before you kick back and relax, ensure that you release the valve to allow the still to cool down completely. This will help to avoid any damages to your equipment that can hamper distillation in the future.
Remember to take caution during this step and always wear protective gear, including gloves and safety goggles. This way, you will stay safe and avoid any potential accidents.
Step 5: Turn on compressor
Once you’ve checked all the connections and made sure everything is in place, it’s time to turn on the compressor. Before you hit the on switch, make sure the pressure gauge is at zero to prevent any sudden bursts or leaks. It’s important to follow the manufacturer’s instructions when it comes to turning on the compressor and adjusting the pressure settings.
Always start with a low pressure setting and gradually increase it until you reach the desired level. Keep an eye on the pressure gauge and turn off the compressor once you’ve achieved the desired pressure. Remember to follow safety precautions when using a compressor, such as wearing protective gear and never exceeding the maximum pressure limit.
With these steps, you’ll be well on your way to successfully using your compressor for your DIY projects or professional endeavors.
Step 6: Close release valve
Closing the release valve is the final step of the whole process of using a steam cleaner. After you have finished your cleaning task, you need to shut off the steam by turning the machine’s release valve. This will prevent any residual steam from escaping or causing harm.
It is essential to close the valve only once you are sure that all the steam has dissipated. The release valve is usually located on the front or top of the steam cleaner and can be easily turned off with a simple twist or lever. Always make sure that you follow the manufacturer’s guidelines and instructions carefully to ensure you don’t damage the machine or cause any unnecessary accidents.
By following this critical step and shutting off the release valve, you can keep your steam cleaner in good condition, ready for the next use.
Step 7: Fill to desired pressure
When it comes to inflating your tires, it is important to make sure that you fill them to the correct pressure. This can help improve your car’s fuel efficiency, traction, and overall performance. The recommended pressure for your tires can usually be found in your car’s owner manual or on a sticker located on the driver’s side door jamb.
Once you have this information, you can use a tire gauge to check the current pressure level of your tires. If they are below the recommended level, you can use an air compressor to fill them up to the right amount. Be sure to fill them evenly and check the pressure regularly to ensure they are at the correct level.
Properly inflated tires can not only improve your car’s performance but can also help prevent accidents on the road. So, take a few extra minutes to check and fill your tires to their recommended pressure level before hitting the road.
Safety Precautions
If you’re planning to fill an air compressor tank, it’s essential to follow some safety precautions to prevent accidents and injuries. Before you start, make sure to wear protective gear such as safety glasses, gloves, and earplugs to shield your eyes, hands, and ears from harm. Additionally, check the tank’s pressure and capacity, and never exceed the recommended limit.
Overfilling can cause the tank to burst, leading to severe property damage and life-threatening situations. Also, ensure that the compressor has ample ventilation to prevent overheating and explosion risks. Always turn off the air compressor and unplug the device before filling the tank and releasing air pressure.
Finally, inspect the hoses and connectors for wear and tear, and replace them if necessary. With these safety precautions in mind, you can fill your air compressor tank safely and confidently.
Wear safety goggles
Safety goggles are an essential piece of equipment for anyone working with machinery or chemicals. It may seem inconvenient or unnecessary to wear them, but they can protect your eyes from significant harm. Even small bits of debris or chemicals can cause permanent damage to your eyes if they come into contact, leading to vision loss or even blindness.
These goggles will also prevent dust and other small particles from entering your eyes, which can cause irritation and discomfort. Don’t skimp on safety – invest in a good pair of safety goggles and wear them every time you work with machinery or chemicals. Your eyes will thank you for it!
Do not exceed tank pressure rating
The safety of your tank is crucial, and its pressure is no exception. It is important that you do not exceed the tank pressure rating. If you exceed this limit, you significantly increase the risk of a burst.
This danger not only puts you at risk, but also those around you, as fragments from a burst tank can cause severe harm and damage. So, it’s critical to know your tank’s maximum pressure rating and keep the pressure within this range at all times. It’s better to err on the side of caution rather than putting yourself and others in harm’s way.
Regularly inspect your tank for any signs of damage or wear and have it repaired or replaced if needed. In doing so, you can ensure the safety of your tank and prevent any unfortunate incidents. Remember, safety should always come first, so always follow the recommended guidelines for your tank pressure rating to stay safe.
Keep hands and loose clothing away from rotating parts
When working with machinery, it’s crucial to be aware of the potential danger that rotating parts can pose. One important safety precaution to keep in mind is to always keep your hands and loose clothing away from these parts. It’s easy to get complacent and forget just how fast these parts can move, but one sudden movement can lead to serious injury or worse.
Imagine getting a piece of clothing caught in a spinning gear and being dragged into the machine. It’s a terrifying thought, but it can happen if you’re not careful. By keeping a safe distance from rotating parts and being mindful of what you’re wearing, you can avoid putting yourself in harm’s way.
Remember, even a small mistake can have big consequences. So always stay vigilant and put safety first when working with machinery.
Conclusion
And there you have it, folks! Filling an air compressor tank may seem intimidating at first, but once you understand the basics, it’s a breeze. Always remember to safety check your equipment, choose the right compressor for the job, and keep a watchful eye on your tank’s pressure levels. With these tips, you’ll be filling your tank like a pro in no time.
So go ahead, press that power button and let the air flow!”
FAQs
What is an air compressor tank and how does it work?
An air compressor tank is a storage container for compressed air that is used to power tools and equipment. It works by using an electric or gasoline-powered motor to compress and store air in the tank.
How often should I fill my air compressor tank?
The frequency of filling your air compressor tank depends on the usage of your equipment. If you use it frequently for heavy-duty tasks, you may need to fill it more often. Generally, it’s recommended to fill the tank after every use.
How much pressure should I fill my air compressor tank with?
The recommended pressure for your air compressor tank may vary depending on the equipment you’re using it with. It’s important to check the manufacturer’s instructions or the equipment’s manual to determine the correct pressure.
How long does it take to fill an air compressor tank?
The time it takes to fill your air compressor tank depends on the tank’s capacity and the output of the compressor. A small tank may take a few minutes, while a larger tank may take up to an hour.
Can I overfill my air compressor tank?
Overfilling your air compressor tank can be dangerous and cause damage to the equipment. It’s important to fill the tank to the recommended pressure and not exceed it.
How do I safely fill my air compressor tank?
To safely fill your air compressor tank, make sure the compressor is turned off and unplugged. Attach the air hose to the valve and slowly open the valve until the tank reaches the recommended pressure. Be sure to wear appropriate safety gear, such as eye and ear protection.
What should I do if my air compressor tank won’t fill?
If your air compressor tank won’t fill, check for any leaks in the hoses or valves. Make sure the compressor is turned on and functioning properly. If the issue persists, it may require professional repair.