How to Operate an Air Compressor: A Step-by-Step Guide for Beginners
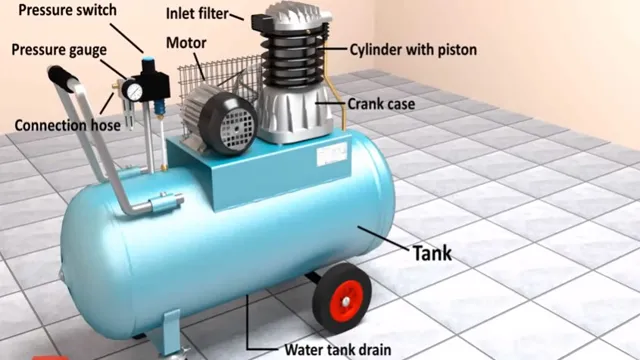
If you’re not familiar with air compressors, they can seem intimidating. However, once you understand the basics, they’re quite simple to operate. In fact, they’re incredibly useful for a variety of tasks around the home and in your workshop.
If you’re wondering how to operate an air compressor, you’re in the right place. In this blog post, we’ll give you a rundown on everything you need to know. We’ll cover how to use an air compressor safely, how to maintain it, and what types of tasks you can accomplish with an air compressor.
So, whether you’re a complete beginner or a seasoned DIY-er, keep reading to learn all about air compressors.
Preparing the Compressor
If you’re wondering how to operate an air compressor, the first step is preparing the equipment. Before turning on the compressor, ensure it’s properly grounded to avoid any potential electrical hazards. Next, check the oil level and add if necessary.
Remember to only use oil designed for air compressors and follow the manufacturer’s recommendations. Connect the air hose to the compressor and ensure it’s tightly secured to avoid any leaks. Set the pressure switch according to the recommended pressure range for your equipment.
Finally, plug in the compressor and turn it on. Let it run for a few minutes to build up pressure, and then you’re ready to use it. Always follow the manufacturer’s guidelines and safety precautions when operating your air compressor to prevent any accidents or damage to your equipment.
With these simple steps, you’ll be able to use your air compressor efficiently and safely.
Check Oil Level and Add Oil as Needed
If you’re planning on using your compressor for any length of time, it’s essential to take care of it properly. Preparing your compressor is the first step toward ensuring it runs smoothly and efficiently. One crucial aspect of this preparation is checking the oil level and adding oil as needed.
Without the proper amount of oil, your compressor won’t work correctly, and it could lead to costly repairs down the road. When checking the oil level, it’s essential to ensure that the compressor is on level ground, so the reading is accurate. To add oil, make sure you use the appropriate type and level of oil as specified in your compressor’s manual.
By taking the time to prepare your compressor properly and ensuring the oil level is correct, you’re setting yourself up for success and preventing any unnecessary headaches.
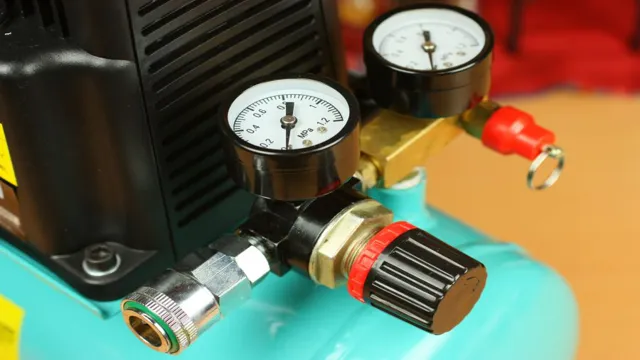
Check Air Filter and Clean or Replace as Needed
As you get ready to use your air compressor, it’s important to ensure that it’s in optimal condition. One crucial step in preparing your compressor is to check the air filter and clean or replace it as necessary. The air filter is responsible for keeping dirt, debris, and other contaminants out of the air supply, ensuring that your compressor functions efficiently and reliably.
Over time, the filter can become clogged or dirty, reducing its effectiveness and potentially leading to damage to the compressor. By inspecting the air filter regularly and taking steps to clean or replace it as needed, you can keep your compressor running smoothly and enjoy the benefits of clean, high-quality compressed air. Don’t overlook this simple but essential step in preparing your compressor for use – it could make a significant difference in its performance and longevity.
Connect Air Hose to Compressor and Tool
To prepare your compressor for connecting the air hose, the first step is to locate the air intake. This is typically located on the side or back of the compressor. Make sure the compressor is powered off and disconnected from any electrical sources.
Then, remove the plastic cap covering the air intake and attach the air filter. This will prevent dirt and debris from entering the compressor while it’s in use. Next, locate the outlet valve, which is where the air hose will be connected.
Make sure the valve is closed before attaching the hose, and then secure it tightly with a wrench. Finally, turn on the compressor and let it build up pressure before connecting the tool. By following these steps, you’ll be able to safely and efficiently connect your air hose to the compressor.
Remember, safety should always be your top priority when working with air compressors or any other power tools. Prepare your compressor correctly using these steps and you’ll be well on your way to completing your project.
Starting the Compressor
If you’re new to using an air compressor, starting it up can seem intimidating. But with a little practice, it’s easy to get the hang of it. First, make sure the compressor is plugged in or the switch is ON if it’s a gas-powered model.
Then, check the oil level and add more if needed. Next, turn the regulator knob to the off position and connect your air tool. Slowly turn the regulator knob to the desired pressure level, then turn on the compressor.
You’ll hear the motor start up and the pressure gauge will begin to rise. Once it reaches the desired pressure, the compressor will automatically shut off. Congratulations, you’ve successfully started your air compressor! Remember to always wear appropriate safety gear and consult the manufacturer’s instructions for specific details on your model.
With a little practice, you’ll be operating your air compressor like a pro in no time.
Plug in the Compressor and Turn On
Starting the compressor is the first step in the process of getting ready to use it. Before plugging in the compressor and turning it on, it’s important to do a few things. First, make sure the compressor is set up properly.
To do this, check the owner’s manual or manufacturer’s website for instructions on how to configure the compressor for use. Once the setup is complete, it’s time to plug in the compressor. Make sure the cord is secure and the outlet is working properly.
Next, turn on the compressor. This may require pressing a button or flipping a switch, but it should be easy to do. With the compressor on, you’ll be ready to start using it for whatever project you have in mind.
Just remember to always follow the instructions provided by the manufacturer to ensure the safety of yourself and others around you.
Allow the Compressor to Build Pressure
When starting up your compressor, it’s important to allow it time to build up pressure before use. This process can take anywhere from a few minutes to half an hour, depending on the size and type of compressor you have. Rushing this step can cause damage to the compressor and reduce its efficiency.
During the building pressure stage, make sure all valves and hoses are securely connected, and be sure to listen for any abnormal noises that could indicate a problem. Once the compressor has reached its desired pressure, it’s ready for use. By taking your time and allowing your compressor to properly build pressure, you’ll ensure a longer lifespan and better performance for your equipment.
Adjust Pressure as Needed
When starting your compressor, it’s crucial to adjust pressure as needed. One of the biggest mistakes people make is assuming that the default pressure setting is right for every task. However, the reality is that different applications require different pressure levels.
For instance, when inflating car tires, you’ll need a different pressure level than when using air tools. Therefore, you should start by checking the manufacturer’s instructions for your compressor and adjusting the pressure accordingly. This will ensure that you don’t damage your equipment by applying too much or too little pressure.
Additionally, it will help you achieve optimal results for every task you undertake with your compressor. So, take a minute to adjust the pressure, and you’ll be glad you did!
Using the Compressor
If you’re new to using an air compressor, don’t worry, it’s not as complicated as it may seem. Before operating the compressor, you need to familiarize yourself with all the components and understand how to control the airflow. Once you turn on the compressor, it will fill up the tank with air until the desired pressure is reached.
You can then connect your air tool to the compressor using the hoses and start using it. Depending on what you’re trying to achieve, you may need to adjust the pressure accordingly. Always ensure that you’re using the right type of oil for lubrication and keep the filters clean.
Proper maintenance is critical to prevent any damages and ensure a long lifespan for your equipment. With these basic tips, you’ll be able to operate your air compressor with confidence.
Attach Tool to Air Hose
Attaching your tool to an air hose is a crucial step in using your compressor. It allows your tool to receive highly-pressurized air to power it. To connect your tool to the air hose, you will need to start by inspecting the connections to make sure they are clean and free from any debris.
Next, you will need to clamp the air hose onto the compressor’s fitting using a hose clamp. Then attach the tool to the other end of the hose by lining up the male and female counterparts and securing them together. Once you’re done, turn on the compressor and check if there are any air leaks.
If you detect any, make sure to correct them before starting to use your tool. Remember that attaching your tool correctly to your air hose is crucial for your safety and the efficiency of your work.
Trigger the Tool to Release the Compressed Air
To use a compressor effectively, you need to know how to trigger the tool to release compressed air. First, make sure that your compressor is fully charged, and that all safety valves are in place and properly secured. Next, attach the hose to the tool that you want to use, ensuring that it is securely fastened.
Then, switch on the compressor and wait for it to build up pressure. Once the pressure gauge indicates that the compressor is ready, you can activate the tool by pulling the trigger. This will release the compressed air and enable you to use the tool to complete your task.
Remember to always follow safety precautions when using a compressor, such as wearing protective gear and ensuring that the tool is properly aligned with your work surface. By using the compressor correctly, you can achieve professional-grade results in less time and with minimal effort.
Shutting Down the Compressor
Knowing how to properly operate an air compressor includes knowing how to safely shut it down. Before shutting down the compressor, it’s important to ensure that all tools and equipment are turned off and disconnected from the compressor. Next, switch off the compressor and unplug it from the power source.
Allow the compressor to run for a few minutes to release any residual pressure in the tank. Once all pressure has been released, open the drain valve to release any remaining moisture. It’s important to never touch the compressor’s discharge tube or discharge valve when releasing pressure, as this can cause injury.
Once the compressor has been properly shut down, make sure to store it in a dry and safe location until its next use. By following these steps, you can ensure the safe and efficient operation of your air compressor.
Turn Off the Compressor and Unplug it
Shutting down the compressor correctly is crucial to maintaining its longevity and preventing any safety hazards. The first step is to turn off the compressor and unplug it from the electrical source. This ensures that there is no electricity running through the machine, reducing the risk of any accidents.
It’s also important to wait a few minutes for the compressor to cool down before attempting to perform any maintenance or inspections. By allowing time for the machine to cool down, you prevent the risk of injury from hot moving parts or release of hot air. Remember, safety always comes first when dealing with any kind of machinery.
By following these simple steps, you can ensure that your compressor will last for years to come.
Drain Moisture from the Tank
When shutting down your air compressor, it’s important to properly drain any excess moisture from the tank. Moisture buildup can lead to corrosion and damage to your equipment, reducing its lifespan and efficiency. To drain the tank, start by turning off the compressor and unplugging it from the power source.
Open the drain valve and allow any water or condensation to escape. You can also use an air compressor drain valve extension to make the process easier. Once all the moisture has been removed, close the drain valve and ensure that the tank is completely dry before storing it.
By taking these steps, you can prevent costly repairs and ensure that your compressor runs smoothly for years to come. Remember to regularly check and maintain your equipment to prolong its lifespan and efficiency.
Store the Compressor in a Dry and Safe Place
When it comes to shutting down your air compressor, there are a few steps you should follow to ensure it remains in good condition and ready for the next use. One important step is to store the compressor in a dry and safe place. This means finding an area in your workspace that is free from moisture and dust, and where the compressor won’t get knocked over or damaged.
It’s also a good idea to cover the compressor with a tarp or other protective material to keep it clean and prevent any accidental spills or debris from getting inside. By taking the time to properly store your compressor after use, you’ll extend its lifespan and ensure that it’s always ready to perform when you need it most.
Conclusion
Congratulations! After reading this guide, you are now equipped with the knowledge and skills to operate an air compressor like a pro. Remember to always prioritize safety by wearing the appropriate gear and following the manufacturer’s instructions. With a little bit of practice, you’ll be pumping up tires, powering tools, and creating a whole lot of compressed air awesomeness in no time.
So go ahead, take a deep breath, and let that air compressor do its thing. Your projects (and your lungs) will thank you.”
FAQs
What are the basic components of an air compressor?
The basic components of an air compressor are compressor pump, motor or engine, tank, pressure switch, regulator, safety valve, and pressure gauge.
How to choose the right size of air compressor?
The right size of air compressor depends on the tools or applications you will use it for. To determine the required size, consider the required CFM (cubic feet per minute) and PSI (pounds per square inch) of your tools, and choose an air compressor with a higher CFM and PSI rating than what you need.
How to properly maintain an air compressor?
Proper maintenance of an air compressor includes regularly checking and changing air filters, draining water from the tank, inspecting and tightening all fittings and connections, checking and changing lubricant, and inspecting and replacing worn-out parts.
How to troubleshoot air compressor problems?
Common air compressor problems include low pressure, leaks, and overheating. To troubleshoot these problems, check the intake filter, pressure switch, regulator, safety valve, and motor or engine. Refer to the manufacturer’s manual for specific steps.
How to safely operate an air compressor?
To safely operate an air compressor, use appropriate personal protective equipment (such as safety glasses and gloves), follow the manufacturer’s instructions, keep the compressor away from flammable materials, and regularly inspect and maintain the compressor for any damages or leaks.
How to reduce the noise level of an air compressor?
To reduce the noise level of an air compressor, use a compressor with a lower decibel rating, install an acoustic enclosure around the compressor, use vibration isolation pads, and locate the compressor in a remote area or a soundproofed room.
How to choose the right type of air compressor for your needs?
The right type of air compressor depends on your needs and applications. Consider factors such as the required CFM and PSI, portability, power source, noise level, and budget, and choose from different types such as reciprocating, rotary screw, and centrifugal compressors.