If you’re a DIY enthusiast or someone working on a construction project, you know how important air compressors can be. They are versatile tools that can help you spray paint, power pneumatic tools, and inflate tires with ease. But one thing that can be confusing for many people is how to hook up an air compressor hose.
With so many different connectors, valves, and couplers, figuring out which parts to use and how to connect them can sometimes feel like a daunting task. In this blog post, we’re going to guide you step-by-step on how to hook up an air compressor hose, so you can get the most out of your tool. We’ll explain how to choose the right hose and fittings, how to check for leaks, and how to safely operate your air compressor.
Whether you’re a seasoned pro or just starting, we’ve got you covered. So, let’s dive into the world of air compressors and learn how to hook up your hose!
Gather necessary tools
If you’re planning to use your air compressor, you’ll need to know how to hook up the hose properly. To start, you’ll require a few necessary tools. First and foremost, you’ll need an air compressor hose—a flexible and durable tube designed to connect the air compressor to the air tool securely.
You’ll also need tools like pliers and adjustable wrenches to tighten and secure the hose fittings correctly. Additionally, you might need Teflon tape to seal any potential leaks in the fittings. By having these tools on hand, you can ensure safe and efficient use of your air compressor.
When hooking up the hose, it’s essential to connect the appropriate fittings securely, as loose connections can cause air leaks, lower the efficiency of the compressor, and even cause safety hazards.
Air compressor, hose, fittings, adapters, thread sealant
Before beginning any air tool project, it’s essential to gather all the necessary tools. This includes an air compressor, hose, fittings, adapters, and thread sealant. An air compressor is the heart of the air tool system, providing the necessary power to operate the tools.
The hose, fittings, and adapters are necessary to connect the air compressor to the air tool securely. Ensuring that all fittings and adapters match the air tool’s specifications is vital to providing a safe and efficient operation. Additionally, thread sealant should be used on all connections to prevent air leaks and maintain optimal performance.
By gathering all of these tools before beginning a project, you can ensure that you have everything you need to get the job done right.
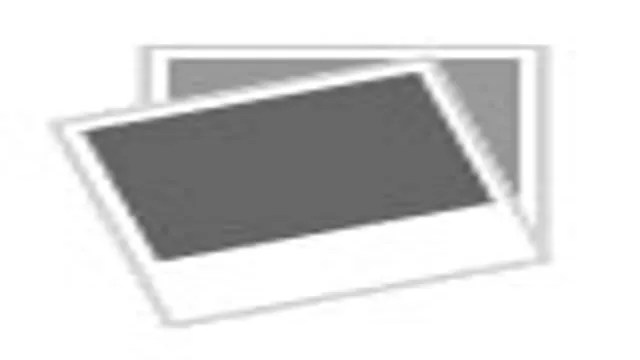
Prepare compressor and hose
Hooking up your air compressor hose might seem like a simple task, but there are a few things to keep in mind to ensure that it is done safely and efficiently. The first step is to prepare your compressor by checking the oil level and making sure it is up to the recommended level. Next, locate the air outlet port on the compressor and remove the cap.
This will allow you to attach the quick-connect fitting onto the port. When attaching the fitting, be sure to tighten it securely, but avoid over-tightening as it can damage the port. Finally, attach the other end of the hose to the fitting and tighten it securely.
Before using your compressor, make sure that all connections are secure and the hose is free of kinks or twists. By following these simple steps, you’ll be able to hook up your air compressor hose with ease and confidence.
Turn off compressor, release pressure, attach fittings to hose and compressor
When it comes to using a compressor and hose, preparation is key to ensure safety and efficiency. Before attaching any fittings to the hose and compressor, it’s essential to turn off the compressor and release any pressure that may be built up. This will prevent any accidental releases of air and keep you safe during the process.
Once the compressor is off, you can securely attach the fittings to the hose and compressor with ease. Be sure to choose the appropriate fittings for the job to ensure a tight, leak-proof connection. Preparing your compressor and hose may seem like a minor detail, but it can have a significant impact on your project’s outcome.
By taking the time to properly turn off your compressor and release pressure, you’ll be able to work without the worry of accidents or mishaps. Remember to choose the right fittings for your job, and always double-check that they are properly secured before use. With these tips in mind, you’ll be well on your way to completing your project with ease and confidence.
Apply sealant
If you’re wondering how to hook up an air compressor hose, you’re in the right place! The first step is to make sure that your hose connection is clean and free from any debris. Next, apply a small amount of sealant to the male end of your hose before attaching it to your compressor or tool. This will help keep the connection airtight and prevent any leaks.
Be sure to tighten the connection securely, but avoid overtightening, as this can damage the brass fittings. Finally, turn on your compressor and test your hose to make sure you have a steady flow of air. With these simple steps, you’ll be up and running with your air compressor in no time!
Wrap thread sealant tape around fitting threads and tighten securely
When it comes to installing pipes or fittings, it’s crucial to ensure they’re secure and don’t leak. That’s where thread sealant tape comes in. This handy little tool can be wrapped around the fitting threads to create a tight seal and prevent any leaks.
First, ensure that the threads are clean and free from any debris before applying the tape. Then, wrap the tape around the threads in a clockwise direction. Be sure to overlap each wrap slightly, so there are no gaps for leaks to occur.
After you’ve wrapped the tape around the threads a few times, screw the fitting into place and tighten it securely. The tape will compress, creating a tight seal between the threads and preventing any leaks from occurring. Applying sealant isn’t just important for proper installation but also the longevity of your pipes and fittings.
So, don’t skip this crucial step when installing or assembling.
Attach hose to compressor
If you have an air compressor, knowing how to hook up the hose is essential. First, make sure the compressor is turned off and unplugged. Then, locate the hose attachment point on the compressor.
This is typically located near the tank and will be marked with a quick-connect fitting or threaded valve. If there is a fitting, simply push the hose onto it until it clicks into place. If the attachment is threaded, wrap Teflon tape around the threads to ensure an airtight seal.
Hand-tighten the hose onto the valve until it is snug, but do not overtighten. Once the hose is attached, turn on the compressor and check for any leaks. If you notice any air escaping around the hose, shut off the compressor and tighten the connection.
With the hose attached properly, you’re ready to start using your air compressor for all your projects.
Push hose fitting onto compressor outlet, secure with a clip or collar
When it comes to attaching the hose to the compressor, it’s important to make sure you do it properly to ensure there are no leaks or accidents down the line. The first step is to push the hose fitting onto the compressor outlet. This can be a bit tricky to do, especially if you’re working with a larger hose or a tighter space.
But with a bit of patience and persistence, you should be able to get it on there securely. Once you’ve got the fitting in place, you’ll want to make sure it’s secure by attaching a clip or collar to hold it in place. This will ensure that the hose doesn’t accidentally slip off or come loose while you’re using it.
With these steps done, you can rest assured that your compressor is connected properly and is ready to use. Just be sure to double-check everything before you turn it on, and you should be good to go.
Test the connection
So, you’ve got an air compressor and a hose, but aren’t sure how to hook them up? Don’t worry, it’s simpler than you might think. First, make sure your compressor is turned off and unplugged. Then, take the female end of your hose and attach it to the compressor’s air outlet.
Screw it on tightly, making sure there are no leaks or gaps. Next, attach the male end of the hose to your desired tool or accessory. Again, ensure a tight connection to prevent air loss.
Once everything is securely connected, turn on your compressor and give it a test run. Listen for any strange sounds or vibrations, and check for any air leaks. Congrats, you’ve successfully hooked up your air compressor hose! Just remember to always wear proper safety gear and use caution when working with compressed air.
Turn on compressor and check for air leaks, adjust fittings as needed
When it comes to using a compressor, it’s important to test the connection before getting started. Turn on the compressor and listen for any air leaks or unusual sounds. If you do notice any leaks, it’s important to adjust the fittings as needed to ensure a tight connection.
You don’t want to lose any air pressure or waste any of your compressed air due to a faulty connection. One trick to test the connection is to use a soapy solution and apply it to the connection points. The solution will bubble at the point of the leak, making it easier to identify and fix the issue.
Once you have checked for air leaks and adjusted the fittings as needed, you can move on to using your compressor with confidence. Remember, it’s crucial to regularly check the connection to ensure optimal performance and efficiency. So, go ahead, turn on your compressor and test that connection!
Safety precautions
Hooking up an air compressor hose may seem like a simple task, but it’s important to take the necessary safety precautions. Before beginning, make sure the air compressor is turned off and unplugged. Next, attach the hose to the compressor’s outlet valve and tighten it securely using a wrench.
Then, attach the other end of the hose to the tool or accessory you’ll be using and tighten that connection as well. Make sure that both connections are secure and tight before turning the compressor back on. When using the tool, always wear appropriate safety gear, such as eye and ear protection, and never aim the compressed air at yourself or others.
With these simple steps, you can hook up your air compressor hose safely and confidently.
Wear eye protection, follow manufacturer’s instructions, turn off air supply when finished
When undertaking any DIY project, it is essential to take safety precautions seriously. Whether you are a novice or an experienced professional, accidents can happen in the blink of an eye. When it comes to using power tools for any project, make sure you wear eye protection at all times.
Flying debris or chemicals can cause serious damage to your eyes, so investing in proper safety gear is a must. It is also important to follow the manufacturer’s instructions carefully. Each tool is unique, and the instructions provided are tailored to ensure optimal performance and safety.
To avoid accidents or injuries, make sure you read and understand each instruction before using the tool. Additionally, always make sure the air supply is switched off when you finish using the tool. Leaving the air supply on can cause the tool to move or spin rapidly, leading to potential danger.
Remember, taking safety precautions may seem like a hassle, but they can ultimately save your life. So, always prioritize safety and stay alert while using any power tool.
Conclusion
Just like finding the perfect partner, connecting an air compressor hose requires a bit of finesse and a clear understanding of what you want. So be patient, take your time, and make sure you have the right connection before sealing the deal. Remember, communication is key – make sure you listen to your compressor’s needs and requirements, and you should have a long and happy partnership.
And who knows – maybe you’ll even end up with a little extra power and pressure in your love life… I mean, air tools.”
FAQs
What tools do I need to hook up an air compressor hose?
You will need a compressor hose, couplers, and fittings.
Can I use any type of hose for my air compressor?
No, you should only use a hose that is specifically designed for high pressure air compressors.
How do I connect the hose to my air compressor?
You will need to use couplers and fittings that match the thread size of your compressor’s outlet.
How much pressure can my air compressor hose handle?
The maximum pressure that your hose can handle will be listed on the package or in the product description.
Can I use Teflon tape on the threads when connecting my hose?
Yes, applying Teflon tape can help create a tight seal and prevent air leaks.
How often should I inspect my air compressor hose for cracks or damage?
You should inspect your hose before each use and replace it if you notice any signs of wear or damage.
What should I do if my hose is leaking air?
Check the connections and make sure they are properly tightened. If that doesn’t work, you may need to replace the hose or fittings.