How to Install a 60 Gallon Air Compressor: A Step-by-Step Guide for Maximum Efficiency
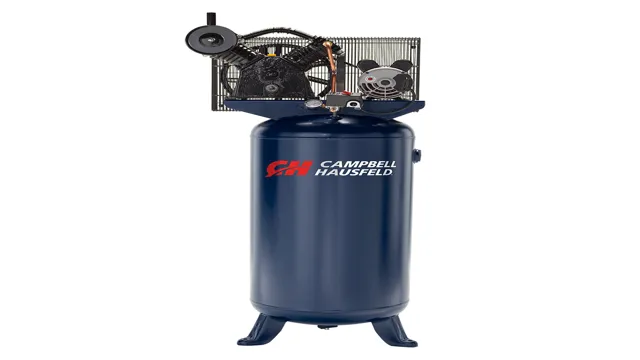
Installing a 60-gallon air compressor in your home workshop or garage is a game-changer. It opens up a whole new world of possibilities when it comes to powering your pneumatic tools, such as nail guns, sanders, and impact wrenches. However, the installation process can be a bit daunting if you don’t know where to start.
Fortunately, it’s not as complicated as it seems! In this blog post, we’ll walk you through the steps you need to take to install your 60-gallon air compressor like a pro. You’ll be up and running in no time, and ready to take on any DIY project that comes your way. So grab your tool belt and let’s get started!
Pre-Installation Steps
Before diving into the installation process, there are some important pre-installation steps to consider when installing a 60 gallon air compressor. First off, it’s crucial to check the voltage, amperage, and phase requirements of the compressor and your electrical system to make sure they are compatible. Next, it’s recommended to install a proper air filtration system to keep the air flowing into the compressor clean and dry.
This can be achieved by installing a pre-filter and after-filter to prevent moisture and debris from damaging the compressor. Another important step is to properly anchor the compressor to a solid, level surface, as it can weigh over 400 pounds when full of air. Lastly, it’s important to choose an installation location that has proper ventilation and adequate space around the compressor for maintenance and repairs.
By taking the time to follow these pre-installation steps, you can help ensure a successful and efficient installation for your 60 gallon air compressor.
Evaluate the Space
When it comes to installing any type of equipment, it’s crucial to evaluate the space before starting the process. When installing a new system, such as a security system, you want to make sure that the space you’re working with can handle the equipment you’re installing. This includes making sure that there is enough power to support the system, that the wiring can be routed correctly, and that there are no obstructions that could interfere with the system’s operation.
Taking the time to thoroughly evaluate the space beforehand can save you a lot of headaches later on. Additionally, identifying any potential issues early on can help you come up with a plan to address them before they become major problems. Keyword: security system, evaluate the space, installing equipment.
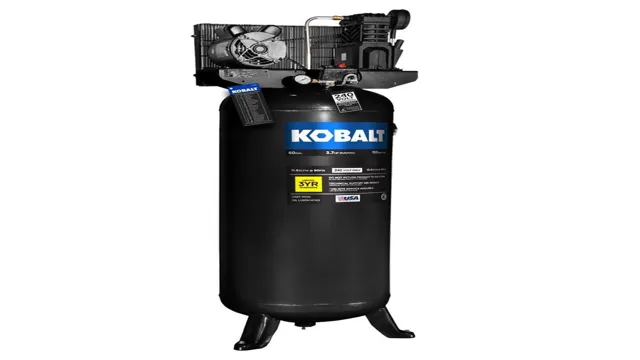
Check Electrical Requirements
Before any installation can take place, it’s essential to check your electrical requirements. Understanding the voltage, amperage, and phase requirements are necessary to ensure that your future electrical system can handle the electrical load required by your equipment. This information can be found on the equipment nameplate or in the manufacturer’s manual.
You may also need to install additional wiring and upgrade your electrical panel to accommodate the new equipment adequately. It’s crucial to have a licensed electrician inspect and update your electrical system to ensure that the connections and wiring meet the electrical codes and are safe. Neglecting these steps may result in power overloads, equipment damage, and electrical hazards that can be dangerous for both your employees and your equipment.
Remember, preventative measures are always more cost-effective in the long run. So, before any installation, always perform a thorough check of your electrical requirements to avoid any mishaps and ensure safe and efficient operation.
Assemble Necessary Tools
Before proceeding with the installation process, certain pre-installation steps need to be followed, such as assembling the necessary tools. It is crucial to have all the required tools in hand before beginning the installation process to avoid any unnecessary delays or obstacles. The tools needed may vary depending on the installation type and the specific manufacturer’s recommendations.
Typically, a screwdriver, wire stripper, pliers, drill, level, and ladder are essential tools for most installations. Moreover, in some cases, special tools, such as crimping tools, may be required for specific installation types. Keeping all the necessary tools handy and organized in one place will make the installation process more manageable and less time-consuming.
Therefore, it is essential to ensure that all the required tools are present before starting any installation process.
Installation Process
Installing a 60 gallon air compressor can be a daunting task for those who are new to the world of DIY projects. Firstly, ensure that you have sufficient space to accommodate the compressor and the necessary electrical outlets. Secondly, place the compressor on a flat surface away from direct sunlight and damp areas.
Make sure that you have all the tools required for the installation process including plumbing fittings, air hose, and pressure gauge. Once you have checked and prepared everything, connect the air compressor to the electrical outlet and ensure that all wiring is done correctly. Fit the plumbing fittings and air hose appropriately, ensuring that there are no leaks.
Adjust the pressure gauge to the desired pressure, and the air compressor is ready for use. With a little bit of patience and attention to detail, anyone can install a 60 gallon air compressor with ease.
Secure Air Compressor to Platform
In order to ensure the safety and stability of an air compressor, it is important to properly secure it to the platform. The installation process involves a few steps to ensure a secure fit. The first step is to check the surface of the platform to make sure it is level and free from any debris.
It is important to choose the right bolts and anchors based on the size and weight of the compressor. Once the bolts and anchors have been installed, the compressor should be mounted and tightened securely. It is crucial to make sure that the compressor is level and stable before using it.
It is also a good idea to periodically check the bolts and anchors to ensure that everything is secure. By following these steps, you can ensure that your air compressor is safe and secure on the platform, and ready for use whenever you need it.
Attach Air Filter and Pressure Regulator
When it comes to installing an air compressor, one of the most important steps is attaching the air filter and pressure regulator. These components are essential for ensuring that the air coming out of your compressor is clean and regulated to the proper pressure. To begin, make sure your compressor is turned off and unplugged.
Then, locate the air outlet on the compressor and attach the filter to it. This will help prevent contaminants from entering your air tools and equipment. Next, attach the pressure regulator to the outlet side of the filter.
This component allows you to set the desired pressure for your air tools and equipment, ensuring that they operate efficiently and safely. Once both components are securely attached, you can turn on your compressor and test the system to make sure everything is working properly. So whether you’re a DIY enthusiast or a professional mechanic, attaching an air filter and pressure regulator is an essential step in setting up your air compressor.
Install Pressure Switch
Installing a pressure switch can seem like a daunting task, but it’s actually quite simple. To get started, make sure you have all the necessary tools, such as a wrench, a screwdriver, and Teflon tape. The first step is to turn off the power to the pump or compressor.
Next, remove the cover from the switch box and use the wrench to disconnect the old pressure switch. Be sure to label the wires so you know where they go later. Then, wrap Teflon tape around the threads of the new pressure switch and carefully screw it into place.
Connect the wires to their proper terminals, making sure they’re tight. Finally, turn the power back on and test the new pressure switch to ensure proper functionality. With a little bit of patience and attention to detail, you’ll have a newly installed pressure switch in no time.
Electrical Wiring
If you want to install a 60-gallon air compressor, the first key step is to understand the electrical requirements. For safety reasons, it’s absolutely vital to ensure that the wiring is appropriate for the compressor’s power supply needs. A 60-gallon compressor typically needs 220 volts to run efficiently, so you’ll likely need to hire a licensed electrician to wire the outlet and breaker for the compressor.
This is important, as a poorly-wired outlet and breaker can be extremely dangerous and can even cause electrical fires. Once the electrical wiring is properly installed, you can begin the process of setting up and installing the compressor itself. This includes things like adding oil, mounting the unit, and connecting the hoses and fittings.
With careful planning and attention to detail, you can safely and effectively install a 60-gallon air compressor that will provide many years of reliable service.
Connect Power Supply
The first and most important step when it comes to electrical wiring is connecting the power supply. This may seem daunting to someone who has little experience with electrical work, but it’s actually quite simple as long as you follow the appropriate safety precautions. Before you begin, make sure that you have all the necessary tools and equipment.
This includes a voltage tester, wire strippers, circuit breaker, and electrical tape. Once you have these, you can start the process. First, locate the main electrical panel or circuit breaker box and turn off the main power switch.
This will ensure that there is no power flowing through the wires and thus minimize the risk of electrical shock. Next, locate the wires that need to be connected to the power supply and strip off the insulation from the ends of the wires. Connect the red wire to the positive terminal and the black wire to the negative terminal.
Finally, once all connections have been made, turn on the circuit breaker and test the power supply with a voltage tester. If everything checks out, you’re good to go! Just remember to always work carefully and methodically when it comes to electrical wiring, and never take unnecessary risks.
Wire Pressure Switch
“wire pressure switch” When it comes to electrical wiring, a wire pressure switch is an essential component to help control the flow of electricity. Essentially, it’s a switch that relies on pressure (often from a fluid like air or water) to control whether the circuit is open or closed. In other words, when the pressure reaches a certain level, the switch activates and allows electricity to flow through the circuit.
This can be incredibly useful in a variety of applications, from controlling the operation of heating and cooling systems to regulating the pressure in hydraulic machinery. One important thing to keep in mind when installing a wire pressure switch is to make sure you are following proper electrical safety protocols. It’s important to isolate the power source before making any electrical connections to ensure that you don’t accidentally shock yourself or cause damage to the wiring.
With the right precautions and expertise, however, a wire pressure switch can be a highly effective way to control electricity flow and ensure that your systems are operating as they should be.
Testing and Maintenance
Installing a 60 gallon air compressor may sound like a daunting task for a beginner, but with the right tools and guidance, it can be done with ease. Firstly, identify a suitable location for the air compressor; the site should be away from moisture and should have plenty of ventilation. Once you’ve found a suitable site, ensure that the compressor is on a sturdy base and secure it firmly.
Connect the air compressor to the power source and ensure that all the parts are well-connected. Now turn on the compressor and let it run for a few minutes to ensure that everything is working as expected. Testing is an essential part of the installation process and should be carried out to ensure that the compressor is working correctly.
Finally, to ensure optimal performance from your 60 gallon air compressor, regular maintenance is necessary, including a weekly check of the oil levels, filters, and belt tension. With a little bit of care, your air compressor will last for many years and provide you with reliable service when you need it.
Check for Leaks
When it comes to testing and maintaining your home or business’s plumbing system, it’s crucial to check for leaks regularly. Even small leaks can waste hundreds of gallons of water a day and cause water damage, leading to expensive repairs. Leaks commonly occur at the joint connections, showerheads, faucets, and toilet flappers.
You can detect a leak by checking your water bill for unexpected increases, noticing the sound of running water when the fixtures are off, or inspecting for water stains or puddles. A professional plumber can conduct pressure and dye tests to locate leaks that are hidden from the naked eye. It’s always better to detect and fix leaks right away before they cause more significant issues, so be sure to keep a close eye on your plumbing system and call a plumber immediately if you suspect a leak is present.
Don’t let an unnoticed leak waste your time and money. Check for leaks regularly!
Test the Air Compressor
An essential aspect of maintaining an air compressor is regularly testing it for optimal performance. Testing your air compressor ensures that all parts are working correctly, and potential issues are identified early on before they turn into bigger problems. One of the critical components to check during testing is the tank pressure.
Simply turning on the air compressor and monitoring the tank pressure gauge can give you an idea of how well your compressor is functioning. If the pressure drops quickly, it may be a sign of a leak or a faulty pump. Additionally, you can test the compressor’s airflow by using a tool such as a blowgun or tire inflator.
These tools will help you determine if the compressor is producing enough airflow needed for your projects. Regularly testing your air compressor can prevent future repairs, save money, and keep your compressor running efficiently.
Regular Maintenance Schedule
Regular Maintenance Schedule Keeping your systems in good shape requires regular maintenance. A maintenance schedule is essential to keep everything running smoothly and prevent problems before they occur. Testing and maintenance should be carried out regularly to identify any potential issues and fix them as soon as possible.
This can help to extend the lifespan of your equipment and save you money in the long run. Regular testing and maintenance can also prevent downtime and ensure that your systems are working efficiently. By following a regular maintenance schedule, you can rest assured that your equipment is in top shape and ready to perform when you need it.
So, don’t neglect your systems and make sure you’re following a regular maintenance schedule to keep everything running smoothly.
Conclusion
Congratulations, you have successfully learned how to install a 60 gallon air compressor! Now when your neighbors hear the satisfying whoosh of compressed air, they will know that you are a true DIY master. Just remember to always take safety precautions, read the instructions carefully, and never underestimate the power of a good air compressor. With this knowledge, you’ll be ready to take on any project that comes your way – from basic home repairs to the construction of a giant inflatable balloon of yourself.
So go ahead, embrace the power of compressed air and let your creativity soar!”
FAQs
What are the dimensions of a 60 gallon air compressor?
The dimensions of a 60 gallon air compressor vary depending on the model, but on average, they are around 24 inches in diameter and 70 inches tall.
Can a 60 gallon air compressor be installed outdoors?
Yes, a 60 gallon air compressor can be installed outdoors, but it is recommended to keep it in a covered or sheltered area to protect it from the elements.
How much does a 60 gallon air compressor weigh?
The weight of a 60 gallon air compressor varies depending on the model, but on average, they weigh around 200-400 pounds.
How much horsepower do I need for a 60 gallon air compressor?
The horsepower needed for a 60 gallon air compressor depends on the intended use. Generally, a 3-5 horsepower motor is sufficient for most applications.
Can a 60 gallon air compressor be used for industrial applications?
Yes, a 60 gallon air compressor can be used for industrial applications, but it may not have the power or capacity to meet the demands of heavy-duty use.
Do I need to install a separate electrical circuit for a 60 gallon air compressor?
Yes, a 60 gallon air compressor typically requires a dedicated electrical circuit to avoid overloading the existing circuits.
Can a 60 gallon air compressor be used with multiple tools at the same time?
Yes, a 60 gallon air compressor can be used with multiple tools at the same time, but it is important to ensure that the compressor has enough air capacity to power all the tools.