How to Regulate Air Compressor Pressure: A Comprehensive Guide for Optimum Performance
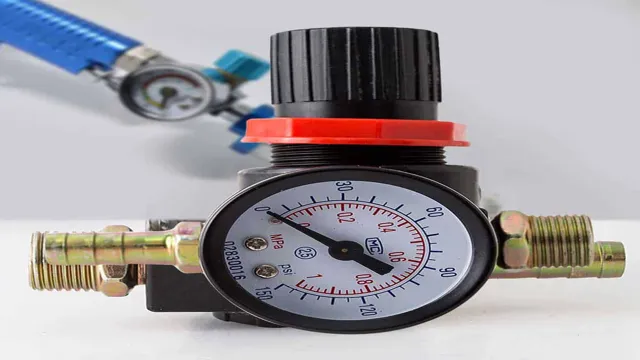
Have you ever been in a situation where the pressure of your air compressor was too high or too low for the task at hand? Regulating air compressor pressure is an essential skill that every DIYer or professional should know. Whether you’re using an air compressor to power your tools, inflate tires or paint, understanding how to adjust the air compressor pressure can make a huge difference in the quality of your work. Regulating the pressure of an air compressor is not rocket science, but it requires a bit of technical know-how.
In this blog post, we’ll share simple steps on how to regulate air compressor pressure and keep it at a consistent level, ensuring that your tools or equipment perform at their best. From understanding the different types of regulators to setting the desired pressure, we’ll equip you with all the information you need to optimize your air compressor performance. So, are you ready to learn how to regulate air compressor pressure like a pro? Let’s get started!
Understanding Air Compressor Pressure
If you are using an air compressor, it is important to understand how to regulate the pressure for optimal performance. There are a few key factors to consider when adjusting the pressure on your compressor. Firstly, it is important to determine the required pressure for your specific tool or application.
This can typically be found in the user manual or online. Once you have this information, you can adjust the pressure using the regulator knob on your compressor. It is important to not exceed the maximum pressure rating for your compressor as this can lead to dangerous situations such as burst hoses or damaged equipment.
Regularly checking and adjusting the pressure on your air compressor can ensure that it is operating efficiently and safely.
What is an Air Compressor Pressure Regulator?
An air compressor pressure regulator is a vital component that helps regulate the pressure in an air compressor. It works by adjusting the airflow into the compressor and maintaining a consistent and safe pressure level. The regulator controls the pressure by limiting the amount of compressed air that is released and allows for the compressor to function efficiently.
Understanding the importance of maintaining the correct air pressure is essential in ensuring the longevity of your air compressor and equipment. Too much pressure causes mechanical stress on the equipment and can cause it to fail prematurely. On the other hand, not enough pressure can result in subpar performance and slower work output.
By using an air compressor pressure regulator, you can adjust the pressure as needed and ensure that your equipment is running at optimal levels. A properly functioning air compressor pressure regulator is critical for the safety and efficiency of any pneumatic system.
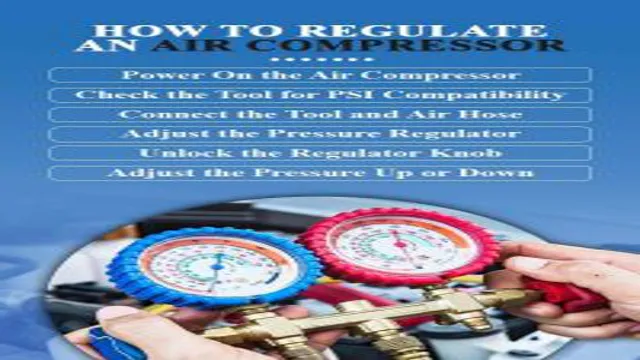
Why Regulate Air Compressor Pressure?
Air compressor pressure is an essential aspect to consider when working with compressed air systems. Regulating air compressor pressure helps to maintain the desired pressure levels, which ensures optimal compressed air performance and reduces energy consumption. Over-pressurization can lead to equipment failure and leaks, while low pressure can result in production inefficiency and poor quality outcomes.
By regulating air compressor pressure, operators can keep the system running smoothly, preventing costly repairs and downtime. Think of it like driving a car – you wouldn’t want to go too fast and risk crashing, but you also wouldn’t want to drive too slowly and cause a traffic jam. Similarly, by regulating air compressor pressure, you can maintain a safe and efficient system that keeps your operations running smoothly.
Steps to Regulate Air Compressor Pressure
If you’re new to using an air compressor, one of the most important things you’ll need to learn is how to regulate its pressure. Thankfully, this is a relatively simple process that you’ll be able to master in no time. The first step is to identify the pressure limit of your particular compressor, which should be listed in the manual.
Once you know this, you can use the pressure regulator to adjust the pressure to the desired level. Make sure to use a pressure gauge to monitor the pressure accurately, and adjust the regulator accordingly until you reach the right level. It’s also important to keep an eye on the pressure as you work, as changes in temperature and other factors can affect the pressure level.
With a little practice, regulating the pressure of your air compressor will become second nature.
Step 1: Determine Desired Pressure
One of the essential steps in regulating air compressor pressure is determining the desired pressure level. Whether you plan to use an air compressor for DIY projects at home or for professional applications, it’s crucial to set the correct pressure. The ideal air pressure depends on the type of tool or application you plan on using.
For instance, if you’re using a nail gun, you need to set the air pressure at around 100 PSI. On the other hand, some air compressors require lower pressure levels for specific tools. Therefore, it’s essential to read through the manufacturer’s recommendations to ensure proper pressure regulation.
By determining the desired pressure, you can avoid problems such as underinflated tires or damaged tools due to excessive pressure. Remember to always keep in mind the working environment and application when choosing the right pressure level.
Step 2: Adjust Pressure Regulator Knob
When it comes to regulating the air compressor pressure, adjusting the pressure regulator knob is a crucial step. But before you even start adjusting the knob, it’s essential to understand your specific air compressor and what pressure it requires to perform at its best. Once you have that information, locate the pressure regulator knob and turn it clockwise or counterclockwise to increase or decrease the pressure, respectively.
It’s crucial to make small adjustments and wait for the compressor gauge to catch up to the new setting before making any additional changes. Always ensure that the pressure does not exceed the limits set for your compressor, as it can damage the machine and put you at risk. With careful, gradual adjustments, you should be able to achieve the perfect pressure setting that suits your needs.
Remember to regularly check and adjust the pressure as needed for smooth and efficient air compressor performance.
Step 3: Monitor Pressure Gauge
When using an air compressor, it’s important to monitor the pressure gauge regularly to ensure that the pressure remains at the desired level. Keeping an eye on the gauge allows you to adjust the regulator knob as needed to maintain consistent pressure throughout your work. This not only ensures proper functioning of your tools but also helps prevent damage to them.
It’s also essential to keep an eye on the gauge during the cooling-down period after use as pressure can rise as the air cools. As a result, it’s important to pay close attention to the pressure gauge when regulating air compressor pressure. By doing so, you’ll be able to achieve the optimal level of pressure for your specific application, ensuring smooth operation and longevity of your equipment.
Maintaining Proper Pressure Regulation
One of the most essential components of maintaining your air compressor is keeping the pressure regulation in check. To regulate the air compressor pressure, you need to first locate the regulator knob that’s usually located on the compressor tank. Turning it clockwise or counterclockwise will adjust the pressure accordingly.
It’s important to set the pressure to the manufacturer’s recommended levels as excessive pressure can cause damage, while insufficient pressure can lead to poor performance. To ensure that the pressure stays constant, you should also regularly check the pressure gauge and adjust it as needed. Proper pressure regulation not only improves the efficiency and lifespan of your compressor but also enhances your safety while working with compressed air.
So make sure you have a good understanding of how to regulate air compressor pressure, and follow the above tips to maintain your compressor in tip-top condition.
Regularly Check and Adjust Pressure Regulator
Maintaining proper pressure regulation is essential for making sure that your equipment runs smoothly and efficiently. One critical step in maintaining proper pressure regulation is regularly checking and adjusting your pressure regulator. This is especially important if you are using your equipment for extended periods or in harsh environments.
A pressure regulator helps to ensure that your equipment operates consistently at a particular pressure level, protecting it from wear and tear caused by inconsistent or excessive pressure. Checking your pressure regulator periodically will help to ensure that it is functioning correctly and that your equipment is performing at its best. Be sure to make adjustments to your pressure regulator as needed to maintain the desired level of pressure.
A properly functioning pressure regulator will help to extend the lifespan of your equipment and prevent costly repairs or replacements in the long run. So, don’t forget to give your pressure regulator some attention during your regular maintenance routine to keep your equipment running smoothly!
Keep Air Compressor Components Clean and Lubricated
Air compressor components play a crucial role in keeping the pressure regulated within the system. Maintaining the proper pressure regulation is essential for efficient and safe operation. One way to ensure this is by regularly cleaning and lubricating the components.
Dirty or clogged components can cause the pressure to fluctuate, resulting in subpar performance and even damage to the compressor. Lubrication, on the other hand, helps reduce friction between moving parts, which can also affect pressure regulation. By keeping the components clean and lubricated, you can ensure that your air compressor runs smoothly and efficiently, making it last longer and saving you money on repairs and maintenance.
Conclusion
In summary, regulating air compressor pressure is an essential skill to ensure that your tools and equipment operate smoothly and efficiently. By following these simple steps, you can responsibly control the pressure and prevent any unwanted accidents or mishaps. Whether you’re a DIY enthusiast or a seasoned professional, mastering the art of pressure regulation will help you unleash the full potential of your air compressor and take your projects to new heights.
So don’t let the pressure get to you, take charge of your air compressor today and watch your creativity soar!”
FAQs
1. How do I adjust the regulator on my air compressor to control pressure? A: Locate the regulator knob and turn it clockwise to increase pressure and counterclockwise to decrease pressure. 2. What should be the ideal pressure range for an air compressor? A: The ideal pressure range for air compressors is typically between 90-110 psi (pounds per square inch). 3. Can I use a pressure gauge to measure the pressure of my air compressor? A: Yes, a pressure gauge can be used to accurately measure the pressure of your air compressor. 4. How often should I check the pressure level of my air compressor? A: It is recommended to check the pressure level of your air compressor before each use and periodically throughout the day. 5. What happens if I exceed the recommended pressure range of my air compressor? A: Exceeding the recommended pressure range of your air compressor can result in the risk of injury, damage to the compressor, and decreased efficiency. 6. Why does my air compressor pressure fluctuate? A: Air compressor pressure can fluctuate due to factors such as temperature changes, air leaks, or an improperly functioning regulator. 7. Can I adjust the pressure of my air compressor while it is running? A: No, it is not recommended to adjust the pressure of your air compressor while it is running. Always turn off the compressor and ensure it is depressurized before making any adjustments.