If you own an air compressor, you know how important it is to keep it in good working condition. But what do you do when you suddenly discover a hole in the compressor tank? You can’t just let it be, as that could lead to further damage or even an explosion. The good news is that it’s possible to weld a hole in an air compressor tank and get it back to its full function.
It may seem daunting, but with the right tools and instructions, you can do it yourself. In this guide, we’ll walk you through the process step-by-step so you can get your air compressor tank back to working like new. So let’s get started!
Safety Precautions When Welding
Welding is a relatively straightforward and common process. However, there are certain safety precautions that need to be followed to avoid serious accidents. Firstly, always wear protective gear such as gloves, helmet, goggles, and a fire-resistant jacket.
Secondly, ensure that you are in a well-ventilated area as welding produces toxic fumes that can be dangerous to inhale. But coming to the question, can you weld a hole in an air compressor tank? The answer is yes, but only if certain precautions are taken. Before welding, make sure the tank is empty of any air or gas.
A small spark from the welder can ignite any residual fuel or gas in the tank, causing a blast. Additionally, ensure that the tank is grounded, and any combustible materials are kept away from the welding area. Finally, use a qualified welder who understands the process, can follow these precautions, and has experience in repairing compressed air tanks.
Safety should be the top priority when welding, and these precautions should never be overlooked, especially when repairing a container that stores compressed air or gas.
Understanding the Type of Air Compressor Tank
When working with an air compressor tank, it is important to understand the type of tank you are dealing with. There are two main types of air compressor tanks: portable and stationary. Portable tanks are often small and designed to be easily transported, while stationary tanks are larger and meant to stay in one place.
Regardless of the type of tank, safety should always be a top priority when using them. This is particularly true when welding, where sparks and flames can be hazardous. Some safety precautions to take when welding with an air compressor tank include ensuring the tank is properly grounded, keeping flammable materials away from the welding area, and wearing appropriate protective gear such as gloves and goggles.
By taking these precautions, you can help ensure a safe and successful welding project.
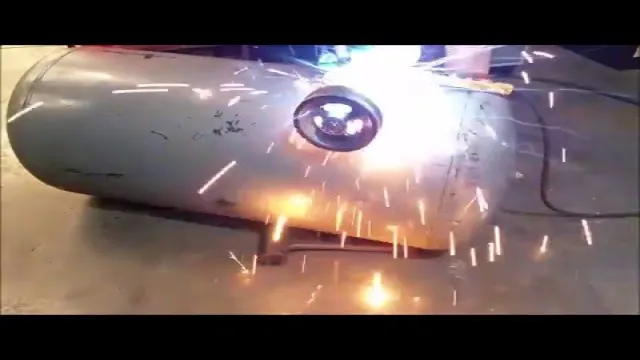
Proper Cleaning and Preparation of the Affected Area
Proper cleaning and preparation of the affected area is essential when welding, and safety precautions must be taken to avoid any potential accidents. First and foremost, it’s imperative to wear protective gear, including gloves, safety glasses, and a welding helmet. Before beginning, remove any flammable materials from the area and ensure that the workspace is well-ventilated to avoid inhaling dangerous fumes.
It’s also important to clean the work surface thoroughly to remove any rust, dirt, or grease that can affect the quality of the weld. This ensures that the welding arc has a clean contact surface to prevent contamination and maintain proper penetration depth. Additionally, inspect the welding equipment to ensure they are functioning correctly and that the welding rods are not damaged or contaminated.
With these safety precautions in mind, you can ensure that the welding process is productive, and the resulting weld will be of high quality.
Welding Techniques for Air Compressor Tanks
If your air compressor tank has a hole, you may be wondering whether you can weld it. The answer is that it depends on the type of tank you have. Welding is a common method for repairing air compressor tanks, but it is not always the best solution.
If you have a steel tank, it may be possible to weld the hole closed. However, welding can be dangerous and it requires a great deal of skill and expertise. If you are not experienced with welding, you should not attempt to do it yourself.
Instead, it is best to contact a professional welder who can assess the damage and determine the best course of action. If welding is not an option, there are other methods for repairing air compressor tanks, such as using epoxy or installing a patch. Whatever method you choose, it is important to take the time to carefully inspect your tank for any other signs of damage or weakness before using it again.
Gas Metal Arc Welding (GMAW)
Gas Metal Arc Welding (GMAW) If you’re someone who works with air compressor tanks, then you know that welding is an essential aspect of maintaining them. The Gas Metal Arc Welding (GMAW) technique is a popular choice for welding air compressor tanks. This technique involves using a wire electrode that melts and joins metal pieces together through an electric arc.
The process uses a shielding gas to protect the molten metal from the atmosphere. This technique is ideal for welding stainless steel and aluminium, which are commonly used in air compressor tanks. One of the advantages of GMAW is that it produces high-quality welds that are strong and aesthetically appealing.
Moreover, this method is more efficient and faster than many other welding techniques. With GMAW, the welders can work on thin materials easily without causing too much damage. By using GMAW, welders can ensure that their air compressor tanks are durable and long-lasting.
Shielded Metal Arc Welding (SMAW)
When it comes to welding techniques for air compressor tanks, Shielded Metal Arc Welding (SMAW) is a commonly used method. Also known as stick welding, SMAW involves using an electrode (or “stick”) made of filler metal that is coated in flux. The electrode is connected to a power source and when struck, an arc is created that melts the filler metal and deposits it onto the joint to be welded.
The flux coating protects the molten metal from contamination by the air and creates a slag that can be easily removed after the weld cools. SMAW is a versatile and relatively easy welding technique that can be used in a variety of positions, making it a great choice for welding air compressor tanks. However, it does require a certain level of skill and experience to achieve high-quality welds.
Gas Tungsten Arc Welding (GTAW)
Gas Tungsten Arc Welding, Air Compressor Tanks, Welding Techniques. When it comes to welding air compressor tanks, Gas Tungsten Arc Welding (GTAW) is a preferred method due to its precision, control, and quality results. GTAW, also known as Tungsten Inert Gas (TIG) welding, involves using a non-consumable tungsten electrode to create an arc that melts the metal and a shielding gas to protect the weld from oxidation and contamination.
This method is ideal for welding thin materials, such as those used in air compressor tanks, as it allows for a delicate welding process and produces a clean, smooth finish. The key to successful GTAW welding of air compressor tanks is to thoroughly clean and prep the metal surface. Any contaminants or impurities can affect the weld’s integrity and result in leaks or other issues down the line.
GTAW welding also requires a skilled and experienced welder who can control the temperature and welding speed to avoid overheating the metal and causing warping or other damage. Overall, GTAW is a reliable and efficient method for welding air compressor tanks, producing strong, high-quality welds that can withstand the rigors of everyday use. By understanding the process and taking care to prep and maintain equipment properly, welders can achieve reliable, long-lasting welds that keep air compressors running smoothly for years to come.
Post-Welding Inspection and Testing
If you have an air compressor tank with a hole, you might wonder if it’s possible to weld that hole shut. The answer is yes, but it’s important to follow proper post-welding inspection and testing procedures to ensure safety and effectiveness. Before welding, make sure the tank is empty and free of any flammable or explosive materials.
Once the welding is complete, inspect the area thoroughly for any cracks or other defects that may have occurred during the welding process. Pressure testing the tank is also crucial to ensure the weld has held up under the pressure of normal use. It’s important to note that not all holes can be welded, especially if they are in critical areas of the tank.
Always consult with a professional welder and follow best practices for safety and effectiveness when repairing any damaged air compressor tank.
Visual Inspection
Visual inspection is an essential part of post-welding inspection and testing. It involves a thorough assessment of the welded joint or surface using visual aids such as magnifying glasses, mirrors, and cameras. The objective is to identify any surface defects, such as cracks, porosity, undercutting, and improper weld bead profiles.
Visual inspection is a non-destructive testing method that can reveal defects that can then be repaired before the component or structure is put into service. It is a cost-effective and non-invasive way to assess the quality of a welded joint or surface. In industries that demand high levels of safety and reliability, visual inspection is a crucial step in ensuring that welded structures or components are safe and meet the required standards.
With its ability to detect even the slightest defects, visual inspection is a valuable tool in the welding industry.
Pressure Testing
Pressure testing is a crucial step in ensuring the safety and integrity of welded joints. After welding, it is important to perform post-welding inspection and testing, including pressure testing, to ensure that the weld is strong enough and will not fail under pressure. Pressure testing involves subjecting the weld to a specific level of pressure, often higher than the normal operating pressure, to check for leaks or other defects.
This type of testing can help identify any weaknesses in the weld that could lead to failure over time. By detecting these issues early on, it is possible to make necessary repairs or modifications to avoid costly and potentially dangerous failures in the future. In short, pressure testing is a critical component of post-welding inspection and testing that helps ensure that welded joints are strong, safe, and reliable.
Conclusion
In conclusion, attempting to weld a hole in an air compressor tank is about as wise as trying to stop a leak in a dam with duct tape. Sure, it may seem like a quick fix, but the consequences could be disastrous. The high pressure and volatile nature of the compressed air in the tank make it a recipe for disaster.
So, rather than trying a DIY fix, invest in a replacement tank and breathe easy knowing your compressed air system is safe and sound.”
FAQs
What is the proper way to weld a hole in an air compressor tank?
The proper way to weld a hole in an air compressor tank is to clean the surface and use a specialized welding technique, such as TIG or MIG welding, to ensure a strong bond.
Can a hole in an air compressor tank be patched instead of welded?
Yes, a hole in an air compressor tank can be patched with an epoxy or putty specifically designed for metal repairs. However, welding is generally considered a stronger and more reliable solution.
Is it safe to weld an air compressor tank yourself, or should it be done by a professional?
It is generally recommended to have a professional weld an air compressor tank to ensure proper safety measures are taken. However, if you have the necessary welding skills and equipment, it can be done yourself.
Are there any safety precautions you should take when welding an air compressor tank?
Yes, when welding an air compressor tank, it is important to wear proper protective gear such as gloves, long sleeves, and a welding helmet. The area should also be well-ventilated to prevent inhalation of fumes.
Can a leaking air compressor tank be repaired, or should it be replaced?
Depending on the severity and location of the leak, an air compressor tank can often be repaired by welding or patching. However, if the tank is severely damaged or corroded, it may be safer and more cost-effective to replace it.
How often should you check your air compressor tank for leaks and damage?
It is recommended to inspect your air compressor tank for leaks and damage at least once a year, and more frequently if it is used often or in harsh conditions.
Can I use a damaged air compressor tank if it still seems to be holding air and functioning?
It is not recommended to use a damaged air compressor tank, as it can be dangerous and lead to serious injury or property damage. It is important to have any damage or leaks repaired or the tank replaced before use.