How a Metal Lathe Works: An In-Depth Guide to Understanding Lathe Mechanics

Are you curious about how a metal lathe works? If so, you’ve come to the right place! A metal lathe is a machine tool used to shape and cut metals with precision. It’s a versatile machine that can be used for a variety of tasks, including turning, drilling, and threading. One of the key components of a metal lathe is the spindle, which is powered by a motor and holds the workpiece in place.
The cutting tool is then moved along the workpiece to create the desired shape or cut. Depending on the type of lathe, the cutting tool can be controlled manually or with computer numerical control (CNC). If you’ve ever used a pencil sharpener, you can think of a metal lathe as a sophisticated version of that.
Just as a pencil sharpener carefully removes just the right amount of wood from a pencil to make it sharp, a metal lathe precisely cuts away metal to create the desired shape. However, unlike a pencil sharpener, a metal lathe is highly versatile and can create complex shapes with extreme accuracy. Whether you’re a professional machinist or a curious DIYer, understanding how a metal lathe works can open up a world of possibilities.
So, let’s dive in and explore the world of metal lathes together!
Overview of a metal lathe
A metal lathe is a machinery tool used to remove material from a metal workpiece through a rotating cut. The material to be removed is held in place by clamps or chucks, and the workpiece is rotated against a cutting tool. This tool, which can be made of high-speed steel, tungsten carbide, or diamond-tipped material, cuts away small chips from the surface of the workpiece as it rotates.
A lathe may have several tools, each of which can be adjusted to create different cuts or shapes on the material. To operate the lathe, the workpiece must first be secured in place and the tool set at the right height and angle. The spindle is then set into motion, rotating at high speeds to allow the tool to cut through the metal.
With proper care and precision, a lathe can produce intricate shapes and smooth finishes on metal components with great accuracy. Overall, a metal lathe is an essential tool for any individual or business involved in metalworking.
Understanding its components and functions
A metal lathe is an important tool used in machining processes for cutting, drilling and shaping metal into different forms. It comprises of several components such as the headstock, tailstock, carriage, bed, gears, and chuck, each serving a unique function. The headstock includes a spindle that rotates the metal piece while the tailstock holds and supports one end of the metal to be worked upon.
The carriage holds the cutting tool which cuts into the metal, and it moves along the bed, which provides support and stability to the metal lathe. The gears change the speed and direction of the rotation of the spindle. Lastly, the chuck grips the metal and holds it in place while the cutting tool shapes it.
It is essential to understand these components and their functions to effectively operate and maintain a metal lathe and produce the desired results. By regularly inspecting and maintaining the various parts, a metal lathe can be used for a long time and ensure the precision and accuracy of the products created using it.
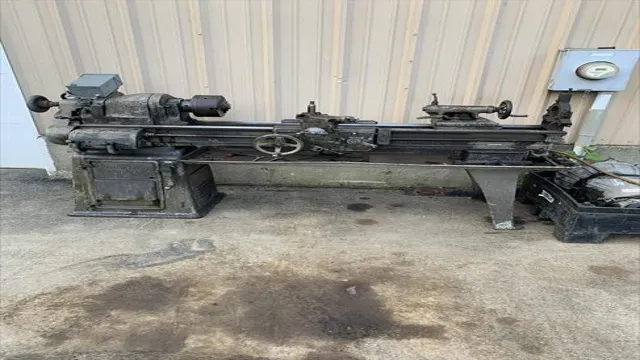
Types of metal lathes available in the market
A metal lathe is a beneficial machine commonly used in industrial settings to cut and shape metal workpieces. These lathes work by rotating a workpiece while a cutting tool removes material from it, creating an accurate and precise cut. There are several types of metal lathes available in the market, ranging from smaller benchtop machines to larger industrial-grade models.
Small benchtop models are used for light-duty work, while larger lathes are designed for cutting larger or more complex pieces of metal. Some common types of metal lathes include engine lathes, turret lathes, and CNC lathes. Engine lathes are the most common type of lathe and are ideal for general-purpose cutting, while turret lathes are used to cut multiple pieces of metal simultaneously.
CNC lathes are computer-controlled machines suitable for creating complex and precise metal parts. No matter what type of lathe you choose, each machine provides a unique set of cutting capabilities that can help you achieve the desired results for a range of metalworking projects.
Preparation of a metal lathe for operation
Metal lathes are an essential tool for any metalworking hobbyists or professionals. Operating a lathe may seem overwhelming, but with proper preparation, it can be a fun and exciting experience. To begin, make sure the lathe is properly cleaned and lubricated before operating.
It’s also important to wear proper gear such as gloves, eye protection, and comfortable non-loose clothing. Once ready, secure the metal you will be working with onto the spindle, ensuring it is centered properly. Look for the feed and speed controls and adjust them accordingly depending on the desired outcome and the type of metal being used.
The metal lathe uses a cutting tool to remove material from the workpiece, so it’s important to be mindful of the sharpness of the tool and avoid overheating. With practice and patience, anyone can learn how a metal lathe works and produce finely crafted metalwork.
Safety precautions to be considered
When it comes to metal lathe operation, safety should always be the top priority. Preparing the lathe for use is an important step in ensuring safe and efficient operation. Before starting any work, it’s crucial to conduct a thorough inspection of the machine to ensure that all parts are in proper working order.
Check the belts, gears, and bearings for any signs of wear or damage. Make sure that all guards and safety devices are in place and functioning correctly. It’s also essential to keep the workspace clean and free of clutter, as this can prevent accidents and injuries.
Always wear appropriate personal protective equipment, such as safety glasses and gloves. By taking these precautions, you can minimize the risk of injury and ensure that your metal lathe performs at its best.
Installation and alignment of the workpiece
When preparing a metal lathe for operation, it’s crucial to be mindful of safety measures and the proper techniques for aligning and securing the workpiece. Firstly, inspect the machine for any damage or wear and replace any faulty components as necessary. Next, ensure that the spindle and tailstock are aligned correctly before securing the workpiece between centers or in a chuck.
Use a dial indicator to check for any runout or misalignment and adjust accordingly. Always use appropriate personal protective equipment, such as safety glasses and gloves, and avoid loose clothing or jewelry. Safely operating a metal lathe requires attention to detail, so take the time to properly set up the machine and align the workpiece for accurate results.
Remember to always adhere to the manufacturer’s instructions and guidelines for safe and efficient operation.
Metal turning process on a lathe
If you’re interested in machining, you might be curious about how a metal lathe works. Essentially, a lathe is a machine that rotates a workpiece while a cutting tool removes material from the surface of the workpiece to create a shape or finish. This process is called turning, and it’s one of the most common types of machining operations.
The metal turning process on a lathe involves several parts, including the lathe bed, which provides a stable foundation for the machine, and the headstock, which holds and rotates the workpiece. The cutting tool is mounted on a tool post, which moves along the length of the workpiece to make cuts. Operators adjust the cutting speed, depth, and angle to achieve the desired shape or finish.
Overall, a metal lathe is a versatile and precise tool that can create a variety of parts and components for everything from household items to high-tech machinery.
Step by step explanation of cutting tool operation
Metal turning process on a lathe is an essential manufacturing process for producing various cylindrical components. The first step in this process is to select the lathe machine and the cutting tool. The lathe machine rotates the metal workpiece, while the cutting tool removes unwanted material from the workpiece to obtain the required shape and size.
The cutting tool is made of hardened steel and has a sharp tip that cuts the metal workpiece as it rotates. The machine operator sets the cutting speed, depth of cut, and feed rate based on the material being worked on and the desired finish. Once the lathe machine and the cutting tool are set up, the operator positions the workpiece on the machine’s chuck.
The chuck holds the workpiece securely in place and rotates it while the cutting tool moves along its length to remove material. The operator feeds the cutting tool into the workpiece gradually, and the tool removes a thin layer of material with each pass. As the tool moves along the workpiece, it creates chips of metal that are removed through the machine’s chip breaker.
The metal turning process on a lathe requires precision, skill, and experience to produce high-quality components. The operator must constantly monitor the machine and the cutting tool to ensure they are working correctly, and adjust the settings if necessary to obtain the desired finish. In addition, the operator must be familiar with the different types of cutting tools and their uses, as well as the various materials that can be worked on with a lathe.
In conclusion, metal turning process on a lathe involves using a lathe machine and a cutting tool to remove unwanted material from a metal workpiece. The process requires precision and skill to obtain the desired finish, and the operator must be familiar with the lathe machine, cutting tools, and the materials being worked on. Overall, the metal turning process on a lathe is an essential manufacturing process that produces various cylindrical components used in different industries.
Application of tool angles and feed rates
Metal turning process on a lathe is a fundamental machining operation. It involves the removal of material from a rotating workpiece using a cutting tool. During this process, the tool angle and feed rate are critical variables that affect the outcome of the operation.
The tool angle determines the shape of the chip formed during cutting and the cutting force that is generated. A smaller tool angle results in a thinner and more extended chip and, therefore, less cutting force. On the other hand, a larger tool angle causes a thicker and shorter chip and, therefore, more cutting force.
The feed rate is the speed at which the cutting tool is advanced into the workpiece. It directly affects the surface finish, chip formation, and cutting forces. However, using a high feed rate increases the likelihood of tool wear and shortens tool life.
Thus, it’s essential to find the optimal tool angle and feed rate for specific machining operations to achieve the desired result. Overall, with the correct application of tool angles and feed rates, metal turning on a lathe can produce high-quality and precise components for various industries.
Lathe control settings
When it comes to understanding how a metal lathe works, one important aspect to consider is the control settings. These settings determine the speed and position of the cutting tool as it moves across the rotating workpiece, shaping it into the desired shape. Modern lathes come with a range of sophisticated control settings, such as computer numerical control (CNC), which allows for precise and complex cuts to be made with ease.
However, even on a basic manual lathe, understanding how to adjust the control settings is crucial to getting the best results. It’s all about finding the right balance between the spindle speed, the feed rate, and the depth of cut, as well as positioning the cutting tool correctly. Experimentation and practice are key, as is a good understanding of the materials you are working with and the type of finish you want to achieve.
With patience and persistence, anyone can master the art of lathe control settings.
Speed and feed regulation for turning operations
When it comes to turning operations on a lathe, the speed and feed of the cutting tool are crucial for achieving optimal results. The control settings on the lathe play a major role in regulating these parameters. Speed regulation refers to the rotational speed of the spindle, while feed regulation controls the rate at which the cutting tool moves along the workpiece.
These settings determine the quality and accuracy of the finished product, as well as the tool life and surface finish. It is important to pay close attention to the material being machined, as different materials require different speeds and feeds to yield the best results. By properly adjusting the control settings on the lathe, operators can improve productivity and efficiency while ensuring consistent quality.
So, before starting a turning operation, take the time to review the material specifications and adjust the lathe control settings accordingly for optimal results.
Conclusion
In summary, a metal lathe works by using the power of physics and the precision of engineering to turn raw materials into finely-tuned masterpieces. With the skillful hands of a machinist and the force of a spinning spindle, metal is shaped, cut, and carved into intricate designs and functional parts. It’s a symphony of form and function, a dance between man and machine, and a shining example of the ingenuity and creativity of the human mind.
So whether you’re a metalworking enthusiast or simply curious about the inner workings of this magnificent machine, there’s no denying that a metal lathe is a thing of beauty and purpose.”
FAQs
What is a metal lathe and how does it work?
A metal lathe is a machine tool that rotates a workpiece on its axis to perform various operations such as cutting, drilling, or shaping. The tool is stationary while the workpiece moves. The machine works by using a motor to spin the workpiece and a series of gears and belts to transmit the power to the cutting tools.
What are the different types of metal lathes available and how do they differ?
There are several types of metal lathes available, including engine lathes, bench lathes, turret lathes, and CNC lathes. Engine lathes are the most popular and versatile lathes, used for a wide range of applications. Bench lathes are smaller and designed for lighter work, while turret lathes are used for complex and repetitive operations. CNC lathes are computer-controlled and automated for precision and efficiency. The main difference between these lathes is their size, capacity, and specific features.
What are the main components of a metal lathe and how do they work together?
A metal lathe consists of several main components, including the headstock, tailstock, bed, carriage, cross slide, apron, and cutting tool. The headstock holds the spindle and chuck, which rotate the workpiece. The tailstock supports the other end of the workpiece and allows for drilling or boring. The bed provides a stable base for the lathe, while the carriage and cross slide move the cutting tool back and forth across the workpiece. The apron controls the feed and speed of the cutting tool.
What are the safety precautions to take when using a metal lathe?
When using a metal lathe, it is important to wear eye protection, gloves, and proper clothing. Keep loose clothing, jewelry, and long hair away from the lathe. Make sure the lathe is properly grounded and that all guards are in place. Always use the proper tools and techniques for each job, and never force the workpiece or cutting tool. Stop the lathe immediately if there is anything unusual or if you feel uncomfortable.
What are some common applications of metal lathes in the metalworking industry?
Metal lathes are used in a wide variety of applications in the metalworking industry, such as turning, facing, drilling, boring, threading, grooving, and knurling. They are used to make precision parts, such as shafts, gears, valves, bearings, and bushings. Lathes are also used for repair and maintenance work, such as reaming, tapping, and polishing. Metal lathes are a fundamental tool in the metalworking industry and are essential for many manufacturing processes.