How Cold Welding Machine Works: Step-by-Step Guide to Efficient Cold Welding

Have you ever wondered how metals are joined together without the use of heat or pressure? The answer lies in the process of cold welding, which is achieved through the use of specific machines designed for this purpose. Cold welding machines are becoming increasingly popular due to their efficiency and cost-effectiveness in joining metals. In this blog post, we will dive into how cold welding machines work and what makes them unique compared to traditional welding methods.
From the mechanics of the machines to the principles behind the process, we will cover every aspect of this fascinating technology. So, let’s get started and explore the world of cold welding machines!
Introduction
Have you ever wondered how cold welding machines work? These machines are essential in joining materials without heat, which is useful in preserving their properties. Cold welding is a process where metal surfaces are joined under pressure, without heat or added materials, by removing their oxide layers to achieve a clean surface. The welding process works by pressing two surfaces together until they bond, creating an interface with a strong bond that is almost as strong as the original material.
Cold welding machines can be used to join various types of metals, like aluminum, copper, brass, and steel, and are used in several industries, including aerospace, automotive, and electronics. The process also ensures minimal waste as there is no need for additional materials such as adhesives, solders, or flux.
Definition of cold welding and its uses
Cold welding is a process that involves joining two pieces of metal together without the use of heat or soldering. Instead, it relies on the principle of diffusion, where atoms from each piece of metal migrate to the other and bond together. This process occurs because of the high pressure applied to the surfaces of the metals.
Cold welding is commonly used in the aerospace and electronics industries, where highly precise connections are required. It is also used in the construction of pipelines and other structures, where it provides a seamless and strong bond between metal components. Overall, cold welding is a fascinating and useful process that continues to find new applications in a variety of industries.
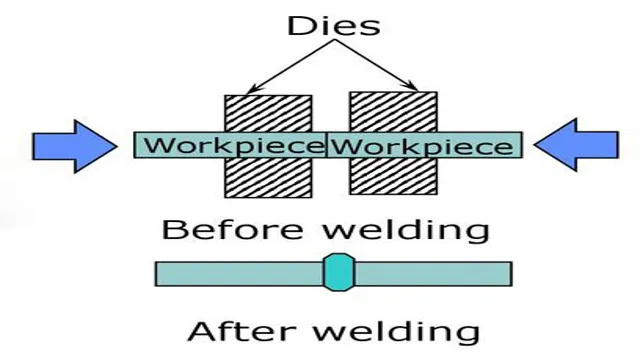
Principles of Cold Welding
If you’ve ever wondered how cold welding machines work, it all comes down to the principles of cold welding. Essentially, cold welding involves joining two metal surfaces together by applying pressure, without any heat or filler material. This is possible because of the atoms on the surface of the metals, which have a natural tendency to bond with each other.
When the two surfaces are pressed together, these atoms bond at the molecular level, creating a strong and seamless joint. Cold welding machines are designed to apply precise pressure to the surfaces, often using hydraulic or pneumatic systems, to ensure a tight bond. This process is particularly useful for joining metals that cannot be soldered or welded using traditional methods, and it is also quicker and more cost-effective than other bonding techniques.
Overall, the principles of cold welding allow for a reliable and efficient way to join metal surfaces together without using heat or filler material, making it a valuable technique for a wide range of applications.
Surface Preparation
One of the most important aspects of surface preparation for cold welding is understanding the principles behind the process. Cold welding involves the joining of two metals by applying pressure without the use of heat. In order for this process to be successful, the surfaces of the metals being joined must be thoroughly cleaned and free from any form of contamination.
Even the tiniest particle of debris can compromise the integrity of the bond between the metals, resulting in a weak joint. Abrasive blasting, chemical cleaning, and solvent wiping are all effective methods for removing contaminants from the surface of the metals prior to cold welding. By following these principles and taking the necessary care during surface preparation, strong and reliable joints can be achieved through cold welding.
Pressing and Forging the Materials
When it comes to fabricating metal parts, pressing and forging are two common techniques used to reshape materials into desired shapes. Cold welding, a process of bonding two materials together without the use of heat, is employed during the pressing and forging processes. The principle of cold welding relies on the compression of two clean metal surfaces in intimate contact with each other to create a strong bond between them.
During pressing, metal sheets are squeezed between two rollers to flatten and shape them. As the sheets are pressed, the surface area in contact with each other increases, and the pressure applied creates friction that cleans away surface contaminants, allowing the metal to bond through cold welding. Forging, on the other hand, involves reshaping a metal piece using pressure in a specific direction to create a desired shape.
The same principle of cold welding is used, as the metal surfaces are compressed and bonded together through cold welding upon application of force. The beauty of cold welding is that it allows for strength to be preserved in metal without compromising its structural integrity, making it an ideal technique for creating high-quality metal parts.
Types of Cold Welding Machines
A cold welding machine works by creating a strong bond between two metal surfaces without the need for heat or electricity. There are two main types of cold welding machines, including ultrasonic cold welding machines and pressure cold welding machines. Ultrasonic cold welding machines use high-frequency vibrations to bond metals together, while pressure cold welding machines rely on a combination of force and friction to create the bond.
Both types of machines can be used for a variety of applications, including joining thin metal sheets, repairing damaged metal parts, and creating electrical connections. Unlike traditional welding methods, cold welding does not produce any sparks or fumes, making it a safer and more environmentally-friendly option. Overall, cold welding machines are a valuable tool for anyone looking to join two metal surfaces without the need for heat or electricity.
Capacitive Discharge Welding
Capacitive Discharge Welding Cold welding machines, also known as capacitive discharge welding machines, come in different types depending on their functionality and usage. The most common types of cold welding machines are handheld portable units, benchtop models, and fully automated systems. Handheld machines are ideal for small to medium-sized welding jobs where precise control is required, while benchtop models are better suited for larger and more complex welding projects.
Fully automated systems are often used in industrial settings where high-volume welding is required. Capacitive discharge welding machines work by storing electrical energy in capacitors and then discharging it through a welding electrode to create a high-intensity arc that melts the surfaces of the metal being welded. These machines offer a faster and more cost-effective welding solution compared to traditional welding methods.
With the right machine and proper training, cold welding can be a reliable and efficient method for joining metal components.
Ultrasonic Welding
Ultrasonic Welding Ultrasonic welding is a popular choice in cold welding machines due to its ability to weld intricate parts and high-precision components. There are two types of ultrasonic welding machines: handheld and bench-top. Handheld machines are ideal for welding small parts such as wires, electronic components, and plastic products.
They are lightweight, portable, and easy to operate, making them perfect for on-site repairs. Bench-top machines, on the other hand, are designed for larger parts and high-volume production. They are more complex and require more setup time, but they offer precise control over parameters such as welding time, power, and amplitude.
Both handheld and bench-top machines work on the same principle: they use high-frequency vibrations to produce heat and weld two materials together. This technique eliminates the need for adhesives or fasteners and creates a strong and reliable bond between the parts. Overall, ultrasonic welding is an efficient and cost-effective method for assembly and repair of components in various industries, including automotive, aerospace, medical, and electronics.
Explosive Welding
Explosive Welding If you’re in the market for a cold welding machine, it’s important to understand the different types that are available. One type is a resistance welding machine, which uses an electrical current to fuse two pieces of metal together. Another type is a friction welding machine, which uses rotational friction to create heat and then applies pressure to join the metals.
However, explosive welding machines are a type of cold welding that uses explosives to create a powerful shock wave that fuses metals together. The process involves placing two metals in contact with each other and detonating explosives on one side, which generates a high-pressure shock wave that creates a metallurgical bond between the two metals. Explosive welding is often used to create bimetallic plates and components for the aerospace and defense industries.
Advantages and Disadvantages of Cold Welding
Cold welding is a unique process that joins two metals together without the need for heat or electricity. It works by applying high pressure to the metals, causing their atoms to bond together at the molecular level. Unlike traditional welding, cold welding produces little or no distortion or discoloration of the material being joined.
This results in a smooth, seamless finish that is both strong and durable. However, cold welding does have its downsides. For one, it is not suitable for all metals and materials, as some may not bond effectively.
Additionally, the process can be slow and labor-intensive, making it less efficient than other welding methods. Despite these limitations, cold welding remains a popular choice for applications where strength, aesthetics, and precision are critical, and heat damage is a concern.
Advantages
Cold welding is a process that uses high pressure and no heat to join two metal surfaces together. The advantages of cold welding are numerous, including the ability to join dissimilar metals, minimal distortion and reduced warping, and low energy consumption. Additionally, cold welding produces a clean joint with no oxidation or other impurities, making it ideal for use in sensitive applications such as electronics and medical devices.
Another advantage of cold welding is that it does not require any additional materials, such as solder or adhesive, reducing the overall cost of the process while also minimizing waste. However, it is important to note that cold welding does have some limitations and may not be suitable for all applications, such as high-stress environments or those requiring a strong bond between the metals. Overall, the advantages of cold welding make it a valuable option for many applications, but it is important to carefully consider the specific requirements of the project before choosing this method.
Disadvantages
When it comes to cold welding, there are definitely pros and cons to consider. One major advantage is that it allows for the joining of dissimilar metals, which is not always possible with other welding methods. Additionally, cold welding does not require the use of heat, which can be beneficial in situations where high temperatures could cause damage or distortion.
However, there are also some disadvantages to consider. For example, the process can be quite slow, which can make it impractical for some applications. Additionally, it may not be as strong as other welding methods, which could limit its usefulness in certain situations.
Overall, while cold welding can have its benefits, it is important to carefully consider its limitations before deciding whether or not to use it for a particular project.
Conclusion
In the world of metal fabrication, cold welding machines are like magic wands, capable of bonding metal pieces without the need for heat or electricity. How do they work, you ask? Well, imagine two pieces of metal being placed in a vacuum chamber where they are pressed together with incredible force. This force causes the atoms on the surfaces of the metal pieces to intermingle, creating a molecular bond that is stronger than any mechanical fastening method.
The result? A flawless, seamless joint that is virtually invisible and highly durable. Cold welding machines – making metal bonding look easy since forever!”
FAQs
What is a cold welding machine?
A cold welding machine is a device used to bond two pieces of metal together without using heat.
How does a cold welding machine work?
A cold welding machine uses high pressure to create a bond between two pieces of metal without adding heat. It works by compressing the metal at a molecular level, creating a permanent bond.
What types of metals can be bonded with a cold welding machine?
A cold welding machine can bond a wide variety of metals, including aluminum, copper, and steel.
What are the advantages of using a cold welding machine over traditional welding methods?
The advantages of using a cold welding machine include no heat affected zone, a stronger bond, and a faster bonding process.
Is cold welding a reliable method for bonding metals?
Yes, cold welding is a reliable method for bonding metals and is commonly used in the aerospace and automotive industries.
Can cold welding be used to repair damaged metal parts?
Yes, cold welding can be used to repair damaged metal parts, including cracks and breaks.
Is it difficult to operate a cold welding machine?
No, it is not difficult to operate a cold welding machine. It requires basic training and practice to master the technique.