How Cordless Drills Are Made: A Comprehensive Guide to the Manufacturing Process
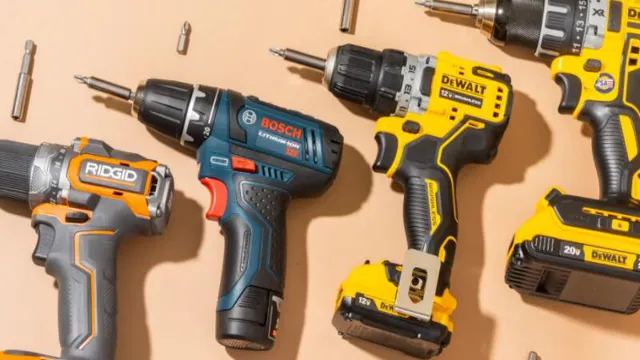
Cordless drills have become a go-to item for many DIY enthusiasts and professionals, making life easier when it comes to DIY tasks. But have you ever wondered how cordless drills are made? It’s a fascinating process that involves cutting-edge technology and skilled craftsmanship. From the creation of the motor to the final assembly, each step in the process is critical in ensuring the drill operates at maximum efficiency and reliability.
Imagine the cordless drill as a puzzle, with its various components fitting together perfectly to create a powerful and versatile tool. From the ergonomic grip to the interchangeable batteries, each part plays a crucial role in the drill’s functionality. And with the growing demand for cordless drills in the market, manufacturers are constantly innovating, using new materials and design techniques to create more powerful and longer-lasting tools.
But what’s the driving force behind the construction of cordless drills? To put it simply, it’s about tapping into the potential of the latest technology to create a tool that can efficiently and effectively accomplish designated tasks. This approach also ensures that the tool can withstand wear and tear, as well as challenging working conditions. Overall, the process of making a cordless drill is a complex one that draws from creativity, innovation, and a focus on delivering high-quality products that meet the needs of various users.
Introduction
Cordless drills have revolutionized the world of power tools, and their production is a fascinating process. How cordless drills are made involves several distinct parts and highly specialized manufacturing techniques. The process begins with the creation of the drill motor and battery assembly, which consists of interlocking parts and specialized wiring.
Once the primary components are assembled, the exterior of the drill is designed and created using high-precision milling and casting techniques. Finally, the components are assembled and tested to ensure quality control and safety. The entire process requires a team of highly skilled engineers, designers, and machinists to work collaboratively to create a precision tool that is both reliable and high-performing.
Despite the complexity of their manufacturing process, cordless drills are essential tools for both professionals and DIY enthusiasts alike, providing quick and easy access to reliable power in a compact and portable design. So, next time you pick up a cordless drill to complete a project, remember the intricate and precise manufacturing process that went into its creation.
What is a cordless drill?
A cordless drill is a portable hand-held tool that allows you to drill holes or drive screws without the need for an electrical outlet. This versatile and handy tool has become a staple in every DIY enthusiast’s toolkit. Unlike traditional drills that have cords tethering them to electrical outlets, cordless drills operate using rechargeable batteries.
The battery pack that powers the drill has a limited charge, but the latest models have longer battery life and faster charging times. Cordless drills vary in size, power, and features, making them suitable for a range of applications, from light DIY drilling to heavy-duty construction work. Investing in a cordless drill is a wise choice for anyone who enjoys DIY projects or works in the construction industry, as it is both convenient and efficient.
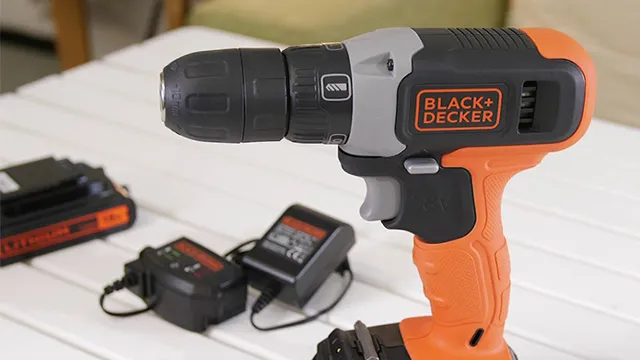
Why are cordless drills popular?
Cordless drills have become quite the popular tool among DIYers and professionals alike for a variety of reasons. Perhaps the most significant factor contributing to their popularity is their convenience. Unlike their corded counterparts, cordless drills allow users to move around freely without worrying about getting tangled in wires, making them ideal for both indoor and outdoor projects.
Additionally, advances in battery technology have made cordless drills more powerful and longer-lasting than ever before, eliminating the need for frequent charging and making them a reliable option for even the most demanding tasks. These factors, along with their relatively affordable price point, have made cordless drills a go-to tool for many individuals in need of a reliable and versatile power tool.
Design and Materials
Have you ever wondered how cordless drills are made? Well, it takes more than just a few parts put together. The design and materials used are essential in creating a reliable and long-lasting power tool. The outer shell is usually made of high-quality plastic or metal, ensuring durability and reducing the weight of the drill.
The chuck, which holds the drill bits in place, is typically made of hardened steel or carbide for optimum grip and to prevent wearing. The motor, on the other hand, is the heart of the drill, and the materials used to make it plays a vital role in determining the power rating. Most cordless drills are powered by lithium-ion batteries, which are lighter and provide more power, making them ideal for heavy-duty tasks.
These drills also have electronic control systems that regulate the power supply, allowing the battery to last longer and prevent overheating. In summary, cordless drills are made up of carefully selected materials and designed to cater to the various needs of the user. From the outer shell to the internal components, each part plays a significant role in determining the quality, reliability, and performance of the drill.
Key components of a cordless drill
When it comes to cordless drills, the design and materials used are key components that heavily impact the tool’s functionality and efficiency. The design of a cordless drill typically includes a hand-held drill body, which contains the motor and battery pack, and a removable chuck that holds the drill bit. The materials used in the drill body and chuck can vary, but most manufacturers typically use durable plastics and high-quality metals such as steel and aluminum.
These materials provide the necessary strength and rigidity to handle a variety of drilling tasks. Additionally, the ergonomics of the drill body design play a significant role in the tool’s ease of use and comfort level during extended use. A well-designed cordless drill should have a balanced weight distribution and a comfortable grip to minimize user fatigue and strain.
You May Also Love:
Proper design and material selection are crucial to ensure the overall performance and longevity of a cordless drill.
Materials used in cordless drill manufacturing
When it comes to cordless drill manufacturing, the design and materials used play a crucial role in determining the quality of the product. The materials used in cordless drill manufacturing are carefully selected to ensure durability, strength, and reliability. The most common materials used in making the body of the drill are metal and plastic.
Metal is used for the chuck which holds the bits in place, as well as for the gears and motor housing. Meanwhile, the plastic is used for the outer casing which gives the drill its shape and protects the inner components. Additionally, lithium-ion batteries are the most commonly used power source in cordless drills due to their high energy density and long lifespan.
The design of the drill is also important, with ergonomics being a top priority to ensure comfortable use and reduce operator fatigue. Overall, the materials used in cordless drill manufacturing are chosen for their strength, durability, and functionality to provide users with a reliable and efficient tool.
Assembly Process
Have you ever wondered how cordless drills are made? The assembly process for these handy power tools involves several steps. It starts with creating a design for the drill, ensuring that it meets all necessary safety and functionality requirements. Then, the individual components of the drill, such as the motor and battery, are manufactured and tested to ensure they meet the specifications outlined in the design.
Once these components are made, they are assembled together using specialized tools and machinery. This process is precise and requires a skilled technician to ensure each part is attached correctly and functioning properly. After the drill is assembled, it undergoes a rigorous testing process to ensure it meets quality standards and is safe to use.
Only after passing these tests is the drill packaged and shipped to the customer. Overall, the assembly process of cordless drills is complex and requires careful attention to detail, but the end result is a high-quality, versatile power tool that can be used for a variety of tasks around the home or job site.
Step by step assembly process
Assembling a product can be a daunting task, but by following a step-by-step process, it can be made a lot easier. To start, make sure you have all the necessary parts and tools needed for the assembly. Begin by reading the instruction manual, familiarizing yourself with the product and its components.
Lay out all the parts in an organized manner to help you keep track of pieces as you go. Next, start putting together the base or frame of the product first. Ensure that the screws and bolts are tightened enough but not too tight to avoid damages.
Once the base is put together, continue adding the other parts according to the instructions provided. Throughout the assembly process, make sure each piece fits securely and is placed in the correct spot. Finally, check that all components are properly fixed and tightened to guarantee the product’s stability before testing.
By following this step-by-step process, you can quickly and easily assemble your product without any difficulty.
Quality control checks
In any manufacturing process, quality control checks are essential to ensure that the final product is defect-free and meets the required standards. This is especially crucial in the assembly process, where multiple components come together to form the final product. The quality control checks in the assembly process involve inspecting each component before assembly, ensuring that the assembly process is done correctly, and testing the final product for defects.
By doing so, manufacturers can identify and fix any issues that may arise early on in the process, saving time and resources in the long run. Proper quality control checks can also help ensure customer satisfaction by guaranteeing that each product meets the required specifications, and is safe and functional. It’s essential to implement thorough quality control checks throughout the assembly process to minimize errors and defects and produce high-quality products.
Testing and Certification
If you’ve ever wondered how cordless drills are made, it’s an interesting process with several steps involved. The production of cordless drills typically begins with the design and development of the drill. The drill is then tested to ensure that it meets safety standards, performance requirements, and other necessary criteria.
Once the designs are finalized, the drill is manufactured using various materials and components, including the motor, gears, chuck, and battery. Assembly of the drill is also an important part of the process, ensuring that all components are properly put together. Before the drill is sold, it must go through a certification process to ensure that it meets all relevant safety standards and regulations.
Overall, the production of cordless drills is an intricate process that involves a combination of design, testing, manufacturing, and certification.
Types of tests performed on cordless drills
When it comes to cordless drills, there are various types of tests that are performed to ensure their quality and reliability. One important aspect is testing and certification. Before a cordless drill hits the market, it needs to undergo rigorous testing to meet safety standards.
It is essential to make sure that the drill will not only perform well but also safe to use. The certification process includes tests like overload testing, electrical safety testing and EMF (electromagnetic field) testing. These tests are necessary to ensure that the drill is up to standard and can be safely used by consumers.
It is crucial to look for cordless drills that have been certified by reputable organizations to ensure safety and reliability. Make sure to check for certification marks like ETL, CSA, FCC, and UL. By conducting these tests, manufacturers can address any potential issues to ensure the quality of the product.
Certifications and safety regulations
When it comes to manufacturing products, it is important to ensure that they meet all necessary safety regulations. This is where testing and certification comes in. Before a product can be sold, it must undergo rigorous testing by a certification body to ensure that it meets safety standards.
This can include things like electrical safety, fire safety, and chemical safety. By obtaining certifications and complying with safety regulations, manufacturers can not only protect their customers but also their business. Not only can non-compliance lead to legal issues and fines, but it can also damage a company’s reputation.
It’s important to keep in mind that obtaining certifications is not a one-time thing. Manufacturers must continue to meet safety standards and regularly renew their certifications to ensure ongoing compliance. Ultimately, the investment in testing and certification is well worth it to ensure the safety and success of a product and its manufacturer.
Conclusion
In conclusion, cordless drills are a marvel of modern engineering, with every component finely tuned and precisely crafted. From the motor and battery to the chuck and clutch, each element comes together to form a powerful tool capable of tackling any DIY project. It’s amazing to think that something as seemingly simple as a drill involves so many complex processes and technologies.
And yet, thanks to the skill and dedication of designers and engineers around the world, we can all enjoy the convenience and versatility of these wireless wonders. So next time you pick up a cordless drill, take a moment to appreciate the ingenuity and craftsmanship that went into its creation – and use it to make something awesome!”
Future of cordless drill manufacturing
As the demand for cordless drills increases, manufacturers are under pressure to ensure the safety and reliability of their products. To address this concern, testing and certification are crucial stages in the manufacturing process. These tests involve rigorous trials to ascertain that each drill meets safety standards and is capable of handling various jobs.
The certification process ensures a product is safe according to standards set by regulatory bodies, increasing confidence in the product. Testing and certification are costly, but they demonstrate a manufacturer’s commitment to quality and safety standards. Manufacturers need to continually evaluate their products through testing and certification to maintain their competitive advantage and retain customer trust.
By using certified products, consumers will be assured of the product’s quality and safety, which will increase brand loyalty. Consequently, the future of cordless drill manufacturing is dependent on the thoroughness of their testing and certification processes.
FAQs
What are the main components of a cordless drill?
A typical cordless drill consists of a motor, battery, gearbox, chuck, and a trigger or switch.
What types of batteries are used in cordless drills?
Cordless drills typically use lithium-ion batteries as they are rechargeable and offer longer run times compared to other types of batteries.
How are the motors for cordless drills made?
The motors for cordless drills are manufactured using various materials such as copper wire, steel laminations, and magnets, which are then assembled together to form the motor.
Can cordless drills work continuously without overheating?
Cordless drills have built-in thermal protection that prevent overheating and extend the life of the tool. However, continuous use without break can cause the tool to get hot and reduce its performance.
How do cordless drills achieve variable speed control?
Cordless drills achieve variable speed control by using a trigger or switch that controls the power output to the motor, allowing the user to adjust the drilling speed.
How strong is the grip of the chuck in cordless drills?
The chuck in cordless drills has a strong grip that ranges from 1/4 inch to 1/2 inch, depending on the model.
How long do cordless drill batteries last?
The battery life of a cordless drill varies based on factors such as usage, battery capacity, and age of the battery. On average, cordless drill batteries last between 1 to 3 years depending on the usage.