How Does a Screw Air Compressor Work? A Comprehensive Guide to Its Mechanism
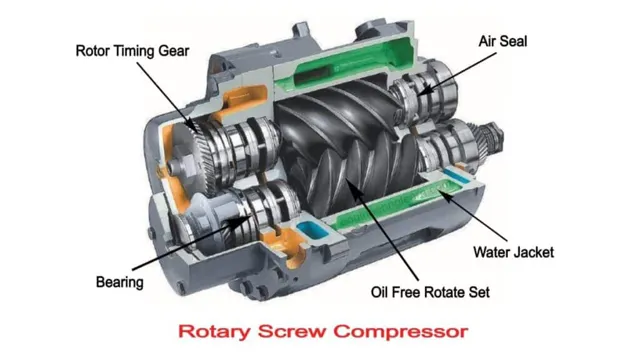
If you’ve ever wondered how a screw air compressor works, you’re in the right place. These machines play a vital role in powering a variety of tools and machinery across countless industries. They work by compressing air inside a chamber to increase its pressure and deliver it to where it’s needed.
But how exactly do they do it? In this blog, we’ll break down the components and mechanics behind screw air compressors to give you a better understanding of how they work. So buckle up, and let’s dive in!
Introduction
Have you ever wondered how does a screw air compressor work? Screw air compressors are popular in industrial settings because they are reliable, efficient, and capable of producing large amounts of compressed air. The mechanism behind the screw air compressor is fairly simple. It works by using two rotating screws or rotors, which compress the air and force it through a chamber where it is released at a higher pressure.
The screws are known as the male and female rotors, and they work in tandem to trap and push air through the system. These rotors are precisely manufactured to fit together perfectly to create a tight seal, which is critical for the compressor to work effectively. This compression process generates heat which will automatically release through the cooling system present in the air-compressor.
As the compressor runs continuously, air is drawn in and compressed to high pressures, which can be used for various industrial applications. Overall, the screw air compressor is a highly efficient piece of equipment, and it plays an essential role in many industries, including manufacturing and construction.
Basic Function of a Screw Air Compressor
A screw air compressor is a device that compresses air using two helical screws, which rotate against each other. It is widely used in industrial and commercial applications for its efficiency, reliability, and versatility. The basic function of a screw air compressor is to take in air, compress it, and then release it under high pressure.
This compressed air is used in various operations, such as powering tools and machinery, controlling pneumatic systems, and generating energy for different processes. The principle of screw air compressors is quite simple yet effective. When the two screws rotate together, they create a tight seal, which forces air into a smaller and smaller space.
The compressed air is then released, ready to be used for various purposes. Overall, screw air compressors are an essential tool for many different industries and play a crucial role in making our lives easier.

Types of Screw Air Compressors
Screw air compressors are essential machines used to convert mechanical energy into kinetic energy by compressing air. There are different types of screw air compressors, including oil-free and oil-injected compressors. Oil-free compressors are ideal for environments that cannot tolerate oil contamination, such as laboratories, food processing plants, and hospitals.
On the other hand, oil-injected compressors can handle higher capacity and are commonly used for industrial and manufacturing applications. Another classification of screw air compressors is based on the number of rotors, with two and three rotors used respectively for twin-rotor and triple-rotor models. The design and usage of screw air compressors are dependent on the intended application and the ideal type of screw air compressor necessary for optimal performance.
Components of a Screw Air Compressor
If you’ve ever wondered how a screw air compressor works, here’s a breakdown of its components. At its most basic, a screw air compressor is a positive displacement machine that compresses air through two interlocking screws. The screws have a special profile that allows them to trap air between them and transport it towards the outlet.
The compressor’s main components include the screws, inlet and outlet valve, bearings, and a motor. The inlet valve allows ambient air to enter the compressor, while the outlet valve releases compressed air. The screws rotate thanks to a motor, while the bearings ensure limited friction between the screws and the compressor casing.
Once air enters the compressor through the inlet valve, it’s squeezed by screw rotation until it reaches its maximum pressure and volume. Finally, the outlet valve opens to release compressed air, and the cycle begins anew. With its simple but effective design, a screw air compressor can generate continuous, high-precision compressed air, making it an ideal choice for many industrial applications.
Screw Rotors and Casing
A screw air compressor consists of various components, and among them, screw rotors and casing are perhaps the most essential. The screw rotors work together to compress and discharge air while the casing provides a secure environment for this process. The rotors are designed in such a way that they fit together perfectly while rotating in opposite directions.
This movement results in air being pushed from the inlet to the outlet while being compressed. The casing, on the other hand, holds the rotors in place and allows the machine to work efficiently. Think of the rotor and casing as a lock and a key – one doesn’t work without the other.
A good-quality casing helps prevent any leaks or irregularities, ensuring that the screw rotor can do its job properly. Choosing a high-grade screw compressor with suitable rotors and casing can make a significant difference in the compressed air output and operational efficiency of your business.
Air Intake Filters
When it comes to understanding the components of a screw air compressor, one crucial element that often goes overlooked is the air intake filter. This small yet mighty piece of equipment plays an essential role in ensuring the efficiency and longevity of the compressor by preventing dirt, debris, and other contaminants from entering the system. Without a properly functioning air intake filter, the compressor may experience decreased performance, increased energy consumption, and even damage.
It’s important to regularly check and replace the air intake filter, as neglecting this simple task can have costly consequences down the line. Think of the air intake filter as the immune system of your screw air compressor, working diligently behind the scenes to keep everything running smoothly and efficiently.
Inlet and Outlet Valves
When it comes to screw air compressors, there are a variety of components that work together to ensure proper operation and maximum efficiency. Among these components are the inlet and outlet valves. These valves play a critical role in the compression process, allowing air to enter the compressor through the inlet valve and exit through the outlet valve.
The inlet valve opens to allow air to be drawn into the compressor chamber, where it is compressed by the rotating screws. Once the air has been compressed, it is then expelled through the outlet valve and into the air receiver. These valves are often made from durable materials such as steel or brass, and are designed to withstand the high pressures and temperatures encountered during the compression process.
Without properly functioning inlet and outlet valves, a screw air compressor may experience reduced efficiency, increased wear and tear, and even premature failure. So, it is important to ensure that these critical components are regularly inspected and maintained to ensure optimal performance.
Oil Separator
An essential component of a screw air compressor is the oil separator. As the name suggests, it is responsible for separating oil from the compressed air before it leaves the compressor. The oil separator comprises of several layers of fine mesh fibers that trap the oil and allow only the clean air to pass through.
In addition to improving the quality of the compressed air, the oil separator also helps in extending the lifespan of the compressor. Without a functioning oil separator, the oil would accumulate in the compressed air pipes, leading to clogs and decreased efficiency. It’s important to regularly maintain and replace the oil separator to ensure optimal performance of the air compressor.
Think of the oil separator as a filter for your drink- you wouldn’t want to drink particles of dirt or debris, and similarly, you wouldn’t want to use compressed air with oil particles. Therefore, investing in a good oil separator is vital for any air compressor system.
Air Receiver Tank
An essential component of a screw air compressor is the air receiver tank. This tank acts as a storage unit for the compressed air produced by the compressor. It is crucial in ensuring a steady flow of compressed air to downstream equipment and tools.
The air receiver tank helps to cool the compressed air, which reduces moisture build-up and allows for more efficient operation of the compressor. It also acts as a buffer, reducing the amount of surge or pressure fluctuation that may occur when the demand for compressed air varies. The size of the air receiver tank varies depending on the requirements of the system.
A larger tank typically means more storage capacity and can provide a more stable flow of compressed air, while a smaller tank may be more suitable for systems that require frequent start-stop cycles. Proper maintenance and inspection of the air receiver tank are essential for the safe and efficient operation of a screw air compressor system.
Working of a Screw Air Compressor
If you’re wondering how a screw air compressor works, then you’ve come to the right place. A screw air compressor operates by using a pair of meshing rotors in a casing to compress and transfer air. The male and female rotors work together to create a tight seal as they rotate, which traps air as it moves along the length of the rotors.
As the air moves towards the smaller end of the compressor, the volume between the rotors decreases, leading to an increase in pressure. The compressed air then exits the compressor and travels through a discharge valve. One of the primary benefits of a screw air compressor is its ability to provide a continuous flow of air, making it ideal for industrial applications.
Additionally, they operate quietly and are easy to maintain. So, if you’re in the market for a powerful and efficient air compressor, then consider investing in a screw air compressor.
Compression Process
A screw air compressor utilizes a compression process, which involves reducing the volume of a gas by increasing the pressure. This process is achieved by a rotating screw that compresses the air or gas as it moves through the machine. The screw compressor consists of two interlocking rotors that trap the gas and compress it as the rotors turn, like gears in a machine.
The gas is then forced out through the discharge port, where it can be used for a variety of applications. The screw air compressor is a highly efficient machine, as it can operate continuously and provides a steady flow of compressed air or gas. The compression process of a screw air compressor is an essential part of its operation, as it allows the machine to produce compressed air or gas on demand, providing a reliable source of power for a variety of applications.
Whether for industrial or personal use, a reliable screw air compressor is a valuable investment, providing years of dependable service.
Oil and Air Separation
When it comes to air compressors, one of the essential components is the oil and air separator. This device is responsible for separating oil from compressed air, ensuring that the air output is clean and free from contaminants. The oil and air separator works by utilizing a filter element made from a specialized material that attracts oil particles and traps them.
As the compressed air flows through the filter element, the oil is gradually removed, resulting in cleaner air. Screw air compressors are one of the most common types of compressors that rely on oil and air separation. These compressors feature two interlocking screws that produce compressed air as they rotate.
Typically, these compressors require lubrication to keep the screws rotating smoothly, which is where the oil and air separator comes in. The separator helps remove any oil particles from the compressed air, ensuring that the air output is clean and dry. In summary, the oil and air separator is a vital component of screw air compressors, and it plays a crucial role in keeping the compressed air clean and free from contaminants.
Without this device, the compressed air would be of low quality and may damage pneumatic tools or other equipment that relies on compressed air. So, if you are working with a screw air compressor, ensure that the oil and air separator is functioning correctly to maximize its performance and longevity.
Delivery of Compressed Air
Delivery of Compressed Air When it comes to understanding the working of a screw air compressor, it’s important to first understand the delivery of compressed air. A screw air compressor works by drawing in air through an inlet valve and compressing it with the help of rotating screws. This compressed air is then discharged through an outlet valve, which delivers a steady flow of compressed air at high pressure.
The delivery of compressed air is crucial for many industrial processes, including powering pneumatic tools, operating heavy machinery, and providing air for spray painting. In order to ensure reliable delivery of compressed air, it’s important to regularly maintain and service your screw air compressor. This may include performing routine checks for leaks and wear and tear, as well as replacing worn components as needed.
By understanding the delivery of compressed air and ensuring the proper maintenance of your screw air compressor, you can ensure that your industrial processes are able to run smoothly and efficiently.
Advantages and Disadvantages of Screw Air Compressors
Are you curious about how screw air compressors work? These machines use two interlocking screws, or rotors, to compress air. As the rotors turn, they reduce the volume of the air trapped inside, increasing its pressure. Screw air compressors are widely used in various applications, from powering pneumatic tools to supplying air to industrial processes.
One of the biggest advantages of screw air compressors is their efficiency. They can produce large amounts of compressed air quickly and continuously, making them ideal for high-demand environments. They also require less maintenance than other types of compressors, reducing downtime and operating costs.
On the downside, screw air compressors can be quite expensive to install and operate. They also generate a lot of heat during operation, which can be a safety hazard and require additional cooling systems. Overall, screw air compressors are a powerful and reliable solution for many industrial needs, but it’s important to consider both their benefits and drawbacks before investing in one.
Advantages
Screw air compressors are widely popular in different industrial settings for their numerous advantages. One significant advantage of using screw air compressors is their high efficiency rate, which results in lower energy costs. They are also durable, reliable and require less maintenance than conventional reciprocating compressors.
Screw air compressors can handle a wide range of air demands, making them suitable for different applications. Furthermore, these compressors are compact, making them ideal for locations with limited space. They are also user-friendly, and operators can easily control their performance using digital controls and display panels.
On the downside, screw air compressors can be noisy, and their installation and maintenance cost can be higher than other types of compressors. However, despite these disadvantages, many industries still prefer using screw air compressors due to the significant energy savings and overall efficiency they provide.
Disadvantages
Screw air compressors have several advantages that make them a popular choice for industrial operations. However, they also come with some disadvantages that should be considered. One of the main downsides of screw air compressors is their initial cost, which tends to be higher than other types of compressors.
Additionally, screw compressors require regular maintenance to ensure optimal performance, which can be time-consuming and costly. Another disadvantage is their high noise levels, which can be a concern for workers, especially in small or enclosed spaces. Despite these drawbacks, screw air compressors are highly efficient and reliable, making them a worthwhile investment for businesses looking to increase productivity while minimizing downtime and energy costs.
Conclusion
In conclusion, a screw air compressor works by using the power of two interlocking rotors to compress and deliver air at high pressure. It’s like a dynamic duo of mechanical genius, with one rotor playing the role of Batman, creating suction and pulling in the air, while the other rotor is the Robin to his Batman, squeezing and compressing the air until it’s pressurized and ready to go. It’s a match made in mechanical heaven, and the result is a highly-efficient and effective way to power everything from heavy-duty machinery to everyday tools.
So the next time you hear the sound of a screw air compressor in action, take a moment to appreciate the clever engineering behind it all – it’s like a silent superhero, working hard to keep the world moving forward one screw at a time.”
FAQs
What is a screw air compressor?
A screw air compressor is a type of compressor that uses a rotary screw element to compress air.
How does a screw air compressor work?
A screw air compressor works by using two rotating screws to compress air. As the screws turn, air is drawn in and compressed.
What are the advantages of using a screw air compressor?
The advantages of using a screw air compressor include high efficiency, low maintenance requirements, and quiet operation.
What applications are best suited for screw air compressors?
Screw air compressors are ideal for applications that require a continuous supply of compressed air, such as industrial manufacturing and processing.
How do you choose the right size screw air compressor for your needs?
The right size screw air compressor depends on factors such as the required air flow rate, the operating pressure, and the duty cycle. Consult with a compressor supplier to determine the appropriate size for your needs.
What maintenance is required for a screw air compressor?
Screw air compressors require regular maintenance, such as oil changes and filter replacements, to ensure proper operation and prevent breakdowns.
How do you troubleshoot a problem with a screw air compressor?
Troubleshooting a problem with a screw air compressor involves identifying the symptoms, such as low pressure or unusual noise, and then checking various components, such as the filters or oil level, for issues. Consult with a compressor technician if further assistance is needed.