Have you ever wondered how the arm gears of your drill press work? Well, fear not, because in this blog post, we’re going to dive into the inner workings of this powerful tool. Drill press arm gears are responsible for powering the arm that holds the drill bit in place, allowing for precision drilling in a wide range of materials. But how does this mechanism actually work? Think of it like a set of interlocking gears, each with their own teeth that fit together perfectly to turn the drill bit.
These gears are powered by the motor within the drill press, which rotates them at various speeds depending on the user’s needs. At its core, the drill press arm gear system is a marvel of engineering. It allows for precise and consistent drilling, making it an essential tool for any professional or DIY enthusiast.
But there’s more to these gears than just power and precision. They also play a crucial role in protecting the user and the drill itself from damage. The gears are designed to slip or stall if the bit encounters too much resistance, preventing the motor from burning out or the bit from breaking off.
So, the next time you fire up your drill press, take a moment to appreciate the mechanics at work. From the interlocking gears to the protective mechanisms in place, this tool is truly a masterpiece of modern engineering. And now, armed with a better understanding of how it all works, you can feel even more confident in your ability to use it effectively and safely.
Overview of Drill Press Arm Gears
If you’re wondering how drill press arm gears work, it’s simpler than you might think. Arm gears are responsible for moving the drill press spindle up and down, and they do so by converting the rotational motion of the drill press crank into vertical motion. The gears are housed in the arm of the drill press, and they are connected to the spindle via a series of cogs or pulleys.
When you turn the crank, the arm gears engage and start to rotate, which moves the spindle up or down depending on how you adjust it. The gear ratio of the arm gears determines how fast or slow the spindle will move, and generally, the higher the gear ratio, the faster the spindle will rotate. Understanding how drill press arm gears work is essential if you want to get the most out of your machine, so be sure to familiarize yourself with this important component.
What are Drill Press Arm Gears?
Drill Press Arm Gears Drill press arm gears are an essential component of a drill press machine. The arm gears assist in controlling the vertical movement of the drill press arm, which is typically used to lower or raise the drill bit. The gears use a system of interlocking cogs to transmit motion from the drill press motor to the arm.
When the user lowers the arm, the gears are engaged, and the motor’s torque is transferred to the drill bit. Similarly, when the arm is raised, an opposite movement occurs, which disengages the gears and stops the drill bit. These gears come in various sizes and materials, depending on the drill press machine’s size and intended use.
It is crucial to keep these gears well lubricated and maintained to ensure optimal performance and prevent wear and tear. Drill press arm gears are a critical part of any drill press machine and ensure precise and efficient drilling for most applications.
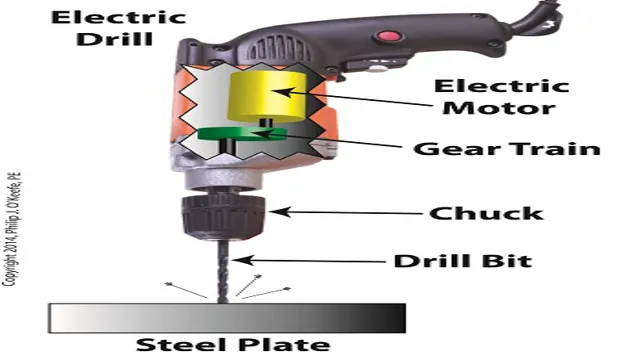
How Do They Work?
If you’ve ever used a drill press, you may have noticed the arm that moves up and down as you drill. This arm is typically controlled by gears, which work together to smoothly and efficiently move the arm. The gears are responsible for transferring the power from the motor to the arm so that it can move up and down.
The arm gears are also responsible for controlling the speed and direction of the arm’s movement. This is important because it allows you to drill holes precisely and accurately. When you turn on the drill press, the motor’s power is transferred through the gears and into the arm, which then moves up and down as you engage the drill bit.
The arm gears are an essential part of the drill press and ensure that you have the precision and control necessary for any drilling job.
Types of Drill Press Arm Gears
If you’ve ever wondered how drill press arm gears work, then you’re in the right place. There are actually several types of drill press arm gears that work differently depending on the specific model. The most common type of arm gear is the ring and pinion, which uses a ring gear attached to the drill press spindle and a pinion gear attached to the arm.
As the arm is raised or lowered, the pinion rotates the ring gear to move the spindle up or down. Another type of arm gear is the rack and pinion, which uses a vertical rack attached to the arm and a pinion gear that slides up and down the rack to move the spindle. Worm gears are also used in some drill presses, and they work by using a rotating worm gear to turn a larger spur gear that moves the arm up or down.
Understanding the different types of drill press arm gears can help you choose the best one for your specific needs.
Single Gear Arm System
When it comes to drill press arm gears, the single gear system is a popular choice. This type of gear system consists of a single gear that controls the movement of the drill press arm. One of the advantages of a single gear system is that it is simple and straightforward, making it easy to use for beginners.
However, it does have its limitations, as it may not be able to handle larger jobs or tougher materials. There are different variations of the single gear system, including those with variable speed control or adjustable tension. It’s important to consider your specific needs and the materials you will be working with when choosing a drill press arm gear system.
Whether you opt for a single gear system or a more complex alternative, having the right gear system can make all the difference in the success of your drilling projects.
Double Gear Arm System
The Double Gear Arm System is an innovative addition to the drill press machines. It allows you to select between two gears, one for high speed and the other for more torque. This is a significant advantage as it allows you to work on different materials with varying hardness levels.
There are essentially two types of Drill Arm Gears in a Double Gear Arm System – the Primary Gear and the Secondary Gear. The primary gear is generally the larger of the two and has more teeth. It is designed for efficiency and high-speed operation for lighter materials.
The secondary gear, on the other hand, is smaller and has fewer teeth, providing more torque for heavy-duty drilling operations. Both gears work in sync to provide the maximum output in the easiest way possible, and they can be switched quickly depending on the type of project you are working on. The Double Gear Arm System ensures that you can have complete control over your drill press, making it a versatile tool that can be used for different purposes.
In conclusion, the Double Gear Arm System is a revolutionary addition to the drill press machine, allowing users to switch between two gears for different drilling tasks. The different types of Drill Arm Gears, such as the Primary Gear and Secondary Gear, offer varying advantages depending on the type of work at hand. This innovative system provides a level of versatility and control that is unique to the drill press machine.
Triple Gear Arm System
If you’re in the market for a drill press, you might be wondering about the different types of arm gears available. One popular option is the triple gear arm system. As the name suggests, this system consists of three gears that help to increase or decrease the speed of the drill bit.
The triple gear system offers a range of speed options, which can be helpful when working with different materials. Depending on your needs, you might prefer a slower speed for delicate work or a faster speed for heavy-duty drilling. With the triple gear arm system, you can easily adjust the speed to suit your needs.
One thing to keep in mind is that this system can be more complicated to operate than other types of arm gears, so be sure to read the manual carefully before getting started. Overall, the triple gear arm system is a reliable option that can help you get the most out of your drill press.
Advantages of Drill Press Arm Gears
Drill press arm gears are an essential component in the functionality of a drill press. By controlling the movement of the arm of the drill press, gears ensure precision and accuracy when drilling holes. The gears have teeth that fit together, making them an effective way to transfer power from the motor to the drill bits.
With the help of the gears, the arm of the drill press can be adjusted to the correct height, angle, and depth, making it perfect for repetitive tasks and ensuring uniformity in results. These gears also allow for a much smoother operation, reducing the amount of wear and tear on the drill press machine. Due to their effectiveness, drill press arm gears are highly favoured within the woodworking and metalworking communities.
In conclusion, knowing how drill press arm gears work is essential for anyone who wants to use a drill press correctly and efficiently.
Efficient Power Transmission
Efficient Power Transmission/ Drill Press Arm Gears When it comes to power transmission in drilling, efficiency and accuracy are key factors. That’s where drill press arm gears come in handy. These gears provide a smooth and precise transmission of power from the motor to the drilling spindle.
One of the key advantages of drill press arm gears is that they can transfer power efficiently over long distances without any loss of power. This means that the drill can work at its full capacity, producing consistent results every time. Another significant benefit of drill press arm gears is that they help to reduce the wear and tear of the drill.
Since the gears can transfer power smoothly and precisely, the drill’s motor doesn’t have to work as hard, resulting in less stress on the components. This means that the drill will last longer, saving you money in maintenance and repair costs. Additionally, drill press arm gears allow for easy speed and depth adjustments, increasing the drill’s versatility and making it suitable for a wide range of applications.
In conclusion, drill press arm gears are an essential component in getting accurate and efficient power transmission in drilling. They provide a smooth and precise means of transmitting power to the spindle, reducing wear and tear on the motor, allowing easy speed and depth adjustments, and maintaining consistent results. Investing in a drill press with arm gears is a wise decision for those who want to maximize their drilling capabilities while reducing maintenance and repair costs in the long run.
Ease of Use and Versatility
Drill Press Arm Gears. Drilling can be a challenging task, but with the right equipment, it can become a breeze. One such piece of equipment that can make drilling more manageable and versatile is the drill press arm gears.
The main advantage of using a drill press arm gear is the ease of use it provides. The gears allow users to adjust the drill arm to the desired height and tilt, making it easier to drill at any angle or location. Additionally, the arm gears provide versatility to the drill press machine by enabling it to handle various drilling tasks, including drilling larger holes and tapping.
With the gears, users can set the drilling depth and maintain it consistently, ensuring accurate and precise results every time. When using the drill press arm gears, drilling tasks become more comfortable, quicker, and more convenient, making it a must-have piece of equipment for every drill press.
Maintenance Tips for Drill Press Arm Gears
Drill presses are a powerful tool for boring holes in a variety of materials, from wood to metal. The key to their effectiveness lies in the drill press arm gears, which rotate the drill bit at high speeds to effortlessly cut through even the toughest surfaces. To keep your drill press running smoothly, it’s important to regularly maintain these gears.
Start by wiping them down with a clean, dry cloth to remove any debris or dust that may have accumulated. Next, apply a small amount of lubricant to the gears to reduce friction and ensure a smooth operation. Finally, be sure to inspect the gears for any signs of wear or damage, and make any necessary repairs or replacements before using the drill press again.
With these simple maintenance tips, you can ensure that your drill press arm gears continue to work effectively and efficiently for years to come.
Conclusion
After diving into the inner workings of drill press arm gears, it’s clear that these mechanical marvels are the unsung heroes of every workshop. Using a combination of precision engineering, tooth meshing, and good ole elbow grease, these gears are able to turn even the most mundane of drills into a swiss army knife of drilling precision. So the next time you reach for your trusty drill press, take a moment to appreciate the gears that make it all possible – they may not be flashy, but they sure get the job done.
“
FAQs
What is a drill press arm and how does it work?
A drill press arm is the part of the drill press that supports and guides the drilling process. It is responsible for controlling the movement of the drill bit. The arm is connected to the gears which power the drill bit’s rotation and control its speed.
How do the gears in a drill press arm work?
The gears in a drill press arm work by controlling the speed and rotation of the drill bit. When the drill press is running, the motor turns the large gear which then moves the smaller gear. The smaller gear is connected to the drill bit, and as it rotates, it powers the drill bit.
What are the different types of gears used in drill press arms?
Typically, drill press arms use spur gears, bevel gears, or worm gears. Spur gears are the simplest, with straight teeth that run parallel to the drill shaft. Bevel gears are angled gears that allow the drill press to pivot. Worm gears are used for precise movements, but they are slower and less efficient.
How do you maintain the gears in a drill press arm?
To maintain the gears in a drill press arm, it’s important to keep them clean and lubricated. This will help to reduce friction and wear, and ensure that the drill press operates smoothly. Regular maintenance and inspections are also recommended to catch any problems early on.
What are some safety precautions you should take when using a drill press arm?
When using a drill press arm, it’s important to wear protective gear such as safety glasses, gloves, and earplugs. Always make sure the drill bit is securely in the chuck before starting the machine, and never adjust the drill while it is running. Keep loose clothing and long hair out of the way, and avoid distractions when operating the machine.
How do you choose the right drill press arm for your needs?
To choose the right drill press arm, consider the type of material you’ll be drilling, the size of the holes you need to make, and the precision of the work required. You should also consider the power and speed of the drill press, as well as the size and weight of the machine.
Can a drill press arm be used for other applications besides drilling?
Yes, a drill press arm can be used for other applications besides drilling, such as sanding, polishing, or even grinding. However, you will need to use the appropriate attachments and tools to do so safely and effectively. Always consult the manufacturer’s instructions and safety guidelines before using a drill press arm for any other applications.