How to Build a Gas Powered Air Compressor: A Comprehensive Guide for Beginners
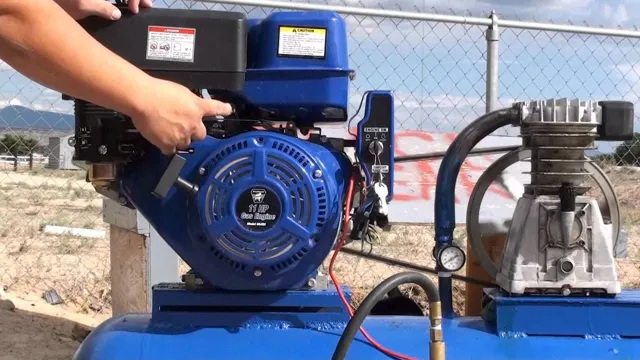
Have you ever found yourself in need of a powerful air compressor but unwilling to spend a fortune on a commercial-grade model? Building your own gas-powered air compressor might be the solution! With the right tools and some patience, creating a customized air compressor at home can save you money and give you the power you need for various tasks. In this comprehensive guide, we’ll walk you through the steps to build a gas-powered air compressor from scratch. We’ll cover everything from choosing the right engine and materials to assembling and testing your machine.
Whether you’re a DIY enthusiast who loves a challenge or a professional looking to create a versatile compressor for your workshop, this guide has got you covered. But first, you might be wondering: why go gas-powered? Although electric air compressors are often more convenient for indoor use, gas-powered models offer greater portability and power – making them ideal for outdoor projects, emergency uses, and remote locations. Plus, they don’t require any electrical outlets, making them more flexible when it comes to finding a power source.
So, let’s dive in and get started on building your very own gas-powered air compressor – a machine that will not only save you money but also bring a sense of satisfaction and pride to your DIY efforts.
Introduction
Building a gas-powered air compressor may seem like a daunting task, but with the right tools and a bit of know-how, anyone can do it. To start, you’ll need a gas engine, an air compressor pump, and some basic plumbing supplies. Begin by mounting the gas engine and the pump to a sturdy base, making sure to align the pulleys correctly.
Next, connect the pulleys with a belt, ensuring that the tension is just right. Then, attach the plumbing supplies, using T-fittings to connect the various components. Finally, add a pressure regulator and a tank to store the compressed air.
Once everything is in place, test the compressor and adjust the pressure as needed. With these simple steps, you can build a gas-powered air compressor that can power pneumatic tools, inflate tires, and more.
Why Choose a Gas-Powered Air Compressor?
If you are searching for a powerful and reliable air compressor, a gas-powered option may be just what you need. Gas-powered air compressors are designed for high-performance applications and are capable of delivering more power than electric models. They are also highly portable, making them ideal for use in remote locations or on job sites where electrical power may not be available.
With their excellent efficiency and durability, gas-powered air compressors are a popular choice for professionals and DIY enthusiasts alike. Whether you need to power tools or inflate tires, a gas-powered air compressor can help get the job done quickly and efficiently.

What You Will Need
Introduction: Planning a project may seem easy at first glance, but it is a complicated and tedious process. To ensure that you are successful, you need to have a plan and know what you will need. Every project is unique and will require certain things for its completion.
In this blog, we will discuss the essentials you will need to plan and execute any project successfully. From project management software to a project team and budget, we will cover everything you require for a successful project. The most important thing you will need is a project management tool.
It is essential to keep every task, deadline, and budget in one place. A project management tool will help you manage the project and keep track of all the details. A project management tool is intuitive as well as user-friendly, making it an excellent choice even for people who aren’t tech-savvy.
Furthermore, you will need a project team to execute the plan. An efficient team comprises of skilled professionals with diverse abilities who can perform various roles without error. Therefore, it is essential to have capable team members who understand the project’s goals and can efficiently execute the plan.
Another crucial element is the project budget. You must have a clear understanding of all expenses. It is helpful to set realistic expectations in initial stages, review the expenses at regular intervals and be flexible if necessary.
In conclusion, planning a successful project is more manageable with the right tools, a well-rounded team, and a clear budget plan. Whether it’s a personal project or a corporate initiative, these essential requirements are the most valuable resources for your success.
Step-by-Step Guide
Are you looking to build a gas powered air compressor? It may seem like a daunting task, but with the right tools and instructions, it can be done easily. The first step in building a gas powered air compressor is to gather all the necessary materials such as an engine, a compressor pump, a pressure switch, and an air tank. Once you have all the materials, start by mounting the engine onto a frame and attaching a belt to the compressor pump.
Next, connect the pressure switch to the pump and set it to the desired pressure. Connect the air tank to the pump and make sure it is secure. Finally, fill the tank with gas and oil, start the engine, and test your compressor.
With these simple steps, you can easily build your very own gas powered air compressor that will make all your tasks much easier.
Step 1: Tank Selection and Preparation
When it comes to Saltwater Aquariums, selecting the right tank in the first place is essential. A larger tank is always better than a smaller one, as it provides more space and stability for fish and they will be less likely to become territorial and aggressive towards each other. Before purchasing the tank, it’s important to take into account the type of fish you want to keep and make sure you have adequate filtration and lighting.
Once you have the tank, it’s important to prepare it properly. This includes cleaning it thoroughly with aquarium-safe cleaners and allowing it to cycle for at least a week before adding any fish to ensure that the water is properly conditioned to support marine life. Lastly, when setting up the tank, it’s important to ensure that the substrate, decorations, and water temperature are all suitable for the type of fish you plan to keep.
By taking these steps in the initial stages, you’ll set your saltwater aquarium up for success in the long run, and keeping your fish healthy and happy.
Step 2: Compressor Selection and Mounting
When it comes to selecting and mounting a compressor for your project, there are a few key factors to consider to ensure its performance and longevity. The first step is to determine the air demand needed for your tools and equipment. This will dictate the size and capacity of the compressor you will need.
It is also important to consider the power supply and space available for the compressor. Once you have selected the appropriate compressor, it is important to mount it securely to prevent vibration and noise. This will also ensure proper airflow for cooling and prevent damage to the compressor.
Whether you are using a stationary or portable compressor, proper selection and mounting are crucial for optimal performance and safety of your project. So take the time to consider your options and choose a compressor that suits your needs.
Step 3: Engine Selection and Mounting
When it comes to selecting and mounting an engine for your project, there are a few key considerations to keep in mind. First, you’ll need to choose an engine that fits the requirements of your project in terms of power and size. This can be a tricky task, as there are many different options available and each has its own strengths and weaknesses.
You’ll also need to consider the mounting process, ensuring that the engine is securely attached to the frame and that all necessary components, such as the fuel system and electrical connections, are properly installed. One important factor to keep in mind throughout the engine selection and mounting process is safety. This should be a top priority, as a poorly mounted engine can be dangerous and even deadly.
By carefully weighing your options and taking the necessary precautions, you can ensure that your engine selection and mounting process is successful and safe.
Step 4: Assembly and Wiring
Now that all the components have been prepared, it’s time to assemble the keyboard and wire everything up. The first step is to mount the PCB onto the case, ensuring that all the switches are in their designated places. Then, the stabilizers must be attached to the necessary switches to ensure stability and smooth key press.
Next, the keycaps can be placed onto the switches. Once the keyboard is assembled, it’s time to wire it up. The wiring process can be quite complex, but following a comprehensive guide or schematic can make it much simpler.
The wires must be connected to the correct locations on the PCB, and the process must be repeated for each switch. This process can take some time, but it’s essential to ensure the keyboard will function correctly. Once all the wires are in place, it’s time to test the keyboard.
This is when all the hard work pays off, and the keyboard becomes operational. It’s essential to test each key to ensure it registers correctly and that all the functions work correctly. If there are any issues, it’s usually due to a mistake in the wiring, which can be easily fixed by double-checking the connections.
In conclusion, assembling and wiring a custom keyboard can be a daunting task, but it’s also incredibly rewarding. Taking the time to double-check each step and ensuring everything is correctly wired is essential for a functional keyboard. The process can be time-consuming, but it’s well worth the effort when you can enjoy your custom keyboard design.
Testing and Maintenance
Building a gas-powered air compressor is a great DIY project for those with a knack for engineering. However, before you start building, it’s important to conduct several tests to ensure the safety and functionality of the air compressor. First, check the pressure gauge to ensure it’s compatible with the pressure level of the compressor.
You should also check the oil level and ensure it’s filled to the correct level. Once you’ve conducted these tests, it’s crucial to carry out regular maintenance checks for optimal functionality. This includes regular oil changes and replacing any worn-out parts.
By conducting these tests and regular maintenance checks, you can be confident in the safety and functionality of your gas-powered air compressor.
Testing your Gas-Powered Air Compressor
Testing your gas-powered air compressor is crucial to ensure that it’s working effectively and efficiently. Regular maintenance checks and testing can prevent costly breakdowns and prolong the life of your compressor. One way to test your compressor is by checking its pressure levels.
Use a pressure gauge to determine the pressure levels of your compressor. If the pressure level isn’t up to the specified level in the user manual, it may indicate a problem. Another way to test your compressor is by checking the oil levels.
Low oil levels can cause premature wear and tear on the compressor’s components and reduce its lifespan. Replace the oil regularly, and keep the levels filled within the recommended range. Additionally, inspect the air filters frequently, as clogged filters can cause the compressor to overheat and malfunction.
Regular maintenance and testing of your gas-powered air compressor can save you both time and money in the long run.
Maintaining Your Gas-Powered Air Compressor
Maintaining your gas-powered air compressor is crucial to ensure it operates at peak performance and lasts for many years. Testing and maintenance are essential to keeping your compressor in optimal condition. Periodically checking the oil levels and replacing the filters are simple tasks that can save you from costly repairs in the future.
Additionally, testing the pressure regulator and safety valve guarantees that your compressor is functioning correctly and efficiently. Proper maintenance not only extends the lifespan of your compressor, but it also ensures your safety and the safety of those around you while you work. Think of it as the same as keeping your car engine running smoothly; regular maintenance will help the compressor run at its best and avoid potential issues in the future.
Overall, while it may seem like an extra task to take on, maintenance is key for trouble-free and continuous operation of your compressor.
Safety Tips
If you’re looking to build your own gas-powered air compressor, it’s important to take safety precautions to ensure that no one gets hurt. First and foremost, make sure that you are working in a well-ventilated area, as gas-powered equipment can produce toxic fumes. Additionally, use only high-quality materials and follow all manufacturer instructions carefully.
Be sure to wear proper protective equipment, like goggles and gloves, and keep a fire extinguisher nearby in case of emergency. Finally, never leave gas-powered equipment unattended and always turn off the fuel source before performing any maintenance or repairs. By taking these steps, you can build a safe and reliable gas-powered air compressor that will serve you for years to come.
Precautions Before Building and Using Your Compressor
Safety Tips Building and using your compressor can be a great way to save money and have more control over your compressed air supply. However, you should always prioritize safety when using any type of tool or equipment. Before you start building your compressor, be sure to read the instruction manual thoroughly and familiarize yourself with all the parts and components.
Always wear the appropriate safety gear, such as safety glasses, gloves, and ear protection. It is also important to make sure that your workspace is well-ventilated and free from any flammable materials or explosive gases. While using your compressor, avoid overloading it with more pressure than it can handle, and be sure to turn it off and unplug it before making any adjustments or repairs.
Remember, taking the proper safety precautions can help prevent accidents and injuries when building and using your compressor.
Safety Measures While Running Your Compressor
Running a compressor is a job that requires safety precautions to be taken to avoid accidents and injuries. The first and most important safety tip is to always follow the manufacturer’s instructions and guidelines. Before starting your compressor, make sure to check all of its components for any damage or defects.
It’s also essential to wear safety glasses, gloves, and earplugs to protect yourself from any flying debris or loud noise that might occur while the compressor is running. Always keep the compressor away from flammable substances to prevent any risk of fire. Additionally, it’s important to keep the work area clean and organized, ensuring that there are no tripping hazards or anything that could cause you to fall while operating the machine.
By following these safety tips, you can prevent accidents and enjoy a smooth and uninterrupted experience while running your compressor.
Conclusion
In conclusion, building a gas powered air compressor requires a combination of mechanical expertise, creativity, and a deep appreciation for the power of compressed air. Like a master chef crafting the perfect dish, a skilled builder must carefully select the right ingredients – a powerful engine, robust air tank, and efficient compressor – before bringing them together in just the right way to create a tool that can handle even the toughest pneumatic challenges. So whether you’re powering pneumatic tools at a construction site or filling up your car’s tires at home, with a little know-how and a lot of elbow grease, you too can create the ultimate gas powered air compressor.
Happy building!”
FAQs
What materials are needed for building a gas powered air compressor?
The materials required for building a gas powered air compressor include an engine, pump, tank, pressure gauge, regulator, belts, bolts, and fittings.
What should be the horsepower of the engine for the compressor?
The horsepower rating of the engine depends on the requirements of the compressor. A 5-7 horsepower engine is sufficient for light-duty tasks, while a 10-13 horsepower engine is suitable for heavy-duty applications.
How to maintain a gas powered air compressor?
Regular maintenance is essential for the proper functioning of a gas powered air compressor. It includes cleaning the air filter, engine oil change, checking the belt tension, inspecting hoses for leaks and cracks, examining the pressure regulator, and ensuring proper fuel mixture.
What is the maximum pressure that a gas powered air compressor can generate?
The maximum pressure generated by a gas powered air compressor can range from 100 PSI to 175 PSI, depending on the type and size of the compressor.
What is the capacity of the air tank in a gas powered air compressor?
The air tank capacity of a gas powered air compressor varies from model to model. It can range from 20 gallons to 80 gallons or even more, depending on the intended use.
How to troubleshoot common issues in a gas powered air compressor?
Common issues in a gas powered air compressor include low pressure, compressor not starting, excessive noise, and air leaks. The best way to troubleshoot these issues is to refer to the manufacturer’s manual or consult a professional.
How long can a gas powered air compressor run on a full tank of fuel?
The runtime of a gas powered air compressor on a full tank of fuel depends on the tank size, the load on the compressor, and the engine efficiency. Generally, a gas powered air compressor can run for a few hours up to 8-10 hours on a full tank of fuel.