If you’re a DIY enthusiast or a professional mechanic, you know how valuable an air compressor can be. It’s a powerful tool that can help you tackle various projects with ease. However, connecting an air compressor can be a daunting task for anyone, especially if you’re doing it for the first time.
But fear not, in this step-by-step guide, we’ll walk you through the process of connecting an air compressor. Whether you’re looking to inflate tires or power your tools, this guide will help you get started quickly and easily. So, grab your air compressor and let’s get started!
Gather Essential Tools
Before you can connect your air compressor, you need to gather the essential tools needed for the job. Firstly, you will need a suitable air compressor hose that can handle the required PSI and CFM that your compressor outputs. Make sure to choose the right length of hose that will allow you to move the compressor around easily while still reaching your tools.
Next, you will need quick-connect fittings to attach to both the compressor and the tool you’re using. These fittings are essential as they allow you to quickly and easily switch between tools without having to unscrew and rescrew different hoses. Some other tools you may need depending on your setup include teflon tape to ensure a tight seal between fittings, a pressure regulator to control and adjust the output PSI, and an oil/water separator to prevent any unwanted moisture reaching your tools.
By gathering all the necessary tools beforehand, you can ensure a smooth and straightforward process when connecting your air compressor.
What You Will Need
If you are planning to start any DIY project, the first step is to gather essential tools. These tools will help you perform tasks more efficiently and accurately. Some of the basic tools that you will need include a measuring tape, a level, a screwdriver, a hammer, and pliers.
Additionally, you might need other specialized tools depending on the type of project you’re working on. For instance, if you are working on a woodworking project, you might need a saw, a chisel, and a hand plane. Similarly, for electrical projects, you might need a wire cutter, a wire stripper, and a voltage tester.
Therefore, before starting any project, make sure to take inventory of the necessary tools and acquire them if you don’t already have them. That way, you won’t have to stop halfway through your project to search for missing tools.
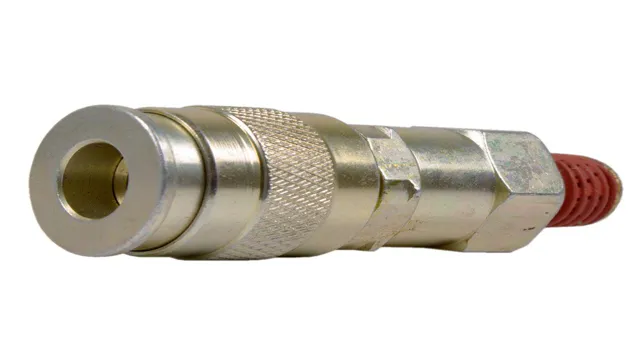
Safety Precautions
When it comes to taking on any DIY project, safety should always be a top priority. One of the first steps in ensuring you remain safe during your project is to gather essential tools. Having the right safety equipment can help protect you from serious injuries.
Before you begin any project, make sure you have safety goggles, a dust mask, gloves, and ear protection. Depending on your project, you may also need a hard hat and steel-toed boots. We understand that safety gear might not be the most comfortable or stylish option, but it should always be given priority.
These safety tools can make all the difference in protecting you from potential accidents while working on your DIY project. By taking the necessary precautions and using the right tools, you can ensure your safety and make your project more enjoyable and worry-free.
Preparing the Air Compressor
Connecting an air compressor is not as easy as just plugging it in and turning it on. Preparation is key to ensure maximum efficiency and safety. First, check the manufacturer’s instructions to determine the proper voltage and power source for the compressor.
Confirm that the compressor is grounded and has the appropriate electrical wiring and circuit breaker. Next, adjust the pressure switch to the desired level before connecting any hoses or accessories. Once your compressor is properly set up, attach any necessary hoses or attachments tightly to prevent leaks.
It’s essential to wear safety glasses, ear protection, and gloves when using an air compressor. A good rule of thumb is to conduct routine checks and maintenance to ensure optimum performance. Now that you know how to get your air compressor up and running, let’s get to work!
Choose a Location
When it comes to preparing your air compressor, choosing the right location is crucial for achieving optimal performance and longevity. A suitable location should be well-ventilated and free from dust and debris that can clog your filters and damage your equipment. Preferably, it should be situated in an area that’s close to your main power supply, where you won’t have to worry about tripping over cords or cables.
Additionally, you’ll want to place your compressor on a stable surface that’s level and firm, with adequate space around it to allow for proper airflow. By taking these essential steps, you’ll ensure that your compressor works efficiently and lasts for years to come. Remember, a well-prepared location can make all the difference!
Assemble the Compressor
Preparing the air compressor is essential before assembling it. First, ensure that the compressor is placed in a well-ventilated area and that all the necessary components are easily accessible. Then, check if the air filter is clean and replace it if necessary.
The next step is to add the oil and fill it to the recommended level. It’s crucial to use the right oil type and follow the manufacturer’s instructions carefully. Once the oil is added, connect the hose and plug it into a power source.
Turn it on and let it run for a few minutes to test its functionality. Lastly, inspect all the parts to make sure that everything is tightly secured and there are no leaks. By performing proper preparation and maintenance, you can ensure that your air compressor is functioning at its best and producing clean and reliable compressed air for your needs.
Attach Air Filter and Regulator
When setting up your air compressor, it’s important to attach an air filter and regulator to ensure your tools and equipment receive clean, consistent air pressure. The air filter works to remove contaminants from the air, such as dust and debris, which can damage your tools and affect their performance. The regulator controls the air pressure, allowing you to adjust it to the appropriate level depending on the task at hand.
Before attaching the filter and regulator, be sure to consult your air compressor’s manual for specific instructions and make sure you have the necessary tools, such as Teflon tape. Once you have attached the filter and regulator, make sure they are functioning properly before using your air compressor. By taking the time to properly prepare your air compressor with these essential components, you’ll be able to work with confidence knowing your tools are receiving clean, consistent air pressure.
Connecting the Hose
Connecting a hose to your air compressor is a breeze and can be done in just a few simple steps. Start by turning off your air compressor and relieving any pressure in the hose. Next, locate the outlet valve on your compressor and ensure the hose you plan to use is the correct size for that outlet.
Connect one end of the hose to the outlet valve and ensure it’s secure before connecting the other end to your tool or accessory. Finally, turn your compressor back on and ensure it’s functioning correctly. It’s always important to double-check the connection before using your tool, so perform a quick visual inspection to make sure everything is fitted correctly.
Overall, connecting a hose to your air compressor is a straightforward process that can be done without any hassle.
Select the Right Hose
When it comes to connecting hoses, it’s crucial to select the right one for the job. First, consider the type of hose needed for the specific task. There are various types of hoses, including garden hoses, fire hoses, and reinforced rubber hoses, each designed for particular purposes.
Second, consider the diameter of the hose, as a larger diameter means a higher flow rate. Additionally, the material of the hose should be chosen based on the type of liquid or gas it will be carrying, as some materials may be more durable under certain conditions. Overall, selecting the right hose for the job is essential to prevent leaks, bursts, or damage to the end product.
Attach the Hose to the Compressor
When it comes to using a compressor, it’s important to connect the hose properly. Begin by finding the outlet on the compressor and screwing the end of the hose into place. Make sure it’s secure before you turn the compressor on.
Some hoses may require an extra attachment, like a coupler, to connect properly. Be sure to check the manual for specific instructions on how to attach the hose to your particular compressor model. Remember, safety is key when working with a compressor, so always wear the necessary protective gear and keep a close eye on the pressure gauge to ensure you don’t exceed the maximum pressure limits.
With these steps and precautions in place, you’ll be able to connect your hose safely and efficiently.
Connect Hose to Air Tools
Connecting the hose to your air tools may seem like a simple task, but getting it right is crucial for effective performance. Firstly, ensure that the hose you are using is suitable for your air tool. Using the wrong hose can lead to lower airflow, poor efficiency, and even damage to your tool.
Next, attach the hose to your tool using the proper fittings. Most air tools have a male quick-connect fitting, while hoses have a female fitting. Press the two fittings together until you hear a click, indicating they are securely attached.
Finally, make sure the hose is tight by pulling on it gently. A loose connection can lead to air leakage, which will negatively impact the tool’s performance. By following these steps, you can connect your hose and air tool effectively and ensure optimal performance.
Testing the Connections
Connecting an air compressor may seem like a daunting task, but with the right steps, you can do it yourself. Before you begin, ensure that you have all the necessary components, including the compressor, regulator, hoses, and connectors. Start by attaching the regulator to the compressor and tightening it securely.
Connect the hoses to the regulator and tighten the connectors with a wrench. Make sure that the hose connections are secure and tight, as this will prevent any air leakage. Once you have connected the hoses, switch on the compressor and check for any air leaks.
If everything is working properly, you should be able to inflate tires or operate air tools with ease. Connecting an air compressor is a simple process, and with these steps, you can do it yourself in no time.
Test for Leaks
When it comes to testing for leaks, one of the most critical steps is to test the connections. Making sure that all your connections are secure is essential since even the slightest leak can cause water damage and result in hefty repair bills. The first thing you should do is turn off the water supply and check all the connections for signs of leaks.
Be sure to examine each component of the plumbing system, including faucets, pipes, joints, and valves. Once you’ve inspected all the connections, it’s time to conduct a pressure test to confirm that everything is secure. You can do this by attaching a pressure gauge to the faucet and turning on the water supply.
If the pressure holds steady, then your connections are secure. If you notice any drop in pressure, then you’ll need to identify and fix the leak. Taking the time to test for leaks can save you from a lot of headaches and hassles down the road.
Check for Proper Airflow
When testing the connections of your air conditioning system, it’s crucial to check for proper airflow. After all, blocked or restricted airflow can result in a plethora of problems, including poor performance and increased energy bills. To ensure optimal airflow, make sure to inspect all vents and registers, removing any obstructions such as dirt, debris, or furniture that may be blocking them.
Additionally, check the air filter to verify that it’s clean and free from debris, as this too can impede proper airflow. If airflow problems persist, it may be time to call in a professional to diagnose and resolve the issue. By performing regular maintenance and keeping an eye out for any potential airflow issues, you can keep your air conditioning running smoothly and efficiently throughout the hot summer months.
Conclusion
Connecting an air compressor is like putting together pieces of a puzzle. It may seem daunting at first, but with careful attention to detail, anyone can succeed. Remember, safety comes first.
Always make sure to read the manufacturer’s instructions and wear protective gear. Don’t be afraid to ask for help from a knowledgeable friend or professional. With a little patience and determination, you’ll be ready to power up your air tools and tackle any project with ease.
So, go ahead and take a deep breath (or two) – you’ve got this!”
FAQs
What type of plug do I need to connect my air compressor?
The plug required for your air compressor may vary depending on the model. Check the product specifications or consult with a professional electrician to determine the appropriate plug type.
What size air hose should I use to connect my air compressor?
The size of the air hose largely depends on the air compressor’s output and your intended use. A general rule of thumb is to use a hose with a diameter equal to or greater than the compressor’s outlet port for maximum efficiency.
Can I use a regular extension cord to connect my air compressor?
It is not recommended to use a regular extension cord to connect your air compressor, as it may not be able to handle the machine’s power requirements. A dedicated, heavy-duty extension cord with the appropriate amperage rating is a better option.
What is the appropriate pressure setting for my air compressor?
The appropriate pressure setting for your air compressor depends on the tool or application you will be using it for. Refer to the tool’s specifications or consult with a professional to determine the correct pressure setting.
Is it necessary to use an air regulator when connecting my air compressor?
An air regulator can help to control the output pressure and airflow of your air compressor, preventing damage to both the machine and any attached tools. Therefore, it is highly recommended to use one when connecting your air compressor.
How often should I drain the moisture from my air compressor tank?
Moisture can build up in your air compressor tank over time, affecting your tools’ performance and causing damage to the machine. It is recommended to drain the moisture from the tank after each use or at least once a day.
Can I connect multiple tools to my air compressor at once?
It is possible to connect multiple tools to your air compressor at once, but it is crucial to ensure that the compressor has enough power to handle the combined airflow requirements of all the tools. Check the machine’s specifications and the tools’ requirements before attempting to connect them.