How to Connect Air Compressor to PVC Pipe: A Step-by-Step Guide
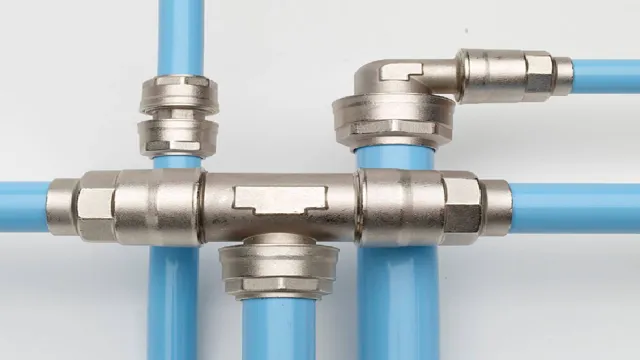
Are you looking for an efficient and cost-effective way to connect your air compressor to PVC pipe? Look no further! In this blog post, we will guide you through the process step-by-step. We recognize that connecting an air compressor to PVC pipe can be a bit daunting for those who are new to the game. But fear not, because with some basic tools and a bit of know-how, you can easily connect your air compressor to PVC pipe with confidence.
Similar to fitting a puzzle piece, we’ll show you how to seamlessly attach your air compressor to PVC pipe and ensure a smooth flow of air to power your projects. So, let’s get started!
Gather the Necessary Materials
Connecting an air compressor to PVC pipe is a simple process, but it requires some basic materials. Firstly, you will need a good quality air compressor with a built-in pressure regulator and valve. Secondly, you will require PVC pipe, preferably rated for pressure above your compressor’s output pressure.
A polyurethane tubing can also work; however, it has a lower working pressure and can become damaged over time. You will also require a fitting to connect the PVC pipe or tubing to the compressor. A brass or stainless-steel fitting is recommended because they are more durable and corrosion-resistant.
Lastly, you will need Teflon Tape for wrapping around the threads of the fitting to create a seal. With all these materials, you are ready to proceed to the connection process.
Air Compressor, PVC Pipe, Fittings, Teflon Tape, Wrenches
Assembling your own air compressor system can be a fun and rewarding project, but before you get started, you’ll need to gather all the necessary materials. First and foremost, you’ll need an air compressor itself. Look for one that meets your specific needs, whether for industrial use or personal DIY projects.
Next, you’ll need PVC pipe, which will serve as the main conduit for delivering compressed air to your tools. Make sure to choose a pipe size and thickness that can handle the pressure of your compressor. Fittings, such as elbows and tees, will also be necessary to connect your PVC pipe components.
Be sure to select high-quality fittings that are compatible with your pipe size and style. Teflon tape will come in handy when attaching fittings to prevent air leaks. Lastly, you’ll need a set of wrenches to tighten and loosen fittings as needed.
Gather all of these materials before diving into your air compressor project to ensure a smooth and seamless assembly process.

Prepare the PVC Pipe
If you’re wondering how to connect an air compressor to a PVC pipe, the first step is to prepare the pipe. You want the pipe to be clean and smooth on the inside so that the air can flow through it without any obstructions. Start by cutting the PVC pipe to the desired length.
Then, use a deburring tool or sandpaper to smooth out the rough edges on the inside of the pipe. Any debris or dust left behind can cause problems when connecting the air compressor. After smoothing out the edges, wipe down the inside of the pipe with a clean cloth to remove any remaining debris.
This ensures that the air compressor can be properly connected and that there are no leaks or inefficiencies in the system. With the PVC pipe properly prepared, you’re ready to move on to the next steps in connecting your air compressor.
Cut the pipe to the desired length and remove any burrs or sharp edges
Preparing the PVC pipe for your project is one of the most essential steps to ensuring a successful outcome. To begin, it’s necessary to cut the pipe to the required length, which can be done using a hacksaw, pipe cutter, or PVC cutting tool. Once you have cut the pipe, it’s essential to remove any burrs or sharp edges with sandpaper or a file to avoid damage to the materials you intend to use.
These rough edges can be a hazard and, if left untreated, can cause injuries or create leaks in your project. By removing any sharp edges, you can ensure a smooth and level connection with other components, resulting in a stronger and more reliable project. In conclusion, preparation is key when it comes to successfully working with PVC pipe.
By using proper tools and taking the time to remove any rough edges, you can make sure that your project is safe, functional, and long-lasting.
Install Fittings
When it comes to setting up an air compressor to a PVC pipe system, one important step is to properly connect the fittings between the compressor and the PVC pipe. First, make sure to select fittings that match the size and type of both the compressor outlet and the PVC pipe being used. Then, use a wrench to secure the fittings tightly onto each component.
It’s important to ensure that the connections are airtight to prevent leaks and ensure efficient operation. Additionally, it may be helpful to use Teflon tape or thread sealant on the threads of the fittings to further prevent leaks. Overall, taking the time to properly install fittings is essential for a successful and safe air compressor setup.
Apply Teflon tape to the threads of the fittings to ensure a secure seal
When it comes to installing fittings, there are a few important steps you need to follow to ensure everything is secure and leak-free. One key step is to apply Teflon tape to the threads of the fittings before installation. Teflon tape acts as a sealant, helping to create a tight bond and prevent any leaks from occurring.
It’s important to apply the tape correctly, starting at the end of the fitting and wrapping it in a clockwise direction around the threads. Make sure to wrap the tape around the fitting at least two or three times to ensure a good seal. When you’re ready to install the fitting, make sure that it is tightened firmly but not over-tightened, which can damage the threads.
By taking the time to properly install your fittings and apply Teflon tape, you can help to ensure a secure and leak-free plumbing system.
Hand-tighten the fittings onto the PVC pipe and use wrenches to tighten them further if necessary
When it comes to installing fittings onto PVC pipes, it’s essential to use the right tools and techniques to avoid any leaks or damages down the line. Firstly, you should hand-tighten the fittings onto the PVC pipe, making sure that they are correctly aligned. Once you have done this, you can use wrenches to tighten them further if needed.
It’s crucial to avoid over-tightening the fittings, as this can cause cracks or breaks in the pipes, resulting in leaks. On the other hand, if you don’t tighten them enough, you may experience issues with water pressure or leaks. Thus, it’s essential to strike the right balance between hand-tightening and tool-tightening to ensure maximum stability and durability.
Pay close attention to the instructions provided by the manufacturer and use high-quality fittings to ensure that everything fits together correctly. So, grab your PVC pipes, fittings, and wrenches and get to work – you got this!
Connect the Air Compressor
Connecting an air compressor to PVC pipe is a simple process that anyone can do, but it requires a few steps to complete correctly. Firstly, ensure that the air compressor is turned off and unplugged, and then identify the intake port on the compressor. Fit a quick-connect or male pipe fitting to its end and use Teflon tape to wrap the threads.
The tape ensures an airtight seal when the fitting is tightened, preventing leaks. Next, check the PVC pipe for any cracks or damage before attaching it to the fitting using a female pipe fitting or slip coupling. Tighten the fitting by hand and then use a wrench or pliers to secure it firmly in place.
Finally, turn on the air compressor and test the system for any leaks or malfunctioning. If there are no issues, then you can use the air compressor as needed. By properly following these steps, you can safely and efficiently connect your air compressor to PVC pipe without any problem.
Attach the air compressor hose to the fitting on the PVC pipe
If you’re looking to attach an air compressor to your PVC pipe system, it’s crucial to ensure a proper connection. You can start by attaching the air compressor hose to the fitting on the PVC pipe. This can be done by simply pressing the hose’s end onto the fitting and twisting it clockwise to tighten.
Make sure it’s secure before switching on the air compressor. Once you’ve connected the hoses, it’s essential to regulate the air pressure and oil levels before using your PVC pipe system. The air compressor is the driving force behind the PVC pipe system, and without it, your system won’t function.
Take your time and double-check all connections before operating the air compressor. In this way, you can avoid any mishaps or emergencies while using your PVC pipe system. Finally, remember to disconnect the air compressor when you’re finished using it to protect it from damage and extend its lifespan.
Turn on the air compressor and ensure there are no leaks in the connections
When it comes to powering up your air compressor, you’ll want to make sure everything is connected properly and there are no leaks in the system. Start by plugging in the compressor and ensuring it’s on a stable surface. Next, attach the air hose to the compressor using the appropriate fittings.
Remember to tighten all connections and inspect for any leaks or loose connections. Turning on the compressor will help you detect any leaks in the system, and it’s important to address them before using your compressor. A leak-free system will keep your compressor running efficiently and help you complete your projects faster.
So, make sure to double-check your connections and turn on the compressor with confidence.
Conclusion
In conclusion, connecting your air compressor to PVC pipe is a breeze! With the right tools and a little know-how, you can easily create a durable and reliable system that will handle all of your pneumatic needs. Just remember to take your time, follow the steps carefully, and don’t be afraid to ask for help if you need it. With a bit of patience and determination, you’ll be blowing out pipes like a pro in no time! So, go ahead and connect that air compressor to your PVC pipes – and get ready for some seriously impressive results!”
Connecting an air compressor to PVC pipe is a simple process that can be done with just a few tools and materials. Make sure to follow the proper steps and take precautions to ensure a secure and leak-free connection.
Connecting an air compressor to PVC pipe is a simple process that requires a few essential materials and tools. First, determine the size of the compressor’s outlet and the PVC pipe’s inlet to ensure compatibility. Next, purchase the appropriate PVC fittings, such as a threaded male adapter and a PVC cement.
Before assembling the connection, make sure to clean both the compressor’s outlet and the PVC pipe’s inlet to remove any debris or oil residue. Apply a generous amount of PVC cement to one end of the threaded male adapter and screw it onto the compressor’s outlet, hand tighten and use pliers if necessary. Then, apply PVC cement to the other end of the adapter and insert it into the PVC pipe’s inlet, hand tight and use pliers if necessary to tighten it further.
Let the cement dry for at least an hour before turning on the compressor. Always wear safety goggles and gloves during the installation process to protect yourself from any potential hazards. With these simple steps, you can connect your air compressor to PVC piping efficiently and safely.
FAQs
What type of fittings do I need to connect an air compressor to a PVC pipe?
You will need a threaded male adapter that fits the air compressor outlet and has a socket to fit the PVC pipe.
Can I use regular PVC pipe for compressed air?
No, regular PVC pipe is not strong enough for compressed air. You will need to use Schedule 40 PVC pipe that is rated for pressure.
How can I ensure that my PVC pipe system is safe for compressed air?
You should consult with a professional to ensure that your PVC pipe system is properly designed, installed, and rated for the pressure and flow requirements of your compressed air system.
What should I do if I have a leak in my PVC pipe system for compressed air?
You should shut off the air compressor and release the pressure from the system. Then, identify and repair the leak before it causes further damage or poses a safety hazard.
Can I install my own PVC pipe system for compressed air?
While it is possible to install your own PVC pipe system for compressed air, it is highly recommended that you consult with a professional to ensure safety and compliance with regulations.
What is the maximum pressure that PVC pipe can handle for compressed air?
The maximum pressure that Schedule 40 PVC pipe can handle for compressed air is 150 PSI.
Do I need to use PVC cement to connect the fittings and pipe for compressed air?
Yes, you should use PVC cement to ensure a strong, leak-free connection between fittings and pipe for compressed air.