How to Convert Drill Press to Knee Mill for Precision and Efficiency

If you’re an avid DIY-er or machinist, you may have come across the common complaint of limited workspace and equipment. However, with just a few modifications, you can transform your drill press into a functional knee mill. Not only will you save space and money, but you’ll also have the ability to work on larger, more intricate projects.
Converting a drill press to a knee mill may sound like a daunting task, but with the right tools and a bit of know-how, it’s actually quite achievable. By adding a few crucial components, such as a column, spindle, and knee, you can transform your drill press into a versatile milling machine.
One of the biggest advantages of converting a drill press to a knee mill is the enhanced precision and accuracy you’ll have with your milling projects. With the added control and stability of the knee, you’ll be able to make micro-adjustments and create complex shapes with ease.
Plus, you won’t have to invest in an entirely new machine, which can save you thousands of dollars. So, if you’re looking to expand your machining capabilities without breaking the bank, converting your drill press to a knee mill may be the solution you’ve been searching for.
With a bit of time and effort, you can transform your workshop into a space that’s capable of handling even the most intricate and challenging projects.
Introduction
Are you tired of limited capabilities with your drill press but don’t want to invest in a full knee mill? There is a solution! You can easily convert your drill press into a knee mill with some simple modifications. First, you will need to securely mount a milling vise onto the drill press table. Then, attach a milling head to the drill press quill and add a digital readout to accurately measure your cuts.
By adding a knee to the table and a way to adjust the height, you can now take advantage of the capabilities of a milling machine with the convenience of a drill press. With this conversion, you can now mill slots, flats, keyways, and perform other milling operations with your modified drill press. So, give your old drill press a new lease on life and start milling!
Explaining the difference between a Drill press and Knee Mill
A drill press and a knee mill are two essential power tools in the metalworking industry. They share similar functions, yet they are different in many ways. A drill press is primarily used for drilling holes into different materials, including wood and metal.
On the other hand, a knee mill is designed for milling operations, which involve removing materials from a workpiece’s surface. In simple terms, knee mills are used for cutting and shaping metals in various forms, while drill presses are used only for drilling holes. Regardless of the differences in their functionalities, both tools use a rotating drill bit to create holes or remove materials.
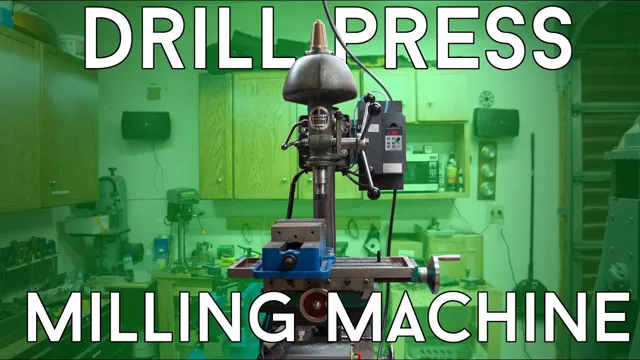
Benefits of converting a Drill Press to a Knee Mill
If you’re a DIY enthusiast who loves working with metal, you might be wondering what the next project should be. Converting a drill press to a knee mill could be an excellent idea as it offers a range of benefits. A knee mill is a type of vertical mill that sits on top of a knee.
It has a spindle that can move up and down and also provides horizontal movement. Converting a drill press saves you both money and space since a knee mill with similar features can be pretty expensive and takes up a lot of space. Additionally, the knee mill’s design makes it more precise than a drill press, especially for milling metal.
The knee’s presence provides a precise vertical axis, stability, and a method for locking the workpiece in place. Overall, converting a drill press into a knee mill is an excellent idea for the enthusiastic DIY-er.
Required Tools
If you’re looking to turn your drill press into a knee mill, there are a few tools you’ll need to get started. First and foremost, you’ll need a milling vise that can securely hold your workpiece in place. A set of end mills will also be necessary for cutting through metal, as well as a collet system to hold them.
To adjust the position of your workpiece, a milling table will be required, along with a dial indicator and edge finder to ensure accuracy. For precise cuts, a digital readout unit is highly recommended. Finally, don’t forget safety gear such as gloves, eye protection, and a respirator if you’ll be working with metal or wood shavings.
With these essential tools in hand, you’ll be on your way to converting your drill press into a versatile knee mill.
List of all tools required
If you’re planning a DIY project, it’s essential to have the right tools on hand to ensure you can get the job done efficiently and safely. Here’s a list of some of the most common tools you may need for your project: Hammer: A hammer is a basic tool that’s used to strike an object or drive nails into wood.
Screwdriver: A screwdriver is a tool used to tighten or loosen screws.
Pliers: Pliers are a versatile tool that can be used for gripping, bending, or cutting wires. Level: A level is a tool used to ensure that an object is straight and level.
Tape Measure: A tape measure is an essential tool for measuring lengths and distances accurately.
Saw: A saw is a cutting tool that’s used to cut through wood or other materials. Drill: A drill is a power tool that’s used to make holes in wood or other materials.
Safety Gear: Safety gear, such as gloves, goggles, and ear protection, is essential for protecting yourself while working with tools. Having the right tools on hand can help make your DIY project a success.
Explaining each tool and its use
When it comes to woodworking, using the right tools can make all the difference. There are several must-have tools for any woodworker, including a jigsaw, circular saw, power drill, orbital sander, and hand saw. A jigsaw is a versatile tool that can make intricate cuts and curves in wood, while a circular saw is ideal for straight cuts.
A power drill is necessary for making holes and attaching screws, while an orbital sander can smooth out rough surfaces. A hand saw is useful for making precise cuts by hand. Each of these tools plays a crucial role in woodworking and can significantly impact the quality of the final product.
Whether you’re a beginner or an experienced woodworker, having these tools on hand is essential for achieving your desired results.
Steps to Convert a Drill Press to a Knee Mill
If you’re looking to upgrade your workshop, converting a drill press to a knee mill can be a cost-effective solution. The process is not overly complicated, but it will require some time and effort. The first step is to remove the spindle from the drill press and replace it with a knee mill spindle.
This will enable you to adjust the spindle height and depth for greater precision. Once the spindle is in place, you’ll need to attach a knee to the base of the drill press. This will allow you to adjust the height of the workpiece and move it along the x and y axes.
Finally, you’ll need to add a rotary table to the drill press to enable 360-degree rotation of the workpiece. Overall, converting a drill press to a knee mill is a great way to expand your workshop capabilities without breaking the bank.
Step-by-step process to follow for the conversion
If you’re a machinist or DIY enthusiast who wants to save money and space by converting your drill press into a knee mill, you can follow these steps to achieve your goal. Firstly, you must prepare all the essential equipment and tools for the modification. This includes a mounting bracket, drawbar, milling chuck, and other relevant bits and pieces.
Secondly, remove the drilling head from the drill press and mount the knee mill head on the same place. Ensure that the new head fits correctly and securely on the column. Thirdly, install the quill of the knee mill and insert the spindle into the milling chuck.
Fourthly, attach the mounting bracket to the knee mill and fasten it to the column of the drill press. This step may require some custom modifications to fit the drill press column correctly. Finally, connect the drawbar to the spindle and milling chuck and test the Knee Mill to ensure that everything works correctly.
With these five easy steps, you can convert your drill press into a Knee Mill. This will allow you to tackle bigger projects that a drill press would not handle, such as milling metal parts, making threads, or enlarging holes. The best part is that the conversion process is relatively inexpensive compared to buying a new knee mill, and it saves an enormous amount of space in your workshop.
So, give it a try, and you’ll be surprised at the versatility and capability of your newly-created Knee Mill!
Detailed explanation of each step
“Drill Press to Knee Mill Conversion” Converting a drill press to a knee mill may sound daunting, but it can be done with the right tools, equipment, and know-how. The first step is to acquire a knee mill conversion kit, which typically includes the necessary hardware, such as spindle bearings, motor adapter plate, and drive belt. The next step is to remove the original drill press spindle and replace it with the new spindle provided in the conversion kit.
It is important to ensure the new spindle is properly aligned and secured in place. Once that is done, the next step is to mount the motor adapter plate onto the drill press column and attach the motor to the plate. The drive belt should then be installed, connecting the motor to the new spindle.
After the mechanical modifications are complete, it is time to make electrical modifications. Start by wiring the motor to a power source and adding a switch to control the motor’s on/off function. Next, install a digital readout kit to provide accurate measurements of the workpiece’s position.
This is essential for precision milling operations. Finally, adjust the knee mill’s table to ensure it is level and perpendicular to the spindle, and install any necessary accessories such as collets, end mills, or clamps. In conclusion, converting a drill press to a knee mill is a complex yet rewarding process that requires patience, attention to detail, and proper equipment.
By following these steps and ensuring proper alignment and calibration, you can turn your drill press into a versatile milling machine capable of handling a wide range of materials and applications. Do remember to adhere to safety guidelines and use proper personal protective equipment at all times.
Testing and Calibrating
If you’re looking to convert a drill press to a knee mill, there are a few key steps to follow to ensure that the final product meets your needs and expectations. First, you’ll want to make sure that your drill press is sturdy enough to handle the modifications you’ll be making – adding a knee and adjusting the height of the head can place additional stress on the machine. Once you’re confident in your drill press, you’ll need to remove the chuck and begin making modifications.
This might include adding a knee, adjusting the motor mount, and installing a milling head. Once you’ve made these changes, it’s crucial to test and calibrate the machine to ensure that it’s working properly and accurately. This might include checking the alignment of the spindle and milling head, testing the depth and accuracy of the cut, and adjusting any settings or components as needed.
With patience and attention to detail, you can successfully convert your drill press into a functional knee mill that’s ready for whatever tough machining projects come your way.
Importance of Testing and Calibrating after the conversion
When it comes to converting systems, testing and calibrating are crucial steps that should not be overlooked. Even if the conversion process ran smoothly and there were no apparent issues, it is still essential to double-check everything before using the system. Testing ensures that the system is functioning correctly and all data, functions, and features are working as intended.
This step can save time and resources in the long run by avoiding potential problems and errors. Calibration, on the other hand, ensures that the system is accurate and producing reliable results. This is particularly important if the system is involved in critical processes or decision-making.
Failing to calibrate the system can lead to incorrect data and flawed outcomes. In summary, testing and calibrating after a system conversion is essential to maximize system performance, maintain accuracy, and avoid potential issues.
Step-by-step process of testing and calibration
Testing and calibrating are essential steps in ensuring that equipment and instruments are functioning correctly. The process involves carefully verifying the reliability, accuracy, and precision of the machines and devices used in various applications. Testing is done by following a step-by-step procedure that starts by examining the equipment specifications, determining the testing requirements, and setting up a testing environment.
Calibration, on the other hand, involves adjusting and aligning the equipment to ensure that it meets the specified accuracy and precision levels. This process is done by comparing the measurement results obtained from the device being tested to a reference standard. Regular testing and calibration of equipment and instruments can improve their reliability, accuracy, and lifespan.
It also helps to ensure that the results obtained from measurements and experiments are valid and reliable. By implementing these steps, equipment users can be confident in the results obtained from their instruments and machines, allowing them to make informed decisions based on accurate data.
Benefits and process of converting a Drill Press to a Knee Mill
Testing and Calibrating your converted Drill Press Knee Mill is crucial in ensuring accuracy and safety in your machining projects. It is best to start with a thorough inspection of your machine, checking for any loose parts or misalignment. Next, you will need to check the tramming of your knee mill to ensure that your spindle and table are perpendicular.
This is done by mounting an indicator on the spindle and measuring the variance as you move it along the table. Adjust the knee and head until the variance is within acceptable limits. Once you have checked the tramming, you can move to test the accuracy of your spindle and quill travel.
Install an edge finder and bring it close to your workpiece, ensuring that there is no movement. Turn on your spindle, and slowly move the quill down until the edge finder is touching the workpiece. Record the reading on your digital readout.
Repeat the process for different positions on your table to ensure that the readings are consistent. Finally, you will need to calibrate your machine’s digital readout to ensure that it accurately reflects the movement of your spindle and quill. Follow the manufacturer’s instructions, and make sure to enter the correct values for your machine.
Calibration may require adjustments to your scale or backlash compensation to ensure accurate readings. By testing and calibrating your converted Drill Press Knee Mill, you can ensure that your machine is accurate, precise, and safe to use. Don’t rush the process, take the time to get every measurement and readout correct, and you’ll be set up for success in your machining projects.
Conclusion
In conclusion, converting a drill press to a knee mill is a smart way to repurpose a machine that may have been collecting dust in your garage. With a few simple modifications, you can transform your drill press into a versatile milling machine that can handle a wide range of projects. This DIY project is a great way to save money, improve your skills, and unleash your creativity.
So if you’re ready to take your DIY projects to the next level, grab your tools and let’s convert that drill press into a knee mill!”
FAQs
What are the advantages of converting a drill press to a knee mill?
Converting a drill press to a knee mill allows for more accurate and precise milling, as well as the ability to perform more complex milling operations.
Can any drill press be converted to a knee mill?
No, not all drill presses can be converted to a knee mill. It is important to thoroughly research and ensure that the drill press being used has the necessary components and rigidity to perform as a knee mill.
What tools and materials are needed to convert a drill press to a knee mill?
The necessary tools and materials may vary depending on the specific drill press being used, but typically include a milling table, mounting brackets, T-nuts, and a vise.
Is it difficult to convert a drill press to a knee mill?
Converting a drill press to a knee mill can be a challenging and time-consuming process, especially for those without experience in metalworking or machine building.
Can a converted drill press knee mill be used for professional machining work?
While a converted drill press knee mill can be a cost-effective solution for hobbyists or DIY projects, it may not be suitable for professional machining work due to the differences in precision and rigidity compared to a dedicated knee mill.
What safety precautions should be taken when using a converted drill press knee mill?
It is important to always wear proper personal protective equipment, such as safety glasses and gloves, when using any machine tool. Additionally, it is important to follow all manufacturer instructions and to never try to perform operations that exceed the machine’s capabilities.
Can a converted drill press knee mill be converted back to a drill press?
Yes, a converted drill press knee mill can typically be converted back to a drill press by removing the milling components and returning the machine to its original configuration.