How to Diagnose Air Compressor Problems: A Step-by-Step Guide for Quick Troubleshooting
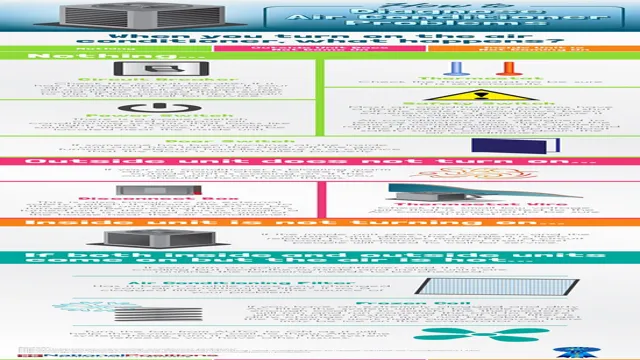
Air compressors are a indispensable tool for countless industries, from manufacturing to automotive to construction. They provide a reliable source of compressed air for powering machinery and tools, filling tires, and various other tasks. However, no machine is perfect and air compressors can experience problems from time to time.
Diagnosing air compressor problems can be a daunting task, especially for those who are not mechanically inclined. Fortunately, many common air compressor issues have straightforward solutions once the problem is identified. In this article, we’ll cover the most common air compressor problems and their possible causes, along with steps that can be taken to fix them.
Don’t let a malfunctioning air compressor bring your work to a halt. Read on to learn more about diagnosing air compressor problems and keep your operation running smoothly.
Introduction
If you’re facing problems with your air compressor, it can be difficult to know where to start. Diagnosing these problems can save you time and money in the long run and help you figure out if and where you may need to seek professional help. Some common signs of air compressor issues can include slow air pressure build-up, strange sounds coming from the compressor, or a compressor that won’t turn on at all.
In order to diagnose these problems and more, there are a few things you can do. One approach is to do a visual inspection of the unit and check for any visible damages or leaks. Additionally, you can check the compressor’s air filters and see if they need to be cleaned or replaced.
Another option is to check the compressor’s electrical connections and see if any wires or connections have come loose or been damaged. These simple steps can be enough to help you diagnose air compressor problems on your own.
Understanding Air Compression
Air compression is a process that involves the reduction of the volume of air by applying pressure. This is a critical concept to understand for anyone dealing with air compressors or pneumatic systems. The process of compression involves forcing the air into a smaller space, which increases its pressure and temperature.
This pressure can be measured in different units like psi, bar, or kPa. Understanding air compression is important because it impacts the efficiency and effectiveness of various applications that use compressed air, including air-powered tools, HVAC systems, and pneumatic machines. By properly managing the compression of air, you can ensure enhanced performance, reduced downtime, and maximum cost savings.
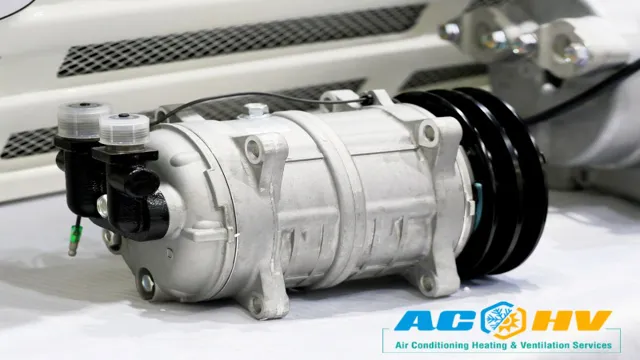
Common Air Compressor Problems
Air compressors are essential tools, but like any other machine, they are prone to problems. These problems can be caused by a variety of factors, including overheating, leaks, and improper maintenance. If you ignore these issues, they can damage your air compressor and render it useless.
In this blog section, we will discuss some common air compressor problems and how to solve them. By learning about these issues, you’ll be able to keep your equipment running smoothly and avoid costly repairs. Keyword: Air compressor problems.
Diagnosing Air Compressor Problems
If you’re experiencing issues with your air compressor, diagnosing the problem can seem like a challenge. The good news is that there are a number of common issues that can cause your compressor to malfunction. One of the most common is a leak in one of the hoses or connectors.
This can cause your compressor to lose pressure and eventually shut down. Another common issue is a faulty pressure switch, which can cause your compressor to turn on and off intermittently. In some cases, the problem may be as simple as a clogged air filter, which can prevent the compressor from taking in air properly.
By understanding the common causes of air compressor problems, you can often diagnose the issue and take steps to resolve it. If you’re not comfortable making repairs yourself, be sure to contact a professional. With the right care and attention, your air compressor can provide reliable service for years to come.
Visual Inspection and Basic Checks
If you’re experiencing issues with your air compressor, the first step in diagnosing the problem is to conduct a thorough visual inspection and basic checks. Start by checking the power source and electrical connections to ensure everything is properly connected. Next, examine the compressor for any signs of damage, such as leaks or worn out belts.
Check the air filters and oil levels to ensure they are clean and at the appropriate levels. If everything looks good, try turning on the compressor and listen for any unusual noises or vibrations. If you notice any issues during this inspection, it’s important to address them as soon as possible to prevent further damage to your equipment.
By conducting these basic checks, you can quickly pinpoint the issue and minimize downtime for your compressor.
Listening for Unusual Noises
Diagnosing air compressor problems can seem like a daunting task, but one effective method is to listen for unusual noises. When your compressor is powered on and running, take note of any sounds that are out of the ordinary, such as excessive hissing, clanking, or rattling. These noises could indicate a variety of issues, from loose or damaged components to clogged filters or excessive pressure buildup.
By paying attention to unusual sounds and working with a professional to diagnose and address the underlying issue, you can keep your compressor running smoothly and avoid costly repairs or downtime. So, next time you fire up your air compressor, listen closely and proactively address any unusual noises that arise, ensuring efficient and effective operation for all your compressed air needs.
Checking for Airflow and Pressure Problems
When your air compressor starts experiencing problems, it could be due to a number of different issues. One of the most common issues is a loss of airflow or pressure. This can be caused by a variety of factors, such as dirty or clogged filters, a leak in the hose or connectors, or a malfunctioning component.
One way to diagnose this problem is by checking the air compressor’s gauges. Check the pressure gauge to make sure it’s at the recommended level and that it’s holding steady. If the pressure is dropping, then there could be a leak somewhere.
You can also check the airflow by placing your hand over the output port and feeling for air flow. If there is little to no airflow, then there may be a blockage in the system. By identifying these issues early on, you can have them fixed before they become bigger and more costly problems.
So, always make sure to regularly inspect and maintain your air compressor to prevent any issues.
Common Solutions for Air Compressor Problems
If you’re experiencing problems with your air compressor, there are a few common solutions you can try before resorting to calling a professional. First, check for leaks in your intake valve, hoses and fittings – these can cause a decrease in pressure and affect the performance of your compressor. Additionally, if the air being produced is not the right volume or pressure, there may be a problem with the air filter or regulator.
Another issue could be the belt on the compressor, which can become worn and loose over time, causing a decrease in efficiency and power. By taking the time to diagnose air compressor problems, you can save money on repairs and keep your equipment running smoothly for years to come.
Replacing Faulty Parts
Air compressor problems, replacing faulty parts When your air compressor is giving you trouble, the first thing to consider is whether faulty parts are causing the issue. Common parts that may cause problems include the pressure switch, the motor, and the starter capacitor. If you’re experiencing issues with the pressure switch, you may notice that the compressor doesn’t turn on or off automatically, or that it’s not building up pressure properly.
A faulty motor may cause the compressor to run hot or to not run at all. The starter capacitor, on the other hand, can cause the compressor to start up slowly or to not start at all. Luckily, replacing these parts is often a straightforward process that can be done at home with some basic tools.
If you’re unsure of how to do it, consider seeking the help of a professional. By replacing these faulty parts, you can get your air compressor back up and running smoothly in no time.
Cleaning and Maintaining Air Compressor
As a responsible air compressor owner, it’s important to keep it clean and well-maintained. However, even with regular cleaning, problems can still occur. A common issue is a clogged air filter, which affects the compressor’s airflow and can cause damage to the motor.
In this case, simply cleaning or replacing the filter is the solution. Another problem can be leaks, which often occur at the hose connections. Tightening or replacing the fittings can fix the issue.
If the air compressor is producing less air than usual, it could be due to a damaged pressure switch. A replacement will be needed in this case. Finally, unusual noises coming from the compressor can indicate a loose or worn out belt.
Tightening or replacing the belt will resolve the issue. By addressing these common problems, you can prolong the life of your air compressor and ensure it is always working at its best.
Conclusion
In the end, diagnosing air compressor problems is like solving a mystery. You must pay close attention to the clues and use your detective-like skills to piece together the evidence. Sometimes the culprit is a simple fix, like a leaky valve or dirty filter, while other times it may require a bit more investigating and problem-solving.
But with a sharp mind and a trusty toolbox, you can get to the bottom of any air compressor trouble and emerge victorious!”
FAQs
What are the common signs of air compressor problems?
Some of the common signs of air compressor problems include reduced airflow, strange noises, excessive moisture in the compressed air, and repeated tripping of the circuit breaker.
How to diagnose an air compressor that won’t start?
To diagnose an air compressor that won’t start, first check the power source, then inspect the pressure switch, motor overload switch, and capacitor for any damages. If all of these components are working properly, examine the motor and the pump for any mechanical issues.
What could be the issue with an air compressor that fails to build up pressure?
If an air compressor fails to build up pressure, the issue could be due to several reasons, including a damaged pressure switch, a clogged air filter, a faulty compressor valve, or a worn-out piston or cylinder.
Why is an air compressor making loud and unusual noises?
An air compressor could be making loud and unusual noises due to several reasons, such as loose components, worn-out piston rings, a failing crankshaft bearing, or a damaged reed valve.
How to fix a leaking air compressor tank?
To fix a leaking air compressor tank, you can try tightening the drain valve or one of the fittings on the tank. If the leak persists, you may need to replace the tank gasket, the safety valve, or the entire tank.
What is the ideal pressure range for an air compressor?
The ideal pressure range for an air compressor depends on the type of tool or equipment you are using with it. However, most air compressors operate at a range of 90-150 PSI.
How often should I perform maintenance on my air compressor?
You should perform maintenance on your air compressor regularly, including checking the oil level, replacing the air filter, draining the tank, and inspecting the components for wear and tear. The frequency of maintenance depends on the usage and the manufacturer’s recommendations.