Do you find yourself frustrated with the wobbling of your drill press? It’s a common problem and can seriously affect your working accuracy and productivity. However, don’t worry too much, as fixing drill press wobble is easier than you may think. With a comprehensive guide, you will be able to make your drill press sturdy, accurate, and efficient in no time! The wobbling of a drill press can be caused by various factors, including misaligned pulleys, worn-out spindle bearings, or loose belts.
It can also happen due to improper maintenance, or simply with time and usage. But whatever the cause, the end result is a shaky drill press that can ruin your workpiece and put you off your project. In this blog post, we will walk you through the steps to identify the cause of the wobble and how to fix it.
We will cover everything from inspecting the pulleys to replacing the bearings, tightening the belts, and adjusting the quill. You will learn simple tips and tricks to get your drill press to function smoothly and precisely, without any unwanted movement or vibrations. Imagine working with your drill press, feeling confident and in control, as you create precise holes with ease.
Fixing your drill press wobble will not only enhance your accuracy, but it will also save you time, frustration, and even money in the long run. So let’s dive in and start fixing that wobbly drill press!
Diagnosing the Problem
If you’ve noticed your drill press wobbling or shaking while in use, there are several potential culprits to consider. First, check the chuck and make sure it’s properly tightened and securely holding the drill bit. From there, inspect the table and column for any misalignments or defects.
It’s also important to confirm that the drill press is sitting on a level surface and that its feet are properly adjusted. If none of these solutions work, there could be an issue with the spindle or bearings, which may require professional servicing. Remember, fixing a drill press wobble is not only important for accurate drilling, but also for safety.
Examining the Chuck
When it comes to examining the chuck, there are a few potential problems that could be causing issues. One common problem is the jaws not gripping tightly enough, which can cause the chuck to slip and make it difficult to use. This could be due to a worn chuck key or a need to clean the chuck surfaces.
Another issue could be a bent or damaged chuck, which can cause the drill bit to wobble and produce inaccurate holes. Additionally, a misaligned chuck can also cause similar problems, leading to frustration and wasted time. It’s important to carefully examine the chuck and diagnose any potential problems before attempting to use the drill, as this can save time and prevent errors.
So next time you’re having trouble with your drill, be sure to check the chuck for any potential issues.
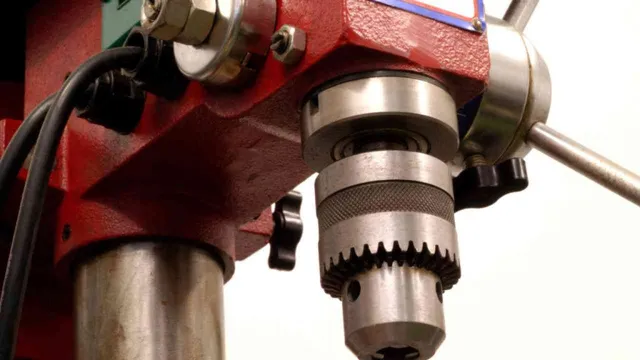
Checking the Spindle
When it comes to diagnosing problems with your spindle, there are a few key things to keep in mind. One of the first things to check is the condition of the spindle bearings. If the bearings are worn or damaged, it can cause the spindle to wobble or vibrate, leading to poor surface finish and accuracy.
Another important area to check is the spindle runout. Excessive runout can cause tool chatter and poor surface finish, as well as premature tool wear. If you notice any issues with spindle performance, it’s important to take action right away to avoid further damage.
By checking the spindle regularly and addressing any problems as soon as they arise, you can keep your machine running smoothly and ensure high-quality results.
Fixing the Wobble
If you’re experiencing wobbling on your drill press, it can be quite frustrating. Not only does it affect the accuracy of your drilling, but it can also be dangerous. Fortunately, there are a few things that you can do to fix the wobble.
The first thing you should check is the chuck. If it’s not properly tightened, it can cause the bit to slip and wobble. Make sure it’s firmly secured to the spindle before you start drilling.
If the chuck is tightened and the wobble persists, it could be due to an unlevel base. Check the levelness of your drill press and adjust the feet as needed to ensure it’s on a stable surface. If neither of these things solve the issue, you may need to replace the spindle or bearings.
It’s best to consult with a professional if you’re not comfortable doing this yourself. With a little effort, you can get your drill press running smoothly again.
Tightening the Chuck
Tightening the chuck on a drill is essential in ensuring precision and accuracy in your work. However, if you experience a wobble in the chuck, it can throw off your entire project. Don’t fret, though, as fixing the wobble is an easy fix.
First, remove the drill bit and check for any debris or buildup in the chuck. Clean it thoroughly with a clean cloth or compressed air. Next, tighten the jaws of the chuck by hand using a firm grip.
If the wobble persists, try tightening it further with a chuck key. If that still doesn’t work, it may be time to replace the chuck entirely. By taking the time to tighten your chuck properly, you’ll ensure that your drill bits stay secure and your projects are completed with precision.
Adjusting the Spindle Bearings
Spindle bearings in any machine are crucial components that bear the weight of the rotating parts and ensure proper alignment. However, over time, these bearings can wear out or become misaligned, causing a wobble in the spindle. This wobble can lead to poor performance and accuracy issues in the machine.
Adjusting the spindle bearings can solve this problem. To do this, you need to carefully disassemble the spindle, clean it thoroughly, and inspect the bearings. If they are worn out or damaged, they need to be replaced.
If they are still in good condition, you can adjust their position by loosening the locking nuts and adjusting the preload with a torque wrench. It’s important to use the manufacturer’s recommended preload specifications and to tighten the locking nuts evenly. This process may seem daunting, but with the right tools and instructions, you’ll have your machine running smoothly again in no time.
Balancing the Quill
balancing the quill Balancing the quill is an essential part of calligraphy and can make a huge difference in the quality of your writing. When the quill is not properly balanced, it can cause wobbling, leading to smudging and uneven lines. To fix this, there are a few things you can do.
First, make sure that the quill is properly prepared before use. Dip it in ink and then gently wipe off any excess to prevent dripping. Next, use a light touch when writing and focus on maintaining a consistent pressure.
Finally, adjust your grip on the quill, ensuring that it is not too tight or too loose. With practice, you can master the art of balancing the quill and produce beautiful calligraphy every time.
Preventing Future Wobble
If your drill press wobbles, it can be frustrating and even dangerous. But don’t worry, there are ways to prevent future wobble. First, make sure your drill press is level.
Use a level to check the base and table. You may also need to adjust the feet slightly to get it perfectly level. Next, check for any loose parts.
This could include the quill, chuck, or table. Make sure they are tightened securely. Another common cause of wobble is a dull drill bit.
Replace your bit if it is dull or worn. Finally, make sure you are using the correct speed for the type of material and drill bit you are using. By following these tips, you can prevent future wobble and ensure a safe and accurate drilling experience.
Maintaining the Chuck
When it comes to ensuring the quality and accuracy of your work, maintaining the chuck of your tool is crucial. One of the most common issues faced by professionals in this field is wobbling, which can cause significant delay and inconvenience. To avoid this, it is important to take preventive measures.
One such measure is to routinely inspect and clean the chuck. Any debris or dirt stuck in it can cause the wobble, so it is essential to keep it clean. Additionally, make sure to tighten it regularly so that it remains stable.
Another tip is to use a high-quality chuck key that fits perfectly into the chuck. Using a poor quality key can cause damage to the chuck, which can further lead to wobbling. Lastly, if you notice any signs of wear and tear, such as an unusual sound or difficulty in tightening, it is best to get it replaced immediately to prevent any further damage.
By taking these simple steps, you can ensure that your chuck stays in top-notch condition, and wobbling becomes a thing of the past.
Cleaning and Lubricating the Spindle
Cleaning and lubricating the spindle of your machine can greatly contribute to preventing any future wobbling issues. Over time, dust and debris can accumulate on the spindle and cause it to wear down, leading to imbalances and vibrations. To clean the spindle, use a soft cloth or brush with a mild cleaning solution and gently wipe down the surface.
Once it is clean, apply a small amount of lubricating oil to keep it running smoothly. Think of it as giving your machine a ‘spa day’- it will leave it feeling refreshed and ready to tackle any project you throw its way. Taking the time to properly maintain your machine will increase its longevity and create a more pleasant, efficient sewing experience.
So, give your machine the TLC it deserves and say goodbye to any unnecessary wobbling and shaking.
Conclusion
To fix a drill press wobble, one must approach the problem with a steady hand and a keen eye. It may seem daunting at first, but with a few simple steps and some persistence, you can re-align the spindle and eliminate that pesky wobble. So, don’t let the drill press wobble get you down – tackle it head-on and emerge victorious!”
FAQs
What are the common reasons for drill press wobble?
The common reasons for drill press wobble could be an uneven base, bent quill, spindle runout, or issues with the chuck.
Can a drill press wobble be fixed?
Yes, a drill press wobble can be fixed by ensuring an even and stable base, inspecting and replacing bent components, and balancing the chuck and spindle.
How do I check the spindle runout of my drill press?
To check the spindle runout of your drill press, use a dial indicator to measure the spindle while it rotates.
Can using dull drill bits cause a drill press to wobble?
Yes, using dull drill bits can cause the drill press to wobble as they are not sharp enough to cut through material and may cause the drill press to vibrate.
How do I maintain my drill press to prevent wobble?
To maintain your drill press and prevent wobbling, regularly inspect and clean all components, replace any damaged or worn parts, and ensure proper lubrication of moving parts.
Should I attempt to fix a wobbling drill press on my own?
It is recommended to seek professional help if you are unsure of how to fix a wobbling drill press, as attempting to fix it on your own could cause further damage to the machine or cause injury.
Can a wobbling drill press affect the accuracy of my drilling?
Yes, a wobbling drill press can affect the accuracy of your drilling and may cause holes to be drilled in the wrong location or at the wrong angle.