How to Fix Unloader Valve on Air Compressor: Step-by-Step Guide

If you’re the kind of person who likes to work on your own DIY projects or just enjoy fixing things around the house, you might have encountered an issue with your air compressor’s unloader valve. Although this can be an annoying problem to deal with, fixing an unloader valve on an air compressor is actually quite simple if you know what to look for. The unloader valve is a crucial component of an air compressor, responsible for releasing the pressure in the compressor when it shuts off.
Without an unloader valve, the compressor tank could rupture, causing a safety hazard. However, if the unloader valve is faulty, it can cause the compressor to struggle to start, make strange noises, or even shut off completely. Fixing the unloader valve on an air compressor can be as simple as making sure the valve is clean and freely moving, or it might require a replacement part.
Whatever the issue may be, don’t hesitate to take action, as a faulty unloader valve can cause more problems down the line. Plus, learning how to fix an unloader valve yourself can save you both time and money! Stay tuned for our step-by-step guide on fixing an unloader valve on an air compressor, including troubleshooting tips and advice for those new to DIY repair projects. We’ll show you how to get your compressor running smoothly again in no time!
Understanding the Unloader Valve
If you’re having trouble with your air compressor, one of the first things to check is the unloader valve. Essentially, the unloader valve is responsible for releasing air pressure from the compressor after it shuts off. Without this release, the compressor can face serious damage.
If you’re wondering how to fix the unloader valve on your air compressor, there are a few things to keep in mind. First, make sure to turn off the power and unplugged the compressor before attempting any repairs. Then, inspect the valve for any signs of damage or wear.
If it’s simply clogged, cleaning it may do the trick. If it’s beyond repair, replacing the valve is a relatively simple and inexpensive fix. Remember to always follow the manufacturer’s instructions and use caution when working with compressed air.
By knowing how to properly maintain and repair the unloader valve, you can ensure a longer lifespan for your air compressor and avoid costly repairs.
What is an Unloader Valve?
An unloader valve is a crucial component in a pressure washer that functions to regulate the pressure and relieve excess pressure when necessary. To put it simply, the unloader valve is responsible for diverting the flow of water back into the pump when the trigger on the pressure wash gun is released, allowing the pump to maintain a constant pressure level. This can save the pump from damage caused by over-pressurization and can also prevent the pressure washer from stalling out.
The unloader valve works by opening a bypass channel that directs the water back to the pump’s inlet side, thus reducing the pressure in the system. If you encounter low pressure problems on your pressure washer, the unloader valve could be one of the culprits. It requires a clean and unrestricted flow of water to function correctly.
Therefore, it’s essential to perform proper maintenance to ensure its optimal performance.
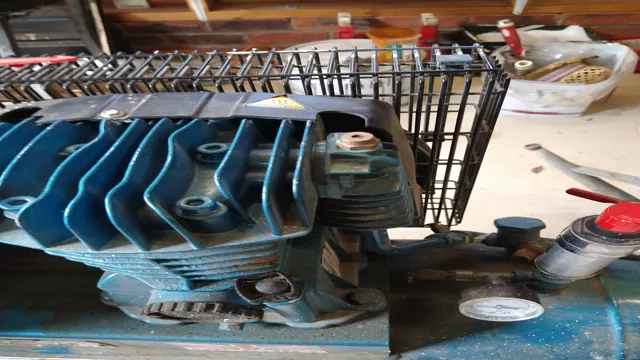
What Does an Unloader Valve Do?
An unloader valve is a critical component of any pressure washer system. Essentially, the unloader valve is a device that relieves pressure on the pump when it’s not in use, ensuring that the pump doesn’t get damaged and prolonging its lifespan. The unloader valve works by redirecting water to a bypass or recirculation loop when the trigger on the pressure washer gun is released.
This action reduces the pressure in the system, protecting the pump and extending its lifespan. The unloader valve is an essential safety feature that prevents the pressure in a pressure washer system from becoming too high, which can lead to dangerous situations. Overall, understanding the function and importance of the unloader valve is crucial for anyone who uses a pressure washer, from homeowners to professional cleaners.
Signs of a Faulty Unloader Valve
If you’re experiencing issues with your air compressor, such as low pressure or strange noises, it could be due to a faulty unloader valve. The unloader valve is responsible for releasing pressure from the compressor’s discharge pipe when the unit stops running. Signs that the unloader valve is malfunctioning include pressure still present after the compressor is turned off, air leaks around the valve, and high-pitched whistling noises.
Luckily, fixing the unloader valve on an air compressor is a relatively simple task. First, turn off the compressor and release all pressure. Next, locate the unloader valve and check for any damage or wear and tear.
If there is any damage, replace the valve with a new one. If there is no visible damage, clean the valve thoroughly with lubricant. Finally, test the compressor to ensure the unloader valve is functioning properly.
By following these steps, you can fix any issues with your compressor’s unloader valve and get it running smoothly again.
Air Leaking
Air leaking is a common problem that can occur in the air compressor system. It can cause a decrease in the pressure and power of the compressor, which can result in reduced efficiency and higher power consumption. One of the most frequent causes of air leaking is a faulty unloader valve.
This valve is designed to displace the air pressure that gets trapped in the compressor’s cylinder head after the motor is turned off. If the unloader valve is damaged or malfunctions, it can cause air to continue to leak out, even when the compressor is not being used. Some of the signs that your unloader valve may be faulty include hissing or sputtering sounds after turning off the compressor, the compressor failing to restart after being turned off, and low pressure on the gauge.
If you notice any of these symptoms, it’s advisable to get your compressor checked by a professional to avoid any further damage.
High Pressure Build Up
If you’re experiencing high pressure build-up in your pressure washer, it’s likely due to a faulty unloader valve. This important component is responsible for regulating the flow of water in your machine, and if it’s not functioning correctly, it can cause serious problems. One of the most common signs of a faulty unloader valve is when the pressure builds up to a level that is too high for your machine to handle.
This can lead to leaks and even damage to your pressure washer. Other signs of a problem include difficulty starting the engine and a decrease in the amount of pressure being produced. It’s important to address any issues with your pressure washer promptly, as they can quickly escalate into more serious problems.
If you’re not sure how to fix the problem, it’s best to consult a professional who can diagnose the issue and offer a solution. By addressing problems with your pressure washer early on, you can avoid costly repairs and ensure that your machine lasts for many years to come. So don’t wait – take action today to keep your pressure washer running smoothly and safely.
Compressor Stalling
Compressor stalling is a common issue that arises when the unloader valve is not functioning properly. There are a few signs that indicate the unloader valve may be faulty. One such sign is that the compressor may have trouble starting up or may take longer than usual to reach full pressure.
Another sign is that the compressor may experience stalling, which occurs when the motor stops turning even though the compressor is still running. This can lead to reduced efficiency and increased wear and tear on the machine. If you suspect your compressor may be experiencing these issues, it’s essential to have it checked out by a professional.
A faulty unloader valve can be replaced relatively easily and inexpensively, preventing further damage and ensuring that your compressor runs smoothly. So, it’s better to fix this issue as soon as possible to save money, time, and stress.
Steps to Fix an Unloader Valve
If you’re experiencing issues with your air compressor’s performance, it could be due to a faulty unloader valve. This small component plays a crucial role in regulating the pressure in your compressor to prevent damage to your system. Luckily, fixing an unloader valve is relatively simple and can save you from costly repairs or replacements down the line.
Firstly, you should locate the unloader valve on your compressor, which will typically be attached to the pressure switch. From there, you can begin examining the valve for any visible damage or debris buildup. If there is debris, you can try cleaning it with compressed air or a special cleaning solution.
If the valve is damaged, you may need to purchase a replacement and follow the manufacturer’s instructions for installation. Once your new valve is in place, test your compressor to ensure that the pressure levels are functioning correctly. Don’t let a faulty unloader valve put a halt to your future DIY projects or work tasks.
With a bit of effort and know-how, you can take care of this repair on your own and get back to business as usual.
Step 1: Shut Down the Compressor
If you’ve noticed your compressor is struggling to turn on, or it’s running but not producing the air pressure it once did, it could be the unloader valve causing the issue. Luckily, fixing this problem is relatively simple if you follow these steps. First and foremost, you’ll need to shut off the compressor and unplug it.
Next, locate the pressure switch and remove the cover to access the unloader valve. Inspect the valve for any debris or damage, and if necessary, clean or replace it. Additionally, check the tubing and fittings to ensure they’re not clogged or leaking.
Once you’ve made any necessary repairs or replacements, reassemble the pressure switch and start up the compressor to see if it’s working properly again. By taking the time to fix the unloader valve, you can avoid costly repairs and potentially dangerous situations down the line.
Step 2: Check for Air Leaks
Checking for air leaks is a critical step in fixing an unloader valve. Any leaks in the system can lead to a drop in pressure, which can cause the valve to malfunction. To check for leaks, you’ll need to close off all of the other outlets in the system and engage the unloader valve.
Then, listen for any hissing sounds or feel for any air escaping around the valve or gasket. If you do detect a leak, pinpoint the source and tighten any loose connections or replace any damaged parts. Remember, a small leak can quickly turn into a big problem, so it’s essential to nip it in the bud as soon as possible.
By taking the time to check for air leaks, you can ensure that your unloader valve operates at its best and keeps your compressor running smoothly.
Step 3: Remove the Unloader Valve
Moving along with the steps to fix an unloader valve, the next thing that needs to be done is to remove the unloader valve. This is a crucial step but it is not something that should cause too much worry. Start by locating the unloader valve which is normally located on top of the pressure washer or the pressure regulator.
This is the valve that helps to regulate the pressure inside the pump and it is usually held in place by a screw or a bolt. Once you have located the valve, carefully unscrew or unbolt it and gently lift it out of its housing. Ensure to keep the valve and all its components safely aside and inspect its condition to determine if it needs to be replaced entirely or if it is fixable.
Removing the unloader valve is an important step towards fixing it, so take your time to do it carefully so as not to cause any damage that could lead to further problems.
Step 4: Inspect the Valve for Damage
One important step in fixing an unloader valve is to inspect it thoroughly for any signs of damage. This can include cracks, wear and tear, or any other issues that may prevent the valve from functioning properly. It’s important to make sure the valve is completely clean and free of debris before inspecting it, as this can sometimes mask any potential problems.
If there are any visible signs of damage, it may be necessary to replace the valve entirely. However, if the valve appears to be in good condition, it’s important to continue with the next steps in the process to determine the root cause of the issue with the unloader valve. Regardless, taking the time to inspect the valve carefully can help ensure that any necessary repairs are completed correctly and prevent future problems from occurring.
Step 5: Replace or Clean the Valve
When dealing with an unloader valve that just won’t budge, it may be time to consider replacing or cleaning the valve altogether. This can be a daunting task for those who aren’t well-versed in the world of valves, but fear not, as it’s not as difficult as it may seem. First, turn off the air compressor and release any excess pressure that may be stored within it.
Next, remove the unloader valve from the compressor and inspect it for any signs of damage or wear and tear. If it looks worn out, it’s time to replace it with a brand new one. If it looks to be in decent shape, it may simply require a good cleaning.
To clean the valve, use a cleaning solution and a soft-bristled brush to scrub away any debris or buildup that may be hindering its performance. Once cleaned, reinstall the valve and turn the compressor back on to ensure that it’s functioning as it should. By replacing or cleaning the valve, you can ensure that your air compressor runs smoothly and efficiently for years to come.
Step 6: Reinstall the Valve
Now that you’ve cleaned and checked the unloader valve, it’s time to reinstall it. Before you do that, make sure you inspect the valve and its components for any damage or wear and tear. If everything looks good, apply some thread seal tape on the threads of the valve and screw it back into its position.
Make sure you don’t overtighten it as it may cause damage. Once the valve is secured, reconnect any hoses or other components you may have removed for access. After that, test your pressure washer to see if the unloader valve is properly working.
If you’re still experiencing problems, you may need to seek professional help. In any case, regular maintenance and cleaning of your pressure washer’s unloader valve will ensure its longevity and optimal performance.
Step 7: Test the Compressor
If you’re dealing with an unloader valve issue on your compressor, the last step in the process is testing the compressor to ensure it’s functioning properly. Begin by making sure the tank is properly pressurized before turning on the compressor. Next, start the compressor and allow it to run until it reaches maximum pressure.
Once it does, turn off the machine and disconnect it from the power source. From here, release any remaining air pressure from the tank and locate the unloader valve. Once found, test it by pushing in the pin and verifying that air is released.
If the air is not escaping, the valve may require replacement or further inspection. By following these simple steps and testing your compressor properly, you can ensure that your system is functioning correctly and safely.
Preventing Future Issues with the Unloader Valve
If you’re experiencing issues with your air compressor’s unloader valve, don’t fret. There are a few things you can do to fix it yourself! First, check the pressure switch to make sure it’s functioning properly. If it’s not, that could be the root of your issue.
Next, inspect the valve itself for any damage or blockages. If it’s damaged, you’ll need to replace it. You’ll also want to clean the valve thoroughly and ensure it’s properly lubricated.
Once you’ve fixed your unloader valve, there are a few things you can do to prevent future issues. Regularly cleaning and lubricating the valve is crucial, and be sure to check for any worn or damaged parts that may need replacing. With a little bit of regular maintenance, you should be able to keep your air compressor’s unloader valve running smoothly for years to come.
Regular Maintenance
Regular maintenance is crucial for the proper functioning of any machine, especially the air compressor. One of the essential parts of this device is the unloader valve, which plays a vital role in reducing the starting load of the compressor motor. Regular maintenance of the unloader valve can prevent future issues, extending the life of the machine.
Some common problems that may occur with the unloader valve include leaking, dirt accumulation, and rusting. However, these problems can be avoided by conducting regular maintenance checks such as cleaning the valve and lubricating its moving parts. Neglecting regular maintenance can result in expensive repairs and even complete machine breakdowns.
Therefore, it is essential to schedule preventative maintenance to keep the unloader valve and the air compressor in top condition.
Avoid Overloading the Compressor
When it comes to maintaining your compressor system, it’s essential to avoid overloading the compressor. Overloading can put undue stress on the system and lead to future issues, including problems with the unloader valve. This valve is responsible for releasing pressure from the compressor head when it shuts off, preventing a buildup of air in the pump.
However, when the system is overloaded, the valve may not work as intended, leading to issues with the compressor’s functionality. To prevent future issues with the unloader valve, it’s crucial to ensure that you’re not overloading your compressor. Make sure that you’re aware of the system’s capacity and don’t exceed it, and that you’re performing regular maintenance to keep the system running smoothly.
By taking these steps, you can avoid potential problems with the unloader valve and ensure that your compressor system is working as it should.
Conclusion
In conclusion, fixing the unloader valve on your air compressor is a breeze. With the right tools and a bit of know-how, you can put the power back in your compressor’s proverbial sails. Just like a skilled mechanic or a seasoned sailor, a little bit of elbow grease and some sound troubleshooting skills will go a long way in overcoming any obstacle.
So, grab your wrenches, tighten those connections, and get your air compressor back up and running like a well-oiled machine. You’ll be the envy of all your DIY friends and neighbors – and you’ll have saved yourself a bundle in repair costs to boot!”
FAQs
What is an unloader valve on an air compressor?
An unloader valve is a safety mechanism that releases pressure from the compressor head when it shuts off.
Why do I need to fix my unloader valve?
If the unloader valve is not functioning properly, it can cause unnecessary wear and tear on the compressor and can lead to decreased performance.
How do I know if my unloader valve needs to be fixed?
signs that your unloader valve needs to be fixed include excessive noise during operation, decreased performance, and visible damage to the valve itself.
Can I fix my unloader valve myself?
Yes, you can fix your unloader valve yourself if you have experience with air compressors and the necessary tools for the job.
What tools are needed to fix an unloader valve on an air compressor?
The tools needed to fix an unloader valve on an air compressor typically include a wrench set, a screwdriver set, and a replacement unloader valve.
How long does it take to fix an unloader valve on an air compressor?
The time required to fix an unloader valve on an air compressor varies depending on the severity of the issue and the level of experience of the person performing the repair.
Are there any safety precautions I should take when fixing an unloader valve on an air compressor?
Yes, always wear safety goggles and ear protection when working on an air compressor, and be sure to disconnect the power source before beginning any repairs.