How to Grease a Hammer Drill: Step-by-Step Guide for Proper Maintenance
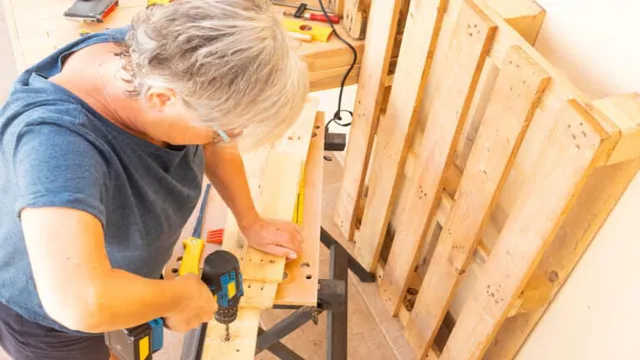
If you own a hammer drill, then you probably know that it needs regular maintenance to keep running smoothly. Greasing your hammer drill is an important part of that maintenance, but it can be confusing if you’ve never done it before. Fortunately, it’s not too difficult once you know what you’re doing.
In this blog post, we’ll walk you through the steps of how to grease a hammer drill, so you can keep it running at peak performance. Whether you’re a seasoned DIYer or a novice, we’ve got you covered with this essential guide. So, let’s get started!
Introduction
If you own a hammer drill, then you already know how essential it is to keep it in good working condition. Regular maintenance is key, and one crucial aspect of maintaining your hammer drill is keeping it properly lubricated. One way to achieve this is by greasing it regularly.
Before you begin, make sure you have the right type of grease. Ideally, you should opt for a high-temperature, lithium-based grease. Once you have your grease, unplug the drill and remove any excess debris from the chuck.
Then, remove the gear casing from the drill and apply grease to the teeth of the gears. Don’t forget to replace any worn-out parts or bearings before reassembling everything. Finally, inspect the chuck and apply a small amount of grease to its threads, ensuring that they are well lubricated.
Your hammer drill is now ready for action!
Why Grease a Hammer Drill?
hammer drill, grease Introduction: A hammer drill is a powerful tool that can drill through hard materials like concrete and masonry with ease. However, overuse or lack of proper maintenance can cause it to break down or become less efficient. One way to prevent this is by greasing the hammer drill regularly.
In this blog, we’ll explore the reasons why it’s important to grease a hammer drill and how you can do it yourself without any hassle. Why is it important to grease a hammer drill? The main reason to grease a hammer drill is to protect its internal components from wear and tear. When you use a hammer drill, the high-speed motion of the drill bit creates a lot of friction, generating heat that can damage the bearings and gears inside the tool.
Greasing the hammer drill helps to lubricate these moving parts and reduce the friction, which minimizes wear and tear and prolongs the life of the tool. In addition to protecting the tool’s internal components, greasing also helps to maintain the hammer drill’s performance. A poorly greased tool can cause the motor to overheat and slow down, reducing the drilling speed and overall efficiency.
By greasing the tool regularly, you can ensure that it operates at peak performance and gets the job done quickly and efficiently. How do you grease a hammer drill? To grease a hammer drill, you’ll need to follow a few simple steps. First, make sure the tool is unplugged and the chuck is empty.
Next, locate the grease fitting on the tool. This is usually located near the chuck or on the handle. If you’re not sure where it is, consult the tool’s manual or contact the manufacturer.
Once you’ve located the grease fitting, insert the nozzle of the grease gun into the fitting and pump the grease into the tool. Be careful not to over-grease the tool, as this can cause excess grease to leak out and create a mess. After you’ve greased the tool, wipe away any excess grease with a clean cloth.
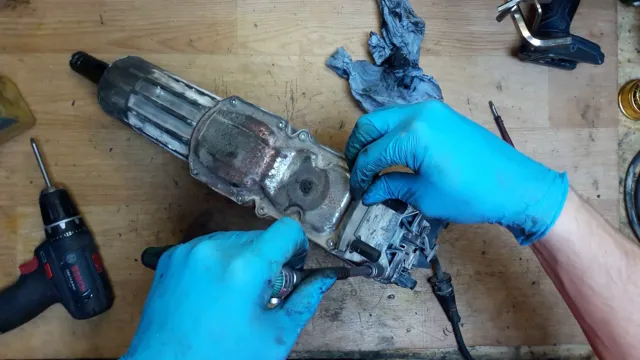
Preparation
If you have a hammer drill that has been in use for a while, it is important to know how to properly grease it in order to maintain it. The first step in preparing to grease your hammer drill is to gather all the necessary materials. You will need to have access to a small grease gun, some general-purpose grease, a paper towel, and a clean workspace.
Once you have these materials in place, you can start preparing your drill by wiping any excess dirt or debris from its exterior using a paper towel. Next, locate the grease fittings on your drill. These fittings usually look like small metal nipples located on different parts of the drill body.
Once you have identified them, use your grease gun to slowly add the general-purpose grease. It is important to be slow and steady in applying the grease, as over-applying it may cause damage to the drill in the long run. After applying the grease, simply wipe away any excess with your paper towel and your drill is ready to go.
Overall, preparing to grease your hammer drill is a simple process that involves gathering the necessary materials, cleaning the drill body, and slowly applying the proper amount of general-purpose grease using a small grease gun. With the right preparation and care, maintaining your hammer drill can be a straightforward task that will help ensure its longevity.
What You Will Need
When it comes to preparing for a specific task or project, having the right tools and resources is essential. The same goes for creating your blog, as there are certain things you will need to have in place before you start writing. Firstly, you will need access to a computer or laptop with an internet connection.
This will enable you to research and gather information for your blog posts, as well as upload and publish them. Additionally, you will need to choose a blogging platform, such as WordPress or Blogger, to host your blog. These platforms offer a range of features and tools to help you customize your blog and make it visually appealing.
Once you have the basic setup in place, you will also need to consider things like your blog’s design, audience, and content strategy. These all play an important role in helping you create engaging and compelling blog posts that resonate with your readers. So, take the time to plan and prepare before you start writing to ensure that your blog is off to the best possible start.
Things to Consider Before Greasing
Before greasing any machinery or equipment, there are a few things you need to consider to ensure that the process is done smoothly and effectively. The first thing to do is to prepare the surface that needs greasing. Wipe off any dust or debris on the surface that could hinder the application of the grease.
You can use a clean cloth or air compressor to blow off any dirt or debris. Also, make sure to have the right type of grease and the right amount. Using the wrong type of grease may cause damage to your equipment, while using too much or too little grease may lead to inefficiency or even failure of your machinery.
Take the time to read your equipment manufacturer’s guidelines or consult an expert if you are unsure about the amount and type of grease needed. By preparing adequately, you can save time and money in the long run and ensure that your equipment runs smoothly for longer periods.
Step-by-Step Guide
If you want your hammer drill to last a long time and keep running smoothly, it’s important to grease it regularly. To get started, you’ll need to gather some supplies: a tube of lithium grease, a clean rag, and a disposable glove. First, make sure the drill is unplugged and the bit is removed.
Next, take the rag and wipe away any dust or debris from the exterior of the drill. Then, put on the glove and apply a small amount of lithium grease to the drill’s chuck (the part that holds the bit). Rotate the chuck several times to evenly distribute the grease.
Finally, apply a small amount of grease to the drill’s gearbox (the part where the motor is housed) through the grease fitting. Once you’ve finished greasing, wipe away any excess grease with the rag and reattach the bit. Your hammer drill should now be well lubricated and ready to use for your next project!
Step 1: Remove the Grease Gun Nozzle
Removing the grease gun nozzle may sound like a complicated task, but it is actually quite simple. The first step is to unscrew the nozzle from the end of the grease gun. This can be easily done by turning the nozzle counterclockwise until it comes loose.
Depending on the model of your grease gun, you may need to use a wrench to help unscrew the nozzle. It is important to make sure that the grease gun is not pressurized before removing the nozzle. You can do this by releasing any pressure in the gun by depressing the priming lever or releasing the pressure valve.
Once the nozzle is removed, you can clean it thoroughly to ensure maximum performance. Regularly cleaning and maintaining the grease gun nozzle will help prolong its lifespan and ensure optimal performance every time you use it.
Step 2: Clean the Drill
Once you’ve finished drilling, it’s crucial to clean your drill properly. Not only will this keep your tool in tip-top shape, but it can also prevent any potential hazards or malfunction from occurring. The first step is to unplug your drill from the power source or remove the battery.
Next, use a dry cloth or brush to remove any debris or dust from the surface and crevices of the drill. You can also use compressed air to blow out any stubborn particles. If there’s any excessive dirt or grease buildup, you can dampen the cloth with a mild soap and water solution, but make sure to dry it thoroughly afterwards to prevent rusting.
Lastly, check the chuck mechanism and make sure it’s tightened properly to avoid any injury or damage during your next use. Remember, a clean drill is a safe drill.
Step 3: Apply Grease
Now that you have cleaned all the old grease from your machinery, it’s time to apply the new grease. Applying grease can be a messy job, so it’s important to take caution and wear protective gear such as gloves or goggles. Here’s a step-by-step guide on how to apply grease like a pro: Step 1: Choose the right grease – Make sure the grease you are applying is compatible with your machinery.
Check the manufacturer’s recommendations or consult an expert to find the most suitable one. Step 2: Apply a thin layer – Too much grease can cause friction and create more problems. Apply a thin, even layer of grease on the moving parts.
You can use a brush or a grease applicator tool for this. Step 3: Cover all the critical points – Pay close attention to the areas that need the most protection and lubrication. Make sure you cover all the crucial points and joints.
Step 4: Replace the parts – After applying the grease, reassemble the parts and make sure they are tightened properly. By following these simple steps, you can keep your machinery in good condition and extend its lifespan. Remember, regular maintenance and lubrication are crucial for the smooth operation of your equipment.
So, don’t neglect it and keep your machinery running like new!
Step 4: Reattach the Grease Gun Nozzle
In the final step of using a grease gun, it’s time to reattach the nozzle. This may seem like a straightforward process, but it’s essential to take your time and make sure it’s done correctly. First, double-check that the nozzle threads are clean and free from debris.
Then, insert the nozzle into the tip of the grease gun and turn it clockwise until it’s snug. It’s essential not to over-tighten, or you could damage the threads. Once the nozzle is firmly in place, give it a quick test squeeze to ensure that grease is flowing as it should.
With that, your grease gun is ready to be stored until its next use! Keyword: grease gun nozzle
Maintenance Tips
If you want your hammer drill to last for years and perform like new, you need to make sure it’s properly maintained. One essential maintenance task that you should perform regularly is greasing the drill. In order to keep your hammer drill moving smoothly, you will need to disassemble it and apply a thin layer of grease to all the moving parts.
To get started with this process, first, turn off your drill and unplug it from the power source. Then, remove the chuck and the drill bit, and clean off any debris or dirt from the drill’s housing. Once the drill is clean, apply a small amount of grease to the moving parts, including the gears, bearings, and bushings.
You can use a small brush or a Q-tip to apply the grease. Finally, reassemble the drill, making sure that all the parts are securely in place. By performing this routine maintenance task on your hammer drill, you’ll be ensuring that it stays in excellent working condition and stays functional for years to come.
How Often to Grease
When it comes to maintaining machinery, one important aspect to consider is how often to grease. Greasing your equipment regularly is crucial to ensure its longevity and optimum performance. The frequency with which you should grease depends on various factors, such as the type of machinery, the environmental conditions it operates in, and the frequency of use.
Most manufacturers provide a recommended greasing schedule in their equipment manual, which can be used as a guideline. It’s also important to inspect the machinery regularly for wear and tear, as this can impact the greasing schedule. Remember, neglecting to grease your equipment regularly can lead to costly repairs and even downtime, so it’s always better to err on the side of caution.
By keeping up with a proper maintenance schedule, you can extend the life of your machinery and ensure that it operates smoothly for years to come.
Signs of Over-Greasing
Over-greasing is a common problem that can lead to serious issues with machinery. It’s important to keep an eye out for signs of over-greasing so that you can address the problem before it’s too late. One of the most obvious signs of over-greasing is excess grease buildup around the bearing housing or other lubrication points.
This can lead to a buildup of heat and cause the bearing to fail prematurely. Another sign is if the machine is using too much grease compared to the recommended amount. Over-greasing can also cause the seals to fail, allowing dirt and other contaminants to enter the system.
To prevent over-greasing, ensure that the appropriate amount of grease is used and that lubrication intervals are followed. It’s essential to conduct regular checks to ensure that everything is running smoothly. By addressing over-greasing, you can prolong the life of your machinery and save the hassle of unexpected repairs or replacements in the future.
Conclusion
In conclusion, greasing a hammer drill is just like taking care of your car’s engine. You wouldn’t leave your car without an oil change, so why leave your drill without grease? By investing a small amount of time in greasing your hammer drill, you’ll prolong its lifespan and make it work smoother than ever. So grab that grease gun, suit up like a mechanic, and go give your hammer drill the maintenance it deserves.
Who knows, you might even impress your DIY-loving friends with your newfound knowledge on how to grease a hammer drill.”
FAQs
What is meant by greasing a hammer drill?
Greasing a hammer drill involves applying lubrication to the moving parts of the drill to ensure smooth function and prevent wear and tear.
How frequently should I grease my hammer drill?
It is recommended to grease your hammer drill after every 30-40 hours of use or as per manufacturer’s instructions.
What type of lubricant should I use for my hammer drill?
It is best to use a high-temperature lithium grease or heavy-duty grease that is specifically designed for high-powered tools like hammer drills.
Can I use regular motor oil for greasing my hammer drill?
No, it is not recommended to use regular motor oil for greasing your hammer drill as it may not provide adequate protection and lead to breakdown of the tool.
How do I grease the chuck of my hammer drill?
To grease the chuck, remove any drill bit or accessory and apply a small amount of grease to the inside of the chuck. Then, close and open the chuck repeatedly to distribute the grease evenly.
Is it okay to over-grease my hammer drill?
No, it is not recommended to over-grease your hammer drill as it can cause clogging and lead to damage of the tool. Apply only the recommended amount of grease.
What happens if I don’t grease my hammer drill?
If you don’t grease your hammer drill, the moving parts may wear out quickly, leading to decreased efficiency, increased energy consumption, and potential breakdown of the tool.