How to Inspect Air Compressor Tank: Tips and Tricks for Ensuring Its Safety and Efficiency
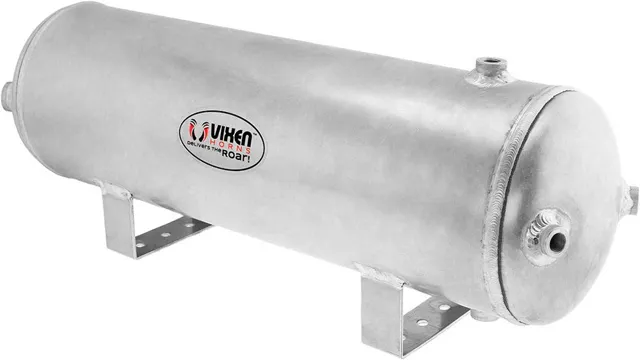
Are you looking to purchase or inspect an air compressor tank? Whether you’re a beginner or seasoned professional, it’s important to know what to look for when it comes to ensuring your safety and the tank’s longevity. A faulty air compressor tank can not only be dangerous, but costly to repair or replace. In this blog, we’ll take a deep dive into the world of air compressor tank inspections.
We’ll cover key points to be aware of, such as tank material, leakage, and corrosion. By the end of this blog, you’ll have a better understanding of what it takes to properly inspect an air compressor tank, and how to keep it running smoothly. So, let’s get started!
Gather Necessary Tools and Safety Gear
If you’re planning to inspect an air compressor tank, you’ll need to gather a few necessary tools and safety gear first. The tools you’ll need may vary depending on the type of air compressor tank you have, but typically, you’ll need a flashlight, a pressure gauge, and a moisture meter. You’ll also want to wear eye protection and gloves to keep your hands safe.
Before you start inspecting the tank, make sure to turn off the power and release any air pressure. Safety should always be your top priority. Once you have all your tools and safety gear, you can start your inspection.
Look for any signs of rust or corrosion on the tank’s exterior. If you notice any damage, take note of it and check the interior of the tank for signs of damage as well. Use your pressure gauge to check the pressure in the tank and your moisture meter to check for any excess moisture that could lead to corrosion.
By taking these steps and inspecting your air compressor tank regularly, you can ensure safe and efficient operation.
Examples: flashlight, safety glasses, gloves
When it comes to any project, it’s essential to gather the necessary tools and safety gear before diving in. These can include anything from a simple flashlight to more specialized equipment like safety glasses and gloves. By having the right gear on hand, you’re not only protecting yourself but also ensuring that the job will be done efficiently and effectively.
Think of it like being a superhero with their trusty tools and gadgets at their side. Without them, they wouldn’t be able to save the day! So whether you’re tackling a DIY home improvement project or working on a construction site, always be sure to gather the tools and safety gear needed before starting. Trust us, your fingers and eyes will thank you!
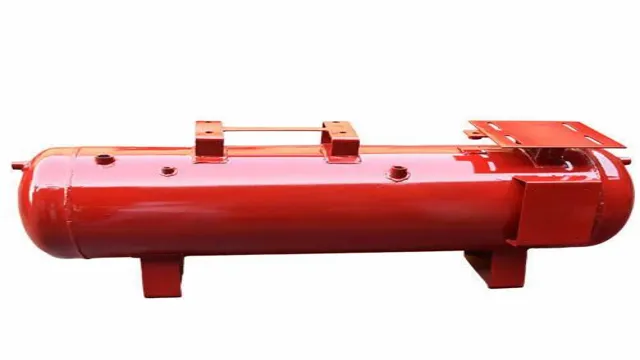
Check for Any Visible Damage
When inspecting an air compressor tank, it’s crucial to check for any visible damage that may compromise the tank’s efficiency and safety. Look for signs of rust, corrosion, or dents that may create weak spots in the tank, resulting in leaks or even a rupture. If there’s rust present, gently scrape it off and check the metal beneath it for any holes or perforations.
In case you discover any dents, ensure they’re not near any welds or seams, as these areas are susceptible to cracking from impact. It’s also wise to examine all the fittings, hoses, and connections for any looseness, wear, or cracks. Any damaged components should be replaced immediately to ensure safe, efficient operation.
By carefully inspecting your air compressor tank for any visible damage, you can detect potential problems early on before they become critical issues and keep your compressor running at optimum performance.
Examples: dents, rust, cracks
When it comes to buying a used car, you need to be extra vigilant and check for any visible damage. This includes dents, rust, and cracks that might affect the car’s performance or compromise your safety on the road. Don’t be fooled by a shiny exterior or a clean interior; these could easily mask more serious issues that could cost you time and money down the line.
Take your time and inspect the car thoroughly, from the roof to the tires, and don’t be afraid to ask the seller for more information or documentation. A dent might seem like a minor problem, but it could indicate a more significant issue with the car’s frame or suspension. Rust is another red flag, especially if it’s spreading or affecting crucial parts of the car such as the brakes or exhaust system.
Cracks in the windshield or windows can also pose a safety hazard, as they can affect your visibility and increase the risk of accidents. To avoid any nasty surprises, it’s best to bring along a trusted mechanic or car expert who can give you an unbiased assessment of the car’s condition. You can also do some research online and check the car’s history and maintenance records to spot any patterns or signs of neglect.
Remember, a used car might have some wear and tear, but it should still be roadworthy and safe to drive. In conclusion, when buying a used car, always check for any visible damage such as dents, rust, and cracks. Don’t overlook these signs, as they could indicate more serious issues that could compromise your safety or cost you money in repairs.
Take your time, inspect the car thoroughly, and don’t be afraid to ask for help or advice from experts. By being diligent and careful, you can find a reliable and affordable used car that serves your needs and lasts for years to come.
Inspect the Drain Valve
Inspecting the drain valve on your air compressor tank is an essential aspect of maintenance that you shouldn’t neglect. The drain valve is responsible for expelling moisture and other contaminants from the tank, preventing rust and corrosion from forming. To inspect the drain valve, turn off your compressor and release the pressure from the tank.
Locate the drain valve and check for any visible damage or wear. Look for cracks, leaks, or rust on the valve and ensure that it’s tightly secured. If you notice any issues with the valve, replace it immediately to prevent any potential hazards.
Checking the drain valve is a quick and easy task that can save you from costly repairs down the line and ensure your compressor runs efficiently. So, make sure to include it in your regular maintenance routine to keep your air compressor tank in top condition.
Examples: check for leaks, check for proper functioning
When it comes to inspecting your water heater, one essential part to check is the drain valve. The drain valve is a small, brass or plastic valve located near the bottom of your water heater, and it’s responsible for draining the tank for maintenance or repair. To inspect the drain valve, turn off the power supply and the cold-water supply valve before opening the valve with a bucket or container underneath to catch the water.
Check for any leaks around the valve or on the threads connecting it to the water heater. If you notice any leaks, try to tighten the valve with a wrench or pliers, and if it still leaks, replace it as soon as possible. Additionally, make sure the valve is opening and closing properly by turning it to the on and off position a couple of times.
If it’s difficult to turn, you may need to lubricate the valve or replace it altogether. Checking the drain valve is a simple but crucial step in ensuring the proper functioning of your water heater, and it can save you from costly repairs in the future.
Check the Pressure Relief Valve
One important aspect of inspecting an air compressor tank is checking the pressure relief valve. This valve serves as a safety mechanism that releases pressure from the tank if it reaches a dangerous level. To test the valve, turn off the compressor and disconnect any power sources.
Then, pull the ring on the valve to release some of the air from the tank. If the valve doesn’t release any air, it may be clogged or damaged and needs to be replaced to ensure proper safety measures. Be sure to check this valve regularly to prevent any unwanted accidents or equipment damage.
Remember, proper maintenance and inspection can save you time, money, and avoid potential hazards in the future. So, make sure you keep your air compressor tank in tip-top shape for optimal performance and safety.
Examples: ensure it releases excess pressure, check for leaks
As responsible owners of pressurized systems, it’s important that we regularly check the pressure relief valve to prevent any catastrophic accidents. This safety valve, often seen at the top of your tank or vessel, is designed to release excess pressure and prevent over-pressurizing of your system. It essentially acts as a safety net against any potential damages, making it crucial to ensure that it’s in good condition.
A common problem that arises is when the valve gets rusted or clogged, preventing it from functioning effectively. To avoid this, we recommend that you regularly test the valve’s mechanism to check if it opens and closes properly. You should also ensure that there are no leaks or damages on the valve that may cause it to malfunction.
After all, it’s always better to be safe than sorry. So, make sure to maintain your system’s pressure relief valve and keep your safety a top priority!
Examine the Tank’s Fittings and Connections
When inspecting an air compressor tank, it’s important to pay close attention to the fittings and connections. These parts can wear out over time, becoming loose or corroded. If left unchecked, this can lead to air leaks, which can be dangerous and reduce the overall efficiency of your compressor.
Start by checking the bolts and screws that hold the fittings and connections in place. If they are loose, tighten them up. If they are rusted or damaged, replace them.
It’s also important to inspect any hoses or tubes connected to the tank, making sure they are securely attached and free of cracks or tears. Don’t forget to check the pressure relief valve, which is designed to release pressure during an emergency. Make sure it’s functioning properly and replace it if necessary.
Keeping an eye on your tank’s fittings and connections will help keep your compressor running smoothly and safely.
Examples: check for leaks, tightness, and corrosion
When examining a tank, it’s crucial to check all fittings and connections. Any leaks in these areas can be harmful to the environment, not to mention costly in terms of lost resources and potential fines. Tightness is also essential, as loose fittings can lead to leaks or even explosions.
Additionally, corrosion can cause fittings to weaken and break, which can be incredibly dangerous. Performing regular inspections and maintenance on the tank’s fittings and connections is crucial to avoid problems down the line. A well-maintained tank not only keeps you in compliance with regulations but also helps ensure the safety of everyone involved.
So don’t forget to give those connections and fittings a thorough check!
Look for Signs of Moisture in the Tank
When inspecting an air compressor tank, one important thing to look out for is any signs of moisture. This can be a sign of a leak or condensation inside the tank. Moisture can cause corrosion and weaken the tank’s structure, leading to a potential safety hazard.
You can check for moisture by looking for any rust or white powdery substance on the tank’s exterior. Another method is to drain the tank and check for any water or contaminants that may have collected at the bottom. If you do find moisture, it’s important to address the issue immediately and repair any leaks or properly drain the tank to prevent further issues.
By regularly inspecting your air compressor tank, you can help ensure safe and efficient operation of your equipment.
Examples: rust, water in drain valve
If you want to ensure the longevity of your hot water tank, then it’s important to keep an eye out for signs of moisture. Moisture can lead to various problems, such as rust and corrosion. One example of moisture build-up is rust, which can occur when the tank is exposed to leaks or condensation.
This rust can leave dark stains on the outside of the tank and can eventually corrode the metal, causing it to weaken and fail. To prevent rust from forming, it’s essential to keep your hot water tank dry and check for leaks or other sources of moisture. Another issue that can arise is water in the drain valve.
This can lead to a build-up of sediment which can lead to clogs. In both cases, fixing the issue as soon as possible is crucial to avoid further complications. By regularly checking your hot water tank for signs of moisture, you can help extend its longevity and avoid costly repairs.
Perform a Hydrostatic Test (if necessary)
When inspecting your air compressor tank, it’s essential to perform a hydrostatic test to ensure it’s safe to operate. This test involves filling the tank with water and pressurizing it to a level higher than its maximum working pressure. During the test, you’ll need to inspect the tank for any leaks or signs of weakness, such as bulges or cracks.
If the tank passes the test, it’s considered safe to use. However, if it fails, you’ll need to replace the tank immediately as it’s a safety hazard. Keep in mind that it’s crucial to follow safety protocols and guidelines when performing this test, as it involves high levels of pressure and can be dangerous if not done correctly.
By performing a hydrostatic test, you can ensure that your air compressor tank is in good condition, reducing the risk of accidents and prolonging its lifespan.
Examples: check manual for recommended frequency and procedures
Performing a hydrostatic test is an important step in ensuring your equipment is safe and functioning properly, especially if it has been exposed to harsh conditions or has not been used for an extended period of time. It involves filling the equipment with water and pressurizing it to a level above its operating pressure in order to check for leaks or structural weakness. It is important to consult your equipment manual for recommended frequency and procedures for this test.
For example, some equipment may require a hydrostatic test to be done annually, while others may only require it every few years. Following the recommended procedures and frequencies can help prevent accidents and ensure the longevity of your equipment. So don’t skip this important step, perform a hydrostatic test if necessary to keep your equipment in top working condition.
Conclusion
Inspecting an air compressor tank may seem like a daunting task, but with a little knowledge and attention to detail, you’ll be able to spot any potential issues before they start to cause problems. So, grab a flashlight, give your tank a once-over, and remember, a stitch in time saves nine..
.or in this case, it prevents a busted tank from leaving you high and dry.”
FAQs
What are the signs of a damaged air compressor tank?
Signs of a damaged air compressor tank include visible cracks, excessive rust or corrosion, and leaks around fittings or welds.
How much pressure can an air compressor tank hold?
The pressure rating of an air compressor tank varies depending on the size and model, but most tanks can hold up to 150 psi.
How often should the air compressor tank be inspected?
It is recommended to inspect the air compressor tank at least once a year to ensure its safety and prevent any potential hazards.
How can I check if there is water in the air compressor tank?
You can check if there is water in the air compressor tank by releasing the air pressure and draining the tank. If there is water, it will come out with the air.
What kind of maintenance should be done on the air compressor tank?
Maintenance on the air compressor tank should include checking for leaks, cleaning the tank, and inspecting for any damage or wear.
How can I prevent rust in the air compressor tank?
To prevent rust in the air compressor tank, you should drain the tank regularly, use a rust inhibitor, and keep the tank dry when not in use.
Can a damaged air compressor tank be repaired?
Depending on the extent of the damage, an air compressor tank can be repaired by a professional welder or replaced entirely for safety reasons.