How to Install Air Compressor Check Valve: A Comprehensive Guide
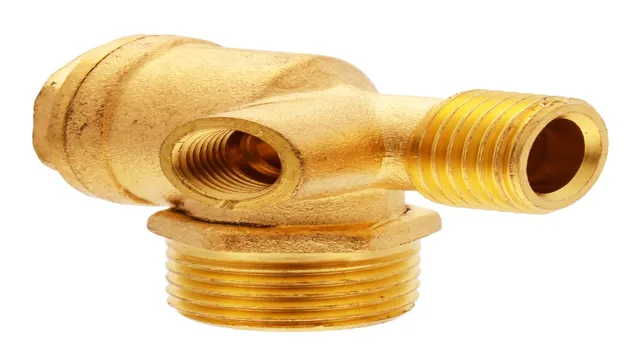
Welcome to another informative blog post! If you’re a DIY enthusiast or an auto mechanic who loves to tinker with machinery, you know that air compressors are an essential tool in your arsenal. But did you know that one of the most critical components of your compressor is the check valve? The check valve plays a vital role in ensuring the smooth operation of your air compressor. It helps maintain the air pressure inside the tank, preventing backflow and protecting your compressor from damage.
If you’re experiencing problems with your compressor, such as air leaking out of the tank or the compressor not turning off, it’s likely that the check valve is faulty. Fortunately, replacing a check valve is relatively straightforward and can be done with a few simple tools and a bit of DIY know-how. In this blog post, we’ll take you through the step-by-step process of installing a new air compressor check valve.
We’ll cover everything from identifying the problem to removing the old valve and installing the new one. So, if you’re ready to learn how to get your air compressor back up and running, grab your tools, and let’s get started!
Introduction
If you’re here searching for solutions on how to install air compressor check valves, you’ve come to the right place. Installing an air compressor check valve may seem daunting at first, but with the right tools and guidance, it can be done in no time. A check valve is an essential component that helps regulate the flow of air and prevent backflow.
It acts as a one-way valve that only allows air to flow in one direction while preventing it from flowing back into the compressor. To install the valve, start by identifying the location of the old valve and removing it. Then, install the new valve and ensure a tight fit.
A secure connection is vital to ensure proper airflow. Finally, test the compressor’s operation to ensure that it’s working correctly. By following these steps, you can efficiently install an air compressor check valve and keep your compressor functioning smoothly.
What is an Air Compressor Check Valve?
An air compressor check valve is a crucial component of an air compressor system that ensures it operates without interruptions. It is a one-way valve that permits a forward flow of compressed air and prevents backflow, ensuring efficient and uninterrupted operation of the air compressor. Think of it like the valve in a water pipe that controls the flow of water, except that an air compressor check valve allows air to flow in only one direction, preventing any air from flowing backward.
This critical component is essential for protecting the air compressor’s longevity and safety, preventing system failure and reducing the need for costly repairs. Ensuring that the check valve is in good working condition is crucial for optimal air compressor performance.
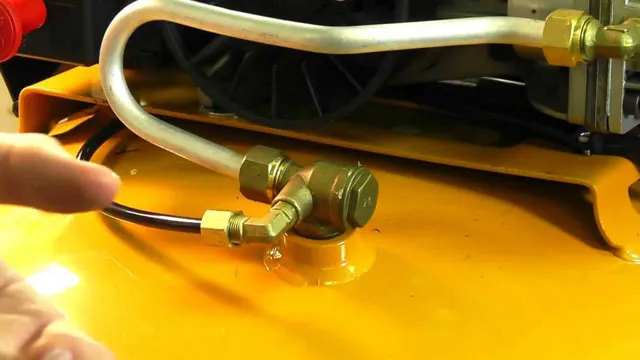
Why is it Important to Install a Check Valve?
check valve Introduction: Installing a check valve is a critically important step in ensuring the safety and efficiency of your plumbing system. This simple device allows water or other fluids to flow in only one direction, preventing backflow, which can cause a range of problems. Whether you’re dealing with wastewater, sewage, or potable water, a check valve is essential for keeping your plumbing system running smoothly and efficiently.
In this post, we’ll explore why it’s so important to install a check valve, and what benefits it can offer to you and your plumbing system. So, let’s dive in!
Step-by-Step Guide
Installing an air compressor check valve is a crucial task that requires proper attention. Here’s a step-by-step guide on how to install an air compressor check valve. First, turn off the power supply and release the pressure of your air compressor.
Next, locate the inlet and outlet ports on your check valve and identify their corresponding connection points. Use appropriate tools to connect the check valve in the correct orientation, ensuring that the arrow on the valve points towards the outlet. Fasten the connections securely, ensuring that no leaks or air pockets remain.
Finally, test your air compressor for proper functioning by turning it on and checking for any unusual noises or leaks. By following these steps, you have successfully installed an air compressor check valve that will help regulate the airflow and ensure a safe and efficient operation of your compressor.
Step 1: Gather Materials
When it comes to starting a new project, gathering the necessary materials is the first step. Whether you’re working on a DIY craft or a home improvement task, having all the right tools and supplies at your fingertips can make all the difference. Depending on the project, materials can range from simple items like glue and tape to more complex tools such as saws and sanders.
It’s important to plan ahead and make a list of everything you need, so you can purchase or locate the necessary items before starting your project. You don’t want to be halfway through your project and realize you’re missing a critical component! By taking the time to gather your materials, you’ll be setting yourself up for success and ensuring that your project runs smoothly.
Step 2: Identify the Installation Location
When it comes to installing a new system or appliance, the location plays a vital role in ensuring efficient performance. The second step to installing any system or appliance is to identify a suitable installation location. You should consider the distance from the power source, ventilation, and other environmental factors that could interfere with the system’s performance.
When it comes to HVAC systems, experts recommend installing the equipment as close to the center of the house as possible. This helps to ensure equal distribution of air throughout the house. Additionally, the location should be accessible for maintenance purposes.
When choosing an installation location, ensure that it is sturdy enough to support the weight of the system. You wouldn’t want the system to come crashing down due to a weak foundation. Remember, a poorly chosen location can lead to inefficiencies and potential hazards that can compromise your system’s integrity.
So take your time and choose a suitable location that meets all the installation requirements.
Step 3: Remove the Old Check Valve (if applicable)
When it comes to removing an old check valve, the process can vary depending on the type of valve and its location. However, we’ve put together a step-by-step guide to help make the process as simple and straightforward as possible! First, you’ll need to locate the old check valve. This is typically located near the pump or along the line where water enters your home.
Once you’ve found it, you’ll need to shut off the water supply to prevent any spills or leaks. Next, you’ll need to loosen the clamps that hold the check valve in place. Depending on the material of the valve and the clamps, this may require a wrench or pliers.
Once the clamps are loosened, carefully pull the valve away from the pipe. If the old check valve is particularly stubborn or corroded, you may need to use a lubricant or tap it gently with a hammer to loosen it. Once it’s free, discard the old valve and clean the surrounding area thoroughly.
It’s important to note that not all systems will have an old check valve that needs to be removed. If you’re unsure whether your system has a check valve or where it is located, it’s always best to consult with a professional. By following these simple steps, you can remove your old check valve with ease and prepare for the installation of a new valve.
Remember to take your time and work carefully to avoid any damage or leaks. Happy plumbing!
Step 4: Install the New Check Valve
Now that you have removed the old check valve, it’s time to install the new one. Here is a step-by-step guide to help you get the job done easily and correctly. First, make sure that the threads on the new check valve match those on the water line.
If they don’t, you may need an adapter to make them fit properly. Next, apply plumber’s tape to the threads of the new check valve. This helps create a tight seal and prevents leaks.
Now, screw the new check valve onto the water line using your hands. Once you have it hand-tightened, use a wrench to tighten it fully. Be careful not to overtighten, as this can cause the threads to strip.
Finally, turn the water back on and check for any leaks. If everything looks good, congratulations, you have successfully installed a new check valve! Remember to always follow the manufacturer’s instructions and safety guidelines when working with plumbing. With a little patience and attention to detail, you’ll have your plumbing system running smoothly in no time.
And don’t forget to replace your check valve regularly to avoid any future issues!
Step 5: Tighten All Connections
Now that all the required cables and wires are correctly connected, it’s time to double-check their tightness to ensure a secure connection. Loose connections result in dropouts, distortion, and reduced performance of your audio system. It is especially vital when dealing with electrical devices that are prone to vibrations.
The best way to do this is to use a wrench or pliers and finger-tighten each connection, then give them a gentle extra twist to ensure they are securely fastened. However, be sure not to over-tighten them, as it may result in a stripped screw or risk damaging the connector and the device. By following this last, but certainly not the least step – tightening all connections, you can avoid future headaches and ensure that your audio system remains in perfect working order for years to come.
Testing and Maintenance
If you own an air compressor, you know how important it is to maintain it regularly to ensure it performs as expected. One of the most critical components of the air compressor is the check valve. A functioning check valve prevents backflow of air into the compressor’s cylinder head, avoiding permanent damage to the compressor.
Installing a new check valve can be a challenging task, but it’s not impossible. You start by removing the old check valve and cleaning the threads of the air compressor. After cleaning the threads, apply regular Teflon tape to the new check valve, ensuring an airtight seal.
Wrench the check valve onto the air compressor securely, and you’re done. Remember that a faulty check valve can be catastrophic and cause damage to the entire air compressor system. Therefore, it’s essential to check and replace your check valve regularly to extend the life of your air compressor.
Step 1: Test the Check Valve
When it comes to the maintenance of your sump pump system, it is essential to ensure that the check valve is properly functioning. This small valve prevents water that has been pumped out from flowing back into the pit, requiring the pump to work harder. To test the check valve, turn off the system and remove the pump.
Look for the valve at the end of the discharge line and lift it out of the pipe. If it is free of debris and moves smoothly, it is in good condition. However, if it is clogged or stuck, it will need to be cleaned or replaced.
It is important to check the check valve regularly to ensure that it is functioning correctly and prevent any potential damage to your pump system. By taking care of this small but crucial component, your sump pump system will be ready for any unexpected weather events or water issues that may arise.
Step 2: Perform Regular Maintenance
Regular maintenance and testing of equipment are essential to ensure smooth operation and optimal performance. Without regular upkeep, equipment can deteriorate quickly, leading to inefficiencies and potential breakages. Therefore, it is important to schedule regular checks and maintenance to identify any issues before they escalate to costly repairs.
Furthermore, regular testing is necessary to ensure that the equipment operates within its maximum efficiency, which saves on operating costs and extends its lifespan. Neglecting equipment can result in unexpected downtime, which can bring operations to a standstill. By regularly testing and maintaining equipment, businesses can ensure uninterrupted and efficient operations.
Therefore, it is crucial to prioritize testing and maintenance to prevent expensive breakdowns and downtime.
Conclusion
Congratulations on making it through the steps to install your air compressor check valve! You’re now one step closer to ensuring optimal performance and safety in your air compressor system. Remember, a check valve is like a bouncer at a club – it only lets in the authorized air and keeps out the unwanted elements. So, just like a bouncer, your check valve is crucial in keeping the party going and avoiding any trouble.
Keep up the good work, DIYers, and keep your compressor systems in check!”
FAQs
What is an air compressor check valve and why is it important in the installation process?
An air compressor check valve is a device that controls the flow of air in one direction and prevents backflow of air. It is important in the installation process as it ensures the proper functioning of the compressor and prevents damage to the motor.
What are the steps for installing an air compressor check valve?
The steps for installing an air compressor check valve are:
1. Turn off and unplug the compressor.
2. Locate the existing check valve and remove it.
3. Install the new check valve in the same location.
4. Reattach any hoses or tubes that were removed.
5. Turn on the compressor and check for any leaks.
6. Test the compressor to see if it is functioning properly.
Can any type of air compressor check valve be used for installation?
No, it is important to ensure that the air compressor check valve is compatible with the specific model and make of your compressor. Using the wrong type of check valve can cause damage to the compressor or render it ineffective.
How often should an air compressor check valve be replaced?
It is recommended to replace the air compressor check valve every two years or sooner if it shows signs of wear or damage.
What are the signs that an air compressor check valve needs to be replaced?
Signs that an air compressor check valve needs to be replaced include:
1. Air leaks around the check valve
2. Difficulty or failure to start the compressor
3. Low or fluctuating air pressure
4. Unusual sounds coming from the compressor
Is it possible to install an air compressor check valve without professional help?
Yes, it is possible to install an air compressor check valve without professional help as long as you follow the manufacturer’s instructions and have some basic knowledge of the compressor’s components.
Are there any safety precautions that should be taken during the installation process?
Yes, it is important to wear protective gear such as gloves and eye protection when working with compressed air. Additionally, ensure that the compressor is completely turned off and unplugged before beginning the installation process.