How to Install Air Compressor Hose Fittings: A Step-by-Step Guide
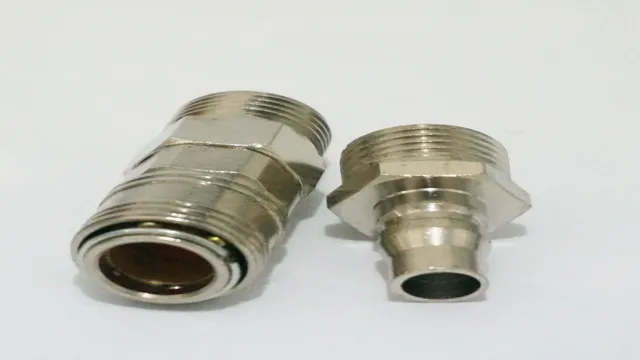
Installing air compressor hose fittings might seem like a daunting task at first, but with the right knowledge and tools, it can be a breeze. Whether you are a seasoned DIYer or a beginner, this guide will walk you through the steps of installing your air compressor hose fittings in no time. Have you ever wondered why some air tools don’t work as expected or air pressure drops? One common reason could be a loose or improperly connected hose fitting.
It’s important to get the installation right to avoid wasting time and money down the road. Think of it like building a sandcastle – proper foundation and structure make all the difference in creating a sturdy and secure sandcastle that can withstand the waves. So let’s dive in and learn how to install those air compressor hose fittings, so you can spend more time working and less time fixing.
Gather Tools and Materials
Installing air compressor hose fittings requires a few materials and tools to make the process simple and effective. First off, you’ll need the air compressor hose fittings themselves. Depending on the type of fitting you prefer, you may also require wrenches, pliers or an adjustable wrench to secure them in place.
Secondly, get teflon tape to wrap around the male threads of the fittings, ensuring that they’re airtight and leak-free. You may also require a pipe cutter or hacksaw to slice your old hose into a suitable length to swap with your new one. To finish, you might need some lubricant to coat the threads of the fittings, enabling them to slide in smoothly.
Once you have all of these materials, you’ll be prepared for a trouble-free installation.
Air compressor hose
When it comes to installing an air compressor hose, you’ll need a few tools and materials to get the job done right. Firstly, you’ll need a wrench to loosen the fittings on the air compressor. A crescent wrench is the most versatile option and can be used on different sizes of fittings.
Secondly, you’ll need teflon tape. This tape will create a proper seal between the fittings and the hose, ensuring no air leaks occur. Finally, you’ll need the air compressor hose itself.
It’s important to choose a hose that matches the size of your air compressor fittings to ensure a secure fit. Remember to check the pressure rating of the hose as well, to ensure it can handle the amount of air being pushed through it. By gathering these tools and materials before starting the installation process, you’ll save yourself time and stress trying to find them halfway through.
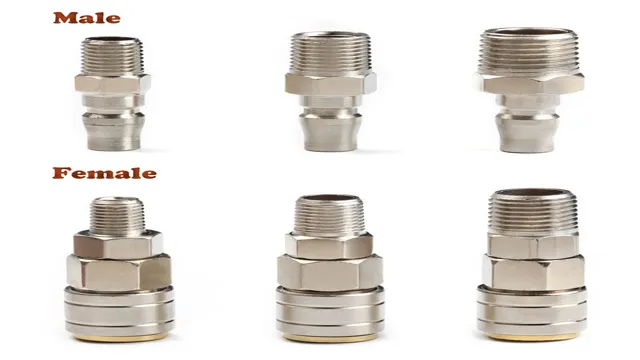
Hose fitting kit
A hose fitting kit contains various materials and tools that are crucial to connect a hose to its fitting. To get started, we need to gather the necessary tools and materials, such as a hose, fittings, clamps, Teflon tape, and a wrench. It is crucial to check the hose’s diameter and match it up with the appropriate fitting, ensuring a tight fit.
The Teflon tape is used to prevent any leaks between the hose and fittings. A pair of pliers or a wrench can be used to tighten the fittings securely. It is essential to keep in mind that the hose fittings are prone to wear and tear, so regular maintenance should be done to prolong their lifespan.
Overall, having a hose fitting kit and understanding how to use it is essential for any DIYer or professional who wants to ensure a leak-proof and secure hose connection.
Adjustable wrench
Adjustable wrench One essential tool that every toolbox should have is the adjustable wrench. These versatile wrenches are perfect for tightening or loosening nuts and bolts of different sizes, making them suitable for a wide range of tasks. To gather these tools together, you’ll need to head over to a hardware or home improvement store.
Adjustable wrenches typically come in different sizes, with jaws that can be adjusted for various bolt and nut sizes. Before you head to the store, make sure you know what size bolt or nut you’ll be working on to get the right size adjustable wrench. Additionally, if you’re planning on using the wrench for extended periods, ensure that you select one with a comfortable handle to prevent hand fatigue.
Although adjustable wrenches might seem like simple tools, they play an important role in making repairs and maintenance tasks easier. Whether you’re a professional mechanic or a DIY enthusiast, adding an adjustable wrench to your toolkit is a must.
Thread sealant
When it comes to applying thread sealant, having the right tools and materials is essential for getting the job done right. You’ll need a few specific items, including the actual thread sealant, a brush or applicator tool for applying the sealant, and some rags or paper towels for cleanup. Additionally, it’s a good idea to have a pair of gloves on hand to protect your hands from any harsh chemicals in the sealant.
If you’re working in a tight space or need to apply the sealant to hard-to-reach areas, consider using a small mirror or flashlight to help guide your work. With these basic tools and materials in place, you’ll be well-prepared to tackle any thread sealant project that comes your way.
Teflon tape
Teflon tape is a versatile material that is essential for many plumbing projects. To get started, you’ll need to gather a few tools and materials. First, you’ll need a roll of Teflon tape – make sure to choose the correct thickness and width for your project.
You’ll also need a pair of scissors to cut the tape to the right length. Next, you’ll want to prepare the surfaces you’ll be sealing by cleaning them with a degreaser or alcohol – this will ensure the tape adheres properly. Finally, you’ll need some patience and a steady hand, as Teflon tape can be finicky to work with but yields great results.
So go ahead and gather your supplies, and don’t be afraid to ask for help if you need it – you’ll be a Teflon tape pro in no time!
Preparing the Hose
When it comes to setting up your air compressor, one important step is preparing the hose. Knowing how to install air compressor hose fittings can make the job easier and more efficient. First, make sure your hose is clean and free from debris.
Use a wire brush to remove any corrosion on the ends of the hose. Next, apply some thread sealant or Teflon tape to the threads of the fittings, as this will create a secure seal and prevent leaks. When attaching the fittings to the hose, make sure the threads are aligned properly and tighten them using a wrench.
Once everything is securely connected, turn on your air compressor and check for any leaks around the fittings. With these simple steps, you can prepare your air compressor hose and ensure a smooth and safe operation.
Cut hose to desired length
When it comes to using hoses, it’s essential to prepare them properly to ensure they function correctly. One crucial step in preparing a hose is cutting it to the desired length. Before you start cutting, make sure you have the correct measurements and take safety precautions to avoid any injury.
Using a sharp cutting tool, like a pair of heavy-duty scissors or a sharp utility knife, carefully cut the hose to the desired length. Keep in mind that you want to make a clean cut to prevent any fraying or damage to the hose’s interior. For a more precise cut, consider using a hose cutter or a saw.
Cutting hoses may seem like a simple task, but it’s important to do it correctly to prevent any leaks or other issues down the line. By preparing your hoses correctly, you can ensure they work efficiently and effectively for any task at hand.
Remove rough edges with sandpaper
Preparing the hose for any project is the first step in ensuring a smooth and efficient outcome. One of the crucial steps in preparing the hose is removing any rough edges with sandpaper. Rough edges can cause kinks in the hose or even punctures that can render the hose useless.
Simply taking a fine grit sandpaper and lightly sanding any rough edges smooths them out and helps prevent these issues. It’s essential to check the entire length of the hose for any rough patches and sand them down. This simple step can help avoid costly downtime due to hose failure during a project.
By taking the time to prepare the hose, you are ensuring that the project will go smoothly, and you will have a successful outcome.
Attach fitting to hose using wrench
Attaching fittings to hoses can be a challenging task, but with the right tools and techniques, it can be done easily. To prepare the hose, start by selecting the correct fitting for your hose. Ensure that both the hose and fitting are clean and free of any dirt or debris.
You can use a wire brush or a cloth to clean them thoroughly. Next, slide the fitting over the end of the hose and tighten it down using a wrench. Be careful not to over-tighten the fitting, as this can damage the hose and cause it to leak.
Once the fitting is secure, check for any leaks by running water through the hose. If there are no leaks, you are all set for your next project! Remember, that preparing a hose can seem daunting at first, but with patience and a little know-how, you’ll be ready to tackle any project in no time.
Apply thread sealant or Teflon tape to fitting threads
When it comes to preparing hoses for various applications, it’s crucial to apply the correct thread sealant or Teflon tape to ensure a secure and leak-free fit. Applying the wrong type of sealant or not applying any sealant at all can result in dangerous and expensive mishaps. It’s essential to use a thread sealant or Teflon tape that is compatible with the type of hose and fitting you’re working with.
For example, Teflon tape is generally used for smaller pipes and fittings, while a liquid sealant may be preferred for larger hoses. Applying the sealant or tape correctly is also important for a successful outcome. Make sure the threads are clean and dry before applying the sealant or tape and wrap it tightly around the threads in a clockwise direction.
Taking the time to properly prepare your hose connections can save you a lot of headaches and expenses in the long run.
Attaching the Hose to the Compressor
Attaching the hose to the compressor is a straightforward process once you have the right fittings. First, identify the type of fitting your compressor uses – whether it’s a quick-connect or threaded fitting. Next, choose the corresponding fitting for your hose.
You can find these fittings at most hardware or home improvement stores. Once you have your fittings, make sure your compressor is turned off and the hose is disconnected. Then, insert the fitting into the compressor’s air inlet and tighten it securely with a wrench.
Do the same for the other end of the hose. Finally, connect the two fittings by pressing them together and twisting until they lock into place. Your hose is now attached and ready to use for all your pneumatic tools and accessories.
Remember to always check your connections before using the hose to ensure that they are secure, leak-free, and safe to operate.
Turn off compressor and unplug
When it comes to attaching the hose to the compressor, there are a few steps you should follow to ensure a safe and secure connection. First and foremost, turn off the compressor and unplug it to avoid any potential accidents. Once that’s done, take a good look at both the hose and the compressor fittings, making sure they’re clean and free from any debris or damage.
Next, align the hose fitting with the compressor fitting and push them together until they’re firmly connected. Double-check that they’re secure by giving them a gentle tug. If they feel loose, disconnect them and try again.
Remember, a faulty connection could result in air leaks and decreased efficiency. Lastly, open the compressor valve and turn on the machine to check for any air flow issues before you start using it for your project. By ensuring a proper connection between the hose and compressor, you’ll have a worry-free and productive work session ahead!
Clean and dry compressor fitting
When it comes to attaching the hose to your compressor, it’s crucial to make sure that the compressor fitting is clean and dry. Any dirt or debris could cause problems with the seal, resulting in a leak or other complications down the line. To start, use a cloth to wipe down the fitting and ensure that there’s no residue left from previous use.
Next, make sure that the fitting is completely dry before attaching the hose. You can use a separate cloth or towel to dry it off thoroughly, or you can use compressed air to blow out any remaining moisture. Remember, taking the time to properly clean and dry the compressor fitting can prevent headaches in the long run and help ensure efficient and safe operation.
Attach hose fitting to compressor using wrench
Attaching a hose to a compressor can seem like a daunting task, but with the right tools and some simple steps, it can be done in no time. Start by finding the hose fitting that matches the compressor’s outlet valve and screwing it in place. Use a wrench to tighten the fitting, ensuring that it is secure and won’t come loose during operation.
Make sure the hose is free from kinks or bends and attach the other end to the tool you will be using. Once everything is securely in place, you can turn on the compressor and start working. Whether you’re working on a DIY project or using a compressor for professional purposes, attaching the hose is a crucial step that shouldn’t be skipped.
With a little practice and patience, anyone can master the art of attaching a hose to a compressor and enjoy the benefits of compressed air.
Apply thread sealant or Teflon tape to compressor fitting
When it comes to attaching the hose to the compressor, it’s important to ensure a secure and leak-free connection. One crucial step is to apply thread sealant or Teflon tape to the compressor fitting. This helps to prevent air leaks and ensures that the connection is strong and stable.
Thread sealant is a viscous liquid that is applied to the threads of the fitting before screwing the hose onto it. Teflon tape is a thin, white tape that is wrapped around the threads of the fitting before attaching the hose. Both of these options help create a seal that prevents air from escaping and ensures that the compressor runs efficiently.
Without proper sealing, the compressor may not function as intended and cause air leakage, which can be frustrating and even dangerous. So take the time to apply thread sealant or Teflon tape before connecting your hose to the compressor and ensure a smooth and safe operation.
Testing for Leaks
Installing the right air compressor hose fittings is crucial for a successful and safe compressor system. However, it is not just about attaching the fittings to the hose and calling it a day. It is equally important to test for leaks before using the system.
One way to perform this test is by applying a soapy water solution to the fittings and hose connections and looking for any bubbles forming. If there are bubbles, it means there is a leak and the fitting needs to be tightened or replaced. This step is critical because even a small leak can lead to decreased efficiency and can be potentially hazardous.
By taking the time to test for leaks, you can ensure your air compressor system is functioning correctly, and avoid any potential issues down the road.
Turn on compressor and check for leaks
When you’re setting up your compressor, it’s crucial to check for leaks before you start using it. A compressed air system can leak in many ways, such as through valves, fittings, or even the hoses themselves. Fixing these leaks is an essential aspect of compressor maintenance, helping to ensure that your system operates effectively and efficiently.
To check for leaks, you need to turn on the compressor and listen for any unusual hissing or whistling sounds. You can also use a soap solution to spray the fittings and hoses. If you see any bubbles forming, then this is a sign of a leak.
Once you’ve identified any leaks, you can get to work fixing them and ensuring that your compressed air system is running at optimal levels. Remember, checking for leaks should be a regular part of your compressor maintenance routine, and addressing them can help save you money in the long run.
Listen for any hissing sounds
When testing for leaks in your home, it’s important to keep your ears open for any hissing sounds. These sounds could be a sign of air escaping from a pipe or a hole in the wall. Start by turning off all water and gas sources in your home, then locate your water meter and check for any movement.
If the needle on the meter is still moving, you likely have a leak somewhere. Next, inspect your pipes and appliances for any signs of damage or wear and tear. If you suspect a leak but can’t locate the source, try using a dye test or a thermal imaging camera to identify the problem area.
Remember, even a small leak can lead to big problems down the line, so it’s always better to be proactive and address any issues as soon as possible.
Spray soapy water on fittings and connections
When it comes to plumbing, leaks are a common occurrence and can cause significant damage if not addressed. That’s why it’s crucial to test for leaks regularly. One simple method is to spray soapy water on fittings and connections.
The soap will create bubbles if there’s a leak, indicating where the issue is. This method is effective for both visible and hidden pipes. It’s essential to check for leaks regularly because they can cause water damage, spike your water bill, and even lead to mold growth in your home.
By regularly checking for leaks, you can catch them early and prevent further damage. Don’t forget to also check your water pressure and look for signs of corrosion on your pipes. By taking these steps, you can ensure your plumbing is in good condition and avoid costly repairs.
Check for bubbles indicating leaks
When testing for leaks in any system, it’s essential to check for bubbles. Bubbles can be a sign that there’s a leak in the system causing air to escape. You can test for leaks by using a soap solution or a leak detector.
Apply the solution to the area you suspect is leaking and observe whether bubbles form on the surface. If you notice bubbles, this is an indication of a leak in the system that needs repair. It’s important to fix any leaks as soon as possible to avoid further damage to the system and to ensure it’s running at optimal performance.
Neglecting leaks can lead to wasted energy, increased utility bills, and even health hazards. So don’t ignore bubbles and take immediate action to address any leaks you detect.
Conclusion
Now that you’ve learned how to install air compressor hose fittings, you’re one step closer to becoming the MacGyver of the DIY world. With your newfound knowledge, you can confidently tackle any project that requires clean, compressed air. The process may seem daunting at first, but with a little bit of practice, you’ll be fitting hoses like a pro in no time.
So, go forth and conquer, my DIY comrades, and don’t forget to breathe in that sweet, sweet compressed air!”
FAQs
What tools do I need to install air compressor hose fittings?
You will need a wrench, Teflon tape, and the appropriate sized fittings for your air compressor and hose.
Can I use any type of fittings for my air compressor hose?
It is important to use fittings that are compatible with your air compressor and hose. Check the manufacturer’s recommendations before purchasing.
How do I determine the size of the fittings I need for my air compressor hose?
Measure the diameter of your air compressor and hose and choose fittings that match those measurements.
Do I need to use Teflon tape when installing air compressor hose fittings?
Yes, using Teflon tape will help create a better seal and prevent leaks.
Can I install air compressor hose fittings myself, or do I need a professional?
If you have basic knowledge and experience with tools, you can likely install the fittings yourself. However, if you are unsure or uncomfortable, it’s best to consult a professional.
What kind of maintenance do air compressor hose fittings require?
It’s important to regularly check the fittings for any signs of wear or damage and replace them as needed. Also, make sure to keep them clean and free of debris.
How can I prevent air leaks from my hose fittings?
Using Teflon tape, regularly checking for wear or damage, and tightening the fittings as needed can all help prevent air leaks from your hose fittings.