How to Install a Pressure Regulator on an Air Compressor: Step-by-Step Guide

Are you tired of your air compressor delivering inconsistent pressure? Or maybe you’ve noticed an unusual amount of wear and tear on your tools due to excessive pressure levels? Whatever the case may be, installing a pressure regulator on your air compressor could be the solution you’re looking for. Think of a pressure regulator like a traffic cop on a busy road. Its job is to monitor the flow of air and keep it running at a steady pace, just like a traffic cop keeps cars moving in an orderly fashion.
By regulating the output of your air compressor, you can ensure that your tools receive the amount of pressure they need without damaging them in the process. Installing a pressure regulator may seem daunting at first, but it’s actually a fairly straightforward process. With a few basic tools and some simple instructions, you can have your pressure regulator up and running in no time.
Not only will this improve the quality of your work, but it will also help prolong the lifespan of your tools by ensuring they’re not subjected to unnecessarily high pressure levels. Whether you’re a DIY enthusiast or a seasoned professional, adding a pressure regulator to your air compressor is a simple yet effective way to improve your workflow and ensure that your tools are protected from damage. So why wait? Get started today and enjoy the benefits of a well-regulated air compressor!
What is a Pressure Regulator?
If you’re looking to install a pressure regulator on your air compressor, the first step is to make sure you have the right regulator for your needs. A pressure regulator controls the amount of pressure coming out of your compressor, ensuring that it stays within a safe and optimal range. To install the regulator, you’ll need to first turn off the air compressor and disconnect it from its power source.
Then, remove the fitting from the compressor’s output port and attach the regulator’s inlet port to the compressor. From there, attach the regulator’s outlet port to the fitting that leads to your tool or application. Be sure to tighten all connections securely and check for any leaks before starting up the compressor again.
A properly installed pressure regulator can help prolong the life of your compressor and give you better control over the air pressure in your tools.
Definition and purpose of a pressure regulator
A pressure regulator is a device that is used to control and maintain the pressure level of a fluid or gas within a system. It works by regulating the flow of fluid or gas through the system and ensuring that the pressure level stays within a defined range. Pressure regulators are commonly used in various applications, such as industrial processes, gas delivery systems, and water supply systems.
The primary purpose of a pressure regulator is to prevent damage to equipment and ensure optimal performance by maintaining a consistent pressure level. Without a pressure regulator, increased pressure levels can cause damage to the system, and low-pressure levels can result in poor performance and efficiency. Overall, a pressure regulator is an essential component in many systems as it helps ensure safe and efficient operation.
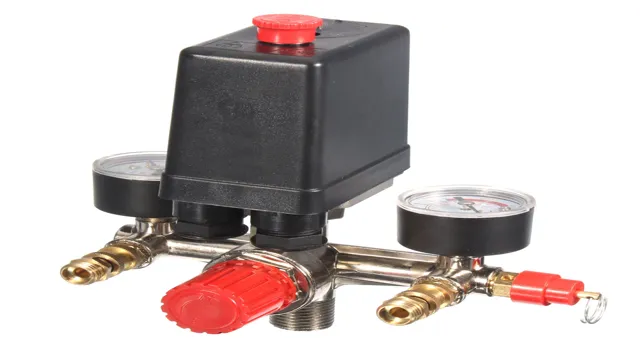
Tools and Equipment Needed
If you have an air compressor, you may want to install a pressure regulator to keep the pressure at a constant level. To do this, you’ll need a few tools and equipment first. You’ll need a pressure regulator, of course, and the appropriate fittings to connect it to the air compressor.
You’ll also need Teflon tape to ensure a tight seal on the fittings and a wrench to tighten them. Once you have all these things, you’ll be ready to install the pressure regulator. Start by turning off the air compressor and releasing the pressure from the tank.
Then, remove any fittings from the regulator and wrap Teflon tape around the threads of the fittings. Screw the fittings into the regulator and tighten them with a wrench. Finally, attach the regulator to the compressor, making sure it’s securely fastened.
With your new pressure regulator installed, your air compressor will be able to operate at a consistent pressure for all your compressed air needs.
List of required tools for installation process
When it comes to installation processes, having the right tools and equipment is essential to ensure that everything is properly installed and functional. If you’re planning to install something at home, make sure you have the necessary tools and equipment on hand before you start the installation process. Some of the tools and equipment you might need include a drill, a hammer, a saw, a level, tape measure, and screwdriver, depending on the installation requirements.
It’s important to use the right tools and equipment as this will help ensure that the installation is done correctly and efficiently. Don’t forget to check the installation instructions or manual before starting the process to ensure that you’re using the right tools and equipment for the job. By having the right tools and equipment at the start, you can complete the installation quickly and without any issues.
Step by Step Installation Process
Are you struggling to control the pressure in your air compressor? Installing a pressure regulator can help you regulate the air pressure with ease. The process of adding a pressure regulator to your air compressor is not as complicated as you may think. Here’s a step-by-step guide on how to install a pressure regulator on an air compressor.
Firstly, you need to turn off the air compressor and disconnect it from the power source. Next, remove the existing regulator or pressure switch from your compressor. Afterward, clean the area where you will install the new pressure regulator.
Once you have selected the best location to mount your pressure regulator, attach the pressure gauge and regulator bracket. Connect the air line to the regulator inlet and outlet and adjust the regulator until you achieve the desired pressure. Lastly, reconnect the power supply and start the compressor to check if it’s running correctly.
Installing a pressure regulator on your air compressor will save you energy and prolong the life of your tools. So go ahead and give it a try today!
Step 1: Turn off power supply
If you’re planning to tackle a DIY electrical installation project, the first step is to turn off the power supply. This may seem like a no-brainer, but it’s important to take this step seriously as it will reduce the risk of electrical shock or fire. Before starting any work, locate the circuit breaker or fuse box that controls the circuit you’ll be working on and switch off the power supply.
Use a voltage tester to confirm that the power has been successfully cut off before proceeding. Don’t forget to inform anyone who may be affected by the power cut, like family members or colleagues, to avoid any disruption. Remember that safety comes first!
Step 2: Disconnect air compressor from power source
When installing or maintaining an air compressor, it’s crucial to follow proper safety measures to prevent any accidents. One necessary step in this process is to disconnect the air compressor from its power source. Make sure to unplug the compressor from the electrical outlet or remove it from any power supply before performing any maintenance or installation work.
This step ensures that the compressor won’t accidentally start while you’re working on it, which could cause injury or damage to the equipment. By removing the power source, you’ll have better control over the compressor and prevent any unwanted start-ups. Following this step may seem minor, but it plays a crucial role in maintaining the safety and functionality of your air compressor.
So never skip this essential step, and always prioritize safety!
Step 3: Remove existing regulator (if any)
When it comes to installing a new voltage regulator in your vehicle, it’s important to do it properly. Step three involves removing any existing regulator that may be in the vehicle already. This is a crucial step because having two regulators in your vehicle can cause electrical problems and other issues down the line.
Before you begin, be sure to disconnect the battery to avoid any electrical shocks or accidents. Once you’ve done that, locate the existing regulator and carefully remove it using the appropriate tools. Make sure to keep track of any screws or bolts you remove so that you can put them back in the right place later on.
Once the existing regulator is removed, make sure the area is clean and free of debris before installing the new one. With a little bit of patience and precision, removing the existing regulator should be a piece of cake.
Step 4: Attach regulator to air compressor
Now it’s time to attach the regulator to the air compressor. This step is crucial as the regulator controls the pressure of the compressed air, preventing damage to your tools or equipment. To start, make sure the air compressor is turned off and unplugged.
Take the regulator and attach it to the port on the air compressor. Use a wrench to tighten it securely, but be careful not to over-tighten it. Next, attach the air hose to the regulator by inserting one end of the hose into the regulator’s coupling and tightening it with a wrench.
Once the regulator is attached, adjust the pressure to the desired level, and connect your tools or equipment to the other end of the hose. Check everything is connected correctly and turn on the air compressor. Congratulations, you’ve successfully installed your air compressor and regulator, and you’re ready to get to work on your latest projects.
Step 5: Connect regulator to air hose
Now that you have attached the pressure gauge to the regulator, it is time to connect it to the air hose. This step is crucial for the proper functioning of the regulator as it allows the compressed air to flow from the tank to the tool. Begin by ensuring that the air hose is clean and free from any obstructions before attaching it to the outlet port on the regulator.
Tighten the connection with a wrench to prevent any air leaks that may affect the accuracy of the pressure readings. Check that the hose is properly connected and secure before turning on the air compressor to test the regulator. Remember to open the valve gradually to avoid sudden pressure surges that may damage the tool or the regulator.
Following these steps will ensure that the regulator and air hose work together efficiently, providing you with the required air pressure for your tools.
Step 6: Adjust regulator settings
After connecting the fuel supply and return lines, the next step to install a regulator is to adjust its settings. The regulator is designed to control the fuel pressure, which is crucial for the engine to function properly. The first thing you need to do is to check the manufacturer’s instructions for the recommended pressure range.
Then, use a pressure gauge to test the readings and make sure they match the specified range. If not, you can adjust the regulator by turning the adjustment screw in the desired direction until the pressure is within range. Keep in mind that the fuel pressure can affect the vehicle’s performance and fuel efficiency, so it’s essential to get it right.
Once the pressure is set, you can start the engine and monitor the performance. If any issues arise, you can tweak the regulator settings accordingly until everything runs smoothly. Overall, adjusting the regulator settings can be challenging, but it’s a crucial step in ensuring the proper functioning of your vehicle’s engine.
Step 7: Test regulator for proper functioning
Before declaring the regulator installation complete, it’s important to test it to ensure it’s working correctly. The first step in testing your regulator is to turn on your gas supply and look for any signs of leaks. If there are no leaks, you can continue with the testing process by turning on your stove and observing the burner shapes and sizes.
Ensure that all burners are producing consistent flames without any flickering or popping sounds. This indicates a well-regulated gas supply. You can also test the regulator by turning on the grill and observing the flame.
The grill flame should be blue and stable, indicating that the regulator is functioning correctly. By checking all these factors, you’ll confirm that your regulator installation was successful and your gas supply is well-regulated. It’s always a good idea to perform regular maintenance on your regulator to ensure it’s working correctly and avoid potential gas leaks or malfunctions.
Conclusion
In conclusion, installing a pressure regulator on your air compressor is a no-brainer if you want to control the flow of your compressed air. It’s a simple process that anyone can easily achieve with the right tools and a bit of know-how. Just remember to read the instructions carefully, double-check your fittings and pressure settings, and always wear the proper safety gear.
Your compressed air system will thank you for it, and you’ll be able to keep your pneumatic tools running at optimal performance levels. So go ahead and regulate that pressure like a boss!”
Summary of the installation process and importance of pressure regulation on air compressors
Air compressors are a vital tool in many industries, from construction to manufacturing. However, improper installation and usage could lead to a risk of injury or damage to the compressor. Let’s walk through the step-by-step installation process.
First, ensure that the area for installation is clean and dry. Next, attach the air compressor to a stable surface using bolts or screws. Then, connect the hoses and accessories to the proper outlets and fittings, being sure to use thread sealant for a secure connection.
Finally, plug in the power and turn on the compressor, making note of any abnormal noises or issues. An important aspect of using an air compressor is pressure regulation. It may seem insignificant, but improper regulation could lead to damage to the compressor, the tools being powered, or even injury to the user.
Prevent over-pressurization by using a pressure regulator, which will limit the maximum pressure output. Check the regulator and gauges periodically to ensure the pressure stays within safe levels. It’s also important to note that different tools and accessories may have different pressure requirements, so always adjust as needed.
Proper installation and pressure regulation will ensure a safe and efficient use of your air compressor.
FAQs
What is a pressure regulator and why do I need it for my air compressor?
A pressure regulator is a device that controls the amount of pressure flowing through your air compressor. It is necessary to regulate the pressure to prevent damage to your equipment and to ensure safety during operation.
How do I choose the right pressure regulator for my air compressor?
You need to consider the maximum pressure your compressor can operate at, the flow rate of your compressed air system, and the type of applications you will be using your air compressor for. You can consult with a professional to help you determine the appropriate pressure regulator for your needs.
Can I install a pressure regulator myself or should I hire a professional?
Depending on your experience with air compressors and plumbing, you may be able to install a pressure regulator yourself. However, if you are unsure or inexperienced, it is recommended to hire a professional to ensure proper installation and avoid any safety hazards.
What are the typical costs associated with installing a pressure regulator on an air compressor?
The cost will vary depending on the type of pressure regulator you need, as well as your location and whether you hire a professional. Typically, pressure regulators can range from $20 to $200 or more.
How do I properly maintain my pressure regulator on my air compressor?
It is recommended to monitor the pressure regulator regularly and clean it as needed to prevent dirt and debris buildup. You should also check for any leaks or damage and promptly address any issues to ensure safe and efficient operation.
Can I use a pressure regulator for other appliances besides my air compressor?
Yes, pressure regulators can be used for a variety of applications, such as for gas grills, propane heaters, and water heaters. However, it is important to ensure that you use the appropriate pressure regulator for each appliance and consult with a professional if unsure.
How do I troubleshoot if my pressure regulator is not working properly?
If you notice a decrease in air pressure or irregular operation, you may need to inspect and clean your pressure regulator. You may also need to test the regulator for leaks or damage and replace any faulty parts. If you are unsure or unable to fix the issue, it is recommended to seek professional assistance.