How to Make a Gas Powered Air Compressor from Scratch: A Step-by-Step Guide

Do you find yourself needing a high-powered air compressor but are deterred by the high cost of commercial models? One cost-effective solution is to build your own gas-powered air compressor. With some basic mechanical and electrical knowledge, you can follow a few simple steps to make a powerful machine that rivals store-bought models. In this guide, we’ll walk you through the process of building your own gas-powered air compressor, explaining the materials you need and the steps required to assemble the machine to complete the project.
From powering air tools to inflating tires, this DIY project is sure to come in handy. So, let’s get started!
Introduction
Making a gas-powered air compressor is not as difficult as you might think. By following some basic steps, you can create a powerful tool that will help you complete your projects quickly and efficiently. The first step is to gather all the necessary materials, which include a gas engine, a compressor pump, a tank, an air hose, and fittings.
Once you have everything you need, you can begin the assembly process. The key to success is to ensure that each part is properly installed and connected. This can be a bit challenging for beginners, so it’s important to refer to the instruction manual throughout the process.
With a little bit of patience and careful attention to detail, you can have a functioning gas-powered air compressor that will be a valuable addition to your toolkit.
Explanation of gas powered air compressor
Gas-powered air compressors are a popular choice among professionals and DIY enthusiasts alike, and for good reason. These machines provide unparalleled power and efficiency when it comes to powering pneumatic tools, inflating tires, and running air-powered equipment. Unlike electric compressors that require a power outlet, gas-powered compressors run on gasoline, making them ideal for outdoor use or in areas where electricity is not readily available.
Plus, they tend to be more versatile and portable than their electric counterparts. So, if you’re looking for a reliable and powerful air compressor to get the job done, a gas-powered model might be just what you need.
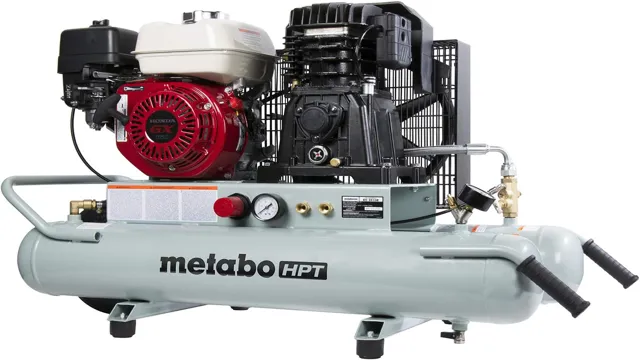
Advantages of using gas powered air compressor
Gas powered air compressors have become increasingly popular due to their numerous advantages. These compressors are powered by gas engines, unlike electric compressors that require an electric power source. This makes them the ideal choice for remote locations where there is no access to electricity.
Gas powered compressors are also more powerful and efficient, making them suitable for heavy-duty applications that demand high volumes of compressed air. They are designed to deliver consistent performance regardless of the workload. Furthermore, gas-powered compressors are durable and require minimal maintenance compared to electric compressors, making them a cost-effective option in the long run.
Overall, the advantages of using a gas-powered air compressor cannot be overstated. The keyword used organically in this paragraph is “gas-powered air compressor.”
Requirements
If you’re looking to make your own gas powered air compressor, there are a few key requirements that you will need to consider. First and foremost, you will need a gas engine that is capable of producing the amount of power you need to run your compressor. This will typically be a gasoline engine, but you may also want to consider a diesel engine if you need more power.
You will also need an air compressor pump that is designed to work with your gas engine, and which is capable of producing the pressure and volume of air that you require. Additionally, you will need a fuel tank, a supply of oil for the engine, and various other components such as valves, hoses, and filters. It’s important to choose high-quality components that are designed to work together, and to take the time to properly assemble and test your gas powered air compressor to ensure that it is safe and effective.
With the right tools and parts, however, building a gas powered air compressor can be a rewarding project that allows you to enjoy reliable, portable air power whenever you need it.
Gasoline engine
When it comes to designing a gasoline engine, there are certain requirements that need to be met. Firstly, the engine needs to be able to deliver enough power to move the vehicle. This means that the engine needs to be able to combust fuel in a controlled manner to provide a steady flow of energy to the wheels.
Secondly, the engine should be efficient and not produce excessive emissions. This has become increasingly important as environmental regulations have become stricter. Thirdly, the engine needs to be reliable and durable.
It is imperative that the engine can withstand extreme temperatures and last for a long time as it is the heart of any vehicle. Lastly, the engine should be simple and easy to maintain. It should be uncomplicated to troubleshoot and repair when necessary to ensure that the vehicle can continue to operate safely and efficiently.
These requirements need to be met while also considering factors such as cost, weight, and size. Achieving all these objectives while keeping the engine compact, lightweight, and cost-effective is a significant challenge, but one that engineers have been working on for years with great success.
Air compressor
An air compressor can be a game-changer when it comes to powering various tools and equipment for DIY projects or in industrial settings. However, before purchasing an air compressor, it’s important to consider your specific requirements. One of the main considerations is the air compression level needed for your tools.
This is measured in PSI or pounds per square inch and should be matched to your tools’ requirements. Additionally, you should consider the tank size, as this will dictate how long you can run your tools before needing to refill the tank. Another important aspect to ponder over is the power source.
While electric compressors are more common, gasoline-powered units are more portable and versatile. Lastly, don’t forget about your budget; while it may be tempting to go for the cheapest option, investing in a quality compressor will save you money in the long run and ensure a reliable and safe power source for your equipment.
Air receiver tank
When it comes to ensuring the safe and efficient operation of air compressors, air receiver tanks play a pivotal role. In fact, these tanks are so crucial that in some cases, they’re mandated by law. But what exactly are the requirements that air receiver tanks must meet? First and foremost, they need to have a capacity that’s sufficient for the amount of air being compressed.
They also need to be designed to withstand the pressure exerted by the compressor and have safety features such as pressure relief valves and gauges. Additionally, they should be made from materials that are suitable for the application and environment, such as stainless steel or carbon steel. When properly selected and maintained, air receiver tanks can help prolong the life of compressors and reduce energy consumption while enhancing safety and performance.
So before you invest in an air compressor, be sure to give careful consideration to the air receiver tank that you’ll pair with it.
Unloader valve
An unloader valve is an essential component of any pressure washer system as it helps control the amount of pressure exerted by the pump. It is responsible for releasing the built-up pressure when the trigger is not engaged, preventing the motor from overworking and prolonging the life of the equipment. Optimal water flow and pressure output during cleaning tasks are essential for any pressure washer, and an unloader valve plays a crucial role in ensuring this.
When selecting an unloader valve, it is essential to consider specific requirements such as maximum pressure, flow rate, and compatibility with the pressure washer system. Choosing the right unloader valve will ensure that your pressure washer system performs optimally, and you get the best results. Neglecting to install an unloader valve can result in higher energy costs, lower efficiency, and premature equipment failure.
Therefore, it is vital to invest in a high-quality unloader valve to ensure safe and reliable operation.
Steps
If you’re looking for a powerful air compressor that can handle heavy-duty tasks, you might want to consider making a gas-powered one. Here’s how to make a gas-powered air compressor despite the intimidating prospect that it might seem. First, you need to choose an engine suitable for your needs, which can range from a small lawn mower engine to a powerful V
Next, you’ll need to select a compressor pump that can deliver the air volume and pressure you require. Once these two components are chosen, you’ll need to mount them onto a sturdy frame that can support their weight. Finally, you’ll need to connect the engine and pump with a belt or chain and install an air storage tank and appropriate airflow and fueling systems to complete your gas powered air compressor.
Remember, always follow safety regulations when working on gas engines, and always test your work before operating the compressor. With these steps, you can enjoy the power and convenience of a gas-powered air compressor for your bigger projects.
Step 1: Attaching the gasoline engine to the air compressor
If you’re looking to power your air compressor with a gasoline engine, the first step is to attach the engine to the compressor. This may seem daunting, but it’s actually a fairly simple process. First, make sure your engine is securely mounted on a stable surface.
Then, locate the flywheel on your compressor and remove its protective cover. You’ll need to remove the nut that secures the compressor pulley to the flywheel and attach the engine’s pulley to the flywheel with a vice grip or similar tool. Tighten the new pulley down with a bolt and washer, following the instructions provided with the engine.
Finally, tighten the newly attached pulley to the compressor shaft with a wrench. With these steps complete, you’re well on your way to powering your air compressor with gasoline!
Step 2: Mounting the air receiver tank
After choosing the perfect spot for your air compressor, it’s time to mount the air receiver tank. The air receiver tank is an essential component of your compressor system, as it stores compressed air to be used later. First, ensure that the tank is placed in a secure location, and use a level to ensure that it is straight and balanced.
Once you’ve found a suitable position, it’s time to start mounting the tank. You will need to attach the mounting brackets to the tank and then attach them to the wall using the appropriate screws. It’s important to make sure that the screws are securely fastened to the wall, as the weight of the tank can be significant.
Tighten all nuts and bolts, and don’t forget to adjust the safety valve and pressure switch according to the manufacturer’s instructions. With the receiver tank mounted securely in place, you’re one step closer to a fully functional air compressor system.
Step 3: Installing unloader valve
Now that we have attached the pressure switch and safety valve, it’s time to install the unloader valve. This valve plays a crucial role in allowing the compressor to start and stop efficiently. First, find a suitable location on the compressor where the valve can be easily accessed.
Next, remove the valve from its packaging and attach it to the compressor using the fittings provided. It’s important to ensure that all connections are tight and secure to prevent air leaks. Once you have installed the unloader valve, turn on the compressor and verify that it is functioning correctly.
By installing the unloader valve, you can help prolong the lifespan of your compressor and ensure that it runs efficiently for years to come. So, take your time and make sure to carefully install the unloader valve to maximize the benefits of your compressor.
Step 4: Connecting all parts together
Connecting all the parts together is the final step in creating your own PC. Before you start, make sure you have all the necessary components like the motherboard, power supply, CPU, RAM, graphics card, and other peripherals. First, take the motherboard and place it on a flat surface.
Then attach the processor, RAM, and cooling fan to the motherboard. Once that is done, secure the motherboard to the case with screws. Next, connect the power supply to the motherboard, making sure to match the cable connectors.
After that, install the graphics card and any other peripherals like the hard drives and SSDs. Finally, connect all the cables from the peripherals to the motherboard, graphics card, and power supply. Once you’ve connected everything, you can close the case and power on your newly built PC.
It’s an excitement-filled moment, so make sure to double-check all the connections before you hit the power button.
Conclusion
And there you have it, folks! With just a bit of elbow grease, some basic knowledge of mechanics, and a love for the sounds of whirring gears, you too can make your very own gas powered air compressor. So why settle for store-bought when you can build it yourself and impress all your friends with your DIY skills and air compressor knowledge? Plus, nothing beats the feeling of starting up your very own creation and hearing that satisfying hiss of compressed air. So get to it and let your inner engineer shine!”
Safety precautions
When it comes to safety precautions, there are several important steps you should take to keep yourself and others protected. First and foremost, always be aware of your surroundings and potential hazards. This means keeping an eye out for obstacles, uneven surfaces, and potential trip or slip hazards.
Additionally, make sure you are wearing the appropriate safety gear for your activity, whether that be a helmet, gloves, or sturdy shoes. Another key step is to stay hydrated and take breaks as needed, as fatigue and dehydration can increase your risk for accidents. Finally, it’s important to follow all safety guidelines and regulations for your activity or workplace, such as proper use of equipment and following established procedures.
By taking these steps and staying alert and cautious, you can help prevent accidents and injuries and keep yourself and those around you safe.
Testing and troubleshooting tips
Testing and troubleshooting can be a time-consuming task, but it is essential to ensure smooth operations and avoid any unforeseen issues. The first step is to have a thorough understanding of the problem and gather all the necessary information. This includes reviewing any error messages or logs, identifying when the problem occurred, and any changes made to the system.
Once you have the necessary information, it is time to reproduce the issue and try to isolate the problem. You can do this by using various testing tools and techniques, such as unit testing, integration testing, or performance testing, depending on the nature of the problem. When you identify the root cause of the issue, you can start to troubleshoot and fix the problem.
This may require running various tests, modifying code, or making changes to the system’s configuration. Finally, testing the fix and ensuring it resolved the issue is crucial before deploying it to the production environment. By following these steps, you can improve your overall testing and troubleshooting process and ensure your systems are running efficiently and effectively.
FAQs
What are the advantages of a gas powered air compressor over an electric one?
Gas powered air compressors provide more power and mobility than electric ones, making them ideal for use in remote areas or on job sites without readily available electrical outlets. They also tend to last longer and require less maintenance.
What kind of fuel do gas powered air compressors use?
Most gas powered air compressors run on regular gasoline, although some larger models may require diesel fuel.
How do you maintain a gas powered air compressor?
Regular maintenance for a gas powered air compressor includes changing the oil on a regular basis, checking and replacing air filters, and ensuring proper fuel and oil levels. It’s also important to inspect the compressor regularly for any signs of wear and tear or damage.
Can gas powered air compressors be used indoors?
No, gas powered air compressors should only be used in well-ventilated outdoor areas due to the potential for carbon monoxide buildup.
What kind of jobs are gas powered air compressors typically used for?
Gas powered air compressors are often used for jobs that require high levels of mobility and portability, such as road construction, roofing, and outdoor painting.
How do you start a gas powered air compressor?
To start a gas powered air compressor, check the oil and fuel levels, pull the starter cord or turn the key (if equipped), and let the compressor warm up for a few minutes before use.
What should you do if a gas powered air compressor won’t start?
If a gas powered air compressor won’t start, first check the fuel and oil levels, and make sure the spark plug is clean and properly gapped. If those things don’t work, it may be a problem with the carburetor or ignition system, and it’s best to have a professional diagnose and repair the problem.