How to Read Air Compressor Gauges: A Step-by-Step Guide for Beginners
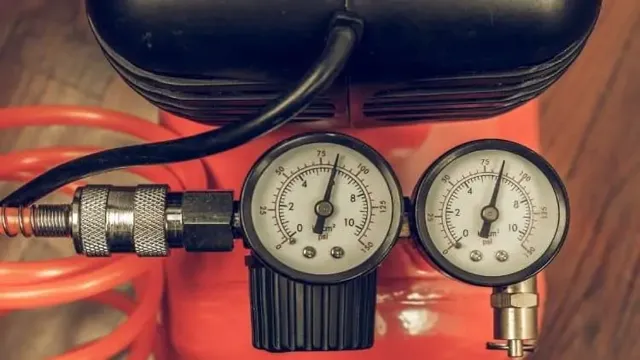
If you’re a regular user of an air compressor, then being able to read your air compressor gauges is essential. These gauges give you important information about the air pressure and flow rate of your compressor, ensuring that you can use it safely and effectively. However, if you’re new to air compressors, it can be confusing to understand what all of the different numbers and symbols on the gauges mean.
Don’t worry, though – in this blog post, we’re going to show you exactly how to read air compressor gauges. By the time you’re done reading, you’ll be able to interpret your gauges like a pro!
What are Air Compressor Gauges?
Air compressor gauges are essential tools that display the air pressure inside your compressor tank. They come in different shapes and sizes, but all share the same purpose: to help you ensure your equipment is running smoothly and efficiently. Knowing how to read air compressor gauges is critical, as it can help you avoid common issues such as low airflow, compressor damage, or even catastrophic tank failure.
The primary reading on your gauge is the pressure level, which is measured in pounds per square inch (PSI). Some gauges show additional information, such as the temperature or airflow rate, depending on the type of compressor you have. If you don’t know how to read your gauge, consult your compressor manual or a knowledgeable professional.
With proper knowledge and maintenance, your air compressor can last for many years and provide you with reliable performance for your various projects.
Definition and Function
Air compressor gauges are essential tools for measuring and regulating the air pressure in your compressor. These gauges can be analog or digital and are usually located on the control panel of the compressor. They measure the pressure of the air flowing through the compressor and display it in units of PSI or bar.
This measurement is crucial in ensuring that the compressor operates within safe limits and doesn’t cause any damage or accidents. Air compressor gauges can also be used to monitor the air pressure in pneumatic systems such as air-powered tools. They are designed to withstand high pressures and can be calibrated to ensure accuracy.
In summary, air compressor gauges are important components of any air compressor and should be checked regularly to ensure proper function and safety.
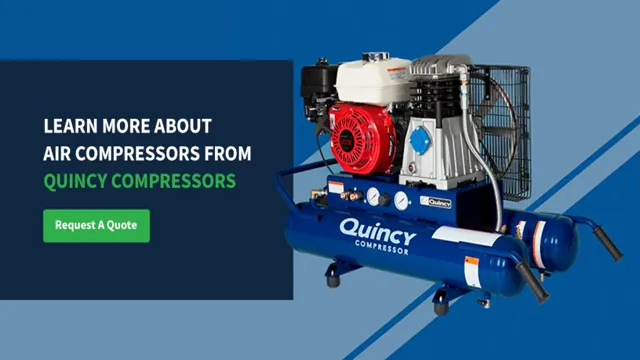
Types of Air Compressor Gauges
Air compressor gauges are critical components that indicate the pressure of air being generated by the compressor. These gauges help users to regulate the pressure and ensure that it remains within safe operating limits. There are various types of air compressor gauges available in the market, each with its own features and functions.
The most widely used gauge is the analog gauge, which uses a needle to indicate the pressure on a dial, while the digital gauge displays the reading on an LCD screen. Furthermore, pressure switch gauges are used to control the on and off switch of the compressor, while differential gauges are designed to measure the pressure difference between two points. It’s important to choose the right type of air compressor gauge to ensure accurate readings and proper functionality of the compressor system.
Installing a high-quality gauge will help you to maintain the optimal pressure and avoid damage to your equipment, while ensuring your safety.
Reading Air Compressor Gauges
If you own an air compressor, it’s vital to know how to read its gauges properly. The primary gauge on the air compressor is the pressure gauge, which indicates the pressure of the air inside the tank in PSI or BAR. The secondary gauge is the regulator gauge, which usually indicates the pressure allotted to the tool or device being used.
To read the gauge, you need to identify the PSI or BAR reading on the gauge. The PSI or BAR value displayed on the pressure gauge should be equal to or above the recommended pressure set by the tool manufacturer. It’s also essential to note that the pressure reading will fluctuate when the compressor is turned on or off, but it should remain within a specific range.
Overall, understanding how to read air compressor gauges is crucial for safety and efficiency when using compressed air tools.
Step-by-Step Process
When it comes to using an air compressor, one important component is reading the gauges. The gauges can give you valuable information, such as the current air pressure and how much pressure is in reserve. To start reading the gauges, locate the main pressure gauge, usually located on the front of the compressor unit.
This gauge displays the current pressure in PSI, or pounds per square inch. The reserve gauge, located next to the main gauge, displays the maximum pressure that has been reached since the last use. To ensure accuracy, it’s important to regularly check and calibrate the gauges.
By doing so, you can prevent overinflation or underinflation of your tires or other tools, prolonging their lifespan. With a clear understanding of how to read your air compressor gauges, you’ll be able to safely and effectively use your equipment.
Understanding the PSI and CFM Readings
An air compressor is an essential tool that can be used for multiple purposes in a workshop or any construction site. Understanding the two readings on an air compressor gauge, PSI, and CFM, is crucial for getting the most out of your air compressor. PSI refers to pounds per square inch of pressure that an air compressor can deliver, while CFM refers to cubic feet per minute of air that an air compressor can supply.
PSI indicates the force of air delivery that can be sufficient for powering tools such as drills, paint sprayers, or construction nailers. On the other hand, CFM signifies the amount of air supply that can be used for powering up pneumatic tools and the rate of air delivery. The combination of both PSI and CFM readings determines the overall performance and output of the air compressor.
It is essential to select the right air compressor based on the PSI and CFM requirements for the intended application. Always remember that higher PSI ratings enable more powerful tools, while higher CFM ratings provide a longer running time.
Interpreting the Gauges
When it comes to using an air compressor, understanding how to read the gauges is a crucial aspect. The two gauges on an air compressor are the tank pressure gauge and the regulator gauge. The tank pressure gauge displays the air pressure level inside the compressor tank, while the regulator gauge measures the pressure coming out of the compressor.
It is important to keep an eye on these gauges during operation to ensure that the pressure level is within the recommended range. If the pressure level gets too low, it can cause damage to the compressor or make it inefficient. On the other hand, if the pressure level is too high, it can cause safety hazards and damage to the equipment being used.
By monitoring the gauges, you can maintain the correct air pressure level for safe use and optimal performance.
Maintenance of Air Compressor Gauges
Air compressor gauges are an essential part of any compressed air system. They allow you to monitor the pressure inside your air tank and ensure that your compressor is running at the correct pressure level. However, it’s important to know how to read air compressor gauges and to maintain them properly to ensure their accuracy.
When reading the gauge, make sure to look at the needle’s position and the numbers representing the pressure. When the needle is in the green zone, the pressure is good. However, if it’s in the red zone or past the recommended pressure limit, you should stop using the compressor until the issue is resolved.
To maintain the accuracy of the gauge, it’s important to keep it clean and free of debris. Over time, the gauge may also need to be recalibrated or replaced. Regular maintenance and proper usage of air compressor gauges can help keep your system running smoothly and safely.
Cleaning and Calibration Tips
Air compressor gauges are important parts of any compressed air system, as they monitor the pressure levels within the tank and regulate the output accordingly. However, just like any other component, they require regular maintenance to perform optimally. Cleaning should be done periodically using a soft, damp cloth to remove any dirt or debris that may have accumulated on the gauge face.
Calibration is also important to ensure accuracy – use a pressure gauge tester to compare your gauge reading with that of a trusted source. If the readings don’t match up, you may need to adjust the gauge or replace it altogether. By taking care of your air compressor gauges, you can ensure that your compressed air system operates efficiently and reliably, so don’t neglect this important maintenance task.
Signs of Malfunctioning Gauges
Air compressor gauges are crucial components of any compressed air system(AC system). A gauge’s primary job is to measure the pressure inside the compressor’s tank and allow the operator to know when the pressure has reached a certain level. Unfortunately, gauges can malfunction if they are not correctly maintained, causing inaccurate readings and potentially leading to equipment failure.
Some common signs of malfunctioning gauges include erratic readings, sticking needles, or consistently reading high or low pressure. Regular maintenance is essential to keep air compressor gauges functioning correctly. This includes making sure they are correctly calibrated, free of dirt or debris and are regularly inspected for damage.
Neglecting to maintain your gauges can result in costly repairs and downtime. Thus, ensuring your gauges are intact and regularly checked should be an essential part of any compressed air system’s maintenance routine.
Conclusion
In conclusion, reading air compressor gauges may seem daunting at first, but like most things in life, it’s all about taking accurate measurements. With a little practice and a keen eye, you’ll soon become an expert at interpreting the numbers displayed on those gauges. Just remember: the pressure is on, so don’t let it get to your head.
Keep a cool head, take your time, and you’ll be reading those gauges like a pro in no time!”
FAQs
What are the different types of air compressor gauges?
There are two main types of air compressor gauges: mechanical gauges and digital gauges.
How do I read a mechanical air compressor gauge?
Mechanical gauges typically have a needle that moves along a scale to indicate the pressure. Simply read the pressure indicated by where the needle points.
How do I read a digital air compressor gauge?
Digital gauges display the pressure numerically on a screen. Simply read the number displayed to determine the pressure.
Why is it important to regularly check the air compressor gauge?
Regularly checking the air compressor gauge ensures that the compressor is running at the correct pressure, which is important for optimal performance and to prevent damage to the compressor.
What is the ideal pressure range for an air compressor?
The ideal pressure range for an air compressor depends on the specific compressor and the tools or equipment being used. Check the manufacturer’s specifications for the recommended pressure range.
How do I calibrate an air compressor gauge?
To calibrate a mechanical gauge, use a known accurate gauge to compare the readings and adjust as necessary. Digital gauges usually have a calibration function that can be accessed through the settings menu.
Can I replace a faulty air compressor gauge myself?
Yes, a faulty air compressor gauge can usually be replaced by following the manufacturer’s instructions. However, if you are unsure or uncomfortable with the process, it is best to consult a professional.