How to Remove Wobble from Drill Press: Easy Steps for Precise Drilling
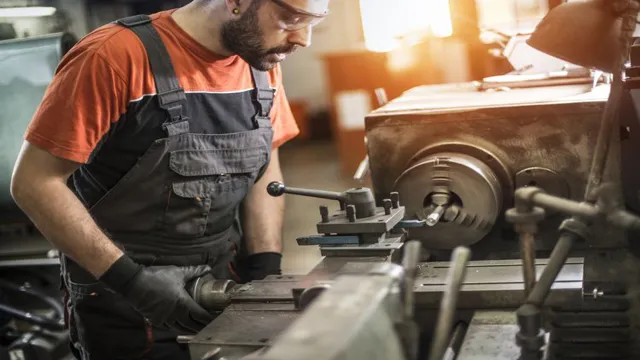
Have you ever felt frustrated when your drill press wobbles? It’s not just an annoyance – it can affect the precision and accuracy of your projects. Fortunately, there are several ways to remove wobble from your drill press and ensure it functions smoothly. Firstly, check the chuck and make sure it’s properly tightened.
If it’s loose, even slightly, it can cause wobbling. You can use a chuck key or wrench to tighten it, and make sure it’s snug. Another cause of wobbling could be a bent or damaged spindle.
In this case, you may need to replace the spindle altogether. Vibration can also lead to wobbling, so make sure your drill press is properly mounted and stable. This can be done by tightening all screws and bolts, or even adding weights to the base.
Lastly, make sure you’re using the correct drill bits for the task at hand. Using the wrong size or type of bit can cause your drill press to wobble. By following these tips and tricks, you can remove wobble from your drill press and ensure it runs smoothly for all your future projects.
Introduction
Are you frustrated with your drill press wobbling during use? Wobbling can not only create an uneven surface but can also be dangerous. Fortunately, there are ways to remove the wobble from your drill press. One common cause of wobbling is a loose chuck, which can be tightened with a chuck key.
Make sure to remove any debris or metal shavings from inside the chuck before tightening. Another cause of wobbling can be a dull or improperly inserted drill bit. Check and replace the drill bit if necessary.
Additionally, a bent spindle can also cause wobbling. If this is the case, it may be best to seek professional help. By following these simple steps, you can remove wobble from your drill press and achieve precise and safe drilling every time.
Explanation of drill press wobble
If you’re a DIY enthusiast or a professional woodworker, you probably know how important a drill press is for your workshop. However, despite being an essential tool, drill presses can sometimes exhibit wobbling issues that can make drilling difficult and compromise the quality of your work. Drill press wobble refers to the side-to-side movement of the drill chuck that results in the bit rotating off-center.
This issue is not only frustrating but can also be dangerous, leading to inaccurate drilling and potential tool damage. The most common cause of drill press wobble is a misaligned chuck, and it’s essential to fix this problem to ensure your drill press is operating at its best.
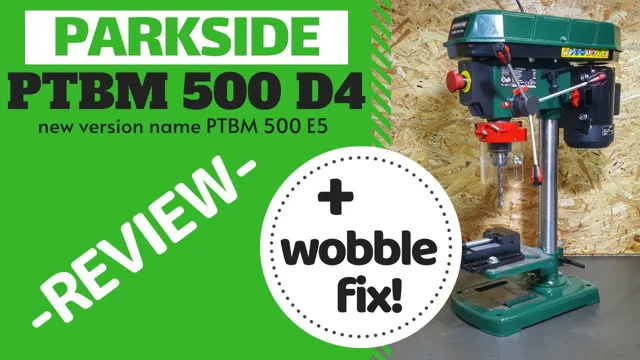
Importance of removing wobble
When it comes to shooting high-quality videos, removing wobble is crucial. Wobble refers to the unwanted movement of the camera that can result in shaky footage. Not only can this decrease the overall quality of the video, but it can also be distracting and even cause motion sickness for viewers.
This is where stabilization technology comes in, which can reduce or eliminate wobble, resulting in smoother and more professional-looking footage. Investing in a camera or software with stabilization features can make all the difference in the final product. So, whether you’re a professional filmmaker or a hobbyist, removing wobble should be a top priority to ensure the best possible video.
Check the Chuck
If you’ve noticed a wobble in your drill press, don’t worry – it’s a common issue that can be easily fixed. The first step in removing wobble from your drill press is to check the chuck. The chuck is the part that holds the drill bit, and if it’s not properly mounted or is damaged, it can cause your drill bit to wobble.
First, make sure the chuck is securely fastened to the drill press spindle. If it feels loose, tighten it with a chuck key or wrench. If the chuck is securely mounted, check to see if it’s damaged.
Look for cracks or chips in the jaws of the chuck, which can cause the drill bit to not be held tightly and wiggle during use. If there is damage to the chuck, replace it with a new one to resolve the wobble issue. By checking the chuck and ensuring it’s properly mounted and undamaged, you can quickly and easily fix any wobble issues with your drill press.
Inspect the chuck for damage
When it comes to inspecting the chuck of your power tool, it’s important to take your time and closely examine it for any potential damage. The chuck is a vital component of your rotary tool that keeps the drill bits or attachments securely in place during use. If the chuck is damaged in any way, it could compromise the safety and effectiveness of your tool.
It’s crucial to check for any cracks, chips, or other signs of wear and tear, especially around the jaws or threading. Don’t forget to give the chuck a good cleaning to remove any debris or buildup that might affect its performance. By taking the time to inspect and maintain your chuck, you can ensure that your power tool is functioning at its best and, most importantly, keeping you safe while you work.
Remove and clean the chuck
When it comes to maintaining your power drill, checking the chuck is an essential part of the process. The chuck is responsible for holding your drill bits in place securely, so ensuring it’s in good condition is crucial for completing any drilling project successfully. Before starting any work, it’s essential to remove and clean the chuck properly to prevent any debris or dirt from affecting its performance.
First, loosen the chuck by turning it counterclockwise and removing any bit that may be still attached. Once it’s free, use a soft cloth and some cleaning solution to remove any dirt or debris that may have built up over time. Afterward, inspect the chuck to ensure there are no visible cracks or damages that could affect its grip or functionality.
By taking the time to check and clean your chuck regularly, you’ll ensure it lasts longer and performs optimally, making all your drilling projects a breeze.
Reinstall the chuck securely
The chuck is a crucial component of any drill or rotary tool, so it’s important to regularly check the chuck and ensure that it’s secure. If your chuck feels loose or wobbly, it’s possible that it could fly off during use and cause injury or damage. To check the chuck, start by removing any bits or attachments and inspecting it for any visible damage or wear.
Next, tighten the chuck by gripping it firmly and turning it clockwise to ensure that it’s securely attached. If the chuck still feels loose, try cleaning the area around it to remove any dirt or debris that might be preventing it from tightening properly. If all else fails, consider reinstalling the chuck securely to ensure that it’s firmly attached to your tool.
With a securely attached chuck, you can feel confident in using your drill or rotary tool for any project or task.
Check the Spindle
If you’re experiencing wobble when using your drill press, the first thing you should check is the spindle. A loose or poorly fitted spindle can lead to wobbling, which can be dangerous and affect the quality of your work. To check the spindle, turn off the drill press and remove the chuck.
Check for any obvious signs of damage or wear, such as cracks or corrosion. Then, reattach the chuck and tighten it fully with a chuck key. If the wobbling persists, you may need to replace the spindle or chuck entirely.
Remember, safety should always come first when working with power tools, so never hesitate to seek professional help if you’re unsure about any aspect of your drill press.
Clean the spindle and arbor
When it comes to maintaining your equipment, one area you should always inspect is the spindle and arbor. These components are essential for keeping your machinery running smoothly. One way to ensure their longevity is by keeping them clean.
Over time, debris and residue can build up, causing problems down the line. To solve this issue, begin by removing any visible debris using a brush or compressed air. Next, wipe down the spindle and arbor with a clean cloth, being sure to get into any crevices.
You can also use a degreaser for a more thorough clean. Check the spindle for any signs of wear or damage, such as cracking or bending, as these can cause issues during operation. By regularly inspecting and cleaning your spindle and arbor, you can extend the life of your machinery and avoid costly repairs in the future.
Inspect the spindle for damage
When it comes to maintaining the performance and longevity of your machine tool, checking the spindle for damage should be on the top of your list. The spindle is responsible for rotating the cutting tool and transferring power to other components of your machine tool. It is critical to inspect the spindle regularly to ensure it is in good condition, preventing any disruptions that can negatively impact the precision and reliability of your machining operations.
Examine the spindle for signs of wear and tear, such as cracks, pits, or corrosion, that can lead to reduced performance or complete failure. A damaged spindle can adversely affect your machining processes, increase downtime, and cause you to invest in costly repairs or replacements. Therefore, schedule routine checks to ensure your spindle is always in optimum condition, avoiding any unintended and costly consequences.
Remember, keeping your spindle healthy is central to a smoothly running and effective machine tool.
Replace the spindle if necessary
When it comes to checking the spindle, it’s important to be thorough and vigilant. A worn or damaged spindle can cause serious problems for your machinery and can even result in safety hazards. Start by inspecting the spindle for any signs of wear or damage, such as cracks, chips, or deformities.
You’ll also want to check for any excessive vibration, which could indicate an issue with the spindle. If you do notice any problems, it’s important to replace the spindle as soon as possible. Don’t try to make do with a faulty spindle, as this can lead to even more problems down the line.
By being proactive and checking your spindle regularly, you can ensure that your machinery stays in top working order and that your operations run as smoothly as possible. So, when it comes to maintaining your equipment, always prioritize spindle health and replace it if necessary.
Check the Table and Base
If your drill press is wobbling, the problem could be with the table and base. Firstly, ensure that the table is level and adjusted properly. Use a spirit level to check if the table is flat.
If it’s not, adjust the screws on the side or back of the table until it is level. Next, check the base of the drill press. If it’s not secured tightly to the ground, it can cause wobbling.
Make sure that the base is on a stable surface and use a clamp or bolt to secure it. If the problem persists, check for worn bearings in the spindle and motor. A loose belt can also cause wobbling, so ensure that it’s tight.
With these steps, you should be able to remove the wobble from your drill press.
Inspect the table and base for damage
When it comes to inspecting a table and its base, it’s essential to check for any signs of damage. Make sure to assess the table’s surface for scratches, gouges, or any cracks that may have developed over time. You’ll also want to give the base a thorough once-over, checking for any loose screws or bolts and any wobbliness in the legs.
Besides, check for rust, corrosion, or any signs of structural damage that could affect the table’s stability. By assessing the table and base’s condition, you can spot any problems before they turn into more significant issues, ensuring your furniture lasts for years to come. If you come across any issues, address them promptly by tightening screws, replacing damaged parts, or seeking professional help.
A well-maintained table and base can not only enhance the aesthetic appeal of your home but can also provide a safe and sturdy surface for daily use.
Level the table and base
When it comes to setting up a table, it’s important to ensure that it’s level and stable. The first step in achieving this is checking both the table and base. Before placing anything on the table, take the time to check that the legs are all securely fastened and level.
A wobbly table is not only annoying but can also be dangerous, especially if you plan to put heavy objects on it. If you find that there’s a leg that’s uneven, you can use small wedges to level it out. You can also use a leveling tool to check if the table is balanced.
A stable table ensures that you’ll have a comfortable and safe working surface, whether you’re using it for eating, working, or studying. So take a few minutes to check and adjust your table and base, and you’ll avoid any mishaps in the future.
Conclusion
In conclusion, removing a wobble from your drill press might seem like a daunting task, but with a little patience and the right tools, you can have it running smoothly in no time. Just remember to check for any loose parts, clean and lubricate the spindle, and make sure your drill bits are properly secured. And if all else fails, don’t be afraid to give your drill press a stern talking to – sometimes a good pep talk is all it takes to get it back on track.
Happy drilling!”
Importance of regular maintenance
When it comes to regular maintenance of your table saw, you don’t want to overlook the importance of checking the table and base. These two components are crucial for ensuring accurate and safe cuts. Start by examining the table for any visible damage or wear, such as scratches, dents, or warping.
A damaged table can cause your wood to catch or kickback during a cut, leading to safety hazards. Next, check the base for stability, especially if you have a portable saw. Loose or wobbly bases can cause inaccurate cuts and increase the risk of injury.
By taking the time to regularly check your table and base, you can ensure that your table saw is working at its best and avoid any potential safety risks. Remember to always prioritize safety when using power tools.
FAQs
What causes wobbling in a drill press?
There could be several reasons for a wobbling drill press, including an unbalanced chuck or a bent spindle.
How can I fix a wobbling drill press?
To fix a wobbling drill press, first, identify the cause, then take appropriate steps such as replacing a bent spindle or adjusting the chuck to balance it.
Can an unbalanced drill bit cause wobbling in a drill press?
Yes, unbalanced drill bits can cause wobbling in a drill press. Using a balanced drill bit can help to reduce or eliminate wobbling.
Is it safe to use a drill press that wobbles?
No, it is not safe to use a drill press that wobbles as it could lead to inaccuracies and even cause injury.
How often should I perform maintenance on my drill press to prevent wobbling?
Regular maintenance of a drill press is essential to prevent wobbling. It is recommended to clean and inspect it after every use and perform a more thorough inspection once every six months.
Can using the wrong speed setting on a drill press cause wobbling?
Yes, using the wrong speed setting on a drill press can cause wobbling. It’s important to use the correct speed for the material being drilled to avoid wobbling and other issues.
Is it necessary to use a drill press table to prevent wobbling?
Using a drill press table can help to prevent wobbling, especially if it has a larger surface area for support. However, it’s not the only factor that affects wobbling in a drill press.