How to Replace Bearings in a Drill Press – A Step-by-Step Guide for DIYers
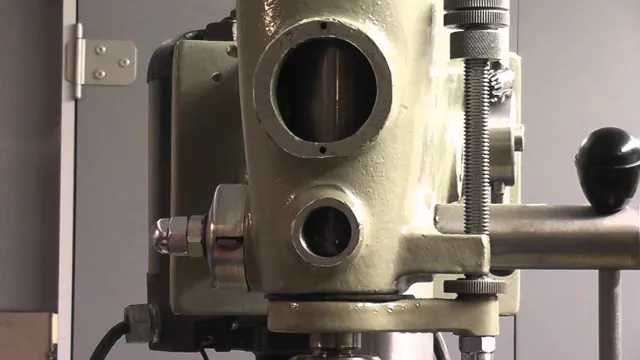
Have you ever noticed that your drill press isn’t working as smoothly as it used to? If so, the problem may be damaged bearings. These small components are crucial for ensuring your drill press operates effectively. Over time, bearings can wear out, causing your drill press to become noisy or even stop working altogether.
If you’re experiencing these issues, fear not – replacing the bearings in your drill press is easier than you might think. In this blog post, we’ll guide you through the process step by step, so you can get back to tackling your next DIY project without any hiccups. So grab your trusty wrench and let’s get started!
Gather Necessary Tools and Materials
When it comes to replacing bearings in a drill press, it’s important to gather all the necessary tools and materials before beginning the process. You’ll need a set of wrenches, pliers, a screwdriver, a hammer, a bearing puller, and replacement bearings that match the size and type of the original ones. It’s also a good idea to have some lubricant on hand to ensure the new bearings operate smoothly.
Before diving in, take the time to read through the manufacturer’s instructions for your specific drill press and make sure you understand the steps involved. Having all the required tools and materials set up and ready to go can make the process run more smoothly and help you avoid any unwanted complications along the way. So, gather everything you need and let’s get started on replacing those worn out bearings!
List of required tools and materials
To get started with your new project, you’ll need to gather the necessary tools and materials. Depending on the project, these items can vary greatly, so it’s important to know exactly what you need. First, consider what tools will be required.
This could include hammers, screwdrivers, saws, drills, and tape measures, among others. Additionally, make sure you have safety equipment like goggles, gloves, and a first-aid kit. Next, think about the materials needed to complete the project.
This could include wood, nails or screws, glue, paint, or fabrics. Don’t forget about any specialized materials required, such as plumbing or electrical supplies. Make a checklist and gather everything before beginning the project to ensure you have everything you need.
By being prepared with the right tools and materials, you’ll be well on your way to successfully completing your project!

Disassembling the Drill Press
Replacing the bearings in your drill press might seem like a daunting task, but with a few tools and the right steps, it can be done easily. The first step is to disassemble the drill press carefully. Start by unplugging the machine and removing the chuck and motor.
Then, remove the belt by loosening the tension screw. After that, remove the pulley from the shaft. To access the bearings, remove the top cover and the quill.
It is now possible to remove the spindle and disassemble it to get to the bearings. Be sure to clean all the parts with a degreaser before replacing the bearings. Install the new bearings and reassemble the drill press in the reverse order of disassembly.
You’ll be surprised at how a simple task like this can restore your drill press to peak performance.
Step-by-step guide to disassembling the drill press
Disassembling a drill press may seem like a daunting task, but with the right tools and knowledge, it can be a straightforward process. To begin, make sure to unplug the drill press and remove any accessories or attachments. Next, use a wrench or socket set to remove the chuck and spindle.
It’s important to note that the spindle may be secured by a retaining bolt that needs to be removed beforehand. After the chuck and spindle are removed, take off the belt and pulley. The motor can then be removed by loosening the mounting bolts or screws.
Finally, disassemble the remaining components such as the quill and table. Remember to keep track of all screws and bolts throughout the process and to refer to the drill press manual for any specific instructions. By following these steps, disassembling your drill press can be done safely and efficiently.
Removing the Spindle from the Chuck
When it comes to disassembling the drill press, one important step is removing the spindle from the chuck. This can be a tricky process, but it’s important to do it correctly in order to access other parts of the drill press as needed. First, make sure the drill press is unplugged and that the chuck is fully open.
From there, you can use a spindle removal tool to loosen the spindle and remove it from the chuck. It’s important to take your time with this step and be gentle, so as not to damage the chuck or any of the surrounding components. By following these steps carefully, you can disassemble your drill press safely and with confidence.
Replacing the Bearings
If you are experiencing issues with your drill press, such as excessive noise or vibrations, it may be time to replace the bearings. The process of replacing the bearings can seem intimidating at first, but with the right tools and a bit of know-how, it can be done easily. First, you will need to remove the drill press from its base and take off the pulley cover.
Next, you will need to remove the spindle and disassemble it to access the bearings. Once you have removed the old bearings, be sure to clean the spindle thoroughly before installing new ones. Finally, reassemble the spindle and replace it back into the drill press along with the pulley cover, and you’ll be able to enjoy a smoother and quieter drilling experience.
By following these simple steps, you can successfully replace the bearings in your drill press and keep it running smoothly for years to come.
Identifying and purchasing the correct replacement bearings
When it comes to replacing bearings, it’s important to identify and purchase the correct ones for your specific needs. You don’t want to end up with a part that won’t fit or won’t be able to handle the conditions of your application. So, how do you go about this process? First, you’ll need to determine the dimensions of the bearing you need, including the shaft diameter, housing bore diameter, and overall width.
You’ll also need to consider the type of bearing you need, such as ball bearings, roller bearings, or sleeve bearings. Make sure to also consider other factors such as load capacity, operating temperature, and speed requirements. Once you have all this information, you’re ready to start searching for a replacement bearing.
Look for a reputable supplier who can provide high-quality bearings that meet your exact specifications. With the right replacement bearing in hand, you can be confident in the longevity and efficiency of your equipment.
Installing the new bearings
Replacing the bearings in your vehicle can be a challenging task, but it’s important to keep them in good condition for optimal performance. Start by removing the old bearings with a puller and cleaning the hub to prepare for the new ones. Then, carefully press the new bearings into place, making sure they are properly inserted before securing them with the retainer.
It’s important to use high-quality bearings that are the correct size and type for your vehicle to ensure proper function and longevity. While it may be tempting to cut corners or use cheaper options, investing in quality bearings will pay off in the long run. By taking the time to properly install new bearings, you can improve your vehicle’s safety and performance on the road.
Reassembling the Drill Press
Replacing the bearings in a drill press can be a tricky task, but with the right tools and a bit of patience, it can be done at home without having to take it to a professional. First, you need to disassemble the drill press, taking care to label and organize all the pieces to make reassembly easier. Next, remove the old bearings and thoroughly clean the spindle and bearing housing.
Once the new bearings are in place and secured, reassemble the drill press and test it out to make sure everything is running smoothly. Remember to lubricate the new bearings to ensure a longer lifespan. By following these steps, you can save money and prolong the life of your drill press.
Step-by-step guide to reassembling the drill press
If you’ve disassembled your drill press to fix a problem or for maintenance and now you’re ready to put it back together, don’t worry, it’s not difficult. Here is a step-by-step guide to help you reassemble your drill press safely and with ease. Firstly, start by checking all the parts and making sure they are clean from debris and free from damages.
Then, attach the central column to the drilling head and tighten the bolts using a wrench. Next, place the base of the press onto a stable surface and fix the column to the base. Double-check the tightness of the bolts.
Now, attach the quill to the column and tighten the bolts. Last but not least, attach the chuck to the quill and tighten it using a chuck key. Voila! Your drill press is now assembled and ready to use for all your DIY and woodworking needs.
Testing the Drill Press
If you’re having trouble with your drill press, it could be the bearings. Fortunately, replacing them isn’t too difficult. First, take off the chuck and remove the spindle from the quill.
Then, remove the bearings and clean out any debris or gunk that may have collected in the housing. Use a press to push in the new bearings, making sure they are properly seated. Finally, reassemble the spindle and chuck, and test the drill press to make sure everything is running smoothly.
Following these steps should have your drill press up and running in no time! Don’t forget to regularly clean and maintain your drill press to prevent future issues.
Tips for checking that the repair was successful
When it comes to testing whether a repair on your drill press has been successful, it is crucial to take the necessary steps to ensure that it is working correctly. To begin, start by powering on the machine and checking to see if it is making any unusual noises or vibrations. Next, adjust the settings and try out a few test drills to see if it is operating smoothly.
You can also test the accuracy by drilling a hole into a piece of wood, measuring the depth and diameter to ensure they are correct. Lastly, check that all of the safety features, such as the emergency stop button, are functioning correctly. By taking these steps, you can rest assured that your repaired drill press is working efficiently and safely.
Remember, when it comes to power tools, safety should always be the top priority.
Conclusion: Proper Maintenance and Care for Your Drill Press
In conclusion, replacing bearings in a drill press may seem like a daunting task, but with the proper tools and technique, it can be done quite easily. Just remember to take your time, stay focused, and always wear protective gear. And who knows, after successfully completing this task, you may just become the resident drill press maintenance expert in your workshop.
So go ahead, spin those bearings and keep drilling to your heart’s content!”
FAQs
What are the signs that my drill press bearings need to be replaced?
Signs that your drill press bearings need to be replaced include increased noise and vibration, decreased accuracy and precision, and difficulty in drilling through hard materials.
Can I replace drill press bearings myself or should I seek professional help?
It is possible to replace drill press bearings yourself if you have the right tools and knowledge, but it is also recommended to seek professional help especially if you are not familiar with drill press maintenance.
What tools and materials do I need to replace drill press bearings?
The tools and materials needed to replace drill press bearings include a wrench, pliers, screwdrivers, bearing grease, new bearings, and a press or hammer.
How do I remove old drill press bearings?
To remove old drill press bearings, you need to dismantle the drill press, remove the motor and spindle assembly, and use a press or hammer to gently tap the bearings out of their housing.
How do I install new drill press bearings?
To install new drill press bearings, you need to clean the housing and shaft, apply bearing grease, insert the new bearings, and reassemble the drill press in reverse order.
How often should I replace drill press bearings?
The frequency of replacing drill press bearings depends on the amount of use and maintenance, but it is recommended to replace them every few years or when signs of wear and tear become evident.
What are the benefits of replacing drill press bearings?
The benefits of replacing drill press bearings include improved accuracy and precision, reduced noise and vibration, increased lifespan and durability of the drill press, and smoother operation.