Is your drill press making weird noises or vibrating excessively? These are telltale signs that your bearings may be worn out and need replacement. Replacing drill press bearings is not as complicated as it may seem, and you don’t even need any special tools or skills. In this step-by-step guide, we’ll show you how to replace your drill press bearings like a pro.
First, you need to identify the type of bearings in your drill press. Most drill presses use ball bearings, but some may use sleeve bearings. You can usually find this information in your drill press manual or by contacting the manufacturer.
Next, you need to remove the chuck and spindle from the drill press. This will give you access to the bearings. You may need a special tool to remove the spindle, depending on the model of your drill press.
Once you have access to the bearings, you can remove them using a bearing puller or pry bar. Be careful not to damage the bearing housing or spindle while doing this. Now it’s time to install the new bearings.
Make sure you use the correct size and type of bearings for your drill press. You can find this information in your manual or by contacting the manufacturer. To install the new bearings, you can use a bearing driver or hammer and block of wood.
Be careful not to damage the new bearings while installing them. Finally, reassemble the drill press, making sure everything is tightened and properly lubricated. Turn on the drill press to make sure everything is working smoothly.
Introduction
If you’ve noticed increased vibration or wobbling in your drill press, it may be time to replace the bearings. Thankfully, with some basic tools and a bit of know-how, you can easily replace drill press bearings at home. Start by removing the motor from the mount, then removing the chuck and its collar.
Next, use a bearing puller to remove the old bearings from the quill. Install new bearings and reassemble the press, being careful to align everything correctly. Don’t forget to lubricate the new bearings before using your drill press again.
With a little patience and attention to detail, you can quickly restore your drill press to top condition.
Why Replace Drill Press Bearings?
If you’re someone who is into woodworking or metalworking, you may be familiar with drill presses. Drill presses are essential tools in these industries as they help to make precise holes in various materials. However, like any other machinery, drill presses require maintenance, and one of the key components that play a significant role in the functioning of a drill press is the bearings.
Over time, bearings can get damaged, resulting in wobbling of the drill bit, hindering its performance. Hence, it becomes important to replace drill press bearings at regular intervals to ensure that the tool performs optimally. In this blog, we’ll discuss the reasons why drill press bearings need replacement and how to go about it.
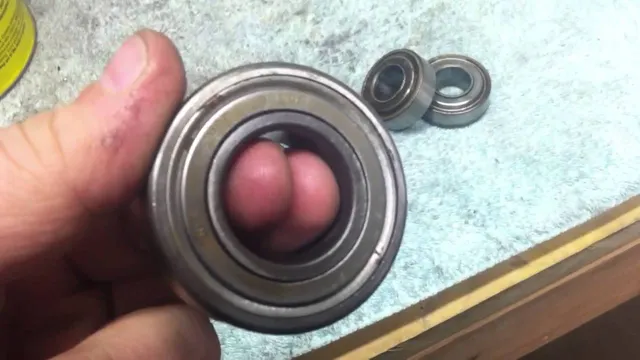
Safety Precautions
When it comes to taking safety precautions, it’s always better to be safe than sorry. Whether you’re at home, work, or out and about, there are always potential hazards that you should be aware of and take steps to minimize. Some common safety precautions include wearing protective gear, following safety protocols, and being mindful of your surroundings.
These precautions are especially important in high-risk industries such as construction, transportation, and healthcare. By taking the time to understand and follow safety guidelines, you can help prevent accidents and injuries from occurring. Remember, safety should always be a top priority in any situation.
Tools and Materials
Replacing drill press bearings can seem like a daunting task, but with the right tools and materials, it can be done easily and efficiently. To start, you’ll need a socket set, pliers, a pry bar, and replacement bearings. First, disconnect the drill press from the power source and remove the drill chuck and spindle.
Next, use a pry bar to remove the covers from the spindle bearings and use pliers to remove the snap rings holding them in place. Carefully remove the old bearings and clean the spindle of any debris or damage. Place the new bearings into position and secure them with snap rings.
Finally, replace the spindle covers and reattach the drill chuck and spindle before reconnecting to the power source. By following these steps, you can successfully replace your drill press bearings and ensure it functions at its best.
Required Tools
When it comes to getting started with a DIY project, having the right tools and materials is essential. There are a few basic tools that you’ll want to have on hand for most projects, including a hammer, screwdrivers, pliers, a level, tape measure, and a saw. If you’re new to DIY, you may want to start with a basic tool kit that includes these items.
As you get more experienced, you may find that you need additional tools for more complex projects. It’s also important to have the right materials on hand, such as screws, nails, wood, and paint. Investing in quality tools and materials will not only make your projects look better, but they’ll also be more durable and last longer.
So before you start your next DIY project, make sure you have all the necessary tools and materials on hand for a successful and enjoyable experience.
Materials
As any DIY enthusiast will know, the right tools and materials are essential for a successful project. Whether you are working with wood, metal, or fabric, having the right supplies on hand can make all the difference in the world. From hammers and screwdrivers to saws and sandpaper, there are a range of tools available to help you bring your vision to life.
The same goes for materials – choosing the right type of material for your project can affect not only the appearance but also the durability and functionality of your finished product. For example, if you are building outdoor furniture, you will want to choose materials that are weather-resistant and able to withstand exposure to the elements. In short, investing in high-quality tools and materials can pay off in the long run by ensuring a successful and long-lasting project.
So, go ahead and take your time researching and selecting the right tools and materials for your next DIY endeavor, it will be worth it in the end!
Removing the Old Bearings
Replacing drill press bearings can be a daunting task, but it’s essential to keep your machine in top working condition. Before you can install new bearings, you must first remove the old ones. The first step is to unplug the drill press from the power source to ensure safety.
Next, remove the chuck by unscrewing it counterclockwise. Then, remove all screws that secure the spindle pulley cover. After this, use a puller tool or a hammer and punch to gently tap the bearings out of the spindle.
Be cautious not to damage the spindle or other surrounding parts during this process. Once the old bearings are removed, clean the area thoroughly, removing any dirt, debris, or grease. This process must be handled with precision and care so as not to cause more damage.
With the old bearings out of the way, you can now move onto the next step in the replacement process.
Steps for Removing the Bearings
Removing bearings from your equipment can be a daunting task, but with the right steps, it can be a seamless process. One of the most crucial steps is removing the old bearings first. To do so, you will need to follow a set of steps, including using a proper tool to remove the retaining ring on the bearing, using a puller to extract the bearing off the shaft, and then repeating the process for the second bearing.
It is essential to be cautious while performing these steps to prevent any damage to the equipment or the new bearings. Once you have successfully removed the old bearings, you are ready to move on to the next phase of the process, which will involve cleaning and preparing the shaft for the new bearings. By following these steps, you can easily remove old bearings and get your equipment running smoothly again.
Tips for Removing the Bearings
When it comes to removing old bearings, there are a few tips to keep in mind to make the process go smoothly and safely. Firstly, it’s important to identify which type of bearing you’re dealing with as this will determine the tools needed to remove it. Some common types of bearings include ball bearings, roller bearings, and needle bearings.
Once you’ve determined the type of bearing, you’ll need to remove any surrounding parts or components to access the bearing itself. This may involve removing seals, snap rings, or retaining clips. Once you have access to the bearing, you can begin the removal process using a suitable puller or press.
It’s important to take your time and use the correct tools to avoid damaging the bearing or surrounding parts. With these tips in mind, you should be able to safely and efficiently remove old bearings and replace them with new ones to keep your machinery running smoothly.
Installing the New Bearings
Replacing drill press bearings may seem like a daunting task, but it’s actually quite simple with the right tools and a bit of know-how. To start, remove the chuck and any other attachments that are connected to the spindle. Carefully take apart the bearing cover, making sure to remember which parts go where.
With the bearings exposed, remove them using a bearing puller or a rubber mallet and a punch. Clean the spindle and bearing housing, removing any debris or old grease. Next, insert the new bearings and align them properly.
You may want to apply a bit of grease to ensure smooth rotation. Once the bearings are in place, reassemble the cover and reattach the chuck. Test the drill press to make sure everything is working properly.
With these steps, you’ll have successfully replaced the drill press bearings and can get back to your DIY projects with confidence!
Steps for Installing the Bearings
Installing new bearings can seem like a daunting task, but with the right steps, anyone can replace them with ease. Firstly, you need to remove the old bearings, clean the area thoroughly, and inspect the bearing housing for any damages. This is important as any imperfections can cause the new bearings to wear out fast.
Secondly, you need to lubricate the bearing housing and the new bearings before fitting them in. It is essential to use the right type of lubricant for efficient performance. Once the new bearings are lubricated, carefully fit them into the bearing housing and ensure they are properly aligned.
Use a torque wrench to tighten the retaining bolts to the recommended torque value. Finally, double-check the bearings for any play and reassemble the machine. Remember to follow the manufacturer’s instructions and maintenance schedule to ensure the longevity of the bearings.
Installing new bearings may seem like a tough job, but following these steps will ensure a smooth and trouble-free experience.
Tips for Installing the Bearings
When it comes to installing new bearings, there are a few tips to keep in mind to ensure the job is done correctly and efficiently. First and foremost, it’s important to choose the right type of bearing for the application and ensure it’s the correct size. Next, it’s crucial to properly clean and prep the mounting surfaces to prevent any debris or contaminants from causing damage to the new bearings.
Once everything is clean and ready, it’s time to install the bearings. One helpful tip is to lightly lubricate the bearings before installation to reduce friction and ensure smooth operation. It’s also important to use the correct tools and techniques for the specific bearing installation to avoid causing any damage.
By following these tips, installing new bearings can be a smooth and successful process that will keep your equipment running smoothly for years to come.
Conclusion and Final Checks
So there you have it, replacing drill press bearings is not rocket science, but it’s definitely not a task for the faint of heart. With the right tools, some technical know-how, and perhaps a bit of grit and determination, you can swap out those old, worn-out bearings for shiny new ones in no time. And who knows, maybe after all that hard work, you’ll swear your trusty drill press feels smoother and more precise than ever before.
Just don’t forget to give yourself a pat on the back (or a cold drink, or both) for a job well done!”
FAQs
What are drill press bearings and what is their function?
Drill press bearings are small metal balls or rollers that help reduce friction and support smooth movement of the drill chuck or spindle.
How do I know if my drill press bearings need replacing?
If you notice any unusual noise, vibration, or difficulty in rotating the chuck or spindle, it may be a sign of worn or damaged bearings that need to be replaced.
Can I replace drill press bearings on my own or do I need to hire a professional?
If you have some mechanical and DIY skills, you may be able to replace drill press bearings on your own with the right tools and instructions. However, if you are not confident or experienced with such tasks, it is recommended to seek the help of a professional.
What are the steps involved in replacing drill press bearings?
The general steps involved in replacing drill press bearings include disassembling the drill press, removing the old bearings, cleaning and lubricating the spindle, installing the new bearings, reassembling the drill press, and testing the new bearings for proper functioning.
Where can I find replacement bearings for my drill press?
You can find replacement bearings for your drill press at hardware stores, online marketplaces, or directly from the manufacturer or distributor. Make sure to check the specifications and compatibility of the bearings before purchasing.
Are there different types or sizes of drill press bearings?
Yes, drill press bearings may vary in size, design, and material depending on the specific model and brand of the drill press. Make sure to choose the right type and size of bearings for your drill press to ensure optimal performance.
How often should I replace my drill press bearings?
The frequency of replacing drill press bearings may depend on various factors such as the frequency and intensity of use, the quality of the bearings, and the maintenance and cleaning practices. As a general guideline, it is recommended to inspect and replace the bearings every 2-3 years or when you notice any signs of wear or damage.