Setting a torque wrench can be a bit tricky, especially if you’re not familiar with the tool. If you need to apply a specific amount of pressure to a bolt or nut, setting the torque wrench correctly is crucial. In this blog, we’ll guide you through the process of setting a torque wrench to 12 pounds.
Whether you’re a DIY enthusiast or a professional mechanic, this guide will come in handy. So buckle up and let’s get started! A torque wrench is a type of wrench that allows you to measure and apply force accurately. This tool is essential when working with components that require precise torque specifications.
A torque wrench is designed to “click” when the desired torque has been reached, letting you know it’s time to stop applying force. To set a torque wrench to 12 pounds, the first step is to loosen the adjustment knob. Next, locate the torque scale on the handle or body of the wrench.
Adjust the scale to 12 pounds by rotating the adjustment knob clockwise or counterclockwise. Once the scale is set to 12 pounds, tighten the adjustment knob to lock in the setting. It’s important to note that not all torque wrenches are the same.
Some may have a lever or a digital readout instead of an adjustment knob. Always refer to the manufacturer’s instructions for your specific model to ensure you’re setting the torque wrench correctly. In conclusion, setting a torque wrench to 12 pounds is a straightforward process if you follow the steps we’ve outlined.
With a little practice, you can master the art of using a torque wrench and achieve precise and accurate results every time.
Introduction
Setting a torque wrench to a specific amount can be tricky, but it’s important for proper tightening and maintenance. For those looking to set a torque wrench to 12 pounds, there are a few steps to follow. First, make sure the torque wrench is calibrated correctly and ready to use.
Then, adjust the torque settings to the desired amount using the manual or digital display on the wrench. Once set, apply the wrench to the bolt or nut and tighten until the wrench clicks or indicates the desired torque has been reached. It’s important to note that torque wrench settings can vary depending on the make and model, so always refer to the manufacturer’s instructions for specific guidance.
With a properly set torque wrench, you can ensure proper tightening and avoid under or over tightening which can lead to mechanical failure or damage.
– Explanation of what a torque wrench is
A torque wrench is a tool used to apply a specific amount of force or torque to a fastener, such as a bolt or nut. This precision tool is essential in many industries and professions, including automotive, aviation, manufacturing, and construction. Unlike regular wrenches that rely on the strength of the user to tighten or loosen a fastener, a torque wrench allows for a specific amount of torque to be applied consistently and accurately.
This prevents over or under tightening, which can cause damage, safety risks, or a decrease in the lifespan of components. With a torque wrench, users can ensure that fasteners are tightened to the correct level of torque, which is critical for the safe and efficient operation of machines, engines, and other equipment.
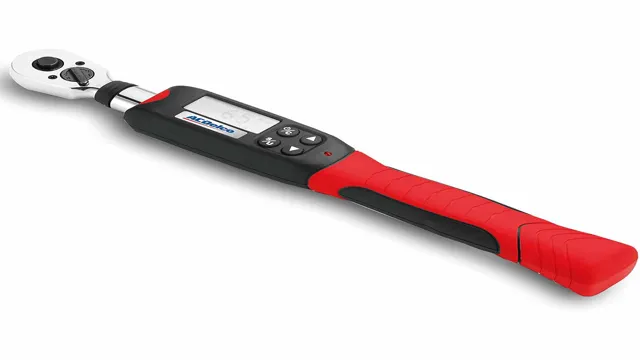
– Importance of setting the right torque for safety and accuracy
Setting the right torque is crucial for both safety and accuracy when working with machinery or equipment that involves fasteners and bolts. This is because the correct torque ensures that bolts are tightened to the required level, preventing them from coming loose or breaking. It is important to note that under-tightening could lead to mechanical failure, while over-tightening could damage the machinery or equipment and pose a potential risk to the operator.
Thus, it is important to set the right torque to ensure safety and accuracy. In this blog post, we will discuss the importance of setting the right torque, how to determine the correct torque setting, and the consequences of not doing so.
Step-by-Step Guide
If you’re wondering how to set a torque wrench to 12 pounds, don’t worry, it’s a simple process that anyone can do. First, make sure your torque wrench is properly calibrated. Then, locate the adjustment mechanism on your wrench.
This may be a rotational dial or a digital display. Next, use the adjustment mechanism to set the wrench to the desired torque value, in this case, 12 pounds. Finally, make sure you’ve properly attached your wrench to the bolt or nut you’ll be tightening and apply pressure until the wrench “clicks” or otherwise indicates that you’ve reached your desired torque.
It’s important to note that torque wrenches are a precision tool, so take your time and use caution to ensure accurate and effective results.
– Check the manufacturer’s instructions for the specific wrench being used
When using a wrench, it’s crucial to refer to the manufacturer’s instructions for the specific wrench being used. This is because different types of wrenches have different tightening specifications, and using the wrong tightening method can result in damage to the equipment or injury to the user. Before using a wrench, make sure you have the correct size for the job at hand.
Next, position the wrench for maximum leverage and grip, ensuring that the wrench is fully seated on the nut or bolt. Tighten the nut or bolt by turning the wrench in a clockwise direction, using a steady and controlled motion. Remember to always use a firm grip, but avoid over-tightening, which can cause the bolt or nut to break or become stripped.
By following these simple steps and referencing the instructions provided by the wrench manufacturer, you can ensure a safe and effective wrenching experience every time.
– Locate the torque setting adjustment on the wrench
If you own a torque wrench, you’ll know how important it is to adjust the torque setting to get the job done just right. The first step is to locate the torque setting adjustment on your wrench. Typically, you’ll find the adjustment on the handle or near the head of the wrench.
Look for a small knob or lever that you can turn or slide. Once you’ve found it, check the wrench’s user manual to determine how to make adjustments. Most torque wrenches have markings that correspond to different torque values.
To adjust the torque, turn the knob or slide the lever until the desired value lines up with the indicator on the wrench. It’s important to use the correct setting to ensure that bolts are tightened properly without being over-tightened, which can cause damage. So take your time, check the manual, and adjust the torque setting carefully to get the best results.
– Turn the adjustment until it reaches the desired pound rating of 12
If you’re looking to adjust the pound rating on your equipment, it can be a bit confusing at first. Luckily, it’s a straightforward process that requires only a bit of attention and the right tools. First off, locate the adjustment mechanism on your equipment – this could be a knob or screw, depending on the model.
Once you’ve found it, turn it in the direction that corresponds with an increase in pound rating. Keep track of your progress by checking the current rating as you go, either by using a scale or by referring to the manufacturer’s specifications. Aim for a rating of 12, but adjust as needed based on your specific needs.
Once you’ve reached your desired rating, finish by tightening or locking the adjustment mechanism so that it stays in place. With a bit of patience and attention, you’ll have your equipment set up exactly as you need it in no time.
– Listen for the click or beep to ensure the wrench is set correctly
When using a torque wrench, it’s crucial to set the correct level of torque for the job at hand. Here’s a step-by-step guide to ensure you’re getting it right every time. First, identify the required torque level for the fastener you’re working on.
Then, adjust the torque wrench to the corresponding level. It’s essential to hold the torque wrench correctly and in the correct orientation for the specific type of fastener you’re working on. Next, apply the torque in a smooth, steady motion.
Finally, listen for the click or beep to ensure the wrench is set correctly. The main keyword, “torque wrench,” should naturally appear throughout the paragraph to emphasize the importance of proper use for this specific tool. Remember that using a torque wrench correctly ensures your fasteners are tightened enough to hold securely without damaging the material.
Tips and Tricks
If you’re wondering how to set a torque wrench to 12 pounds, you’ve come to the right place! First, you need to understand the importance of torque when working on mechanical objects. Torque measures the force applied to rotate an object around an axis, and it’s essential to ensure the object’s parts are firmly attached. To set a torque wrench to 12 pounds, start by checking the manufacturer’s instructions to locate the torque setting adjustment.
Often, you’ll find it near the handle or at the bottom of the tool’s shaft. Then, look for a small lever or knob that adjusts the wrench’s torque. Turn the lever or knob until the arrow or line on the wrench’s scale lines up with the 12-pound setting.
Be sure to adjust it gradually, checking the scale as you go, until it reaches the desired torque setting. Once the wrench is set, it’s ready to use for tightening bolts or fasteners. Don’t forget to check the torque settings and adjust them if necessary before each use, as it’s vital to ensure accuracy and prevent damage to the object.
Happy torque wrenching!
– Calibrate the wrench regularly to maintain accuracy
When it comes to precision work, a calibrated torque wrench is an essential tool. It ensures accurate tightening and avoids under or over-tightening of bolts, which can result in damage or injury. But, even the most precise wrench can lose accuracy over time, so it’s crucial to calibrate it regularly.
Depending on usage, it’s recommended to calibrate a torque wrench every 5,000 or 10,000 cycles or on a yearly basis. Calibration involves comparing the wrench’s reading with a calibrated torque tester to ensure that the readings are accurate. This simple steps helps to maintain the torque wrench’s accuracy, ensuring that it continues to operate efficiently and safely.
So, don’t forget to calibrate your torque wrench regularly to make sure it’s accurate and produces the desired results.
– Store the wrench properly to prevent damage
When it comes to taking care of your tools, one of the most important things to keep in mind is proper storage. This is especially true for wrenches, which are designed to withstand a lot of wear and tear but can still be damaged if not stored correctly. To start, make sure you keep your wrenches in a dry place where they won’t be exposed to moisture or other environmental factors that could cause rust or corrosion.
You should also keep them organized so that you can easily find the right size when you need it. A tool chest or rolling cabinet can be a great option for storing your wrenches, as they provide plenty of space and keep everything in one place. Finally, be careful when handling your wrenches to avoid dropping them or banging them against other tools.
With just a little bit of care and attention, you can keep your wrenches in great condition for years to come.
Conclusion
In conclusion, setting a torque wrench to 12 pounds is a precise task that requires a steady hand and a sharp eye for detail. It’s like performing a delicate surgery on your car or other equipment that needs this specific level of torque. So, when it comes to tightening bolts or nuts to this level, remember to follow the manufacturer’s instructions and use your trusty torque wrench to ensure that everything is tightened to perfection.
And most importantly, don’t forget to apply a touch of humor and creativity to make the whole experience more fun and enjoyable! Happy torquing!”
– Recap on the importance of setting the correct torque for safety and accuracy
Setting the correct torque is vital when it comes to safety and accuracy. It’s important to remember that there are real consequences to not setting the right torque, such as unsafe conditions or improper functioning of equipment. Here are a few tips and tricks to ensure you are setting the correct torque:
Read the manufacturer’s instructions carefully before beginning any task that requires torque. This will help you understand the specific torque requirements for each piece of equipment.
Use a torque wrench to ensure the correct torque is applied. This tool measures the amount of force that is applied to a bolt or nut, helping to prevent over or under-tightening.
Check the torque regularly. As equipment is used, bolts and nuts can loosen over time, so it’s important to periodically check the torque and make any necessary adjustments.
Know the torque specifications for the job. Too often, people are unsure of the specific torque requirements for a task and end up guessing, which can lead to improper functioning and unsafe conditions. By following these tips and tricks, you can ensure that you are setting the correct torque for safety and accuracy.
Remember, taking the time to do so correctly can prevent costly and dangerous mistakes or accidents.
– Encourage readers to share their experiences with using a torque wrench
As someone who has been using a torque wrench for quite some time, I can attest to the fact that it can be quite tricky to get right. However, with a few tips and tricks, anyone can use this tool effectively. Firstly, it’s important to choose the right size torque wrench for the job at hand.
Using the wrong size can lead to incorrect torque readings and potentially damaging the equipment you’re working on. Moreover, it’s crucial to know the torque specifications for the specific task you’re undertaking. This will help you achieve the required torque value and ensure that everything stays in place.
It’s also a good practice to double-check the torque value after the first pass to ensure that it hasn’t changed. Finally, always remember to store the torque wrench in a secure and dry location when not in use to maintain its accuracy and extend its lifespan. So, what are your experiences with using a torque wrench? Have you encountered any difficulties or have any tips to share? Let us know in the comments below.
FAQs
What is a torque wrench and how does it work?
A torque wrench is a tool used to measure and apply a specific amount of force (torque) to a fastener such as a bolt or nut. It works by using a calibrated spring that can be adjusted to a specific torque setting.
What units are used to measure torque on a torque wrench?
Torque can be measured in several units, including foot-pounds (ft-lbs), Newton-meters (Nm), and inch-pounds (in-lbs).
What is the process for setting a torque wrench to a specific torque value?
To set a torque wrench to a specific value, first make sure the tool is properly calibrated. Then, adjust the torque value by turning the handle or dial until the desired torque setting is reached. Be sure to follow the manufacturer’s instructions for your specific torque wrench.
Can a torque wrench be used for both tightening and loosening bolts?
Yes, a torque wrench can be used for both tightening and loosening bolts. When loosening bolts, however, it’s important to set the wrench to its lowest torque setting to avoid over-tightening the bolt when you re-tighten it.
What are some common mistakes to avoid when using a torque wrench?
Some common mistakes to avoid when using a torque wrench include not calibrating the tool before use, using the wrong units of measurement, over-tightening bolts, and not following the manufacturer’s instructions for your specific torque wrench.
How often should a torque wrench be calibrated?
The frequency of calibration for a torque wrench can vary depending on how often it’s used and the manufacturer’s recommendations. Most experts recommend calibrating a torque wrench at least once per year or every 5,000 cycles.
What should you do if you suspect your torque wrench is not calibrated correctly?
If you suspect your torque wrench is not calibrated correctly, the best course of action is to have it recalibrated by a qualified professional. Using an improperly calibrated torque wrench can result in inaccurate torque values, which can lead to unsafe or unreliable bolted connections.