How to Set NM on a Torque Wrench: A Step-by-Step Guide for Accurate Results
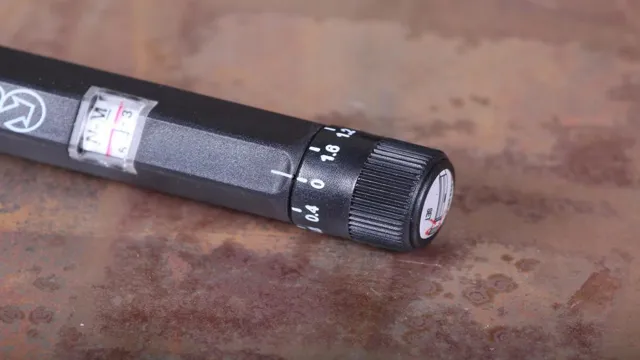
Do you own a torque wrench but aren’t sure how to set it to the appropriate NM? Don’t worry, you’re not alone. For many, setting the desired torque measurement can be a perplexing task. However, it’s important to understand the proper techniques to ensure your fasteners are tightened to the right amount and prevent any potential damage or accidents.
Think of a torque wrench like a clock. Just like how you set the time on a clock, you need to set the torque measurement on a wrench. The difference is that instead of hands, the torque wrench uses a gauge to measure how much force you’re applying.
But before you start adjusting the wrench, make sure to read the manufacturer’s instructions to get a better understanding of how to use it properly. Then, set the initial torque by turning the adjusting knob to the desired value in Newton-meters (NM). Make sure the torque wrench is set to the lowest possible torque setting before making any adjustments.
Now, it’s time to adjust the torque wrench to the right setting. Place the socket on the fastener, and adjust the wrench until the desired torque level is indicated on the gauge. Once the gauge reaches the designated level, stop tightening the fastener.
Setting the appropriate NM on a torque wrench takes practice, and it’s important to remember to reset the tool after it has been used. Nevertheless, with these simple techniques and a little patience, you’ll be able to confidently set your torque wrench and tackle any bolt-tightening task that comes your way.
What is a Torque Wrench
A torque wrench is a vital tool used for tightening bolts to a specific level of tightness, or torque. It is important to set the nm on a torque wrench to ensure the correct level of torque is applied. To set the nm on a torque wrench, begin by turning the handle to set the desired torque level.
Once the desired level is set, tightening the bolt will automatically stop once the set amount of torque is reached. It is important to note that different types of bolts require different levels of torque, so it is essential to consult the appropriate manual or chart to determine the right amount of torque needed. Always ensure that the torque wrench is kept calibrated and maintained to guarantee accurate measurements.
In summary, understanding how to set the nm on a torque wrench is crucial in achieving the correct level of torque and ensuring the safety and integrity of the equipment being tightened.
Definition of Torque
Torque wrenches are specialized tools used to accurately apply a specific amount of force, or torque, to a bolt or nut. This is important because over-tightening can lead to bolts snapping or threads being stripped, while under-tightening can cause components to loosen and fail. Torque wrenches come in different shapes and sizes and have specific torque ranges, which are usually measured in foot-pounds or Newton-meters.
Some wrenches have built-in mechanisms, such as audible clicks or vibrations, to signal when the desired torque has been reached. Others may have a digital readout or be programmable for precise torque settings. Using a torque wrench ensures that bolts are fastened to the correct tightness, reducing the risk of safety hazards or equipment failure.
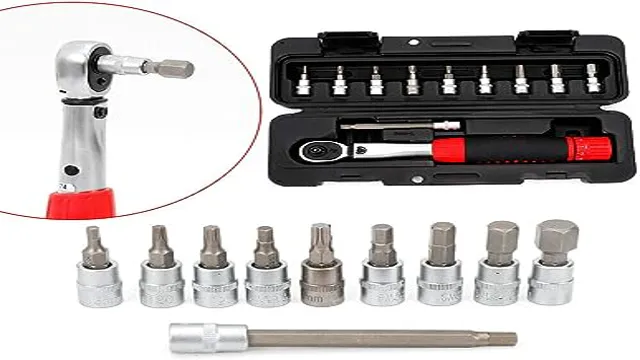
Types of Torque Wrenches
A torque wrench is a tool used to tighten bolts and nuts to a specific torque value. It helps in ensuring that the required amount of force is applied without over-tightening or under-tightening the fastener. There are different types of torque wrenches available in the market, such as click, beam, dial, digital, and electronic torque wrenches, each with its own advantages and disadvantages.
Click torque wrenches are the most commonly used and make a clicking sound when the desired torque value is reached, while beam torque wrenches use a pointer on a calibrated scale to display the torque reading. Dial and digital torque wrenches display the torque value electronically, making them more accurate than other types. Electronic torque wrenches use sensors to measure the torque applied and display it on a digital screen.
Depending on the application and budget, users can choose the appropriate type of torque wrench that best suits their needs.
Selecting the Correct Torque Wrench for your Project
If you are looking to use a torque wrench for your project, it is important to select the correct one for the job. One important aspect to consider is how to properly set the torque in Newton meters (nm) on the wrench. First, consult the specifications of the project to determine the correct torque setting.
Then, locate the torque adjustment mechanism on the wrench and turn it until it aligns with the desired torque setting on the wrench’s scale. Be sure to use a consistent motion and avoid over-tightening, which can lead to damage or failure. Additionally, it is important to regularly calibrate your torque wrench to ensure accurate readings and reliable performance.
By selecting the right wrench and properly setting the torque, you can ensure successful completion of your project.
Matching Wrench to Fastener
Choosing the right torque wrench for your project can be a challenging task, but it is essential for ensuring that your fasteners are tightened to the correct torque. The torque required for a particular fastener depends on its size and material, and using an incorrect torque can lead to stripped threads, broken bolts, or even accidents. There are several types of torque wrenches available, including beam, click, and digital torque wrenches, each with its own advantages and disadvantages.
Click torque wrenches, for example, provide an audible click when the desired torque is reached, while digital torque wrenches offer precise readings and are capable of storing multiple torque values. It is also important to consider the range of torque required for your project and select a wrench that can accommodate it. By selecting the correct torque wrench for your fasteners, you can ensure that your project is completed safely and to the highest standard.
Determining Torque Values Required
When it comes to torque values, it’s crucial to select the correct torque wrench for your project. Torque wrenches come in various sizes and types, and each has its specific use. Determining the torque value required for the job can help you choose the right tool for the task.
This value is usually found in the manufacturer’s manual or instructions. It is vital to consider the material you are working with, its hardness, and the required torque setting for the specific job. A wrench with a too low torque value than required may not tighten the bolts enough, while a wrench with high torque value may damage the material or strip the bolts.
Therefore, ensure you have the correct torque wrench to improve job efficiency and accuracy while preventing damage or injury. Always remember to provide regular maintenance to ensure the durability and accuracy of your torque wrench.
Setting the Torque Wrench
Setting the nm on a torque wrench is an important step in ensuring that bolts are tightened to the correct specification. To begin, determine the specific torque setting required for the task at hand. This information can be found in the owner’s manual of the equipment or can be obtained by researching the manufacturer’s specifications online.
Once you have determined the required torque setting, locate the torque wrench adjustment knob or collar. This is typically found at the base of the torque wrench near the handle. Turn the adjustment knob or collar until the desired torque setting is displayed on the wrench’s scale or digital readout.
It is important to note that torque wrenches should never be used to loosen bolts. They are designed to tighten bolts to a specific torque setting and should only be used for this purpose. After setting the torque wrench to the correct value, test the wrench on a bolt or nut that does not require tightening to ensure that the wrench is functioning properly.
Apply the wrench to the bolt or nut and observe whether the torque wrench indicator reaches the desired value. By following these steps, you can ensure that your torque wrench is properly set to the required torque value and is ready to perform the necessary tightening tasks. Remember to always read the manufacturer’s instructions and specifications before using any tool to ensure safe and proper operation.
Confirm Calibration Before Use
Setting the torque wrench can be a tricky task, and it’s essential to get it right to ensure that it provides accurate results. Before using your torque wrench, always confirm that it’s calibrated correctly. This step is crucial because an incorrectly calibrated torque wrench can provide false readings that could lead to significant issues.
To set your torque wrench correctly, you’ll need to determine the appropriate setting for the bolt or nut you’re working on and adjust the wrench accordingly. You can find this information in the manufacturer’s instructions or by consulting a torque chart. Once you’ve set the wrench, always check it against a torque tester to ensure that it’s providing accurate readings.
Remember that a torque wrench should be recalibrated regularly, so keep track of when it’s due for maintenance. By following these steps, you can ensure that your torque wrench is set correctly and providing accurate results every time.
Identify Fastener
When it comes to setting the torque wrench, there are a few things you need to keep in mind. First and foremost, you need to identify the fastener you’ll be working on. Different fasteners have different torque requirements, so it’s important to know what you’re dealing with before you even touch the torque wrench.
Once you know what you’re dealing with, you can move on to actually setting the wrench. Most torque wrenches have a dial or gauge that you can use to set the desired torque level. Make sure you read the manufacturer’s instructions carefully before attempting to set the wrench, as different models can have different settings.
When you’re ready to use the wrench, make sure you do it carefully and incrementally, checking the torque level after each turn. This will ensure that you don’t over-tighten or under-tighten the fastener, which could lead to all sorts of problems down the road. Overall, setting the torque wrench correctly is crucial for any DIY project or professional work, so take the time to do it right.
Adjust Wrench to Required Torque
When it comes to using a torque wrench, the most important step is setting it to the required torque. This may seem daunting, but it is actually a simple process. First, you need to determine the torque specifications for the job you are doing.
This can be found in your car or equipment’s manual or online. Once you have this information, you can adjust the torque wrench according to the required torque by twisting the handle or using the digital display. It’s important to make sure you’ve set the wrench accurately, otherwise, you may risk damaging your equipment or not tightening a bolt enough.
So, take your time and double-check before you start using the wrench. Remember, a torque wrench is a precision tool, and can be highly effective when used correctly.
Using the Torque Wrench
When it comes to using a torque wrench, one crucial step is setting the appropriate force measurement in newton meters (Nm). This ensures that bolts and nuts are tightened to the correct level, avoiding potential damage or safety hazards. To set the Nm on a torque wrench, first, determine the correct Nm value needed for your specific task by referring to the manufacturer’s instructions or a torque chart.
Once you have the Nm value, adjust your torque wrench’s settings by turning the handle or using the digital display until the correct Nm is displayed. Double-check your settings before using the wrench to avoid any mistakes. It’s essential to maintain your torque wrench properly, including checking calibration regularly and storing it in its case when not in use, to ensure it continues to provide accurate results.
By taking care of your torque wrench and following the correct steps to set it to the correct Nm, you can have added confidence when working with bolts and nuts.
Positioning the Wrench
When it comes to using a torque wrench, positioning the wrench correctly is crucial for accurate readings. To properly position the wrench, first, identify the fastener you want to tighten and select the appropriate socket. Ensure that both the socket and the wrench are clean and free from debris.
Next, place the socket onto the fastener and make sure that it is seated flush. Align the torque wrench in line with the socket so that the handle is perpendicular to the socket and straight. Then, set the torque wrench to the desired torque level, making sure it is within the torque range of the wrench.
Finally, apply force to the handle of the wrench, gradually increasing the pressure until you hear an audible click indicating that the desired torque level has been reached. Remember to always read the manufacturer’s instructions for the specific torque wrench you are using. By following these steps, you can ensure accurate and effective use of your torque wrench, leading to successful projects every time.
Tightening the Fastener
A torque wrench is an essential tool for anyone looking to make accurate and consistent tightness adjustments to fasteners. It’s particularly important when working on high-torque applications such as engines, suspensions, or steering components. The torque wrench works by measuring the amount of force being applied to the fastener and ensuring that it is tightened to a specific level.
This prevents under-tightening, which can lead to parts failing or coming loose because there isn’t enough clamping force, or over-tightening, which can lead to stripped or broken fasteners. With the proper calibration and usage, a torque wrench can be a valuable asset in any mechanic’s arsenal. Just make sure to follow the manufacturer’s instructions and re-check the torque after a few uses to ensure consistent accuracy.
Conclusion
Setting the nm on a torque wrench may seem like a daunting task, but fear not! With just a few simple steps, you’ll be tightening bolts with precision and accuracy in no time. Remember: always consult your manufacturer’s specifications for the correct torque setting and use a reliable torque wrench for the job. So go forth and conquer those stubborn bolts with confidence and ease, thanks to your newfound torque wrench prowess!”
Proper Maintenance for Torque Wrenches
Using a torque wrench is not as complicated as it may seem. The tool is designed to ensure that every bolt is tightened to the specified torque, which is crucial when working on machinery, vehicles, or any equipment that requires a certain level of precision. When using a torque wrench, it is vital to follow the manufacturer’s recommendations, such as which type of lubricant to use on the tool and what type of calibration to use when tightening bolts.
It’s also important to calibrate the wrench regularly to keep it functioning as well. Failing to do so may affect the accuracy of the torque wrench and cause issues with the tightness of the bolts. Whether you’re a seasoned mechanic or a novice, taking care of your torque wrench can go a long way in ensuring that it performs optimally and consistently.
By doing this, you can prevent potential issues and prolong its lifespan.
Importance of Proper Torque Techniques
Proper torque techniques are essential when it comes to maintaining automobiles and ensuring optimal performance. One of the most important tools in any mechanic’s arsenal is the torque wrench, which allows for precise tightening of bolts and nuts to specific torque values. Whether you’re working on your car at home or in a professional garage, using a torque wrench is crucial to prevent overtightening or undertightening, which can result in damage to your vehicle’s components or even failure of critical systems.
By utilizing a torque wrench, you can ensure that every bolt is tightened to the manufacturer’s recommended torque specification, which in turn can help preserve the longevity of your vehicle and improve its overall safety and reliability. It’s important to remember that torque wrenches come in different types and sizes, so be sure to choose the right one for the job to achieve accurate results.
FAQs
What is the purpose of setting the nm on a torque wrench?
The purpose of setting the nm on a torque wrench is to ensure that bolts are tightened to the correct level of torque and to prevent overtightening or undertightening.
How do I know what nm to set my torque wrench to?
You can find the recommended torque specifications in your vehicle or equipment’s owner’s manual, or by checking with the manufacturer.
What should I do if my torque wrench is not accurate?
If your torque wrench is not accurate, it should be recalibrated or serviced by a qualified technician.
Can I set the nm on a torque wrench using my hand?
No, setting the nm on a torque wrench requires a specific adjustment process using the tool’s built-in calibration system or a separate calibration tool.
Is it possible to overtighten bolts with a torque wrench?
Yes, it is possible to overtighten bolts if the torque wrench is not calibrated correctly or if it is not used properly.
Is it necessary to set the nm on a torque wrench for every application?
Yes, it is necessary to set the nm on a torque wrench for every application to ensure that the bolts are tightened to the correct level of torque and to prevent damage or failure.
Can I use a torque wrench to loosen bolts?
No, torque wrenches should only be used to tighten bolts to a specific level of torque. Loosening bolts should be done with a breaker bar or other appropriate tool.