How to Test a Welding Helmet: Tips and Tricks for Ensuring Safety
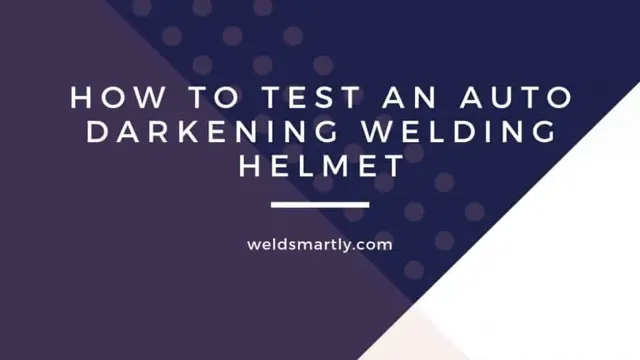
Welding helmets are a crucial piece of safety equipment for anyone engaged in welding activities. They shield your eyes and face from sparks, harmful UV rays, and heat. However, to ensure their effectiveness, it’s essential to test your welding helmet regularly.
But do you know how to test a welding helmet? Don’t worry, we’ve got you covered! In this blog post, we’ll explore the various ways you can check the effectiveness of your welding helmet, from inspecting the lens to checking the headgear’s stability. So grab a cup of coffee, put on your reading glasses, and let’s dive into the world of welding helmet testing!
Introduction
If you’re a welder, you know how important it is to have the right welding helmet to protect yourself from harmful sparks and debris. But how can you be sure that your helmet is actually doing its job? The best way to test a welding helmet is to perform a simple visibility test. Start by putting on the helmet and looking directly at a bright light source, such as a light bulb or the sun (don’t stare too long, though!).
If there are any gaps or holes in your helmet, you should be able to see the light shining through. A fully functioning helmet should block out all light, meaning that you won’t be able to see anything other than darkness. Additionally, you should ensure that the helmet fits properly and comfortably on your head, as a poorly fitting helmet can compromise its efficacy.
By taking the time to test your welding helmet, you can have peace of mind knowing that you’re protected on the job.
Understanding the importance of testing your helmet
When it comes to cycling or any other activity that involves head injuries, wearing a helmet is crucial for safety. But just putting on a helmet isn’t enough; you need to make sure that your helmet is tested and certified to protect your head from potential injury. Helmet testing is done to ensure that the helmets meet the required safety standards and offer optimal protection for the wearer.
The importance of testing your helmet cannot be overstated, as it may help you avoid severe head injuries in case of an accident. Therefore, when buying a helmet, make sure it is certified and has passed the required safety tests to ensure your safety while engaging in various activities.
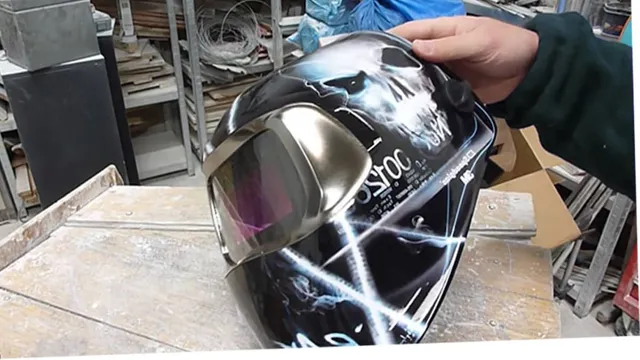
Types of welding helmet tests
When it comes to welding, safety should always be a top priority. One of the most critical safety gear pieces is the welding helmet. To ensure that the helmet provides reliable protection, it undergoes several tests.
One of these tests is the impact test, where a steel ball is dropped on different areas of the helmet to test its ability to withstand hard impacts. Another crucial test is the penetration test, important in evaluating the helmet’s ability to withstand flying objects. There’s also the optical test, which evaluates the helmet’s lens clarity to ensure clear and precise visibility to the welder.
Lastly, the auto-darkening test checks the helmet’s ability to provide immediate lens darkening during welding. All these tests are crucial for a welding helmet to meet safety standards and protect the welder’s eyes and face from harmful radiation and sparks during welding operations. Therefore, it’s essential to choose the right helmet that has undergone these tests and has a safety certification.
It will guarantee that you’re working with reliable and safe welding equipment and, most importantly, protect your eyes and face from harm.
Visual inspection
When it comes to testing a welding helmet, one effective method is the visual inspection. This involves examining the helmet and checking for any signs of damage, wear and tear, or defects. Start by inspecting the lens for scratches, cracks, or discoloration, as these can affect visibility and compromise safety.
Then, check the headgear for any loose parts or straps that may not secure the helmet in place. Other areas to inspect include the shell for any dents or cracks, the filter shade for conformity with the welding process, and the overall ergonomics of the helmet to ensure comfort and flexibility. By conducting a thorough visual inspection prior to use, you can ensure that your welding helmet is in good working order and that you can work safely and effectively.
So, next time before using your welding helmet, examine it closely for any possible issues and protect yourself from any potential hazards.
Inspecting the lens
When it comes to inspecting the lens, a visual inspection is crucial. It’s the first step in determining any damage or wear to the lens that may impact its performance. One thing to keep in mind is to make sure the lens is clean and free from any debris or smudges before inspection.
Look for any scratches on the surface of the lens, as these can affect the image quality. Also, check the lens mount for any damage or looseness, as this can cause the lens to not properly attach to the camera body. Another important factor to consider is the alignment of the elements inside the lens.
Depending on the type of lens, it may have multiple elements that need to be aligned correctly to produce sharp images. Inspecting the lens can take some time, but it’s worth it to ensure you’re getting the best image quality possible.
Inspecting the shell and headgear
When it comes to inspecting the shell and headgear on your equipment, the first step is to conduct a visual inspection. This involves examining the shell for any cracks, dents, or deformities that could compromise its structural integrity. Additionally, you should check the headgear for signs of wear and tear, including frayed straps, torn padding, or loose connections.
These issues can significantly reduce the protection provided by your equipment and should be addressed promptly to ensure your safety on the job. As a safety precaution, it is also advisable to inspect your equipment before each use to identify any potential hazards. By conducting a visual inspection, you can identify any damage or defects that may have occurred during storage or transport and take appropriate action to prevent injury.
Remember, investing time and effort into maintaining your equipment can save your life in the long run.
Functional testing
If you’re looking to test your welding helmet, there are a few functional tests you can do to make sure it’s up to standard. The first thing to check is the lens. This is the most important part of the helmet as it protects your eyes from the bright light of welding.
Ensure that it’s dark enough to protect your eyes from harmful UV rays but not so dark that you can’t see what you’re working on. Another important aspect of your helmet is the fit. It should be snug but not too tight and it should stay comfortably in place while you move your head around.
Lastly, check the headgear. Make sure the suspension is comfortable and that it’s easy to adjust for a good fit. Paying attention to these details will ensure that your welding helmet is safe and efficient when in use.
Auto-darkening lens testing
When it comes to welding, having the right equipment can make all the difference. One crucial piece of equipment is the auto-darkening lens, which provides protection for the eyes from harmful UV and IR radiation. It is important to perform functional testing on auto-darkening lenses to ensure they are working correctly.
One common test is a sensitivity test, where the lens is exposed to different levels of light to ensure it responds properly and darkens as intended. Another test is a delay test, where the lens is exposed to a bright light and timed to see how quickly it darkens. These tests help to ensure that the lens will protect your eyes properly when welding.
Overall, functional testing is a crucial step in ensuring the safety and effectiveness of auto-darkening lenses. By performing these tests, welders can have peace of mind knowing that their equipment is working properly and that they are adequately protected while on the job.
Delay and sensitivity testing
Functional testing is essential to ensure that your software performs as expected in different situations. One of the types of functional testing is delay and sensitivity testing. This type of testing is done to check how the software performs when it encounters delays or delays in the system.
It is important to test the software’s response time because if the software takes too long to respond, it can frustrate the end-user. The sensitivity testing is done to ensure that the software functions well with different input devices. For example, a software program designed to be used with a mouse may not work well when used with a touchpad or a stylus.
It is important to test the software under different conditions to make sure it performs well. By conducting delay and sensitivity testing, you can ensure that your software is user-friendly and performs as expected.
Battery testing
Battery testing is a crucial process to ensure that the battery can perform its functions properly. Functional testing is one of the types of battery testing that focuses on verifying the battery’s electrical and mechanical characteristics. It aims to test the battery’s functionality under normal operating conditions to identify any potential defects that may affect the battery’s performance.
The functional testing process usually involves subjecting the battery to different environmental conditions, such as temperature, humidity, and pressure, to simulate the battery’s actual usage scenarios. This testing process helps to identify potential battery failures that may occur during the battery’s normal usage. In summary, functional testing ensures that the battery performs its intended functions correctly and can prevent potential damages that may arise from faulty batteries.
Overall, battery testing is a critical process that ensures that batteries can perform their tasks effectively and promotes safety.
Conclusion
In summary, testing a welding helmet is not rocket science. Just like you do with your phone before buying, inspect the helmet for an ANSI label, check the shade number, flip the visor up and down, and test the sensitivity and delay settings. Don’t forget to try it on for size and comfort.
And if you really want to get creative, why not test its durability against a falling anvil or a low-speed car collision? Ok, maybe don’t try the latter, but you get the point – the right welding helmet should protect you without compromising your vision, comfort, or style. Happy welding!
FAQs
What should be tested in a welding helmet?
Welding helmets should be tested for optical clarity, light sensitivity, and responsiveness of the auto-darkening feature.
What is the best way to test a welding helmet for optical clarity?
The best way to test a welding helmet for optical clarity is to look through the lens at a bright light source and check for any distortions or discolorations.
How do you test the light sensitivity of a welding helmet?
To test the light sensitivity of a welding helmet, expose it to different intensity levels of light to ensure that the auto-darkening feature is working properly.
What standards should a welding helmet meet?
A welding helmet should meet industry standards such as ANSI Z87.1 and should comply with safety regulations set by government agencies.
Can a welding helmet be used for other applications besides welding?
Yes, welding helmets can be used for other applications such as cutting and grinding, but it is important to ensure that the lens shade is appropriate for the task.
How often should a welding helmet be tested?
Welding helmets should be tested regularly, at least once a year, to ensure that they are functioning correctly and the auto-darkening feature is working.
What should be done if a welding helmet fails a test?
If a welding helmet fails a test, it should be repaired or replaced immediately to ensure that the welder is adequately protected while working.