If you’ve ever worked on a car, a bike, or even some appliances, chances are you’ve heard about torque wrenches. But what exactly are they, and why are they so important? Well, put simply, a torque wrench is a tool used to tighten bolts or nuts to a specific level of tightness, or torque. Why is this important? Because over-tightening can cause damage, while under-tightening can lead to parts coming loose or even breaking off entirely.
Think of it like Goldilocks: you want your bolts to be tightened just right. And that’s where torque wrenches come in – they ensure you get the perfect level of tightness, every time. In this blog, we’ll dive deeper into the benefits of using torque wrenches and why they’re a vital tool for any mechanic or DIY enthusiast.
What is a Torque Wrench?
What is a torque wrench and why is it important? A torque wrench is a tool that helps tighten bolts or nuts to a specific torque, or amount of force, measured in foot-pounds or newton-meters. Using a torque wrench ensures that the fasteners are tightened to the manufacturer’s recommended specifications, preventing overtightening or undertightening which can lead to various problems. But what happens if you choose not to use a torque wrench? Overtightening can cause bolts to break or strip threads, while undertightening can result in improper assembly or frequent loosening during use.
This could potentially lead to safety hazards such as vehicles parts coming loose while in use or machinery not working as intended. Using a torque wrench may seem like an extra step in the process, but it can save you from costly mistakes and ensure the safety of yourself and others. So next time you’re working on a project that requires tightening bolts or nuts, consider using a torque wrench and following the recommended torque specifications.
Your safety may depend on it.
Explanation of How Torque Wrenches Work
A torque wrench is a tool designed to measure the force applied to a fastener, such as a bolt or nut, when tightening it. It is a critical tool in industries that require precision assembly, such as automotive, aviation, and construction. Unlike a regular wrench, which relies on the operator’s experience to judge the amount of force applied, a torque wrench uses a calibrated mechanism to measure the applied torque and ensure that the fastener is tightened to the correct specification.
The mechanism of a torque wrench typically includes a spring-loaded lever or a digital display that shows the applied force. When the operator applies force to the wrench, the mechanism begins to compress the spring. When the required torque is reached, the wrench will “click” or “release,” indicating that the fastener has been tightened to the correct specification.
Some torque wrenches come with adjustable settings that allow the operator to set the desired torque level. This feature is particularly useful when working with different fasteners that require different levels of torque. By adjusting the torque wrench’s settings, the operator can ensure that each fastener is tightened to the correct specification.
In conclusion, a torque wrench is an essential tool in industries that require precise assembly. It ensures that each fastener is tightened to the correct specification and therefore provides a safe and reliable end product. By using a torque wrench, operators can reduce the risk of over-tightening or under-tightening fasteners, which can cause damage to the product or even lead to dangerous situations.
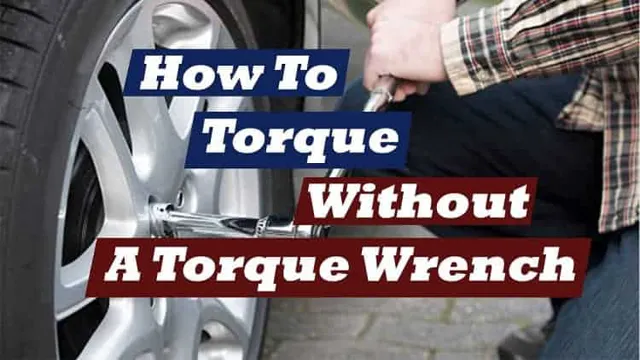
Why Use a Torque Wrench?
If you’ve ever worked on a car or bike, you know that tightness matters. Bolts and nuts have to be fastened just right to keep everything together and prevent damage or accidents. That’s where a torque wrench comes in handy.
Without it, you’re basically guessing how much force to apply, which can be dangerous. Over-tightening can strip threads, warp surfaces, or even crack parts. Under-tightening can cause loosening, vibrations, or failures.
What happens if you don’t use a torque wrench? Well, you may get lucky sometimes, but sooner or later, something will go wrong. Plus, you’ll miss out on the precision and reliability that a torque wrench provides, ensuring that you can tighten components accurately and consistently. Whether you’re a DIY mechanic or a professional, a torque wrench is a must-have tool for any job that requires tightening or loosening bolts and nuts.
Don’t risk your safety or the integrity of your equipment by using guesswork. Invest in a quality torque wrench and use it properly.
Importance of Proper Torque in Preventing Equipment Failure
Proper torque is essential to prevent equipment failure, and one of the best tools for achieving accurate torque is a torque wrench. A torque wrench is a tool that allows you to apply a precise amount of torque to a fastener, ensuring that it is tightened to the manufacturer’s specifications. Using a torque wrench is critical because over-tightening a fastener can cause it to strip or break, while under-tightening can result in it coming loose or not functioning as intended.
It’s essential to know when to use a torque wrench, especially in scenarios where safety and reliability are critical. For instance, during car tire changes, it’s essential to ensure that the lug nuts are tightened to the manufacturer’s recommended level of torque. In conclusion, using a torque wrench is essential to achieving accurate torque levels and ensuring safe and reliable operations of various equipment.
Ensures Safety and Compliance
As a professional technician, using a torque wrench is essential for ensuring safety and compliance in your work. Torque wrenches are designed to provide accurate and consistent torque measurements, which is vital when working with any mechanical or automotive equipment. Without a torque wrench, you risk over-tightening or under-tightening bolts, which could lead to costly damage, injuries, or worse.
Compliance with industry standards and regulations is necessary, and using a torque wrench is a great way to ensure that you meet those requirements. By using a torque wrench, you can maintain the correct levels of torque and tension on bolts and fasteners, preventing accidents and ensuring that your work meets the necessary safety standards. Overall, using a torque wrench is essential if you want to work safely and confidently and avoid the risks that come with not using one.
So, next time you’re carrying out any technical work, make sure you use a torque wrench, and you’ll be able to guarantee safety and compliance.
What Happens When You Don’t Use a Torque Wrench?
If you don’t use a torque wrench, you risk damaging your equipment or causing serious injury. Over-tightening can stretch or snap bolts, whereas under-tightening can lead to parts coming loose or falling off altogether. Without a torque wrench, it’s impossible to accurately measure the force being applied to a bolt.
This is particularly important in automotive or industrial settings, where precise torque settings are crucial to prevent accidents and ensure proper operation. Think of torque like a heart rate monitor that tells you when you’re pushing yourself too hard or not hard enough during exercise. Just as you wouldn’t want to pass out from over-exertion, you wouldn’t want to risk your safety or the safety of others by neglecting the importance of using a torque wrench.
So, to avoid costly repairs or potential harm, always use a torque wrench when tightening bolts.
Under-Torquing
When it comes to working on cars and machinery, using a torque wrench can make a significant difference in the overall outcome. Under-torquing is a common issue that arises when individuals do not use a torque wrench or do not use it properly. Simply put, under-torquing refers to when the bolts on a car or machine are not tightened enough.
This can happen when the person tightening the bolt is unsure of how tight it should be or if they are simply using their own strength to tighten it. The result of under-torquing can be dangerous, as it could lead to the bolt coming loose and a potential malfunction of the machinery. In addition, under-torquing can cause damage to the threads on the bolt, which could lead to costly repairs or replacements.
Therefore, it is always best to use a torque wrench when working on machinery and to make sure that it is calibrated correctly to ensure that the bolts are tightened to the appropriate level.
Over-Torquing
Over-Torquing If you’ve ever worked on a car or tried to fix something yourself, you know how tempting it can be to tighten things up as much as possible. However, over-torquing can actually cause serious damage to your vehicle or equipment. Without the use of a torque wrench, it’s easy to apply too much pressure and overtighten bolts or screws.
This can lead to stripped threads, cracked components, and even complete parts failure. It’s important to use a torque wrench to ensure that each bolt or screw is tightened to the manufacturer’s recommended specifications. This will help prevent over-torquing and ensure that your equipment or vehicle operates safely and efficiently.
Remember, too tight is never right!
Damage to Equipment and Tools
Using a torque wrench is crucial in ensuring that bolted connections are tightened to the right specifications. If you don’t use a torque wrench, you run the risk of damaging your equipment and tools in various ways. For instance, if you over-tighten a nut or bolt, you can strip the threads on both the bolt and the hole.
This damage can be permanent and you may have to replace the whole part. On the other hand, if you under-tighten a nut or bolt, it will become loose and may eventually come off, causing even more severe damage to your equipment. In either case, your equipment’s efficiency and effectiveness will be compromised.
This is why it’s essential to use a torque wrench when making mechanical adjustments. Otherwise, you risk significant damage to your equipment, shortening its lifespan and causing unnecessary costs. Take the extra time to use a torque wrench to avoid the risk of damaging your equipment and your wallet.
Conclusion
In short, not using a torque wrench is like playing Russian roulette with your vehicle or machinery. Sure, you may dodge a bullet and get lucky a few times, but eventually, your luck will run out and you’ll be left with a costly repair bill or worse, a dangerous accident. So, use a torque wrench and give yourself peace of mind knowing that everything is properly tightened to the recommended specifications.
“
Why It’s Important to Always Use a Torque Wrench
Using a torque wrench may seem like an unnecessary hassle, but it’s actually an essential tool for ensuring the safety and longevity of your equipment. When you don’t use a torque wrench, there’s a risk of under-tightening or over-tightening bolts, which can lead to a host of issues. Over-tightening can cause the bolt to snap or strip, while under-tightening can lead to vibration and eventual failure of the nut or bolt.
Imagine trying to build a house without a level – the same principle applies to not using a torque wrench. It’s important to use the proper torque specifications for each bolt, and using a torque wrench is the best way to ensure that you’re doing so accurately and consistently. By taking the time to use a torque wrench, you’re investing in the safety and functionality of your equipment, which will save you time, money, and potential headaches in the long run.
FAQs
What is the importance of using a torque wrench?
A torque wrench ensures that bolts are tightened to the manufacturer’s specifications, preventing over-tightening and potential damage, or under-tightening and potential failure.
Can I use a regular wrench instead of a torque wrench?
It is not recommended as a regular wrench does not provide precise torque measurements.
What happens if you don’t use a torque wrench?
Without a torque wrench, bolts may be over-tightened, causing damage, or under-tightened, leading to potential failure.
How do you calibrate a torque wrench?
Calibrating a torque wrench typically involves applying a known amount of force to a calibration tool and adjusting the wrench accordingly.
Can a torque wrench be reused for multiple projects?
Yes, as long as it is calibrated and maintained correctly.
What is the difference between a click-type and beam-type torque wrench?
A click-type torque wrench will emit an audible “click” when the desired torque is reached, while a beam-type wrench relies on a visual gauge to indicate torque.
How often should a torque wrench be calibrated?
It is recommended to calibrate your torque wrench at least once a year or every 5,000 uses, whichever comes first.