Welding machines are essential tools for any welding project, whether it’s a small DIY project or a large industrial project. Choosing the right welding machine is critical to ensure the success of your project. With so many options available in the market, it can be overwhelming to determine which welding machine is right for you.
But fear not, we’re here to guide you through the process and help you choose the right welding machine for your needs. In this blog, we’ll discuss the factors you should consider while selecting a welding machine and the various types of welding machines available in the market. Choosing the wrong welding machine can be both frustrating and expensive, resulting in a failed project or costly repairs.
However, with the right information and guidance, you can avoid making the wrong decision. So, buckle up and let’s dive into the world of welding machines and find the perfect one for your next project.
Consider your Welding Needs
If you are in the market for a welding machine, the first thing to consider is your welding needs. There are many different types of welding machines available, each with its own set of features and capabilities. Some are designed for home use, while others are intended for industrial applications.
Before you start shopping, take a look at the type of welding you will be doing, the materials you will be working with, and the frequency of use. This will help you narrow down your options and choose a machine that will meet your specific needs. When searching for a welding machine, keep the keyword “what welding machine should I buy?” in mind.
This will help you focus your search and find the best equipment for your needs.
Type of Material
When it comes to welding, the material you are working with plays a crucial role in determining the type of welding process and equipment you need. Whether you are working with aluminum, steel, copper, or other metals, each material has its own unique characteristics that affect the welding process. For example, aluminum is more lightweight and conducts heat better than steel, making it more challenging to weld.
Additionally, the thickness of the material and the desired outcome must also be taken into consideration. High-quality welds require precision, attention to detail, and the right type of equipment for the job. To ensure a successful weld, it is essential to hire a skilled welder with experience working with your particular material.
By considering your welding needs and selecting the right type of material and equipment, you can achieve excellent results that will stand the test of time.
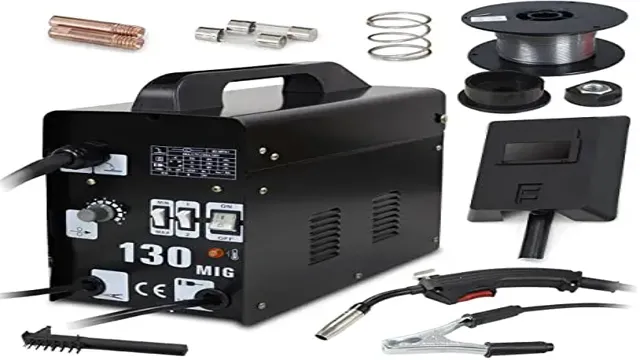
Thickness of Material
When it comes to welding, it’s important to consider the thickness of the material you’ll be working with. Different welding techniques are better suited for different thicknesses. For instance, MIG welding is typically the best choice for thicker materials, as it can produce high-quality welds quickly and efficiently.
TIG welding, on the other hand, is better suited for thinner materials, as it allows for greater precision and control. Of course, the specific technique you choose will also depend on other factors, such as the type of material you’re working with and the desired finish. Ultimately, it’s important to carefully consider your welding needs before choosing a technique, as this can save you time, money, and frustration in the long run.
Type of Welding Process
When it comes to welding, the type of welding process you choose is crucial. Different welding processes are designed for different materials, and choosing the wrong process can lead to weak welds, damage to the materials, or even injury to the welder. Before you decide on a welding process, consider your welding needs.
Are you welding thick or thin materials? Do you need to weld in tight spaces? Will the welds be load-bearing? Answering these questions will help you choose the right welding process for your specific needs. The most common types of welding processes include MIG, TIG, stick, and flux-cored welding, but there are many others to choose from. Take the time to research each process and speak with a welding professional to ensure you make the best decision for your welding project.
Power Output
When it comes to buying a welding machine, power output is a crucial factor to consider. The power output of a welding machine determines the thickness of the metal that can be welded. If you plan on working with thin metals, a welding machine with lower power output will suffice.
However, if you aim to weld thicker metals, you’ll need a machine with higher power output. Choosing the right welding machine with the appropriate power output will ensure that you can handle the welding tasks efficiently and produce high-quality welds. So, if you’re wondering what welding machine you should buy, make sure to consider the power output and the type of work you’ll be doing to make an informed decision that meets your welding needs.
Amperage
Amperage, which is the measure of electrical current, plays a crucial role in determining the power output of a device. Simply put, the higher the amperage, the more power a device can deliver. For example, a device that consumes 10 amps of current will deliver more power than a device that consumes only 5 amps of current.
However, it’s important to note that not all devices can handle high amperage. It’s essential to consider the limits of the device in terms of amperage before connecting it to a power source. Using a device beyond its amperage capacity can cause overheating, damage, and even fire hazards.
Therefore, it’s important to ensure that the amperage of the device and the power source are compatible to ensure safe and efficient power output. By understanding amperage and its role in power output, you can make informed decisions when selecting and connecting devices to power sources.
Duty Cycle
Duty Cycle When it comes to electronic devices that emit power output, the duty cycle is an important factor to consider. Essentially, the duty cycle refers to the amount of time a device is actively emitting power compared to the total time of operation. A 50% duty cycle means that the device is emitting power for half the time it’s operational, while a 100% duty cycle indicates continuous power emission.
Understanding the duty cycle is crucial for ensuring devices don’t overheat or become damaged, and it can also impact their effectiveness. For example, devices with a low duty cycle may be less effective than those with a higher duty cycle because they emit power less frequently. The duty cycle is an important consideration when selecting electronic devices, particularly those that are used heavily or for extended periods of time.
Portability
When considering what welding machine to buy, portability is a key factor to keep in mind. Are you someone who needs to move from job to job, or do you have a dedicated workshop where you can set up a larger machine? If you need to be on the move, consider a smaller, more compact machine that can easily be transported between job sites. These machines are often lighter and more portable, making them ideal for contractors or those who work in multiple locations.
However, if you have a dedicated workshop, you may want to opt for a larger machine that can handle more intensive jobs. Regardless of your needs, the key is to find a welding machine that meets your specific requirements and can get the job done efficiently and effectively. So, when you’re thinking about what welding machine to buy, remember to consider the important factor of portability.
Weight
When it comes to technology, portability is a huge factor for many people. Whether you’re a frequent traveler, a student who needs to take their laptop to and from class, or just someone who likes to work from different locations, having a lightweight device is key. The weight of a device can vary greatly depending on the type of technology you’re looking at.
For example, a tablet will generally be much lighter than a laptop, but may not have the same processing power. However, many laptops now come in ultra-lightweight models, with some weighing as little as 2 pounds.
If you’re in the market for a new device, make sure to consider the weight and how easily you’ll be able to carry it around with you. You don’t want to be lugging around a heavy laptop on your commute every day, so finding a lightweight option that still has all the features you need is key.
Ease of Movement
Portability is a crucial aspect when it comes to ease of movement. The ability to conveniently carry your possessions from one place to another can make a huge difference in your daily life. Whether it’s work-related materials, personal belongings, or electronic devices, having things that are easy to transport can save you time, effort, and money.
Having a portable laptop, for example, can allow you to work on the go and be productive no matter where you are. A lightweight and compact vacuum cleaner makes cleaning around your house an effortless task. And having a portable charger for your phone or tablet ensures that you stay connected to the world at all times.
In essence, portability empowers you to do more, travel further, and accomplish your daily tasks with ease. So, whether you’re a busy professional, a student, or simply someone who enjoys a fast-paced lifestyle, having portable items will undoubtedly make your life more manageable and enjoyable.
Brand and Price Comparison
When it comes to choosing the perfect welding machine, there are a few factors to keep in mind, brand and price being two of the most important. It’s easy to get overwhelmed by the multitude of options available on the market, but knowing which brands are reputable and offer reliable products can make a big difference. While it may be tempting to opt for a cheaper machine, it’s important to remember that quality often comes at a higher price.
That being said, investing in a top-of-the-line machine from a trusted brand can save you money in the long run by providing the durability and functionality necessary for your welding projects. Ultimately, the decision between brand and price will depend on your specific needs and budget, but considering both factors will help you make an informed and practical choice for your welding needs. So, what welding machine should you buy? It all depends on how much you’re willing to invest and which brand you trust the most.
Conclusion
In the end, the welding machine you should buy largely depends on your specific needs and preferences. From MIG to TIG, stick welding to flux-cored, there are a variety of options available to suit different projects and budgets. So do your research, weigh the pros and cons, and weld your way to a world of endless possibilities.
Just remember, the best welding machine is the one that gets the job done, and the only sparks that should be flying are the ones from your welds.”
FAQs
What are the different types of welding machines available in the market?
The different types of welding machines available in the market are MIG, TIG, Stick, and Plasma cutters.
Which type of welding machine is best for beginners?
For beginners, a Stick welding machine is the best option as it is easy to use and is cost-effective.
Can I weld aluminum with a MIG welding machine?
Yes, you can weld aluminum with a MIG welding machine, but you will need to use a spool gun.
What should I consider when selecting a welding machine?
When selecting a welding machine, you should consider the type of welding you will be doing, the material you will be working with, the thickness of the material, and your skill level.
Is it better to buy a welding machine with more amperage?
If you plan on working with thicker materials, it is better to buy a welding machine with more amperage. However, if you will be working with thinner materials, a lower amperage will suffice.
Can I use a welding machine for cutting metal?
Yes, you can use a plasma cutter welding machine for cutting metal.
What safety measures should I take when using a welding machine?
Some of the safety measures you should take when using a welding machine are wearing protective gear, keeping your work area well-ventilated, and not welding near flammable or combustible materials.